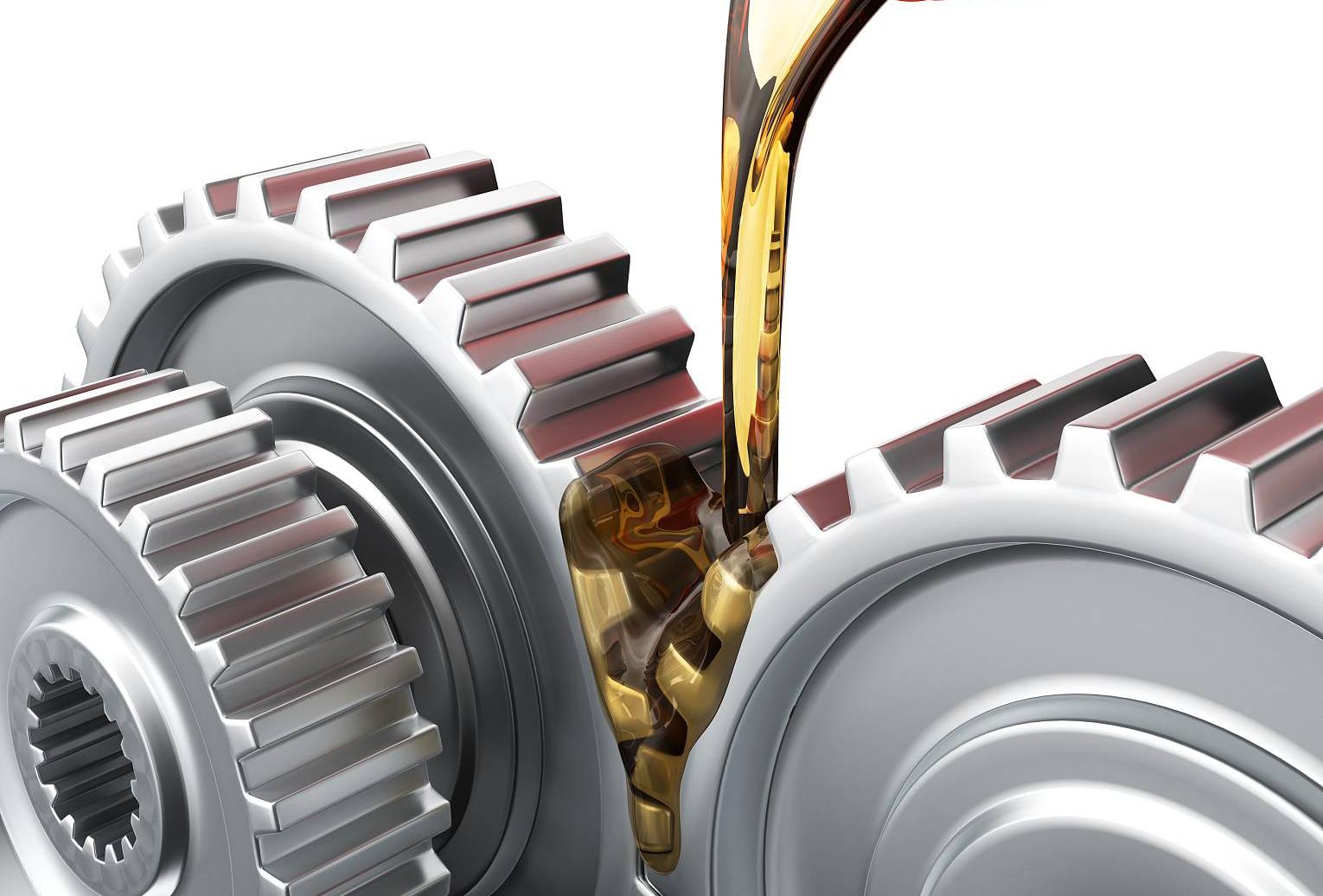
Performance Evaluation of Industrial Gear Oil Additive Packages
Industrial gear oil additive packages are an important part of the lubricant field, and their performance directly affects the operation efficiency and service life of gear systems. In industrial production, gear systems are widely used in various mechanical equipment. Especially under harsh working conditions such as heavy loads, high speeds, and high temperatures, extremely high requirements are placed on the performance of lubricating oils. Industrial gear oil additive packages significantly enhance the lubricating performance of base oils by adding various functional additives such as extreme pressure agents, anti-wear agents, and antioxidants, effectively meeting the special needs of gear systems.
Performance evaluation is a crucial link in ensuring the quality of industrial gear oil additive packages. Through scientific testing methods and standards, various performance indicators of the additive packages can be comprehensively evaluated, including extreme pressure performance, anti-wear performance, oxidation resistance performance, low-temperature fluidity, rust and corrosion prevention performance, and antifoaming performance. These performance indicators not only determine the effectiveness of the gear oil in practical applications but also directly relate to the reliability of the gear system and maintenance costs. Without scientific performance evaluation, the quality of the gear oil cannot be guaranteed, which may lead to wear, seizure, or even failures in the gear system during operation, thus affecting production efficiency and the service life of the equipment. Therefore, establishing a complete performance evaluation system plays an irreplaceable role in product quality control, product research and development, and market application.
Extreme Pressure Performance Testing Methods
Extreme pressure performance is one of the core indicators of industrial gear oil additive packages, reflecting the ability of the gear oil to prevent surface scuffing and seizure of gears under high-load conditions. In heavy-duty gear systems, the tooth surfaces of gears bear huge contact stresses, and the oil film is prone to rupture, resulting in direct contact between metal surfaces, which can then lead to scuffing or seizure. Extreme pressure agents react with the metal surface under high temperature and pressure to form a protective film, effectively avoiding these problems.
The FZG gear test is an internationally recognized method for evaluating extreme pressure performance and is widely used in the quality control and performance evaluation of industrial gear oils.
Test Principle: The FZG tester uses a pair of standard gears (usually type A gears) that operate under controlled temperature, rotational speed, and load. By gradually increasing the load until scuffing occurs on the gear surface, the failure load stage is recorded. The FZG test can simulate the actual working conditions of the gear system under high-load conditions and provide reliable performance data.
Test Steps:
1. Add the gear oil to be tested to the oil tank of the FZG tester.
2. Set the initial load stage (usually stage 1), rotational speed (1450 rpm), and temperature (90°C), and run for 15 minutes.
3. Check the condition of the gear surface. If there is no scuffing, increase the load stage by one level and repeat the running and checking process.
4. When scuffing marks wider than 0.5 mm appear on the gear tooth surface, record the current load stage as the failure load stage.
Evaluation Criteria: The higher the failure load stage of the FZG test, the better the extreme pressure performance of the gear oil. Generally, the FZG failure load stage of industrial gear oils should reach level 12 or above to meet the requirements of heavy-duty gear systems. For special application scenarios, such as wind turbine gearboxes, a higher failure load stage may be required.
In addition to the FZG test, the Timken test and the four-ball extreme pressure test are also commonly used methods for evaluating extreme pressure performance. The Timken test evaluates the extreme pressure performance by measuring the wear of the sample against a steel ring under a certain load; the four-ball extreme pressure test determines the extreme pressure performance by measuring the seizure load of steel balls under increasing loads. These methods can serve as supplements to the FZG test and provide multi-dimensional performance data.
Anti-wear Performance Testing Methods
Anti-wear performance is a key indicator of industrial gear oil additive packages to reduce gear wear under normal working conditions. Even under normal loads, the friction on the gear tooth surfaces will lead to wear, and long-term accumulation may cause a decrease in gear accuracy, an increase in noise, or even failure. Anti-wear agents form an adsorption film or reaction film on the metal surface to reduce the friction coefficient and wear.
The measurement of the wear scar diameter using a four-ball tester is a commonly used method for evaluating anti-wear performance.
Test Principle: The four-ball tester consists of a rotating steel ball and three fixed steel balls, and the gear oil to be tested is immersed between the fixed steel balls. The rotating steel ball comes into contact with the fixed steel balls under the set load to simulate the friction and wear of gears. The anti-wear performance of the gear oil is evaluated by measuring the wear scar diameter on the fixed steel balls.
Test Steps:
1. Add the gear oil to be tested to the oil bath of the four-ball tester.
2. Set the test conditions: load 392 N, rotational speed 1200 rpm, and running time 60 minutes.
3. After the test, measure the wear scar diameters on the three fixed steel balls and calculate the average value.
Evaluation Criteria: The smaller the wear scar diameter, the better the anti-wear performance of the gear oil. The wear scar diameter of industrial gear oils should generally be controlled below 0.3 mm to ensure the stability of gears during long-term operation. In addition, the anti-wear performance can be further verified by measuring the wear amount and friction coefficient.
In addition to the four-ball test, the Falex test and the SRV test are also commonly used for anti-wear performance evaluation. The Falex test evaluates the anti-wear performance by measuring the wear of the sample under increasing loads; the SRV test uses high-frequency reciprocating motion to simulate gear friction and provides test results that are closer to actual working conditions. These methods provide diversified options for a comprehensive evaluation of anti-wear performance.
Oxidation Resistance Performance Testing Methods and Standards
Oxidation resistance performance is an important indicator of industrial gear oil additive packages to resist oxidation and deterioration in high-temperature and high-oxygen environments. When the gear system is in operation, the oil temperature rises and comes into contact with the oxygen in the air, making the gear oil prone to oxidation, which generates acidic substances, sludge, and precipitates, thus affecting the lubricating performance and even damaging the gears. Antioxidants delay the oxidation process and extend the service life of the gear oil.
The rotating oxygen bomb method is a commonly used method for evaluating oxidation resistance performance.
Test Principle: Place the gear oil sample to be tested in a sealed oxygen bomb, add a certain amount of oxygen, and rotate it at a high temperature. The oxygen reacts with the gear oil through oxidation, consuming oxygen and causing the pressure to drop. The oxidation resistance performance is evaluated by recording the time it takes for the oxygen pressure to drop to a specified value.
Test Steps:
1. According to the ASTM D2272 standard, place the gear oil sample and the catalyst in the oxygen bomb.
2. Fill the oxygen bomb with oxygen to an initial pressure of 620 kPa and set the temperature to 150°C.
3. Start the rotation and record the time it takes for the oxygen pressure to drop to 175 kPa, which is called the rotating oxygen bomb time (RBOT).
Evaluation Criteria: The longer the rotating oxygen bomb time, the better the oxidation resistance performance of the gear oil. The RBOT time of industrial gear oils should generally reach more than 1000 minutes to ensure stability under high-temperature working conditions. The RBOT time of high-performance gear oils can even exceed 2000 minutes.
In addition, the thin-film oxidation test and thermogravimetric analysis (TGA) can also be used for oxidation resistance performance evaluation. The thin-film oxidation test determines the oxidation resistance ability by measuring the changes in the acid value and viscosity of the oil product at high temperatures; TGA evaluates the thermal stability by analyzing the weight loss of the oil product at high temperatures. These methods provide supplementary perspectives for the evaluation of oxidation resistance performance.
Evaluation of Other Performance
In addition to the core performance, industrial gear oil additive packages also need to have properties such as low-temperature fluidity, rust and corrosion prevention performance, and antifoaming performance to adapt to different working conditions.
4.1 Low-temperature Fluidity
Low-temperature fluidity affects the starting performance of the gear oil in cold environments. The testing methods include:
Pour Point Test: Determine the temperature at which the gear oil loses its fluidity. The lower the pour point, the better the low-temperature fluidity.
Low-temperature Viscosity Test: Measure the viscosity value of the gear oil at low temperatures. The lower the viscosity, the better the fluidity.
Industrial gear oils should have a low pour point and low-temperature viscosity to ensure their performance in cold regions.
4.2 Rust and Corrosion Prevention Performance
Rust and corrosion prevention performance is related to the protection of metal components in the gear system. The testing methods include:
Copper Strip Corrosion Test: Immerse a copper strip in the gear oil, heat it, and observe the discoloration.
Steel Strip Rust Test: Place a steel strip in a mixture of oil and water and check the degree of rusting.
Qualified gear oils should not cause discoloration of the copper strip and there should be no rust on the steel strip.
4.3 Antifoaming Performance
Antifoaming performance affects the stability of the gear oil during use. The testing methods include:
Foam Tendency Test: Measure the foam volume by introducing air.
Foam Stability Test: Measure the time it takes for the foam to disappear after stopping the air supply.
Good antifoaming performance requires a small foam volume and rapid foam disappearance to prevent the oil film from breaking.
4.4 Thermal Stability and Shear Stability
Thermal Stability: Evaluate the ability of the gear oil to resist decomposition through high-temperature tests.
Shear Stability: Measure the degree of viscosity decrease through shear tests to ensure long-term use stability.
The performance evaluation of industrial gear oil additive packages is a systematic and scientific process, covering multiple indicators such as extreme pressure performance, anti-wear performance, oxidation resistance performance, low-temperature fluidity, rust and corrosion prevention performance, and antifoaming performance. Through standardized testing methods such as the FZG test, the four-ball test, and the rotating oxygen bomb method, the performance of the additive packages can be comprehensively and accurately evaluated to ensure that they meet the high requirements of gear systems. These testing methods are based on scientific principles and strict standards, providing a reliable basis for product quality control.
With the progress of industrial technology, the working conditions of gear systems are becoming increasingly complex, and the requirements for the performance of gear oil additive packages are constantly increasing. The continuous improvement of the performance evaluation system and the introduction of new testing technologies will further promote the development of the lubricant industry. Through scientific performance evaluation, not only can the quality of gear oils be guaranteed, but also solid support can be provided for product research and development and application, ensuring the efficient and safe operation of gear systems under various working conditions.
The Price of Additive Packages
The price of Additive Packages varies depending on factors such as brand, specification, composition, and sales channels. If you are interested in Additive Packages, please feel free to contact us.
Supplier of Additive Packages
UNPChemicals is a professional supplier of high-quality and effective Additive Packages. We offer several remarkable products, namely Industrial Gear Oil Additives UNP IG402A,High extreme pressure (EP) type industrial gear oil additive packages UNP IG402B,Low-Odor Type Industrial Gear Oil Additive Package UNP IG402C,etc.
Industrial Gear Oil Additives UNP IG402Aare a specialized class of compounds designed to enhance the performance of gear oils in various industrial applications.These additives are carefully formulated to provide a combination of properties that improve the efficiency,longevity,and reliability of gear systems.
High extreme pressure (EP) type industrial gear oil additive packages, like UNP IG402B, are specialized blends of chemical compounds designed to enhance the performance of base oils used in industrial gear lubricants. These packages are formulated to provide exceptional protection under conditions where gears experience heavy loads, high pressures, and potential metal-to-metal contact.
The Low-Odor Type Industrial Gear Oil Additive Package UNP IG402C is a specialized blend of chemical additives designed to enhance the performance of industrial gear oils while minimizing the strong odors typically associated with traditional gear oil additives, particularly those containing sulfur-based extreme pressure (EP) agents. This additive package is mixed with base oils (mineral or synthetic) to create gear lubricants that protect industrial gearboxes under demanding conditions, such as high loads and temperatures, while being more user-friendly in terms of smell—ideal for environments where odor control is a priority.
Professional Lubricant Additive Manufacturer
UNPChemicals,aka Luoyang Pacific United Petrochemical Co., Ltd., focuses on the application and development of special lubricating grease additives such as MODTC, MODTP, molybdenum amide, thiadiazole metal deactivators, and phosphate esters. With nearly 30 products in seven series, including extreme pressure anti-wear additives and special grease additives, it is a global manufacturer of special lubricating grease additives and a national high-tech enterprise with great influence and leading role in the industry. If you are looking for Lubricant Additive or technical information, feel free to contact UNPChemicals.