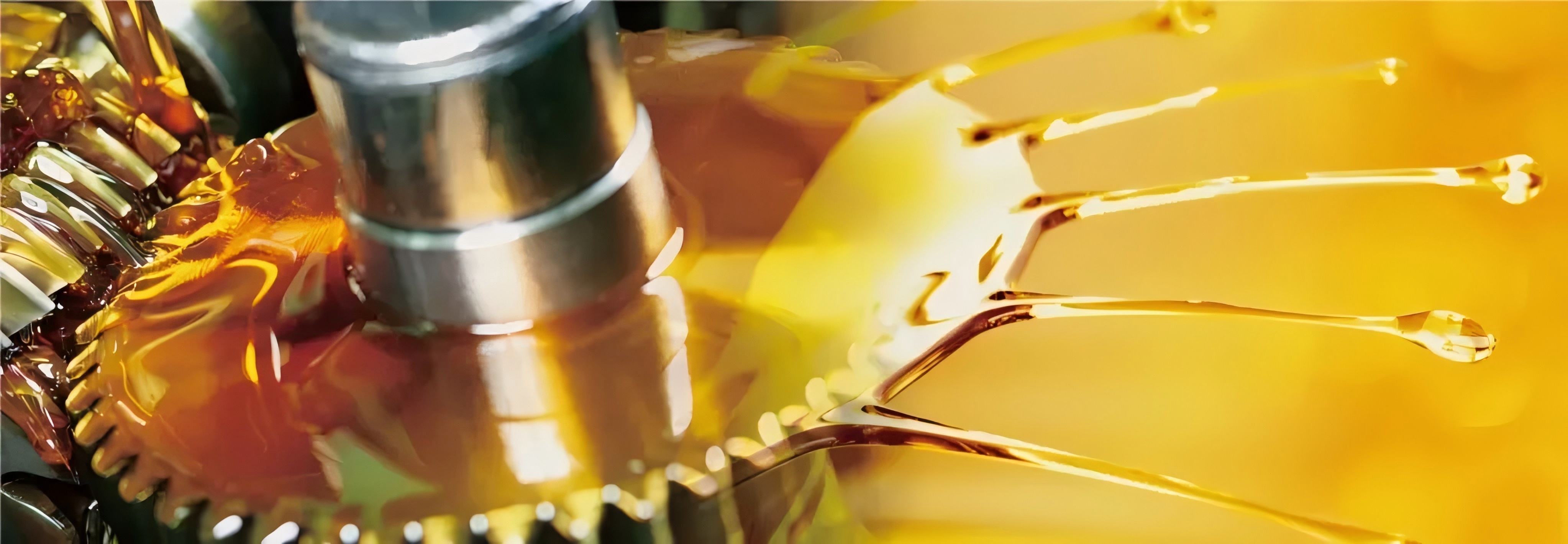
Application of Extreme Pressure Anti - wear Additives in Lubricating Oil Products
What is an Extreme Pressure Anti - wear Additive?
The smooth operation of mechanical equipment relies on the support of lubricating oil. High - quality lubricating oil can effectively reduce friction and wear between mechanical components, lower energy consumption, improve mechanical efficiency, and extend the service life of equipment. It is estimated that approximately 30% of energy is consumed due to friction, and 80% of component damage is caused by friction and wear. Therefore, improving the lubrication performance of oil products is of great economic significance for reducing friction, wear, and preventing sintering. In lubricating oil products, extreme pressure anti - wear agents (Extreme Pressure - Antiwear Additive; EP/AW Additive) are often added to improve the tribological properties of base oils, reduce the resistance between friction pairs, decrease wear and scuffing, and enhance the load - bearing capacity of lubricating oils.
The Role of Extreme Pressure Anti - wear Additives
Extreme pressure anti - wear agentsare mainly used to prevent problems such as scratching, galling, wear, and sintering and welding. They are suitable for harsh lubrication environments such as high - speed, high - temperature, and high - load conditions. Nowadays, a large number of extreme pressure anti - wear agents have been commercially produced, sold, and applied.
Types of Extreme Pressure Anti - wear Additives
Extreme pressure anti - wear agents are usually divided into two categories: active and non - active. Active extreme pressure anti - wear agents have active elements such as sulfur (S), phosphorus (P), and chlorine (Cl) in their molecular structures. Their mechanism of action is that the additive molecules first adsorb on the surface of the metal friction pair. Under high - temperature and high - load conditions, the active elements in the molecules react with the metal to form a protective layer with low shear strength, thus reducing friction and wear on the metal surface. Non - active extreme pressure anti - wear agents form a protective film by depositing themselves or their decomposition products on the metal surface. Such additives mainly include boron - containing compounds, metal salts, etc.
Chlorine - containing Extreme Pressure Anti - wear Agents
Chlorine - containing extreme pressure anti - wear agents have low costs, good performance, and can synergistically enhance the effects with phosphorus - containing and sulfur - containing additives. They are one of the early - used extreme pressure anti - wear components in the lubricating oil industry. Common chlorine - containing extreme pressure anti - wear agents are aliphatic chlorides and aromatic chlorides. Their performance depends on the molecular structure and the chemical activity of chlorine atoms. When the chlorine atom is at the end of the aliphatic hydrocarbon, its activity is the highest, and the extreme pressure anti - wear performance is the best. When it is in the middle of the carbon chain, the activity is second - best. When it is on the carbon ring, the activity is the worst, and the corresponding extreme pressure anti - wear performance is the weakest.
Aliphatic chlorides have strong chemical activity and good extreme pressure anti - wear performance, but poor stability and are prone to corrode metals, such as chlorinated paraffin. Aromatic chlorides have good stability, low chemical activity, relatively weak extreme pressure anti-wear performance, but less corrosion, such as pentachlorobiphenyl. In recent years, with the enhancement of environmental awareness and the tightening of regulations, the use of chlorine - containing additives has gradually decreased due to their toxicity and corrosion problems. For example, chlorine - containing gear oils have been replaced by sulfur - phosphorus gear oils. When in use, chlorine-containing extreme pressure anti-wear agents first adsorb on the surface of the friction pair. As the load on the contact surface and the friction temperature increase, the chlorine-containing compounds decompose or the C-Cl chemical bond breaks, generating chlorine atoms or HCl, which react with the metal surface to form a protective film of FeCl₂ or FeCl₃, showing good anti - wear and extreme pressure effects.
The iron chloride film has a layered structure (similar to graphene and molybdenum disulfide), with low critical shear strength and a small friction coefficient. However, its heat - resistant strength is low, and it will break at 300°C - 400°C. When it encounters water, it will undergo a hydrolysis reaction, producing hydrochloric acid and iron hydroxide, thus losing its lubricating effect and causing chemical wear and corrosion. Therefore, corrosion inhibitors such as amines or alkaline sulfonates are often added to the formulation of chlorine - containing extreme pressure anti - wear agents. This type of additive is more effective when used in a water - free environment and below 350°C.
Sulfur - containing Extreme Pressure Anti - wear Agents
Research has found that the extreme pressure anti - wear performance of sulfur - containing compounds is closely related to the C - S bond energy in their molecular structures. The smaller the C - S bond energy, the easier it is to break during the friction process to form a protective film, achieving better extreme pressure anti - wear effects.
The mechanism of action of sulfur - containing extreme pressure anti - wear agents is that they first adsorb on the surface of the friction pair, reducing the friction resistance. As the load increases, the temperature between the friction pairs rises sharply, and the sulfur - containing compound reacts with the metal to form an iron thiolate film, playing an anti - wear role. When the load further increases, the C - S bond breaks, generating an FeS extreme pressure chemical reaction film, which can prevent scuffing and sintering.
Due to the high melting point of iron sulfide (1193°C - 1199°C) and good heat - resistant performance, sulfur - containing extreme pressure anti - wear agents have a high sintering load. However, the iron sulfide film does not have the layered structure of films such as graphite, molybdenum disulfide, and iron chloride, and its friction - reducing performance is poor. At the same time, although the iron sulfide film has a high melting point and hardness, it is brittle, and the corrosive wear of sulfur - containing compounds is relatively strong, resulting in relatively weak anti - wear performance of sulfur - containing additives.
Sulfur - containing additives are suitable for harsh working conditions such as high - temperature and high - load due to the high melting point of the iron sulfide film and good extreme pressure performance. They are commonly used extreme pressure anti - wear additives in lubricating greases. Currently, commonly used sulfur - containing extreme pressure anti - wear agents include sulfurized olefins, sulfurized oils (esters), polysulfide compounds, dibenzyl disulfide, and xanthates.
Sulfurized Olefins
Among sulfurized olefin additives, sulfurized isobutylene (Sulfurized isobutylene, SIB) is the most widely used. It has good oil - solubility, high sulfur content (40% - 48%), and excellent extreme pressure performance. It is widely used in gear oils, hydraulic oils, lubricating greases, metalworking fluids, etc., and is also the sulfur - containing extreme pressure anti - wear additive with the largest usage amount. The synthesis methods of sulfurized isobutylene can be divided into two categories according to the production process: the traditional two - step method and the one - step method.
The traditional two - step method for preparing sulfurized isobutylene includes two steps: the sulfur - chlorination of isobutylene and the sulfurization and dechlorination. Using isobutylene, sulfur monochloride, sulfur, alkali metal or alkaline earth metal sulfides, etc. as the main raw materials, under the action of a catalyst, through an addition reaction and a sodium sulfide dechlorination reaction, and finally through alkali refining, a product with a sulfur mass fraction of 40% - 45% is obtained. The one - step method (high - pressure method) for preparing sulfurized isobutylene is to first add sulfur powder and a catalyst to a high - pressure reaction kettle in a certain proportion, heat the system to a specified temperature, then pump isobutylene into the reaction kettle for reaction. After the reaction, cool it to room temperature. Purge the kettle with air for 0.5 hours, then release the crude product. The crude product is separated, washed with water, dehydrated, and filtered to obtain the high - pressure sulfurized olefin product.
The one - step method (high - pressure method) using sulfur powder and isobutylene to prepare sulfurized isobutylene in the presence of a catalyst has a simple process, low pollution, and low production cost. The product has low viscosity, light color, and low irritating odor. Research shows that the sulfurized isobutylene prepared by the one - step method has higher activity, better extreme pressure anti - wear performance, and better oxidation stability.
Sulfurized Oil Esters
Sulfurized lard oil (Sulfurized Lard Oil) is an early - widely - used sulfur - containing additive in lubricating oil products. It is a sulfurized animal triglyceride with high viscosity, good adhesion, and good extreme pressure anti - wear performance. Later research found that whale oil is mainly composed of monoesters of long - chain unsaturated fatty acids and long - chain unsaturated fatty alcohols, which is different from most natural animal and vegetable oil esters. Therefore, sulfurized whale oil (Sulfurized Whale Oil) has better oil - solubility, thermal stability, and extreme pressure anti - wear performance, and is widely used in gear oils, metalworking fluids, hydraulic oils, lubricating greases, etc. However, since the commercial whaling ban, sulfurized whale oil has gradually been replaced by other sulfur - containing additives such as sulfurized vegetable oils and sulfurized long - chain α - olefins.
Sulfurized oil esters can be prepared by the addition reaction of elemental sulfur or hydrogen sulfide with the unsaturated bonds in the oil esters. The product prepared from elemental sulfur has a deep color and a strong irritating odor, while the product prepared from hydrogen sulfide has a light color and a low irritating odor. The extreme pressure performance of sulfurized oil esters is related to the content of active sulfur in their molecular structures. The higher the active sulfur content, the better the extreme pressure performance, but at the same time, it will also increase the corrosion of metals and the corrosive wear of friction pairs.
Polysulfide Compounds
Polysulfide additives mainly consist of alkyl trisulfide compounds. The tribological properties of alkyl trisulfides are related to the length and configuration of the alkyl chain. Their properties decrease as the alkyl chain length increases, such as n - butyl trisulfide > n - octyl trisulfide > n - dodecyl trisulfide. The performance of branched - chain alkyl trisulfides is better than that of straight - chain alkyl trisulfides, such as tert - butyl trisulfide < isobutyl trisulfide < n - butyl trisulfide.
Polysulfide compounds have a high sulfur content and good extreme pressure anti - wear performance, and can be applied to gear oils, metalworking fluids, lubricating greases, etc. However, this type of compound has poor stability and is prone to precipitating elemental sulfur during storage.
Benzyl Sulfide Compounds
Among benzyl sulfide additives, dibenzyl disulfide (dibenzyl disulfide, DBDS, commercial code T322) is relatively common. Its appearance is white crystals, which can be synthesized from benzyl chloride and Na₂S₂ or obtained by the oxidation of benzyl mercaptan. Dibenzyl disulfide has a sulfur content of 24 - 26% and good extreme pressure anti - wear performance. It can be compounded with other functional additives to formulate gear oils, hydraulic oils, lubricating greases, etc. However, its poor oil - solubility limits its wide application.
In recent years, to solve the problem of the oil - solubility of dibenzyl disulfide, polyalkyl benzyl sulfide has been developed. This product has a light yellow to brown - yellow liquid appearance, good oil - solubility and extreme pressure anti - wear performance, and can be used in gear oils, oil - film bearing oils, and metalworking fluids.
Xanthate Compounds
The structure of the xanthate group is similar to that of the traditional friction - active functional group, the dithiophosphate group. And the sulfur content of the compound can be increased by adjusting the length of the alkyl chain to meet the requirements of different working conditions for the extreme pressure and anti - wear performance of the additive.
The Price of EP/AW additives
The price of EP/AW additives depending on factors such as brand, specification, composition, and sales channels. If you are interested in EP/AW additives, please feel free to contact us.
Supplier of EP/AW additives
UNPChemicals is a professional supplier of high-quality and effective EP/AW additives. We offer several remarkable products, namely Amine-neutralized hexyl phosphate PSAIL 3490,Amine-neutralized mixed phosphate Esters PSAIL 2280,Phosphorothioate acrylate derivatives PSAIL 3530,etc.
Amine-neutralized hexyl phosphate PSAIL 3490 is a specialized mixture of amine phosphate salts known for its multifunctional ashless additive characteristics. As an ashless additive, PSAIL 3490 does not produce ash as combustion by-products, reducing engine deposits and harmful emissions. PSAIL 3490 is a multifunctional additive, providing a range of benefits in a single product, making it highly versatile and cost-effective.
Amine-neutralized mixed phosphate esters PSAIL 2280 is a multifunctional ashless additive structured as a phosphate ester amine salt with excellent load carrying capacity, anti-wear and corrosion protection properties. As a multifunctional additive, PSAIL 2280 reduces the amount of anti-emulsifier and rust inhibitor and has good tribological properties, especially at higher temperatures, forming thicker boundary lubricant films. In addition, PSAIL2280 is widely used in metalworking fluid formulations in conjunction with sulfur carriers because of its good anti-wear properties.
Phosphorothioate Acrylate Derivatives PSAIL 3530 is an ashless EP/AW additive with dialkyl dithiophosphate structure, especially suitable for industrial lubricating oils with FZG test requirements, such as industrial gear oil, anti-wear hydraulic oil containing ZDDP, lubricating grease and metal processing oil.
Professional Lubricant Additive Manufacturer
UNPChemicals, aka Luoyang Pacific United Petrochemical Co., Ltd., focuses on the application and development of special lubricating grease additives such as MODTC, MODTP, molybdenum amide, thiadiazole metal deactivators, and phosphate esters. With nearly 30 products in seven series, including extreme pressure anti-wear additives and special grease additives, it is a global manufacturer of special lubricating grease additives and a national high-tech enterprise with great influence and leading role in the industry. If you are looking for Lubricant Additive or technical information, feel free to contact UNPChemicals.