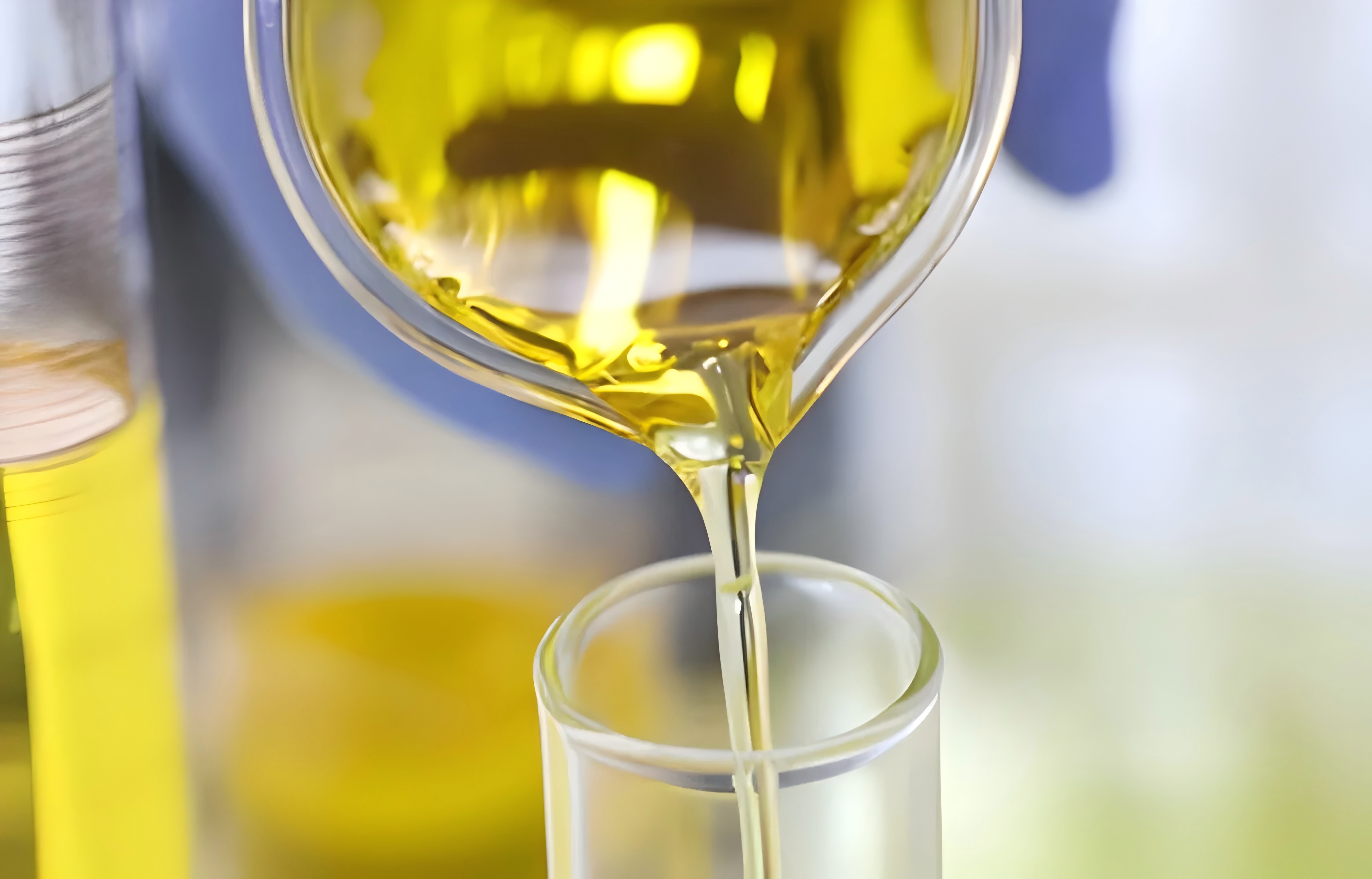
Differences between Foam Resistance and Air Release Property of Lubricating Oil
Although bubbles and foams in lubricating oil can have adverse effects on both the oil and equipment, it is inevitable for lubricating oil to contain some air during production, storage, transportation, and use. Some of the air is dissolved in the lubricating oil, showing no visible signs, so there seem to be no foams or bubbles on the surface. While some air is not dissolved and escapes, creating the bubbles and foams that are visible to the naked eye. Generally, the air dissolved in the lubricating oil is not harmful. The harmful part is mainly the free air in the lubricating oil, namely bubbles and foams.
What is a Lubricating Oil Defoamer?
A lubricating oil defoamer is a chemical additive specifically designed to eliminate the foams generated during the production, storage, and use of lubricating oil. During the circulation of lubricating oil, factors such as contact with air, mechanical agitation, and impurities in the system can easily cause foaming. If these foams are not eliminated in a timely manner, they can have various negative impacts on the performance of the lubricating oil and the operation of the equipment. The lubricating oil defoamer can quickly and effectively break and inhibit the formation of foams, ensuring that the lubricating oil can function properly.
Working Principles of Lubricating Oil Defoamers
Reducing Surface Tension: The formation of foams depends on the support of the liquid surface tension. The main components of lubricating oil defoamers usually have a lower surface tension than the lubricating oil. When the defoamer is added to the lubricating oil system containing foams, it rapidly disperses on the foam surface. With its lower surface tension, it reduces the local tension of the foam surface liquid film. Due to the uneven surface tension of the liquid film, the foam can no longer maintain its original shape, leading to its rupture. For example, in some silicone - based defoamers, the silicon - oxygen bonds in their molecular structure endow them with extremely low surface tension, enabling them to quickly penetrate into the foam liquid film and break the stability of the foam.
Displacement Effect: The defoamer molecules can also displace the foam - stabilizing substances on the foam surface. In a foam system, some surface - active substances adsorb on the foam surface, forming a liquid film with a certain strength to stabilize the foam. The defoamer molecules of lubricating oil have a stronger adsorption capacity and can displace these foam - stabilizing substances from the foam surface. Once the foam - stabilizing substances are replaced, the strength of the foam surface liquid film is greatly reduced, and under the action of external factors such as gravity and mechanical vibration, the foam is more likely to rupture.
Destroying Foam Elasticity: Foams have a certain elasticity and can resist external disturbances to maintain stability. Lubricating oil defoamers can destroy the elasticity of foams. During the spreading process on the foam surface, they thin the foam surface liquid film and reduce the elastic modulus of the liquid film. When the foam is squeezed or vibrated, the thinned and less elastic liquid film cannot return to its original state in time, resulting in the rupture of the foam.
Air in Lubricating Oil and Its Hazards
Air Dissolved in Lubricating Oil: Lubricating oil can dissolve a certain amount of air. Generally, mineral lubricating oil can dissolve about 9% of air.
Appearance: It is dissolved in the lubricating oil and shows no visible signs.
Cause of Generation: When the lubricating oil comes into contact with the air in the environment, the air naturally dissolves into the oil. The amount of air that can be dissolved in the lubricating oil depends on factors such as temperature, pressure, and the solubility of the lubricating oil itself to air.
Impact: Under normal circumstances, it does not cause adverse effects. However, when the temperature and pressure change significantly, the dissolved air will escape, causing bubbles to form in the oil that originally had no bubbles.
Foams and Bubbles in Lubricating Oil: These are the air that has not been dissolved in the lubricating oil, that is, the free air.
Appearance:The ones floating on the surface of the lubricating oil are foams, and some remain inside the lubricating oil liquid as bubbles.
Cause of Generation: Generally, it is because air is entrained into the lubricating oil to form bubbles, such as agitation during mechanical operation, air sucked in by the suction pipe, air leakage in the oil circuit and seals, and the rapid flow of the return oil pipe causing agitation and entraining air.
Impact: Foams and bubbles can cause lubrication problems and equipment problems. Hazards to the lubricating oil include accelerating the oxidative deterioration of the lubricating oil; destroying the integrity of the oil film, resulting in poor lubrication; increasing the compressibility of the oil. For example, in the case of hydraulic oil that plays a transmission role, the increased compressibility of the hydraulic oil causes problems in equipment operation. Bubbles are compressed in the high - pressure area, generating high temperatures, which cause the oil to deteriorate due to high temperatures (micro - dieseling); causing the lubricating oil to overflow; causing cavitation of the equipment; reducing the cooling property of the lubricating oil; affecting the stability of equipment operation, etc.
Hazards of Lubricating Oil Foams
Due to the many hazards caused by foams, the oil tank of the lubricating oil not only serves the functions of oil storage and heat dissipation but also helps to release bubbles. A larger - sized oil tank is beneficial for bubble release. In addition, there should be a sufficient distance between the return oil pipe and the suction pipe, and a baffle should be installed to separate them, which is conducive to bubble release and sedimentation of impurities. If necessary, a filter can be installed between the return oil area and the suction area to help release bubbles. If bubbles are entrained in the lubricating oil, they should float to the oil surface as soon as possible. If the release speed is slow, it will cause an increase in foams. The factors affecting the air release speed of lubricating oil are as follows:
Size of Bubbles: Larger bubbles are easier to escape, while small bubbles remaining inside the lubricating oil are more difficult to release and are very harmful.
Viscosity of Lubricating Oil: Lubricating oil with a higher viscosity has a lower air release speed than low - viscosity oil.
Temperature: Low temperature increases the viscosity of the lubricating oil and reduces the bubble release speed.
Oxidation of Lubricating Oil: The oxidative deterioration of the oil, including the degradation of the base oil and the depletion of additives, will affect the foam resistance of the lubricating oil.
Contamination of Lubricating Oil: Commonly, for example, when water enters the oil, the surface tension of the oil liquid will decrease. Instead of forming large bubbles that float to the liquid surface, they will break into small bubbles and suspend inside the oil liquid. Besides water, the mixing of other oil liquids or solvents into the lubricating oil will also affect its air release property.
Foam Resistance and Air Release Property of Lubricating Oil
The free air in the lubricating oil exists in two forms: bubbles remaining inside the oil liquid and foams floating on the oil surface. Bubbles floating to the oil surface become foams. The time required for bubbles to rise to the oil surface is called the air release property of the lubricating oil. For the foams floating on the oil surface, the time required for the foams to break and disappear is called the foam characteristic or foam resistance.
The air release property of lubricating oil cannot be improved by anti - foam agents, while the foam resistance can be improved by additives. Therefore, silicone anti - foam agents for defoaming or oil - soluble PAG cannot improve the air release property of lubricating oil. On the contrary, if too much anti - foam agent is added, it will significantly reduce the air release property of the lubricating oil, making it difficult for the bubbles in the lubricating oil to be released.
Reasons for Excessive Foams in Lubricating Oil
The reasons for excessive foams in lubricating oil can be divided into two categories: equipment - related reasons and reasons related to the lubricating oil itself.
Reasons Related to Lubricating Oil: High viscosity of the oil, decrease in oil temperature (which also increases the viscosity of the lubricating oil), contamination of the lubricating oil (by water, other oils, liquids, chemicals, impurities, etc.), oxidative deterioration of the lubricating oil (the oil deteriorates during use), depletion of additives - contamination of the lubricating oil can cause premature depletion of additives. In addition, the anti - foam agent may be filtered out by the filter element.
Reasons Caused by Equipment: Air leakage, poor sealing, air sucked in by the oil pipe, air entrained by agitation during mechanical operation, improper design of the oil tank, insufficient residence time of the oil in the oil tank, and too fast splashing speed of the lubricating oil, etc. In practical use, excessive foams are often caused by multiple reasons, so a comprehensive analysis is required. When solving the problem of excessive foams in lubricating oil, the correct method is to find the cause and solve it from the source instead of blindly adding anti - foam agents.
Detection Standards for the Air Release Property of Lubricating Oil
Common standards for the air release property of lubricating oil include ASTM D3427, ISO 9120, and IP 313. The detection methods used in these standards are the same. During the detection, under certain pressure and temperature, air is injected into a certain amount of oil sample to fill the lubricating oil with bubbles, and then the bubbles are allowed to dissipate. When the bubbles in the oil no longer dissipate and remain at a stable volume, the timing stops. The air release property of the lubricating oil is defined as the time (in minutes) required for the volume of bubbles in the oil sample to dissipate to only 0.2% (by volume) in this experiment, that is, the time required for the lubricating oil to release 99.8% of the air under certain conditions. The shorter the time, the better the air release property.
Different types of equipment have different requirements for the air release property of lubricating oil. Some equipment, such as hydraulic oil and turbine oil, has high requirements for the air release property of lubricating oil. International standards have clearly defined requirements for the air release property of these oils. After being put into use, the air release property is also an important detection indicator. When detecting the air release property of high - viscosity lubricating oil, the temperature is set at 75°C, which is higher than the detection temperature of general lubricating oils.
Detection Standards for the Foam Resistance of Lubricating Oil
Common detection standards for the foam resistance (foam generation characteristics) of lubricating oil include ASTM D892, ISO 6247, and IP 146. Under certain temperature and pressure conditions, air is pumped into the oil sample to fill the lubricating oil with bubbles. After the bubbles float to the oil surface, they will form foams. After 5 minutes, the air injection is stopped, and the volume of the generated foams is immediately recorded when the air pump is turned off. Ten minutes after the air pump is turned off, the volume of the foams is recorded again. The recorded volumes are taken as the experimental results. Therefore, the experimental results include two numbers, representing the foam volume respectively.
This experiment needs to measure the foam resistance of the lubricating oil at three temperatures: first at 24°C, then at 93.5°C, and finally at 24°C again. The foam resistance detection of each lubricating oil includes these three groups of experiments, and the steps of each group of experiments are the same and are carried out according to the detection method mentioned above.
Types of Lubricating Oil Defoamers
Silicone - based Defoamers: This is currently the most widely used type of lubricating oil defoamer. Silicone - based defoamers mainly consist of polysiloxane and have excellent defoaming performance. The silicon - oxygen bonds in their molecular structure endow them with extremely low surface tension, enabling them to quickly spread and penetrate on the foam surface, effectively destroying the stability of the foam. Silicone - based defoamers not only have a fast defoaming speed but also a long foam - inhibiting time, and they have good adaptability to various types of lubricating oils. In addition, they have high chemical stability, do not react chemically with the lubricating oil, are resistant to high temperatures and oxidation, and are suitable for defoaming lubricating oils under harsh working conditions such as high temperatures and high pressures. For example, in the lubricating oil systems of some large - scale industrial equipment, silicone - based defoamers can stably play a defoaming role for a long time.
Polyether - based Defoamers: Polyether - based defoamers are polymerized from monomers such as ethylene oxide and propylene oxide. They have good water solubility and dispersibility and can quickly disperse in the lubricating oil and play a defoaming role. The defoaming performance of polyether - based defoamers is less affected by temperature and can maintain a relatively stable defoaming effect under different temperature conditions. At the same time, they are highly environmentally friendly and have good biodegradability, meeting environmental protection requirements. In some industries with high environmental protection requirements, such as food processing and pharmaceuticals, polyether - based defoamers are widely used in the lubricating oils. Because they will not contaminate the products and can effectively eliminate the foams generated during the production of lubricating oil.
Mineral Oil - based Defoamers: Mineral oil - based defoamers are made by using mineral oil as the base and adding some additives such as surfactants. They have the characteristics of low cost and good defoaming effect. Mineral oil - based defoamers can form an oil film on the foam surface, preventing the merging and growth of foams. At the same time, they reduce the surface tension of the foam surface, promoting the rupture of the foam. However, the disadvantage of mineral oil - based defoamers is that they are easy to volatilize at high temperatures, and their defoaming persistence is relatively poor. Therefore, they are usually suitable for some lubricating oil application scenarios where the temperature is not too high and the requirement for the persistence of the defoamer is not particularly strict, such as in the lubricating oils of some ordinary machining equipment.
Significance of Lubricating Oil Defoamers
Ensuring Normal Equipment Operation: The presence of foams seriously affects the lubricating performance of the lubricating oil. Foams can make the fluidity of the lubricating oil worse, preventing it from effectively forming a continuous lubricating film on the friction surface, resulting in increased equipment wear. Equipment operating in a foam environment for a long time will have a significantly shortened service life of its components and may even cause equipment failures. Using a lubricating oil defoamer can promptly eliminate foams, ensuring that the lubricating oil can fully exert its lubricating function, reducing equipment wear, extending the service life of the equipment, and ensuring the normal and stable operation of the equipment. This is of great significance for some large - scale and expensive industrial equipment, as it can avoid production stoppages and economic losses caused by equipment failures.
Improving Production Efficiency: In the industrial production process, if the foams in the lubricating oil cannot be eliminated in a timely manner, it will affect the continuity and stability of production. For example, on some automated production lines, the foams in the lubricating oil may cause blockages in the lubrication system, affecting the normal supply of the lubricating oil and thus preventing the production equipment from operating normally. After adding a lubricating oil defoamer, production interruptions caused by foam problems can be effectively avoided, ensuring the smooth progress of the production process and improving production efficiency. In addition, the use of defoamers can also reduce the equipment maintenance and cleaning work required due to foam problems, further saving production time and costs.
Enhancing Product Quality: In some industries with extremely high requirements for product quality, such as electronics and precision machinery manufacturing, if the foams in the lubricating oil remain on the product surface, they may affect the appearance and performance of the product. For example, in the manufacturing process of electronic products, the foams in the lubricating oil may contaminate the electronic components, resulting in a decline in the electrical performance of the components. Using a lubricating oil defoamer can ensure the purity of the lubricating oil, avoid product contamination caused by foams, and thus enhance the product quality to meet the strict requirements of the high - end market for product quality.
The Price of Special additives
The price of Special additives depending on factors such as brand, specification, composition, and sales channels. If you are interested in Special additives, please feel free to contact us.
Supplier of Special additives
UNPChemicalsis a professional supplier of high-quality and effective Special additives. We offer several remarkable products, namely Sulfolane type seal expansion agent DMET 7300,etc.
Sulfolane type seal expansion agent DMET 7300 is a Sulfolane-type sealing expansion agent that enhances the performance of various base oils and rubber sealing materials. DMET 7300 is a high perfomance seal swell additive offering several advantages, such as low dosage requirements, high resistance against hydrolysis, and superior sealing performance in a wide range of rubber sealing materials.
Professional Lubricant Additive Manufacturer
UNPChemicals, aka Luoyang Pacific United Petrochemical Co., Ltd., focuses on the application and development of special lubricating grease additives such as MODTC, MODTP, molybdenum amide, thiadiazole metal deactivators, and phosphate esters. With nearly 30 products in seven series, including extreme pressure anti-wear additives and special grease additives, it is a global manufacturer of special lubricating grease additives and a national high-tech enterprise with great influence and leading role in the industry. If you are looking for Lubricant Additive or technical information, feel free to contact UNPChemicals.
Conclusion
Lubricating oil defoamers play an indispensable role in industrial production and equipment maintenance. By deeply understanding their working principles, types, and significance, we can more scientifically and rationally select and use lubricating oil defoamers, give full play to their functions, ensure the performance of lubricating oil, and promote the efficient and stable development of industrial production.