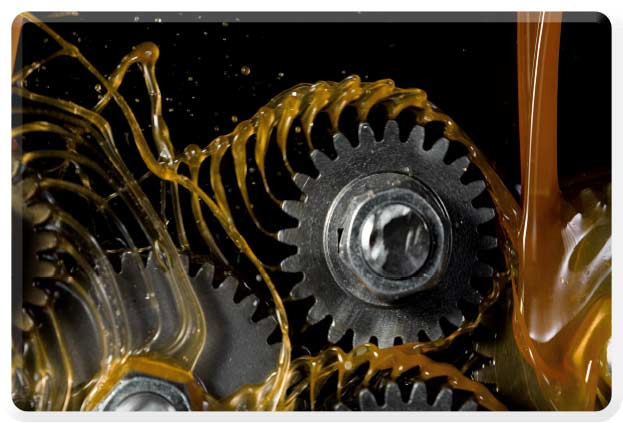
In - depth Exploration of Extreme - Pressure Anti - wear Additives: Characteristics and Application Secrets of Different Types
In modern industrial operations, the efficient and stable operation of mechanical equipment relies heavily on the support of lubricating oils. As a crucial component of lubricating oils, extreme - pressure anti - wear additives act like an "invisible shield" for mechanical equipment. Under harsh working conditions, they shoulder the important responsibilities of protecting friction components, reducing wear, and extending the service life of equipment. With the rapid development of industrial technology, the performance requirements for extreme - pressure anti - wear additives are also increasing day by day. Phosphorus - containing extreme - pressure anti - wear additives have emerged as a new force in the field of lubricating oil additives in recent years due to their unique performance advantages, attracting extensive attention and in - depth exploration from researchers. At the same time, other types of extreme - pressure anti - wear additives, such as boron - containing extreme - pressure anti - wear additives and metal - salt - based extreme - pressure antioxidants, also play key roles in different application scenarios. Next, let's delve into the mysteries of various types of extreme - pressure anti - wear additives.
Phosphorus - containing Extreme - pressure Anti - wear Additives
Phosphorus - containing additives possess multiple functions such as extreme - pressure resistance, anti - wear, friction - reduction, and anti - oxidation. They have good thermal stability, low corrosiveness, and exhibit excellent compatibility when compounded with other functional additives. As a result, they have received extensive attention from researchers and have witnessed rapid development in recent years.
Regarding the mechanism of action of phosphorus - containing additives, there are different viewpoints. Early scholars believed that phosphorus - containing compounds decompose under the instantaneous high temperature at the convex points of the friction surface, react with iron to form iron phosphide, and then iron phosphide reacts with iron to form a low - melting - point eutectic alloy that flows to the concave parts, smoothing the friction surface and playing a "chemical polishing" role to prevent wear. In recent years, some scholars have proposed that under boundary lubrication conditions, phosphides do not form iron phosphide with iron but form a mixture of ferrous phosphite.
The specific action process is as follows: phosphides first adsorb on the iron surface. Under boundary conditions, the C - O bond breaks, generating an organic film of ferrous phosphite or ferric phosphate, which plays an anti - wear role. Under extreme - pressure conditions, the organic ferric phosphate film further reacts to form an inorganic ferric phosphate reaction film, preventing direct metal - to - metal contact and providing extreme - pressure protection.
Phosphorus - containing additives come in a wide variety. Not only are there diverse types of compounds, but their elemental compositions also vary. There are those containing only phosphorus, those containing two elements of sulfur and phosphorus, and those containing multiple elements such as sulfur, phosphorus, and nitrogen. Even if the elemental compositions are the same, the compound structures may be different, and different phosphorus compounds are used in different application scenarios. Generally, according to the active elements, phosphorus - containing additives can be roughly classified into phosphorus - type, phosphorus - nitrogen - type, sulfur - phosphorus - type, sulfur - phosphorus - nitrogen - type, phosphorus - nitrogen - boron - type, sulfur - phosphorus/sulfur - phosphorus - nitrogen - boron - type, etc.
Phosphorus - type Extreme - pressure Anti - wear Additives
Phosphite Esters
Phosphite esters are an important part of phosphorus - type extreme - pressure anti - wear additives. They are usually prepared from phosphorus trichloride and corresponding fatty alcohols or alkylphenols as raw materials. Their load - carrying capacity and anti - wear performance are closely related to the length and structure of the alkyl chain on the alkyl group or benzene ring. When the alkyl chain is long, the anti - wear performance is good, but the load - carrying capacity is poor. Conversely, when the alkyl chain is short, the load - carrying capacity is good, but the anti - wear performance is poor. In addition to good extreme - pressure and anti - wear performance, phosphite esters also have a certain antioxidant capacity and can decompose peroxides and free radicals. In practical applications, dibutyl phosphite (DBP) is a commonly used phosphite - type extreme - pressure anti - wear additive.
Phosphate Esters
Neutral phosphate esters are generally prepared from phosphorus oxychloride and corresponding alcohols or phenols. Acidic phosphate esters are often prepared by incomplete esterification of phosphorus pentoxide and alcohols or phenols under anhydrous conditions. Compared with neutral phosphate esters, acidic phosphate esters have a stronger adsorption capacity on the metal surface and higher reactivity, so they have a greater anti - seizure load. However, acidic phosphate esters are more corrosive and likely to cause corrosive wear. Among many phosphate - type extreme - pressure anti - wear additives, tricresyl phosphate (TCP) is the most widely used. It has the advantages of low corrosiveness and good anti - wear performance and is often used in aviation engine oils, refrigeration oils, anti - wear hydraulic oils, etc.
Phosphorus - nitrogen - type Extreme - pressure Anti - wear Additives
Although acidic phosphate esters have good extreme - pressure and anti - wear performance, they have drawbacks such as high activity, strong corrosiveness, and poor phosphorus retention ability. To address these issues, organic amines are usually used to neutralize them, resulting in acidic phosphate ester ammonium salts with moderate activity. During the friction process, acidic phosphate ester ammonium salts undergo tribochemical reactions with the metal surface. The N element is adsorbed on the metal surface in the form of organic amines, while the P element generates inorganic phosphates. The two combine to form a complex boundary lubricating film. This lubricating film consists of a polyferrous phosphate layer and a phosphoric acid ammonium layer. The ammonium ion, as a counter - cation, can promote the growth of the phosphate boundary lubricating film, thus forming a relatively thick boundary lubricating film on the metal surface and demonstrating good extreme - pressure and anti - wear performance. The production process of acidic phosphate ester ammonium salts is simple, with less industrial "three - wastes" generated, and it has broad development prospects. It contains two active elements, phosphorus and nitrogen (also known as phosphorus - nitrogen agents), and thus has good extreme - pressure, anti - wear, anti - corrosion, anti - rust, and anti - oxidation properties. It is widely used in industrial lubricating oils, vehicle gear oils, lubricating greases, etc. Common acidic phosphate ester ammonium salt additives include dodecyl butyl isooctyl phosphate.
Sulfur - phosphorus - type Extreme - pressure Anti - wear Additives
The phosphorus element shows significant effects under low - speed and high - torque working conditions but performs poorly under high - speed impact. On the other hand, the sulfur element is most effective under high - speed impact. To enhance the extreme - pressure performance of additives, active sulfur elements are often introduced into the molecular structure of phosphorus - containing agents, resulting in sulfur - phosphorus - type compounds. Triphenyl - thiophosphate (TPPT) is an extreme - pressure anti - wear additive that emerged in the late 1980s. It is mainly used in steam turbine oils, bearing and hydraulic transmission oils, refrigeration oils, etc. In the 1990s, attempts to apply this additive in aviation lubricating oils were successful.
Research shows that TPPT combines the advantages of phosphorus - based and sulfur - based extreme - pressure anti - wear additives. It can fully utilize the advantages of phosphorus - based additives under low - temperature and low - load conditions and can also better demonstrate the effects of sulfur - based additives under high - temperature and high - load conditions. Since alkyl phosphite esters have excellent extreme - pressure and anti - wear performance but high activity and poor thermal oxidation stability, Fu Xisheng et al. modified their structure using long - chain fatty alcohols and sulfiding agents, obtaining a new type of sulfur - phosphorus - type extreme - pressure anti - wear additive. This anti - wear additive not only has excellent extreme - pressure, anti - wear, and friction - reduction performance but also has excellent thermal oxidation stability and durability. Compared with dibutyl phosphite (T304), it has significantly improved thermal oxidation stability, friction - reduction performance, and durability.
Sulfur - phosphorus - nitrogen - type Extreme - pressure Anti - wear Additives
Sulfur - phosphorus - nitrogen - type additives (S - P - N agents) are a type of multi - functional additives whose molecular structures contain sulfur, phosphorus, and nitrogen active elements simultaneously. In lubricating oils and greases, dialkyl dithiophosphate ester ammonium salts and dialkyl dithiophosphate complex ester ammonium salts are commonly used as extreme - pressure anti - wear agents. The preparation process of dialkyl dithiophosphate complex ester ammonium salts is relatively complex.
First, phosphorus pentasulfide reacts with alcohol to generate thiophosphoric acid. Then, thiophosphoric acid reacts with diol or epoxide to form dialkyl dithiophosphate hydroxy derivatives. Subsequently, it reacts with phosphorus pentoxide to obtain acidic dialkyl dithiophosphate complex esters. Finally, organic amines are used to neutralize the acidic dialkyl dithiophosphate complex esters to obtain dialkyl dithiophosphate complex ester ammonium salts.
During the preparation process, the phosphorus content of the additive is increased through the re - esterification reaction of thiophosphate esters and phosphoric anhydride. The corrosiveness of the additive is reduced by using amines to neutralize acidic phosphate esters, enabling the additive to have appropriate extreme - pressure and anti - wear properties, oil - solubility, and chemical stability. Sulfur - phosphorus - nitrogen agents have good thermal stability and also have certain anti - oxidation and anti - rust properties. Under boundary lubrication conditions, they undergo tribochemical reactions. The phosphorus element forms a phosphate film on the friction surface, the sulfur element forms an iron sulfate - iron sulfide film on the friction surface, and the N element is only adsorbed on the metal surface in the form of organic amines. Under the combined action of these organic - inorganic films, sulfur - phosphorus - nitrogen agents exhibit good extreme - pressure and anti - wear performance. In addition, sulfur - phosphorus - nitrogen agents have very good compatibility and synergistic effects with isobutylene sulfide (T321) and are the main phosphorus - containing agents in the fourth - generation sulfur - phosphorus gear oils.
Sulfur - phosphorus - boron / Sulfur - phosphorus - nitrogen - boron - type Extreme - pressure Anti - wear Additives
Although sulfur - phosphorus - type or sulfur - phosphorus - nitrogen - type additives have good extreme - pressure and anti - wear performance, their friction - reduction performance is poor. Moreover, if the activity of sulfur and phosphorus elements is too high, it is likely to cause corrosive wear, leading to a decline in anti - wear performance. The boron element can form an adsorption film on the friction surface during the friction process, thus playing a role in friction - reduction and anti - wear. Therefore, introducing the boron element into sulfur - phosphorus - type or sulfur - phosphorus - nitrogen - type additives is beneficial for improving the anti - wear, friction - reduction, and other properties of the additives.
Sulfur - phosphorus - boron - type additives first obtain dialkyl dithiophosphate hydroxy derivatives from phosphorus pentasulfide, fatty alcohols, epoxides, or diols, and then react with boric acid through an esterification reaction to obtain dialkyl dithiophosphate hydroxy derivative borates. Research shows that dialkyl dithiophosphate hydroxy derivative borates have better friction - reduction performance and thermal stability compared to ZDDP. Sulfur - phosphorus - nitrogen - boron additives are borides obtained by reacting sulfur - phosphorus - nitrogen additives with boric acid.
Boron - containing Extreme - pressure Anti - wear Additives
Borates
Borates are high - efficiency, multi - functional, and environmentally friendly lubricating oil additives. They not only have good extreme - pressure, anti - wear, friction - reduction performance, thermal oxidation stability, anti - corrosion and anti - rust performance, but also are non - toxic and odorless. Especially in low - viscosity lubricating oils, their extreme - pressure and anti - wear performance is more outstanding. They have been applied in gear oils and engine oils, and their application effect in lubricating greases is particularly prominent. Borate extreme - pressure anti - wear agents are mainly divided into two categories: inorganic borates and organic borates. Traditional preparation methods for inorganic borates include grinding method and double - decomposition method, and more advanced preparation methods include ultrasonic emulsification method and supercritical fluid drying method, etc. By introducing alkyl groups into the structural units of borate radicals through chemical reactions, oil - soluble organic borates can be prepared.
Borate Esters
The exploration of borate esters as lubricating oil additives began in the middle of the last century. By the end of the last century, a large number of studies on the use of borate esters as friction - reduction and anti - wear additives were reported in US patents. The results showed that when borate esters were added to base oils at a proportion of 0.5% - 4.0%, the wear could be reduced by more than 5% - 50% in almost all cases.
As additives in lubricating oils, borate esters exhibit special and excellent tribological properties such as friction - reduction, anti - wear, anti - oxidation, anti - corrosion, non - toxicity, and odorlessness, making them one of the research hotspots of green lubricating oil additives in recent years. There are many types of borate ester lubricating oil additives. The borate esters prepared in the early stage only contain elements such as B, C, O, and H. These types of borate esters have good friction - reduction and anti - wear performance and load - carrying capacity, and these properties increase with the growth of their molecular chains. However, they are prone to hydrolysis and are not easy to adsorb on the metal surface to form a lubricating film through tribochemical reactions. Therefore, when used alone, their comprehensive performance is poor, and their application is limited under increasingly complex working conditions. In recent years, with the deepening of research, active elements such as S, P, and N have gradually been introduced into the structure of organic borate esters. The introduction of these active elements is beneficial for improving the comprehensive performance of borate esters, such as extreme - pressure, anti - wear, friction - reduction, anti - oxidation, and anti - corrosion. At the same time, it also has a certain positive effect on improving the hydrolysis stability, storage stability, and oil - solubility of borate ester additives. In borate esters, B is an electron - deficient element. Its empty P orbital can capture the d or f orbital electrons or externally excited electrons of the metal friction pair, enriching on the friction surface to form a dense adsorption film, which plays a good role in friction - reduction and anti - wear. As the load increases, these enriched and adsorbed borides react with the metal on the friction surface through tribochemical reactions to form Fe₂B and FeB reaction films. In addition, active elements such as S, P, and N in borate esters also form inorganic reaction films such as FeSO₄, FeS, FePO₄ or nitrogen - containing organometallic complex films on the friction surface under the action of the load. It is under the synergistic action of these organic - inorganic films that borate esters exhibit good extreme - pressure, anti - wear, and friction - reduction effects.
Metal - salt - based Extreme - pressure Antioxidants
Molybdenum - containing Extreme - pressure Anti - wear Additives
Molybdenum - containing extreme - pressure anti - wear additives have been widely used in engine oils, steam turbine oils, gear oils, and lubricating oils (greases) of various machines due to their excellent tribological properties. Molybdenum - salt - based extreme - pressure anti - wear agents mainly include series products such as molybdenum dialkyl dithiophosphate sulfide oxide (MoDTP) and molybdenum dialkyl dithiocarbamate (MoDTC). Their mechanism of action has always been a research hotspot in the modern friction field. Research shows that under harsh working conditions such as high temperature, high speed, and high pressure, molybdenum - type extreme - pressure anti - wear agents decompose into nano - scale MoS₂ chemical reaction films. This protective film has super hardness and lubrication performance, can fill the concave and convex surfaces of the friction pair, relieve friction resistance, reduce the mechanical friction coefficient, and multiply the extreme - pressure performance.
Zinc Salts
Zinc dialkyl dithiophosphate (ZDDP) is known as a multi - effect additive and has excellent properties such as anti - oxidation, anti - corrosion, and anti - wear. It is widely used in internal combustion engine oils, anti - wear hydraulic oils, industrial oils, etc. Its mechanism of action is as follows: when the temperature is below 40°C, ZDDP undergoes physical adsorption on the friction surface. When the temperature reaches 60°C, chemical changes begin to occur, and Zn is transferred from the surface to the oil phase. When the temperature reaches 176°C, ZDDP decomposes upon heating, releasing hydrogen sulfide, sulfides, thiols, and disulfides. These react with the inorganic film formed on the friction surface and the zinc - based sulfurized phosphate to polymerize into a high - polymer film. The high - polymer film formed by the polymerization reaction on the micro - convex bodies of the friction surface has good anti - wear properties.
Over - based Sulfonates
Over - based sulfonates (Ca, Na, Ba) also have good extreme - pressure and anti - wear effects during metal cutting, especially when used in combination with chlorine - based and sulfur - based extreme - pressure anti - wear agents, the synergistic effect is more obvious. Since these additives do not corrode metals, do not pollute the environment, and also have certain functions such as detergency, dispersion, acid neutralization, and anti - corrosion, they are also called inert extreme - pressure anti - wear agents. It should be noted that PEP additives are not the same as the sulfonate detergents used in internal combustion engine oils. As a type of inert additive, over - based sulfonates do not form a reaction film by reacting with the friction surface during the friction process. Instead, they form a carbonate protective film covering the friction surface. This film has a low shear strength, which can reduce friction and prevent welding between the friction pairs.
In conclusion, different types of extreme - pressure anti - wear additives have their own characteristics in terms of composition, performance, and mechanism of action. In practical applications, appropriate extreme - pressure anti - wear additives should be selected according to specific working conditions and the requirements of lubricating oils to fully utilize their performance advantages and ensure the normal operation of mechanical equipment.
The Price of EP/AW additives
The price of EP/AW additives depending on factors such as brand, specification, composition, and sales channels. If you are interested in EP/AW additives, please feel free to contact us.
Supplier of EP/AW additives
UNPChemicals is a professional supplier of high-quality and effective EP/AW additives. We offer several remarkable products, namely Amine-neutralized hexyl phosphate PSAIL 3490,Amine-neutralized mixed phosphate Esters PSAIL 2280,Phosphorothioate acrylate derivatives PSAIL 3530,etc.
Amine-neutralized hexyl phosphate PSAIL 3490 is a specialized mixture of amine phosphate salts known for its multifunctional ashless additive characteristics. As an ashless additive, PSAIL 3490 does not produce ash as combustion by-products, reducing engine deposits and harmful emissions. PSAIL 3490 is a multifunctional additive, providing a range of benefits in a single product, making it highly versatile and cost-effective.
Amine-neutralized mixed phosphate esters PSAIL 2280 is a multifunctional ashless additive structured as a phosphate ester amine salt with excellent load carrying capacity, anti-wear and corrosion protection properties. As a multifunctional additive, PSAIL 2280 reduces the amount of anti-emulsifier and rust inhibitor and has good tribological properties, especially at higher temperatures, forming thicker boundary lubricant films. In addition, PSAIL2280 is widely used in metalworking fluid formulations in conjunction with sulfur carriers because of its good anti-wear properties.
Phosphorothioate Acrylate Derivatives PSAIL 3530 is an ashless EP/AW additive with dialkyl dithiophosphate structure, especially suitable for industrial lubricating oils with FZG test requirements, such as industrial gear oil, anti-wear hydraulic oil containing ZDDP, lubricating grease and metal processing oil.
Professional Lubricant Additive Manufacturer
UNPChemicals, aka Luoyang Pacific United Petrochemical Co., Ltd., focuses on the application and development of special lubricating grease additives such as MODTC, MODTP, molybdenum amide, thiadiazole metal deactivators, and phosphate esters. With nearly 30 products in seven series, including extreme pressure anti-wear additives and special grease additives, it is a global manufacturer of special lubricating grease additives and a national high-tech enterprise with great influence and leading role in the industry. If you are looking for Lubricant Additive or technical information, feel free to contact UNPChemicals.