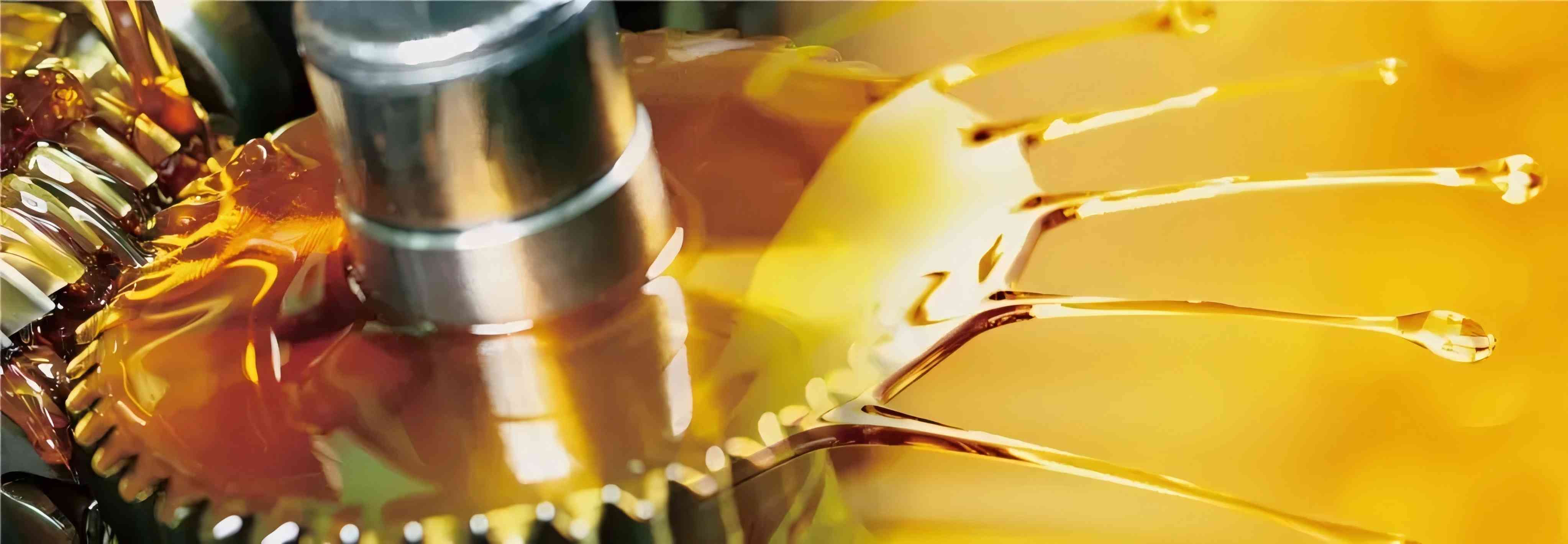
Composition Analysis of Industrial Gear Oil Additive Package
In modern industrial production, gears, as a crucial mechanical transmission component, are widely applied in various equipment. From large industrial machinery to precision instruments, their efficient and stable operation is of vital importance for the smooth progress of the entire production process. The industrial gear oil additive package, as the core material ensuring the normal operation of gears, plays an irreplaceable and key role in the field of gear lubrication.
During the operation of industrial gears, the tooth surfaces bear extremely high pressures and frictional forces. At the same time, they are also affected by various complex working conditions such as temperature changes and oxidation. Without effective lubrication and protection, gears are highly prone to failure modes such as wear, scuffing, and fatigue. This not only reduces the operating efficiency of the equipment and increases energy consumption but may even lead to equipment failure and shutdown, causing huge economic losses to enterprises. Through its unique formulation design, the industrial gear oil additive package can form a firm and stable lubricating film on the gear tooth surface, effectively reducing the friction coefficient between the tooth surfaces, minimizing wear, and at the same time, improving the load-bearing capacity of the gears and extending their service life, ensuring that the equipment can operate reliably under various harsh working conditions. Therefore, a deep understanding of the composition and action mechanisms of the industrial gear oil additive package is of great significance for optimizing the gear lubrication scheme and enhancing the reliability and economic efficiency of industrial production.
Types and Functions of Extreme Pressure Agents in Industrial Gear Oil Additive Package
When industrial gears face heavy-duty working conditions, extreme pressure agents become an indispensable and key component in the industrial gear oil additive package. There are various common extreme pressure agents, mainly including sulfur-containing, phosphorus-containing, and chlorine-containing compounds.
Sulfur-containing extreme pressure agents are represented by sulfides, such as sulfurized olefins and sulfurized fatty acid esters. Under heavy-duty conditions, when the pressure between the gear tooth surfaces is extremely high and the ordinary lubricating oil film is difficult to maintain, the sulfur atoms in the sulfur-containing extreme pressure agents can chemically react with the metal surface to form a layer of iron sulfide protective film. This protective film has good anti-shear performance and can withstand extremely high pressures, effectively preventing direct contact between the tooth surface metals and thus avoiding serious wear and scuffing phenomena. For example, in the gear transmission systems of large mining machinery and heavy-duty transportation vehicles, sulfur-containing extreme pressure agents can ensure the normal operation of the tooth surfaces when the gears bear huge loads, guaranteeing the continuous and stable operation of the equipment.
Phosphorus-containing extreme pressure agents mainly include phosphates and their derivatives. Under heavy-duty working conditions, phosphates will decompose under the action of high temperature and high pressure to generate active phosphorus atoms. These phosphorus atoms will react with the metal surface to form a hard phosphide film with a low friction coefficient. This phosphide film can not only significantly improve the load-bearing capacity of the gears but also, to a certain extent, repair the minor damages on the tooth surfaces, further reducing wear. In the gearboxes of large rolling mills in the steel industry, phosphorus-containing extreme pressure agents can effectively cope with the huge rolling forces that the gears bear during the steel rolling process, ensuring the efficient operation of the rolling mills.
Chlorine-containing extreme pressure agents, such as chlorinated paraffin, in a heavy-duty environment, the chlorine atoms will adsorb and chemically react with the metal surface to form a chloride protective film. This protective film has excellent anti-seizure performance under high loads and can effectively prevent the gear tooth surfaces from sticking together under heavy loads. In some ship propulsion systems with extremely high requirements for the load-bearing capacity of gears, chlorine-containing extreme pressure agents can provide reliable protection for the gears, ensuring the safe navigation of ships under various complex sea conditions.
Types and Functions of Anti-wear Agents in Industrial Gear Oil Additive Package
Anti-wear agents play a crucial role in reducing wear in the industrial gear oil additive package. Common anti-wear agents mainly include organic molybdenum compounds, borate-based anti-wear agents, and fatty acid-based anti-wear agents.
Organic molybdenum compounds, such as molybdenum dialkyldithiophosphate (MoDDP), have a unique chemical structure and excellent anti-wear performance. During the operation of gears, MoDDP will form a protective film on the tooth surface composed of molybdenum sulfide and phosphide. This protective film not only has good lubricity, which can reduce the friction coefficient between the tooth surfaces but also can effectively fill the minor pits and scratches on the tooth surface, reducing wear. Research shows that after using industrial gear oil containing organic molybdenum anti-wear agents, the wear amount of gears can be significantly reduced, especially under medium and low load conditions, and its anti-wear effect is more obvious. For example, in the gear transmission systems of some precision machine tools, organic molybdenum anti-wear agents can ensure low wear of the gears during high-precision operation, guaranteeing the long-term stability of the machining accuracy of the machine tools.
Borate-based anti-wear agents have attracted much attention due to their unique anti-wear mechanisms. Borates will undergo a series of reactions such as hydrolysis in the lubricating oil to generate substances with lubricating properties such as borate esters. These substances can form an adsorption film with high strength and toughness on the tooth surface. This film can effectively buffer the impact force between the tooth surfaces and reduce wear. At the same time, borates also have certain anti-corrosion properties and can protect the tooth surfaces from being eroded by some corrosive media. In the gear transmissions of some chemical equipment, due to the possible presence of corrosive gases or liquids in the environment, borate-based anti-wear agents can simultaneously play the dual roles of anti-wear and anti-corrosion, extending the service life of the gears.
Fatty acid-based anti-wear agents are a relatively common and cost-effective type of anti-wear agents. The carboxyl groups in fatty acid molecules can physically and chemically adsorb onto the metal surface, forming a layer of fatty acid film with directional arrangement on the tooth surface. This film has good lubricity and can reduce the friction and wear between the tooth surfaces. In the gear lubrication of some small industrial equipment that is more sensitive to costs, such as the gearboxes of small motors, fatty acid-based anti-wear agents have been widely used. They can meet the basic anti-wear requirements while reducing the cost of the lubricating oil.
Types and Functions of Antioxidants in Industrial Gear Oil Additive Package
During the use of industrial gear oil, it will inevitably come into contact with air. Under the influence of factors such as high temperature and metal catalysis, it will undergo oxidation reactions, resulting in the aging and deterioration of the oil products and a decline in their performance. The addition of antioxidants can effectively inhibit the oxidation process of the oil products and extend their service life. Common antioxidants are mainly divided into phenolic antioxidants and amine antioxidants.
Phenolic antioxidants, such as dibutylhydroxytoluene (BHT), etc., belong to chain-terminating antioxidants. Their action mechanism is that the active hydrogen atoms in the phenolic antioxidant molecules can combine with the free radicals generated during the oxidation process of the oil products, interrupting the oxidation chain reaction and thus preventing the further oxidation of the oil products. Phenolic antioxidants have good antioxidant performance and can effectively inhibit the oxidation of the oil products in low and medium temperature environments. For example, in the gearboxes of some industrial equipment operating at room temperature, adding phenolic antioxidants can significantly delay the oxidation rate of the oil products, reduce the acidic substances and gums generated by the oil due to oxidation, and ensure the long-term stability of the lubricating performance of the oil products.
Amine antioxidants, such as N,N'-di-sec-butyl-p-phenylenediamine, etc., also belong to chain-terminating antioxidants. Compared with phenolic antioxidants, amine antioxidants have more excellent antioxidant performance in high temperature environments. Under high temperature conditions, the nitrogen atoms in the amine antioxidant molecules can react with free radicals to form stable compounds, thus terminating the oxidation chain reaction. In some industrial gear systems operating at high temperatures, such as the gear transmission devices of cement rotary kilns, due to the large amount of heat generated during the operation of the gears and the high oil temperature, at this time, amine antioxidants can give full play to their advantages and effectively inhibit the oxidation of the oil products at high temperatures, ensuring that the gear oil can still maintain good performance in harsh high temperature environments.
In addition, there are some auxiliary antioxidants, such as phosphite esters, etc. Phosphite ester-based auxiliary antioxidants mainly decompose the peroxides generated during the oxidation process of the oil products and convert them into harmless substances, thus playing an antioxidant role. When it is used in combination with phenolic and amine antioxidants, a synergistic effect can be produced, further improving the overall antioxidant performance of the antioxidants and extending the service life of the industrial gear oil.
Auxiliary Functions of Other Additives in Industrial Gear Oil Additive Package
In addition to the above-mentioned extreme pressure agents, anti-wear agents, and antioxidants, the industrial gear oil additive package also contains various other additives, and viscosity improvers are an important category among them.
Viscosity improvers mainly include polymethyl methacrylate (PMA), ethylene-propylene copolymer (OCP), etc. Their main function is to improve the viscosity-temperature performance of industrial gear oil. Under different working temperatures, the gear oil needs to maintain an appropriate viscosity to ensure good lubrication effects. In a low temperature environment, the viscosity of the oil product will increase. If the viscosity is too high, it will lead to difficult gear starting and increased power loss; while in a high temperature environment, the viscosity of the oil product will decrease. If the viscosity is too low, it will be impossible to form a lubricating oil film with sufficient thickness on the tooth surface, which is likely to lead to increased wear. Viscosity improvers can have little influence on the interaction between the oil product molecules at low temperatures, enabling the oil product to still maintain a relatively low viscosity for easy starting; at high temperatures, the viscosity improver molecules will stretch, increasing the force between the oil product molecules, so that the viscosity of the oil product will not decrease too much. For example, in some industrial equipment operating in cold regions and the gear transmission systems of metallurgical equipment working in high temperature environments, the industrial gear oil added with viscosity improvers can maintain an appropriate viscosity within a large temperature range, providing stable and reliable lubrication for the gears.
In addition, the industrial gear oil additive package may also contain detergents and dispersants, whose function is to disperse the gums, asphaltenes, and other pollutants generated during the oxidation process of the oil products into fine particles to prevent them from depositing on the gear surface and in the oil circuit system and keep the interior of the equipment clean. Rust inhibitors can form a protective film on the metal surface to prevent the gears from rusting due to contact with moisture, oxygen, etc. Antifoaming agents can inhibit the generation of excessive foam during the stirring process of the oil products, avoiding problems such as poor lubrication and accelerated oxidation of the oil products caused by the foam. These additives cooperate with each other to jointly provide guarantees for the performance improvement and stable operation of the industrial gear oil.
In conclusion, the composition of the industrial gear oil additive package shows remarkable diversity, and each component plays a crucial role in gear lubrication. Extreme pressure agents provide strong protection for the gears under heavy-duty working conditions, ensuring that the tooth surfaces do not suffer serious wear and scuffing under high pressures; anti-wear agents reduce the wear of the gears under various working conditions through different action mechanisms and extend the service life of the gears; antioxidants effectively inhibit the oxidation and aging of the oil products and maintain the long-term stability of the oil product performance; while other additives such as viscosity improvers assist in enhancing the comprehensive performance of the industrial gear oil from different aspects, such as improving the viscosity-temperature characteristics, keeping the equipment clean, preventing rust, and inhibiting foam.
It is the synergistic effect of these components that enables the industrial gear oil additive package to meet the gear lubrication requirements under various complex working conditions in modern industry and ensure the efficient and stable operation of industrial equipment. With the continuous development of industrial technology, the requirements for the performance of industrial gear oil additive packages will become higher and higher. Further in-depth research and optimization of their composition and development of industrial gear oil additive packages with more excellent performance and stronger adaptability are of great practical significance for promoting the progress of industrial production.
The Price of Additive Packages
The price of Additive Packages varies depending on factors such as brand, specification, composition, and sales channels. If you are interested in Additive Packages, please feel free to contact us.
Supplier of Additive Packages
UNPChemicals is a professional supplier of high-quality and effective Additive Packages. We offer several remarkable products, namely Industrial Gear Oil Additives UNP IG402A,High extreme pressure (EP) type industrial gear oil additive packages UNP IG402B,Low-Odor Type Industrial Gear Oil Additive Package UNP IG402C,etc.
Industrial Gear Oil Additives UNP IG402Aare a specialized class of compounds designed to enhance the performance of gear oils in various industrial applications.These additives are carefully formulated to provide a combination of properties that improve the efficiency,longevity,and reliability of gear systems.
High extreme pressure (EP) type industrial gear oil additive packages, like UNP IG402B, are specialized blends of chemical compounds designed to enhance the performance of base oils used in industrial gear lubricants. These packages are formulated to provide exceptional protection under conditions where gears experience heavy loads, high pressures, and potential metal-to-metal contact.
The Low-Odor Type Industrial Gear Oil Additive Package UNP IG402C is a specialized blend of chemical additives designed to enhance the performance of industrial gear oils while minimizing the strong odors typically associated with traditional gear oil additives, particularly those containing sulfur-based extreme pressure (EP) agents. This additive package is mixed with base oils (mineral or synthetic) to create gear lubricants that protect industrial gearboxes under demanding conditions, such as high loads and temperatures, while being more user-friendly in terms of smell—ideal for environments where odor control is a priority.
Professional Lubricant Additive Manufacturer
UNPChemicals,aka Luoyang Pacific United Petrochemical Co., Ltd., focuses on the application and development of special lubricating grease additives such as MODTC, MODTP, molybdenum amide, thiadiazole metal deactivators, and phosphate esters. With nearly 30 products in seven series, including extreme pressure anti-wear additives and special grease additives, it is a global manufacturer of special lubricating grease additives and a national high-tech enterprise with great influence and leading role in the industry. If you are looking for Lubricant Additive or technical information, feel free to contact UNPChemicals.