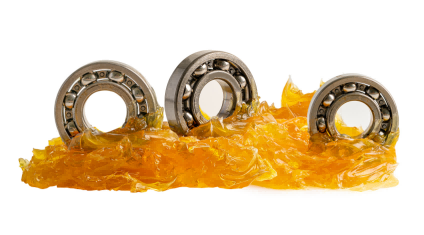
Increase your knowledge | How to choose high-temperature grease
High temperature has high requirements on the performance of grease, so when choosing high-temperature grease, you should fully consider all factors involved in equipment lubrication.
When choosing grease, you should see whether the NLGI consistency of the grease is appropriate, whether the viscosity of the base oil meets the requirements, and whether the type of grease meets the requirements. When choosing high-temperature grease, there are more factors to consider. In addition to choosing the appropriate NLGI consistency grade and the appropriate base oil viscosity, you should also consider the type of base oil, the viscosity index (viscosity-temperature property) of the base oil, the type of thickener, the stability of the grease colloidal structure at high temperature, the oxidation stability of the base oil at high temperature, evaporation loss, additive type, ambient temperature, the temperature when the grease is used, whether it is exposed to pollutants such as water impurities during use, the load and speed of the equipment during operation, how often the grease needs to be changed, whether it is compatible with other greases, cost, etc. It can be seen that when choosing high-temperature grease, it is necessary to fully consider all aspects of the details so that the grease can meet all requirements to the greatest extent.
1. High temperature:
Many greases on the market are marked as "high temperature greases". Users need to pay attention that due to different formulas, the performance of high temperature greases is also different. In addition, "high temperature" itself is a relative concept. How high a temperature can be considered high temperature? Above 65 degrees is considered high temperature, more than 100 degrees is also high temperature, and several hundred degrees is also high temperature. Therefore, users must start from their actual use temperature and combine other requirements to select the appropriate high temperature grease.
For example, the temperature around the bearing of the rolling mill in a steel plant can reach several hundred degrees, and the temperature of the bearing during operation is generally maintained at 120℃~150℃. In automobile assembly, the temperature on the drying line is also very high, and the operating temperature of the drying furnace is about 205 degrees. In these two cases, the requirements for selecting high temperature grease are different. Compared with the grease used on the automobile drying line, the rolling machine bearing grease must not only consider the heat resistance of the grease, but also require the grease to meet other performance requirements, including:
Good extreme pressure performance: Because the load is heavy, the grease needs to have good load-bearing capacity
Good pumpability: Because of the use of centralized lubrication, the grease is required to have good fluidity in the centralized grease supply system and maintain a certain consistency for easy oil pump transportation
Good water resistance: The use conditions of the steel plant require the grease to have good water resistance and not easily lost due to water erosion
Good oxidation stability: High temperature can easily cause the grease to deteriorate, so the grease is required to have good oxidation resistance at high temperature
Good shear stability: Under mechanical rolling and shearing, coupled with high temperature, the grease is required to maintain a certain consistency (not thinning)
Cost: Steel mills use a large amount of grease, so the cost must also be considered.
2. The composition of high-temperature grease:
To choose the right high-temperature grease, let's first look at the composition of the grease:
Composition of grease: base oil (70%~95%) + thickener (3%~30%) + additives (0%~10%)
High-temperature grease is a grease used at high temperatures. When producing high-temperature grease, high-temperature resistant base oil, thickener and additives are selected. The various components are formulated in a reasonable proportion to meet a series of performance requirements under high temperatures. For high-temperature grease, it is necessary to ensure that the base oil, thickener and additive can withstand the high temperatures encountered in actual use.
1) Base oil:
Base oil is the oil contained in the grease. Most of the grease is base oil, and the main lubricant is also base oil.
The performance of the grease is closely related to the grade of the base oil. There are many types of base oils, which can be roughly divided into two categories: mineral oil and synthetic oil.
Mineral oil: Oil extracted from petroleum. About 95% of lubricants and greases are produced using mineral oil as the base oil.
Synthetic oil: Man-made oil, which is synthesized by artificial chemicals and has better performance than synthetic oil, or has special performance in some aspects, such as flame retardancy.
If the base oil is subdivided, it is generally classified into five categories according to the classification standards of API (American Petroleum Institute): API-I oil, API-II oil, API-III oil, API-IV oil, API-V oil.
Mineral oil:
API-I oil: Class I oil is a mineral oil refined by solvent. The operating temperature range is generally 0~65 degrees Celsius. It is the cheapest base oil on the market.
API-II oil: Class II oil is a base oil produced by hydrocracking treatment. After hydrocracking, the content of saturated hydrocarbons is increased, so the antioxidant property is enhanced.
API-III oil: This type of oil has been hydroisomerized. The performance of Class III oil is close to PAO, but the low temperature performance and high temperature oxidation resistance are still a little different from PAO. Due to the removal of some impurities and the increase in saturated hydrocarbon content, the oxidation resistance and heat resistance of Class II and Class III oils are better than those of Class I oils, but the high temperature limit of mineral oil is around 120℃.
Synthetic oil:
Synthetic oil is usually more resistant to high temperatures than mineral oil and has better thermal stability. The synthetic base oils used for high temperature greases mainly include PAO, ester oil, silicone oil, and PAG. The most widely used synthetic oil is synthetic hydrocarbon (SHC), which belongs to API-IV oil, and the representative is PAO (polyalphaolefin). PAO can adapt to a wider range of high and low temperature applications than mineral oil, and has better oxidation stability at high temperatures, so it can meet the application environment of severe cold and high temperatures. Synthetic hydrocarbons can be used continuously at up to 160℃, and the short-term use temperature can reach up to 270℃, and the decomposition temperature is about 280℃~320℃.
Ester oil is also a common base oil for high-temperature grease. The advantages of ester oil are high temperature resistance: good thermal stability, and the evaporation loss at high temperature is lower than that of mineral oil. Among them, diester oil can be used continuously at a maximum of 175℃, and the decomposition temperature is about 275℃. Polyester oil (POE) is higher, about 315℃. POE can be used continuously at a maximum of 200℃, and the maximum temperature for short-term use can reach 300℃.
Silicone oil is rarely used in ordinary applications. The advantage of silicone oil is high temperature resistance, but there will be decomposition products at high temperatures that will cause wear.
PAG is divided into water-soluble PAG and oil-soluble PAG. The decomposition temperature of PAG is about 220℃.
Compared with the synthetic oil mentioned above, perfluoropolyether has better heat resistance, but the price is very high.
2) Thickeners
The upper temperature limit of thickeners must also meet the requirements. Greases are named according to thickeners. For example, if lithium soap is used as a thickener, the grease is called lithium-based grease. Similarly, the thickener used for calcium-based grease is calcium-based thickener, aluminum-based grease, sodium-based grease, etc. Thickeners are mainly salts of fatty acids, also called soaps. Their function is to thicken the base oil and form a semi-solid colloid. Under normal circumstances, the thickener is like a sponge, adsorbing the base oil in the colloid structure, and releasing the base oil when squeezed to play a lubricating role.
If the temperature rises to a certain level, the high temperature will destroy the colloid structure formed by the thickener, and the base oil cannot be normally retained in the thickener colloid structure, and the base oil begins to leak. According to the measurement standard of ASTM D2265, when the temperature rises to a certain level, we call the temperature when the grease starts to drip the first drop of oil the dropping point. When the temperature reaches the dropping point, the colloid structure of the thickener changes and cannot normally adsorb and retain the base oil.
Note that high dropping point does not equal the maximum operating temperature. High temperature grease does require a high dropping point, but a high dropping point is only one of the necessary conditions. In addition to a high dropping point (thickener is resistant to high temperatures), the base oil and additives must also be able to withstand high temperatures. For example, the dropping point of silicone can reach more than 1000 degrees, while clay grease has no dropping point, only a melting point. The melting point of clay grease is also very high, but the base oil cannot withstand such a high temperature. At such a high temperature, the base oil will catch fire, so a high dropping point does not equal high temperature grease.
Common high temperature greases mainly include the following categories: polyurea grease, clay grease (bentonite grease), composite lithium grease, composite aluminum grease, and composite calcium sulfonate grease.
Although the maximum operating temperature of polyurea grease is similar to that of composite lithium grease, polyurea thickener is a non-metallic soap thickener and does not contain metal ions, which avoids the catalytic effect of metal ions in soap thickeners on the oxidation of grease base oil. Therefore, polyurea grease has good oxidation stability and thermal stability, especially when the temperature exceeds 180℃, the thermal stability of polyurea grease is better than that of metal soap thickener. . Polyurea thickener itself has anti-wear properties (even if no anti-wear agent is added, polyurea thickener itself has a certain degree of anti-wear properties). Similarly, when choosing polyurea grease, pay attention to the high temperature performance of the base oil. Some toxic substances are produced during the production process of polyurea grease, which limits its promotion.
Compound calcium sulfonate thickener is more resistant to high temperatures and has better thermal stability than polyurea grease. In addition, compound calcium sulfonate thickener itself has good antioxidant, rust-proof, extreme pressure and anti-wear properties.
Some metal soap thickeners can also withstand high temperatures, such as composite lithium grease (using composite lithium thickener), lithium grease (lithium thickener), and composite aluminum grease (composite aluminum thickener). For the same type of metal soap, the composite type has better performance, for example, composite lithium grease is better than lithium grease, and composite aluminum grease is better than aluminum grease.
The upper limit of the high temperature of metal soap thickeners varies from 120℃ to 220℃. Similarly, for this type of grease, we cannot only look at the dropping point, but also the quality of other ingredients.
3) Additives:
The additive content is the least, but it cannot be ignored. The role of additives is to assist the base oil to achieve better oxidation resistance, rust and corrosion resistance, lubrication and anti-wear properties, etc. Additives must also maintain stable performance at high temperatures.
UNPChemical's grease additives
EPSAIL® T351: Molybdenum dibutyl dithiocarbamate is an advanced solid organic molybdenum extreme pressure anti-wear agent that ensures excellent antioxidant and anti-wear properties in greases and lubricants. It can serve as a complete or partial replacement for molybdenum disulfide.EPSAIL® T351 has a melting point of 260℃, which ensures that the grease has excellent anti-wear, anti-oxidation and friction reduction properties under high temperature and long life conditions.
EPSAIL® 8088: Inorganic extreme pressure agent is a biodegradable additive containing sulfur and phosphorus elements, primarily used as an extreme pressure anti-wear agent for lubricating greases. It delivers exceptional performance in demanding applications, especially in industries like mining, construction, and heavy machinery with high load performance requirements.
EPSAIL® 8290: Thiadiazole dimer is a high-performance additive that delivers exceptional extreme pressure performance and outstanding anti-wear and anti-oxidation properties when dispersed in lubricating greases. With applications that span steel plants and heavy load equipment to various high-pressure lubricating greases, It can also be used as a rubber vulcanization accelerator. EPSAIL® 8290 plays a pivotal role in promoting equipment longevity, reliability, and overall efficiency.
3. Compatibility of high-temperature greases:
When selecting and using high-temperature greases, the compatibility of greases must be considered. If different greases are incompatible after mixing, a series of adverse consequences will occur, and high temperature will intensify chemical reactions, so mixing different greases at high temperatures is more likely to cause incompatibility problems.
In principle, different greases cannot be mixed. If the greases are incompatible, the most common problem is thinning (in some cases, drying). During use, if the grease is found to be thinning, some new grease can be added to gradually squeeze out the old grease. If not, the user may have to disassemble the equipment and clean out the old grease. Therefore, when switching to new grease, it is best to do a mixing experiment first, or try to clean out the old grease, especially for important equipment.
In general, if greases of the same soap base are mixed, the risk of incompatibility is smaller, such as lithium grease and composite lithium grease, aluminum grease and composite aluminum grease. However, different types of polyurea greases are not necessarily compatible.
4. Pay attention to the water resistance of high-temperature grease:
In industrial applications, greases are often exposed to water, so pay attention to the water resistance of grease. For example, grease made of water-soluble PAG is not suitable in a relatively humid environment.
5. Consider the cost:
The performance of grease is also worth the money. If you really need it, you should not save money. High-temperature grease is also divided into grades. When selecting, you should pay attention to whether the high temperature experienced by the equipment is continuous or occasional. If the temperature is close to 200℃ or higher (continuous high temperature), then you must choose a high-end product. If the high temperature only occurs occasionally, you can choose a general high-temperature grease and shorten the oil change cycle as appropriate. Specifically, it includes the following aspects:
(1). Determine the temperature range of the grease in use, and use a thermometer to measure the temperature of the grease during equipment operation. Determine whether it exceeds 200℃.
(2). Is the high temperature continuous, intermittent, or occasional. If the continuous high temperature reaches 200℃, the quality of the high-temperature grease is high, and you should choose a high-end product.
(3). Does the equipment alternate between hot and cold or is easily exposed to moisture during operation? If so, the grease should have good waterproof properties.
(4). Is it easy to change the oil? High temperature will accelerate the deterioration of oil. If frequent oil changes are troublesome, high-end oil products are required.
(5). Is the operating environment dirty? If the grease is inevitably contaminated, it needs to be changed frequently, and the amount used is relatively large. You can choose mid-range products to increase the number of oil changes.