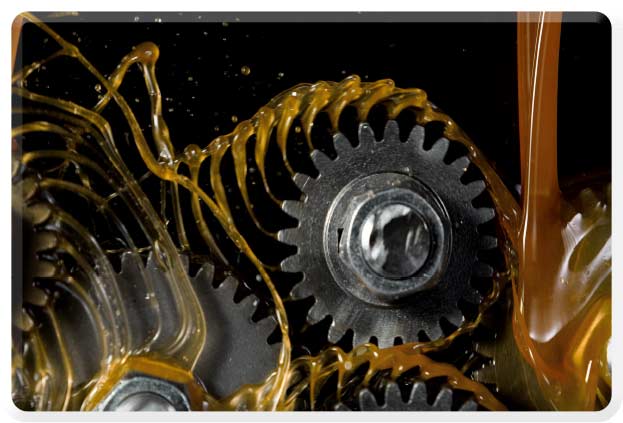
Differences between Lubricating Oil Additives and Grease Additives
In the operation of modern industries and mechanical equipment, lubrication is a crucial aspect for ensuring the normal operation of equipment, extending its service life, and reducing energy consumption. Lubricating oil additives and grease additives, as important components for enhancing lubrication performance, each play a unique and irreplaceable role. A deep understanding of their definitions, characteristics, and differences is of great significance for the rational selection and use of lubricants, and for ensuring the efficient and stable operation of equipment.
I. What are Lubricating Oil Additives?
Lubricating oil additives are a class of chemical substances that are added in small amounts (usually with a mass fraction between 0.1% - 20%) to lubricating oil but can significantly improve its performance. Although base lubricating oil has certain lubricating capabilities, it often struggles to meet all requirements when facing complex and variable working conditions. By adding specific additives, a series of excellent properties can be imparted to the lubricating oil, enabling it to adapt to various harsh working conditions.
(I) Main Types and Functions
1.Detergent - Dispersant: During the operation of equipment such as engines, impurities like carbon deposits, varnish, and sludge are generated. Detergent - dispersants can disperse these impurities in the oil, preventing their deposition on the metal surface and keeping the inside of the engine clean. For example, in automotive engine oil, detergent - dispersants can effectively prevent the formation of carbon deposits in the piston ring grooves, ensuring the normal operation of the piston rings and maintaining the engine's performance.
2.Antioxidant: Lubricating oil comes into contact with oxygen during use. Under the influence of factors such as high temperature and metal catalysis, it undergoes an oxidation reaction, leading to problems such as oil deterioration, increased viscosity, and the formation of acidic substances. Antioxidants can inhibit the progress of the oxidation reaction and extend the service life of the lubricating oil. For instance, hindered phenolic antioxidants and amine - type antioxidants are common types of antioxidants. They can capture the free radicals generated during the oxidation process, interrupt the oxidation chain reaction, and maintain the stability of the lubricating oil.
3.Anti - wear Agent: There is varying degrees of friction between the moving parts of mechanical equipment, such as gears and bearings. Anti - wear agents can form a protective film on the metal surface, reducing direct contact between metals and lowering wear. Common anti - wear agents include organic molybdenum compounds and zinc dialkyldithiophosphate (ZDDP). Taking the gear transmission system as an example, anti - wear agents can effectively reduce the wear of gear tooth surfaces, improve transmission efficiency, and extend the service life of gears.
4.Extreme - pressure Agent: When mechanical equipment operates under extreme pressure conditions such as high load and high temperature, ordinary lubrication methods are often insufficient. Extreme - pressure agents can react chemically with the metal surface to form a reaction film with high compressive strength and shear resistance, preventing serious wear phenomena such as sintering and scuffing of the metal surface under extreme - pressure conditions. For example, in the reducers of heavy - industrial equipment, extreme - pressure agents can ensure the normal operation of gears during high - load operation.
5.Rust Inhibitor: Metal components are prone to rusting due to the erosion of environmental factors such as moisture and oxygen during use. Rust inhibitors can form a protective film on the metal surface, preventing moisture and oxygen from coming into contact with the metal and playing a rust - prevention role. Common rust inhibitors include petroleum sulfonates, fatty acids and their soaps. In some outdoor - used mechanical equipment, rust inhibitors can effectively protect metal components and extend the service life of the equipment.
II. What are Grease Additives?
Grease additives are substances added to grease to improve its performance. Grease is a semi - solid lubricant composed of base oil, thickener, and additives. Additives play a key role in enhancing performance and meeting specific usage requirements.
(I) Main Types and Functions
1.Extreme - pressure Anti - wear Agent: Similar to the extreme - pressure anti - wear agents in lubricating oil, the extreme - pressure anti - wear agents in grease are used to improve the anti - wear ability of grease under high - load and high - pressure conditions. For example, in the bearings and gears of heavy - load equipment such as mining machinery and construction machinery, the extreme - pressure anti - wear agents in grease can effectively prevent the wear and scuffing of metal surfaces, ensuring the normal operation of the equipment under harsh working conditions.
2.Antioxidant: Since grease is also affected by oxidation during use, antioxidants can delay the oxidation and deterioration of grease and extend its service life. Especially in environmental conditions such as high temperature and high humidity, the role of antioxidants is more significant. For example, in the lubricating grease used in the transmission parts of high - temperature furnaces, antioxidants can ensure the stability of the grease under long - term high - temperature conditions and maintain its lubrication performance.
3.Rust Inhibitor: Preventing metal components from rusting is one of the important functions of grease, and rust inhibitors play a key role in this. It can form a dense protective film on the metal surface, preventing moisture, oxygen, and other corrosive substances from coming into contact with the metal, thus achieving the purpose of rust prevention. In mechanical equipment used in marine environments, such as ship deck machinery and port cranes, the rust inhibitors in grease can effectively resist the erosion of seawater and protect metal components.
4.Thickener: Although the thickener is one of the basic components of grease, it can also be regarded as a special additive. Different types of thickeners can endow grease with different consistencies, dropping points, and mechanical stability. For example, grease made with lithium - based thickeners has good high - and low - temperature performance and mechanical stability and is widely used in various mechanical equipment; while grease made with bentonite thickeners has better water resistance and is suitable for lubricating equipment in humid environments.
5.Other Special Additives: According to different usage requirements, some special additives can also be added to grease, such as anti - radiation additives and conductive additives. The grease used in nuclear industry equipment may be added with anti - radiation additives to ensure the stable performance of the grease in a radiation environment; in some electronic equipment, grease with conductive properties is required, and in this case, conductive additives will be added to meet special working requirements.
III. Differences between Lubricating Oil Additives and Grease Additives
(I) Different Emphases in Addition Purposes
The addition purpose of lubricating oil additives is relatively broad, aiming to comprehensively improve the performance of lubricating oil under various working conditions, including but not limited to anti - wear, anti - oxidation, detergent - dispersant, and rust - prevention, to meet the lubrication requirements of different mechanical equipment under different operating conditions. For example, automotive engine oil needs to have good anti - wear, anti - oxidation, and detergent - dispersant properties simultaneously to cope with the engine's operation at different speeds, loads, and temperatures.
On the other hand, the addition purpose of grease additives is relatively more focused on meeting specific usage scenarios and working conditions. Since grease itself has certain adhesion and sealing properties, its additives mainly focus on enhancing the performance of grease in special environments such as high - load, high - temperature, and humid conditions, such as improving extreme - pressure anti - wear performance and enhancing rust - prevention ability. For example, in high - temperature and heavy - load industrial equipment, grease additives mainly focus on improving extreme - pressure anti - wear performance and antioxidant performance to ensure the normal operation of grease under harsh working conditions.
(II) Different Addition Amounts and Proportions
Generally, the addition amount of lubricating oil additives is relatively low, usually with a mass fraction between 0.1% - 20%. This is because the base lubricating oil has good fluidity, and the additives can be evenly dispersed in it. A small amount of additives can significantly improve the performance.
In contrast, the addition amount of grease additives may be relatively higher. Since grease is in a semi - solid state, it is more difficult to disperse the additives in it. In order to achieve the desired performance improvement effect, the amount of additives sometimes needs to be increased. For example, in some high - performance greases, the mass fraction of additives may reach 20% - 50%.
(III) Different Interactions with the Base Medium
The interaction between lubricating oil additives and the base oil is mainly physical dissolution and dispersion. The base oil provides a dispersion medium for the additives, and the additives are evenly distributed in the base oil, improving the performance of the lubricating oil through their respective chemical actions. This interaction is relatively simple, and the compatibility between the additives and the base oil is mainly ensured by the similarity of chemical structures and the solubility of the additives.
However, grease additives not only need to interact with the base oil but also need to consider compatibility with the thickener. The thickener forms a three - dimensional network structure in the grease, encapsulating the base oil. The additives need to function in this complex system. There may be physical adsorption, chemical reactions, and other interactions between the additives and the thickener, which will affect the structure and performance of the grease. For example, certain additives may react chemically with the thickener, changing the structure and performance of the thickener, thereby affecting the consistency, dropping point, and mechanical stability of the grease.
(IV) Different Performance Manifestations and Modes of Action
Lubricating oil additives mainly function by forming molecular films in the lubricating oil, capturing free radicals, dispersing impurities, etc. Their performance manifestations are mainly reflected in the overall performance improvement of the lubricating oil, such as reducing the friction coefficient, extending the oil change interval, and improving the reliability of the equipment. The lubricating oil circulates in the equipment, and the additives can act on each friction part in a timely manner, having a greater impact on the dynamic lubrication performance of the equipment.
Grease additives, on the other hand, mainly function by forming a protective film on the metal surface and enhancing the structural stability of the grease. Due to the semi - solid nature of grease, it forms a lubricating film with strong adhesion on the equipment surface, and the additives are slowly released in it, having a greater impact on the static sealing and protection performance of the equipment. For example, the rust inhibitor in grease can form a long - lasting protective film on the metal surface, preventing the metal from rusting during long - term static conditions or in harsh environments.
IV. Mechanisms of Action of Lubricating Oil Additives and Grease Additives
There are some differences in the mechanisms of action between lubricating oil additives and grease additives, mainly reflected in the following aspects:
(I) Lubrication Mechanisms
For Lubricating Oil Additives:
-Friction - reduction and Anti - wear: Friction - reduction agents in lubricating oil (such as fatty acids) usually form an oriented molecular film on the metal surface through adsorption, transforming the friction between metal surfaces into the friction between molecular films, thereby reducing the friction coefficient. Anti - wear agents (such as zinc dialkyldithiophosphate) can react chemically with the metal surface under medium - load conditions to form a chemical reaction film. This film has low shear strength and good anti - wear performance, effectively preventing the wear of the metal surface.
-Extreme - pressure Lubrication: Under extreme - pressure conditions, extreme - pressure additives (such as sulfur - containing, phosphorus - containing, and chlorine - containing compounds) react chemically with the metal surface to generate metal sulfides, phosphides, or chlorides with low melting points and small shear strengths. These compounds can form a tough solid lubricating film under high temperature and high pressure, preventing direct contact between metal surfaces and avoiding serious wear phenomena such as gluing and sintering.
For Grease Additives:
-Enhancing Oil Film Strength: The base oil in grease forms an oil film on the metal surface to provide lubrication, and additives can enhance the strength and stability of the oil film. For example, some high - molecular polymer additives can increase the viscosity of the base oil, making the oil film thicker and having a stronger load - bearing capacity, thus better maintaining the lubrication state on the metal surface and reducing friction and wear.
-Synergistic Effect: The three - dimensional network structure formed by the thickener in grease can encapsulate the base oil. Additives interact with the thickener and the base oil to further improve the lubrication performance of the grease. For example, certain additives can combine with thickener molecules, improving the structure and performance of the thickener, enabling the grease to maintain good lubrication performance under harsh conditions such as high temperature and high load.
(II) Antioxidation Mechanisms
For Lubricating Oil Additives:
-Free - radical Termination: Antioxidants in lubricating oil (such as phenolic and amine - type antioxidants) mainly capture the free radicals generated during the oxidation process of the lubricating oil, preventing the progress of the free - radical chain reaction, and thus delaying the oxidation of the lubricating oil. For example, phenolic antioxidants can provide hydrogen atoms to combine with free radicals, generating stable products, interrupting the oxidation reaction chain, and extending the service life of the lubricating oil.
-Decomposition of Peroxides: Some antioxidants (such as organic sulfides) can decompose the peroxides already formed in the lubricating oil, converting them into stable compounds, thus eliminating the further oxidation effect of peroxides on the lubricating oil and maintaining the stable performance of the lubricating oil.
For Grease Additives:
-Surface Protection: Antioxidants in grease, in addition to having similar functions of free - radical termination and peroxide decomposition as those in lubricating oil, can also form an antioxidant protective film on the metal surface. This film can prevent oxygen from coming into contact with the metal surface, reducing the catalytic effect of the metal on the oxidation of the grease. At the same time, it can also prevent the base oil and other components in the grease from being oxidized.
-Diffusion Inhibition: Due to the high consistency of grease, the diffusion rate of additives in it is relatively slow. Some antioxidants can form a slow - release system in the grease, continuously releasing antioxidant components, thus effectively inhibiting the oxidation of the grease for a long time.
(III) Rust - prevention and Corrosion - prevention Mechanisms
For Lubricating Oil Additives:
-Adsorption Film Formation: Rust inhibitors (such as petroleum sulfonates) have a strong adsorption ability on the metal surface and can form a dense monomolecular adsorption film on the metal surface. This film can prevent corrosive media such as water and oxygen from coming into contact with the metal surface, thus playing a rust - prevention role.
-Neutralization of Acidic Substances: Alkaline additives in lubricating oil (such as the alkaline components in detergent - dispersants) can neutralize the acidic substances generated during the use of the lubricating oil due to oxidation and other reasons, preventing the acidic substances from corroding the metal and maintaining the chemical stability of the metal surface.
For Grease Additives:
-Isolation Effect: Grease itself has certain sealing properties and can isolate the metal surface from the outside air, moisture, etc. Rust - prevention additives in grease can further enhance this isolation effect. For example, some fatty - acid - type rust inhibitors can react chemically with the metal surface to form an insoluble metal soap protective film, more effectively preventing corrosive media from coming into contact with the metal.
-Corrosion - inhibition Effect: Certain grease additives (such as benzotriazole and its derivatives) have good corrosion - inhibition effects on specific metals. They can form a chemical adsorption film or reaction film on the metal surface, inhibiting the corrosion process of the metal. Even in the presence of a small amount of corrosive media such as moisture, they can protect the metal surface from corrosion.
Although both lubricating oil additives and grease additives are used to improve the performance of lubricants, there are obvious differences in their definitions, types, addition purposes, addition amounts, interactions with the base medium, as well as performance manifestations and modes of action. In practical applications, it is necessary to reasonably select and use additives according to the working conditions of the equipment, lubrication requirements, and the type of lubricant to ensure the efficient and stable operation of the equipment.
The Price of Grease Additives
The price of Grease Additives depending on factors such as brand, specification, composition, and sales channels. If you are interested in Grease Additives, please feel free to contact us.
Supplier of Grease Additives
UNPChemicals is a professional supplier of high-quality and effective Grease Additives. We offer several remarkable products, namely Molybdenum dibutyl dithiocarbamate EPSAIL T351,Inorganic extreme pressure agent EPSAIL 8088,Thiadiazole dimer EPSAIL 8290,etc.
Molybdenum dibutyl dithiocarbamate EPSAIL T351 is an advanced solid organic molybdenum extreme pressure anti-wear agent that ensures excellent antioxidant and anti-wear properties in greases and lubricants. It can serve as a complete or partial replacement for molybdenum disulfide.
Inorganic extreme pressure agent EPSAIL 8088 is a biodegradable additive containing sulfur and phosphorus elements, primarily used as an extreme pressure anti-wear agent for lubricating greases. It delivers exceptional performance in demanding applications, especially in industries like mining, construction, and heavy machinery with high load performance requirements.
Thiadiazole dimer EPSAIL 8290 is a high-performance additive that delivers exceptional extreme pressure performance and outstanding anti-wear and anti-oxidation properties when dispersed in lubricating greases. With applications that span steel plants and heavy load equipment to various high-pressure lubricating greases, It can also be used as a rubber vulcanization accelerator. EPSAIL 8290 plays a pivotal role in promoting equipment longevity, reliability, and overall efficiency.
Professional Lubricant Additive Manufacturer
UNPChemicals, aka Luoyang Pacific United Petrochemical Co., Ltd., focuses on the application and development of special lubricating grease additives such as MODTC, MODTP, molybdenum amide, thiadiazole metal deactivators, and phosphate esters. With nearly 30 products in seven series, including extreme pressure anti-wear additives and special grease additives, it is a global manufacturer of special lubricating grease additives and a national high-tech enterprise with great influence and leading role in the industry. If you are looking for Lubricant Additive or technical information, feel free to contact UNPChemicals.