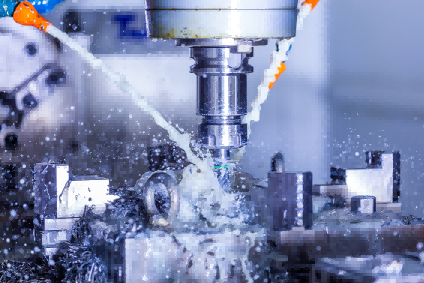
What are the common problems of metalworking fluids? How to choose metal working additives ?
What is metal working fluid?
Metalworking fluid, known as the "blood" of the manufacturing industry, has the main function of achieving lubrication, cooling, rust prevention, cleaning and other functions during metalworking, thereby helping enterprises enhance deep processing capabilities, improve product quality, and improve production efficiency.
However, in the process of fulfilling its mission, metalworking fluids sometimes pose various problems to enterprises, such as: insufficient lubrication or rust prevention performance, unable to meet product quality requirements; metalworking fluids are prone to deterioration, which leads to a shorter service life; employees experience allergies during the use of metalworking fluids.
For enterprises, the dual pressures of economy and environmental protection are already full of challenges, so how to solve the above problems?
About the situation where the machined cast iron and steel parts are not rusted, but the machine tool guide rails are rusted
Some load processing requires the addition of extreme pressure agents (mainly compounds containing extreme pressure active elements such as S, P, Cl). The compound use of such additives and lubricants can greatly improve the difficulty of cutting and improve the wear resistance of the tool. The disadvantage is that these substances are easy to corrode a variety of metals when added to water-soluble cutting fluids. After these compounds are dissolved in water, a small amount of free CL, S, and P is produced, which combines with hydrogen ions in water to produce acid, thereby corroding the guide rails.
For the rust of workpieces caused by fully synthetic cutting fluids in summer
Since fully synthetic cutting fluids do not contain oil, many manufacturers will choose inorganic salts as their anti-rust additives, such as sodium nitrite, boric acid, sodium benzoate, sodium gluconate, sodium carbonate, etc. Sodium molybdate has good anti-rust properties, but the price is too expensive. The amount of other inorganic salts added is generally very high to achieve a good anti-rust effect. In summer, the weather is hot and the water evaporates a lot. In addition, the operator does not add cutting fluid in time, causing the inorganic salts in the liquid tank to reach a saturated state. As a result, it precipitates and adheres to the surface of the workpiece, which not only fails to prevent rust, but also brings great trouble to the subsequent cleaning. Therefore, the amount of inorganic salts added can be appropriately reduced, and the addition of organic rust inhibitors can improve this, such as boric acid esters, amino acid esters, carboxylic acids, etc., which not only prevent rust very well, but also make the system more stable.
Regarding the "burn" during grinding, is it due to insufficient cooling or insufficient lubrication?
The blueing and other problems caused by grinding are caused by local high temperature during grinding. Grinding is a high-speed cutting process, and instantaneous high temperature is generated at the grinding point. Therefore, the burning problem often occurs during grinding. The function of the grinding fluid is to take away the accumulated heat on the grinding wheel and the workpiece in time and keep it at a lower temperature level to ensure the dimensional accuracy of the workpiece. The grinding wheel and the workpiece are at a lower temperature level, which is of course effective in reducing the temperature of the grinding area, but this cooling is indirect. The most direct way is to improve the lubrication conditions of the grinding area, and it is more effective to reduce the instantaneous high temperature of the friction point. Therefore, if the burning problem occurs, it is mainly solved by improving the lubricity of the grinding fluid.
Regarding the problem of blackening and moldy surface of the workpiece when processing aluminum parts
The cutting fluid selection that should be paid attention to when processing aluminum and aluminum alloys. Because the chemical properties of aluminum are relatively active, it is easy to react chemically with acids and alkalis, resulting in corrosion, rust spots, blackening, and mold. When dealing with such problems, the first thing to consider is that the pH value of the cutting fluid should not be too high, and should be maintained between 8.5-9.0. The selected rust inhibitor needs to have the ability to inhibit corrosion and maintain the stability of the pH value. It is best to use those rust inhibitors that can form a protective film on the surface of the workpiece, such as phosphate esters, sodium silicate, etc. Try to use as few inorganic salt rust inhibitors as possible, and the amount of inorganic salts used should not be high. The processed aluminum parts need to be cleaned in time, and then coated with rust-proof oil, etc., which can play a rust-proof role (or passivation).
The reason why a lot of foam appears when the cutting fluid is used
The components of the cutting fluid contain a lot of surfactants, commonly known as cleaning agents, such as TX-4, Pingpingjia, 6501, 6503, etc. These cleaning agents will produce a lot of foam when used, which is not conducive to mechanical processing. It will pollute the processing environment, bring inconvenience to the production personnel, and leakage out of the machine tool will also reduce the cleaning ability of the cutting fluid. At this time, you can add a small amount of defoaming agent (silicone oil has the fastest effect, polyether has strong persistence and can suppress foam) to remedy it. In addition, in summer, the cutting fluid needs to increase the content of defoamer in its mother liquid. At the same time, this is also related to the liquid level of the machine tool tank and the sealing of the circulation pump. For these situations, the problem can be solved by appropriately increasing the amount of defoamer.
The problem of odor when using cutting fluid
The cutting fluid is divided into emulsified oil (emulsion), semi-synthetic (microemulsion), and fully synthetic. Because the emulsified oil contains a large amount of mineral oil, it provides a breeding ground for bacteria, fungi, and mold. If no fungicide is added, bacteria will multiply in a short time and stink will appear. The use of unsuitable fungicides cannot solve the problem. At present, fungicides are divided into triazines (BK), morpholine derivatives (MBM), sodium pyrithione, benzisothiazolinone, polychlorophenol, etc., and BK and MBM are commonly used. BK formaldehyde release type is effective for bacteria, fungi and molds are generally effective, suitable for use in semi-synthetic and fully synthetic, and precipitation and stratification will occur in emulsified oil. In addition, if there are no bacteria in the machine tool tank, formaldehyde will not be produced, and the sterilization effect will not be achieved. MBM morpholine is effective against bacteria, fungi, and molds, and is suitable for use in cutting fluids with high oil content such as emulsified oil.
How to choose metal working additives ?
Compared with the types of materials currently on the market, the types of processing fluids are very single, but for these materials on the market, how should we choose our limited types of processing fluids?
At present, the common materials in the processing market are divided into non-ferrous metals and ferrous metals. Non-ferrous metals are mainly aluminum alloys and copper. Aluminum alloys are simply divided into profile aluminum and die-cast aluminum, and copper is mainly brass. There are many types of ferrous metals, and common processing materials include cast iron, carbon steel, alloy steel, stainless steel, and hard alloy steel.
● In the processing of aluminum alloy materials, the main consideration is anti-corrosion, and emulsified, micro-emulsified, and semi-synthetic products with high oil content are mostly selected. General products do not contain extreme pressure agents or contain less extreme pressure agents.
Siloxane ketone oligomer CSUM® 8150 is a complex product of siloxane oligomer, also known as siloxane ketone, formed by hydrolysis and condensation of various special silanes. Mainly used for corrosion inhibition of aluminum in water-based environments, CSUM® 8150 also offers outstanding corrosion inhibition for soldering tin, reducing its corrosion in water environments.
● The main consideration for copper materials is corrosion. In addition, it is also necessary to consider that there is a lot of copper powder in the copper material during the processing process. Long-term processing of copper powder and processing fluid will react to produce copper soap. Generally, semi-synthetic products or fully synthetic products that protect copper are selected.
Tolyltriazole derivatives (TTA) CSUM® 4200 is a methyl benzotriazole derivative that is soluble in water and ethylene glycol systems. It is a water-soluble copper corrosion inhibitor. It is designed to function as a metal deactivator and provides an effective alternative to solid benzotriazole and methyl benzotriazole.
Thiadiazole derivatives CSUM® 5202 is a completely water-soluble thiadiazole derivative, which has the advantages of low viscosity, good water solubility, good extreme pressure performance, etc. Used for fully synthetic metalworking fluid (oil-free system),semi-synthetic metalworking fluid (low oil system), a substitute for extreme pressure emulsion; especially suitable for wire drawing process.
● Cast iron and carbon steel materials themselves contain more carbon, a small amount of sulfur, phosphorus and other elements, and are more rusty. During the processing process, the first consideration is rust prevention and carbon powder precipitation, and then the lubrication performance of the product. Because this type of product has high requirements for sedimentation and biological stability during processing, generally this type of material uses fully synthetic products with good rust prevention performance.
● Stainless steel materials are sticky, and the requirements for lubrication during processing are high, otherwise it is easy to cause sticking and knife damage. The processing of this type of product generally uses semi-synthetic products or oily products with good extreme pressure lubrication effects. For heavy-load processing of oily products, oil mist problems will occur. It is generally recommended to use high extreme pressure water-based products.
● Cemented carbide materials are generally very hard and brittle, and the requirements for lubrication during processing are very high. Generally, oily products containing active extreme pressure additives are used.
Metalworking Fluid Additives Supplier
UNPChemicals is a professional and trusted Metalworking Fluid Additives supplier manufacturing high quality and range of Metalworking Fluid Additives according to your workflows and products. If you are looking for high performance Metalworking Fluid Additives solution, feel free to contact us.