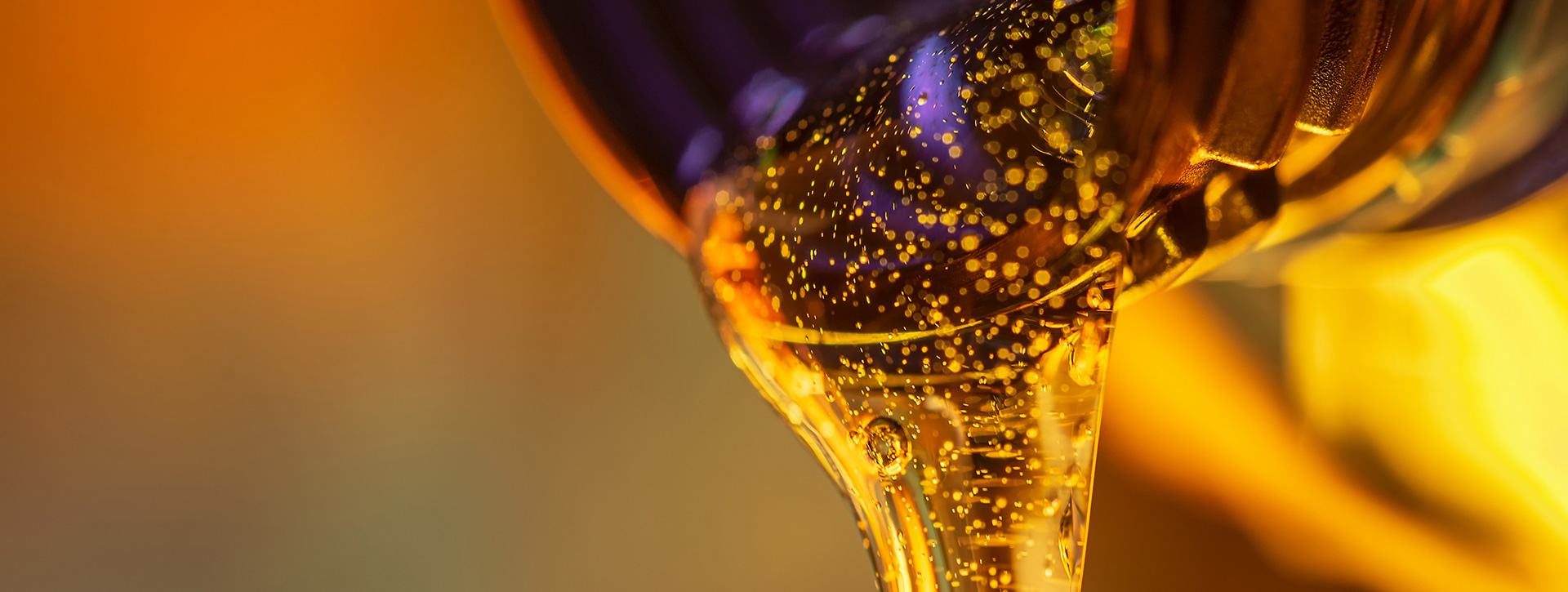
Foam Control in Hydraulic Oil: Composite Additive Solutions
I. Hazards of Foam Problems in Hydraulic Systems
As an indispensable power transmission and control device in modern industry, hydraulic systems are widely used in construction machinery, aerospace, automotive manufacturing, and many other fields. Hydraulic oil serves as the "blood" of hydraulic systems, not only transmitting power but also providing lubrication, heat dissipation, rust prevention, and other functions. However, foam problems often occur during the operation of hydraulic systems, posing multiple hazards to their normal functioning.
Reduced System Efficiency
Foam in hydraulic oil decreases its bulk modulus of elasticity. When foam mixes with hydraulic oil, the compressibility of gas is far greater than that of liquid. Under pressure, foam is compressed, reducing the actual volume of hydraulic oil and thus decreasing the output power of the hydraulic system. For example, in precision-controlled hydraulic systems such as the hydraulic feed systems of CNC machine tools, the presence of foam slows down system response and reduces positioning accuracy, affecting machining quality and production efficiency.
Accelerated Component Wear
Foam collapse generates local high temperatures and pressures. In the high-pressure areas of hydraulic systems, the energy released by foam collapse instantaneously impacts the surfaces of hydraulic components, forming tiny pits and cracks. Over time, this increases surface roughness, accelerates wear, and shortens component lifespan. For instance, moving parts of hydraulic pumps like vanes and plungers wear significantly faster under foam impact, and severe cases can even damage the pump, disrupting the entire hydraulic system.
Enhanced Oxidation and Corrosion
Foam increases the contact area between hydraulic oil and air, accelerating oil oxidation. Oxidized hydraulic oil produces acidic substances and precipitates, which corrode metal components such as cylinders and pipelines. Additionally, precipitates can clog filters and orifices in the hydraulic system, affecting its normal operation. In long-running hydraulic systems, for example, untreated foam problems gradually worsen oil oxidation and corrosion, leading to frequent system failures and increased maintenance costs.
II. Types and Working Principles of Antifoam Composites
Types of Antifoam Composites
1. Silicone-Based Antifoam Agents
Silicone-based antifoam agents are the most widely used type, primarily composed of polydimethylsiloxane and its derivatives, offering excellent defoaming and antifoaming properties. Their molecular structure contains silicon-oxygen (Si-O) bonds with high bond energy, providing good chemical and thermal stability. Meanwhile, silicone molecules have low surface tension, allowing them to rapidly spread on foam surfaces, disrupt surface films, and achieve defoaming.
2. Non-Silicone Antifoam Agents
Non-silicone antifoam agents mainly include fatty alcohols, fatty acid esters, and polyethers. Compared to silicone-based agents, they exhibit better compatibility and shear resistance. For example, polyether antifoam agents are high-molecular compounds polymerized from propylene oxide and ethylene oxide, with adjustable molecular structures and weights to meet different defoaming and antifoaming needs. Non-silicone agents have unique advantages in silicone-sensitive hydraulic systems, such as those in food processing machinery and electronic equipment.
Working Principles of Antifoam Composites
1. Defoaming Mechanism
The defoaming process of antifoam composites involves three steps: adsorption, spreading, and film rupture. When antifoam molecules contact foam surfaces, they rapidly adsorb onto the liquid film. Due to their low surface tension, they spread on the foam surface to form a new liquid film with lower strength, making it easy to rupture. For example, silicone-based antifoam molecules can form a continuous silicone oxide film on foam surfaces, which has extremely low surface tension and rapidly breaks foam films.
2. Antifoaming Mechanism
Antifoaming refers to preventing foam generation. This is mainly achieved by reducing the liquid’s surface tension and altering its surface properties. Antifoam molecules form an adsorption film on the liquid surface, blocking gas molecules from entering the liquid and reducing foam generation. They also decrease surface viscosity, making foam more prone to collapse. For instance, polyether molecules in non-silicone agents form a hydrophilic adsorption film on the liquid surface, preventing gas molecule adsorption and aggregation to inhibit foam formation.
III. How to Select Suitable Composites?
Consider Hydraulic System Operating Conditions
1. Temperature
The operating temperature range of the hydraulic system is a critical factor in selecting antifoam composites. Different antifoam agents perform differently at varying temperatures. For example, silicone-based agents are stable at high temperatures but may precipitate or agglomerate at low temperatures, affecting defoaming performance. Thus, high-temperature hydraulic systems require heat-resistant antifoam agents, while low-temperature systems need those with good low-temperature properties.
2. Pressure
Operating pressure also influences antifoam agent performance. In high-pressure systems, foam is more stable, requiring agents with strong defoaming and antifoaming capabilities. High-pressure systems also demand high shear resistance, as antifoam molecules can be destroyed under high pressure and shear forces, losing efficacy.
Consider Hydraulic Oil Types
Different hydraulic oils have distinct chemical compositions and physical properties, affecting antifoam agent compatibility. Mineral oil-based hydraulic oils are generally compatible with most antifoam agents, but synthetic oils (e.g., phosphate esters, water-glycol fluids) have stricter requirements. When selecting agents, ensure good compatibility with the hydraulic oil to avoid performance degradation or issues like delamination and precipitation.
Consider Environmental Requirements
With growing environmental awareness, hydraulic oils and antifoam agents face stricter eco-standards. Prioritize agents compliant with environmental criteria, such as those free of phosphorus, heavy metals, and other harmful substances. Also, choose agents with good biodegradability to minimize environmental impact.
IV. Impact of Foam Control on System Performance
In summary, foam control is vital for hydraulic systems. Effective control enhances system efficiency, reduces component wear, prolongs oil and component lifespan, and lowers maintenance costs. By selecting appropriate antifoam composites and applying them based on system conditions and oil types, foam issues can be effectively resolved.
The types and working principles of antifoam composites provide a theoretical basis for selection. A comprehensive evaluation of operating conditions, oil types, and environmental requirements ensures optimal agent performance. Additionally, regular maintenance and monitoring of hydraulic systems help detect and address foam problems promptly, ensuring stable operation. Only through these measures can hydraulic systems fully leverage their performance advantages, providing reliable power support for industrial production and social development.
The Price of Hydraulic Oil Additives Package
The price of Hydraulic Oil Additives Package varies depending on factors such as brand, specification, composition, and sales channels. If you are interested in Hydraulic Oil Additives Package, please feel free to contact us.
Supplier of Hydraulic Oil Additives Package
UNPChemicals is a professional supplier of high-quality and effective Hydraulic Oil Additives Package. We offer several remarkable products, namely High zinc hydraulic oil additives UNP AH502A,Low Zinc Hydraulic Oil Additives UNP AH502B,Zinc-free Hydraulic Oil Additives UNP AH502C,etc.
High zinc hydraulic oil additives UNP AH502A are a type of chemical additive used in hydraulic oils that contain high levels of zinc dialkyldithiophosphate (ZDDP). ZDDP is a well-known anti-wear agent that also provides antioxidant, anti-corrosion, and anti-foam properties. The zinc in these additives plays a crucial role in forming a protective film on metal surfaces within the hydraulic system, thereby reducing wear and extending the life of the system components.
Low Zinc Hydraulic Oil Additives UNP AH502B are a class of advanced lubricant additives designed to enhance the performance of hydraulic oils with reduced zinc content.These additives are formulated to provide a balance of anti-wear,extreme pressure,and antioxidant properties,making them suitable for modern hydraulic systems that demand high performance with lower environmental impact.
Zinc-free Hydraulic Oil Additives UNP AH502C are a new class of environmentally friendly lubricant additives designed for hydraulic systems.These additives are formulated to provide the same level of performance as traditional zinc-containing additives but without the heavy metal content,reducing the environmental impact of hydraulic fluids.
Professional Lubricant Additive Manufacturer
UNPChemicals,aka Luoyang Pacific United Petrochemical Co., Ltd., focuses on the application and development of special lubricating grease additives such as MODTC, MODTP, molybdenum amide, thiadiazole metal deactivators, and phosphate esters. With nearly 30 products in seven series, including extreme pressure anti-wear additives and special grease additives, it is a global manufacturer of special lubricating grease additives and a national high-tech enterprise with great influence and leading role in the industry. If you are looking for Lubricant Additive or technical information, feel free to contact UNPChemicals.