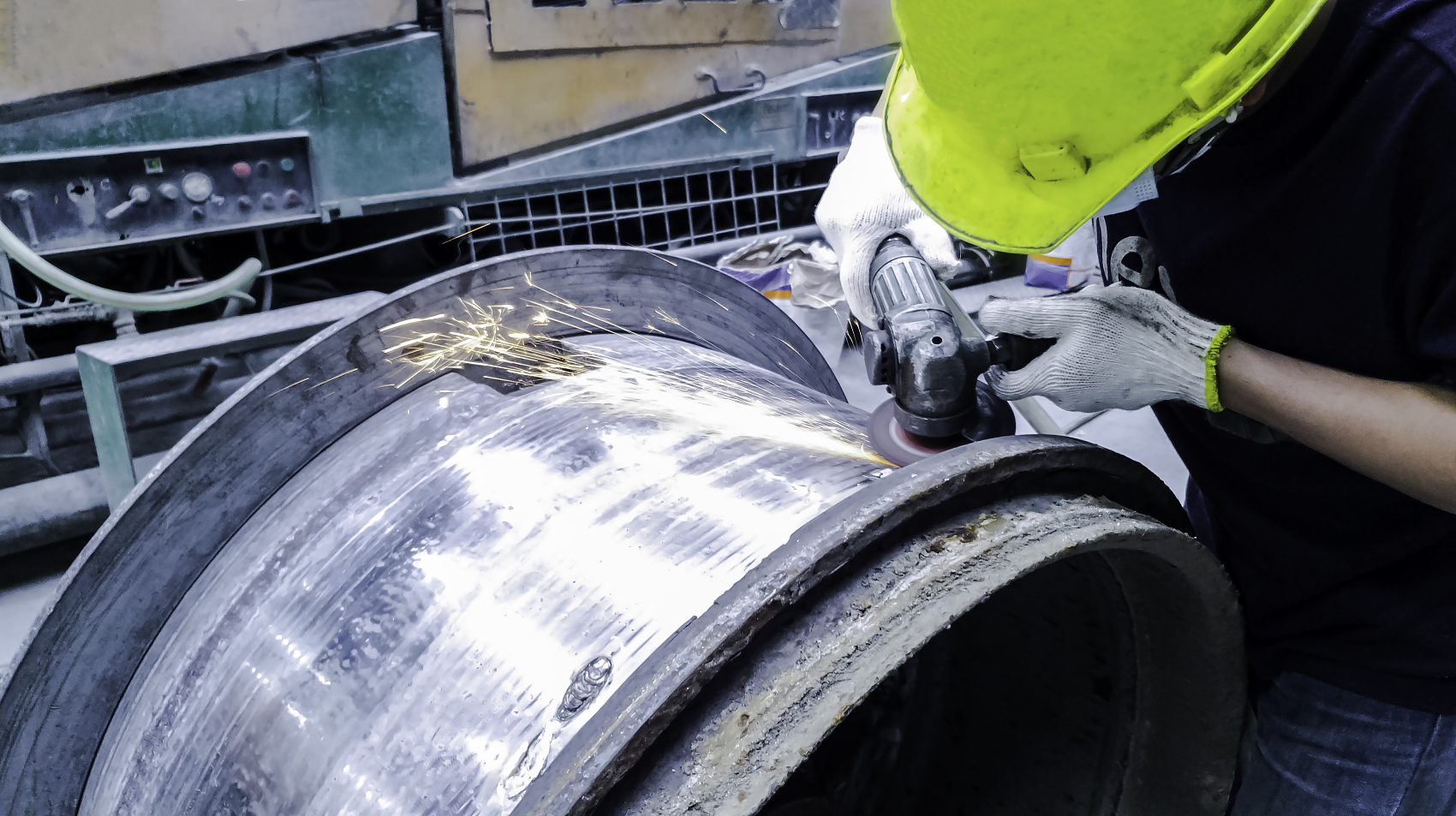
We need that film! The sulfur family of extreme pressure anti-wear agents
What is extreme pressure anti-wear agent?
Extreme pressure anti-wear agent is an important lubricant or grease additive, mainly used to improve the performance of lubricants under high pressure and high temperature environments. It is usually composed of organic polar compounds containing sulfur, phosphorus, chlorine, etc. Under boundary lubrication conditions, extreme pressure anti-wear agents can react chemically with the metal surface to form a chemical reaction film, which can reduce the friction coefficient and prevent the metal surface from sintering, biting, scratching, etc. under high load conditions. Types of extreme pressure anti-wear agents include organic chlorides, organic sulfides, organic phosphides, organic metal salts, borates and boric acid esters. These additives are usually mixed in a certain proportion in practical applications to obtain better performance. Extreme pressure anti-wear agents are widely used in various industrial lubricants and greases, such as steel, mining, electricity, automobiles, aviation and other fields.
What is Sulfurized Extreme Pressure Antiwear Agent?
Sulfurized extreme pressure antiwear agents are additives used in lubricants to prevent scoring, welding, and wear under high loads and extreme pressure conditions.
Characteristics of sulfurized extreme pressure antiwear agents?
Here are some characteristics of sulfurized extreme pressure antiwear agents:
Characteristic | Description |
High Load Capacity | Designed to perform under heavy loads and high temperatures, providing protection against metal-to-metal contact. |
Chemical Reaction | React with metal surfaces to form iron sulfides, which act as a barrier to reduce friction, wear, and the possibility of welding. |
Temperature Range | Sulfurized additives are activated at a higher temperature range, with some operating up to 1,000°C. |
Film Formation | Form a chemical film that serves as a protective barrier between metal surfaces, reducing friction and wear. |
Active Sulfur Content | Differentiated by the concentration of active (or free) sulfur present, which affects their reactivity and staining properties. |
Corrosive Nature | Some sulfurized additives can be corrosive, especially to copper alloys, and their use may require careful consideration to avoid damage to certain metals. |
Wide Application | Used in various lubricants such as gear oils, hydraulic oils, and metalworking fluids due to their excellent performance under severe conditions. |
Environmental Considerations | There is a trend towards replacing sulfurized additives in some applications due to their corrosive nature and environmental concerns. |
We need that film! The sulfur family of extreme pressure anti-wear agents
In most cases, the problem we need to solve is to reduce friction, and the simplest way to reduce friction is what the public usually thinks of: oiling. This understanding is basically our most common adsorption film, just like friction modifiers. Under high temperature, heavy load, strong shear force and other conditions, the adsorption film, a simple lubrication method, can easily fail. We need to form another hard film on the contact surface, and rub this film first when friction occurs to protect the friction pair.
If we rub our hands against each other without pressure, we don’t actually need any lubricating oil, but if the pressure is very high, the friction between flesh and flesh will not be so comfortable. It will cause abrasions, adhesion, peeling and other uncomfortable situations. Therefore, we feel comfortable with moderate friction. Too slippery or too astringent is uncomfortable. When it is harsh, we need that film, which some people call "calluses". This hard callus can help us resist friction, and this chapter is going to study this callus.
In general, there are two types of additives related to calluses, one is anti-wear additives (AW) and the other is extreme pressure additives (EP). The difference between the two is the degree of difference, or the strength of the calluses. Anti-wear agents are lighter, while extreme pressure agents are heavier. In essence, they are all the same type of agents, so they are often called extreme pressure anti-wear agents.
They actually have only one common goal, which is to form a film on the contact surface in advance. And this kind of film chemistry is the most widely known type of lubricant additives, which is aimed at that film.
Let's focus on sulfur extreme pressure agent
How does S form a film?
Compared with other substances, this is relatively simple because there is only S. At present, the general composition of the film has been figured out, which is FeS+FeXOY film, which plays a role in resisting extreme pressure or wear.
For extreme pressure agents containing only S, we usually call them sulfur carrier extreme pressure agents. Although the structure of extreme pressure agents containing only S is relatively simple, it is not so easy to understand. It is simple because it is more like base oil, but with the addition of S element, and it is complex because of the diversity of the base oil itself and the miscellaneous substances that appear during the reaction.
The main reaction of extreme pressure agents containing S is to add S to a hydrocarbon carrier. Of course, in order to be added, the hydrocarbon must have a double bond, just like a fly does not stare at a seamless egg. Otherwise, it is difficult for S to drill a hole.
There are three common types of S extreme pressure agents, which are represented by three letters:
Sulfurized olefins, mainly sulfurized isobutylene. (A)
Sulfurized synthetic esters: (lighter colors): unsaturated esters (B)
And sulfurized fats: (darker colors): unsaturated fats (C)
The biggest characteristic of sulfides is not just sulfur. Many characteristics depend on the raw materials and the process of sulfidation. In theory, the sulfidation of organic matter is not complicated, but its molecular formula cannot be written out at all. The reason is that during the whole process of sulfidation, many uncertain substances will appear, such as whether it is disulfide, trisulfide or polysulfide, whether there is a bridging structure of S, etc. Therefore, the S element is too varied and can adapt to any valence.
FIG. 1 Valence state of sulfur
There are many raw materials that can be sulfided, such as vegetable oils, animal oils, fatty acids, synthetic esters and olefins. The S required for the reaction is also diverse, such as S8, H2S and other substances. The main differences in the process are direct sulfidation using natural sulfur such as S8, or using H2S or thiol, etc. The difference in process will result in the product containing different types of substances, and the color will also be related to the composition.
Differences in raw materials, production processes, S content, and S activity have led to differences in the application areas of S additives.
Extreme pressure performance
Many people think that this extreme pressure property mainly depends on the amount of S, which is wrong; because the anti-wear extreme pressure property of S compounds is to form a film, so those who like to get close to the film the most have the opportunity to react the S they carry with Fe to form a film, so those who are more likely to contact the polar contact surface have strong extreme pressure resistance, so the order is A<B<C. This part is mainly due to the base oil of the S carrier. This factor is the most critical.
Activity
This is also an interesting topic, that is, don't think that having S is enough. The activity of S is the most important factor that affects the extreme pressure properties besides the raw materials. In layman's terms, it means whether S can run out of the base oil of the S carrier by itself and find Fe to complete the extreme pressure film by itself. The one with high activity will naturally have a good extreme pressure resistance effect, and the one with poor activity will be average. This part of activity has nothing to do with the base oil, but mainly depends on the S part. For example, monosulfide and disulfide are basically not that active, while pentasulfide is highly active. In layman's terms, C can no longer catch S, so S goes out. Of course, there will be differences in activity at different temperatures. Activity will greatly affect performance. The stronger the activity, the better the extreme pressure effect, but the more severe the corrosion to metal, so special attention should be paid during use.
Generally speaking, as an anti-wear additive, it is natural to hope that the activity is low, and as an extreme pressure agent, the activity should be higher. The activity of double S in ZDDP is not that high. For general industrial oils and vehicle oils, the activity of S is relatively low, and it mainly plays the role of an anti-wear additive. For industrial and vehicle gear oils, the activity should be moderate, otherwise the extreme pressure effect will not be strong. When it comes to metalworking fluids, the activity of sulfur must be very high, especially in high-temperature cutting areas, where high-strength extreme pressure properties must be guaranteed.
Antioxidation
The main effect of this is inactive S, while active S goes to process metals. Only inactive S will gradually come into contact with oxygen to replace hydrocarbon oxidation.
Lubricity
This is very simple and mainly related to the base oil, so A<B<C
Color
We often see the distinction between dark and light colors. Generally speaking, there are two aspects that affect it, one is the raw material, and the other is the production process; generally speaking, if the H2S route and the thiol route are used, the color will be lighter, and if the raw material is fat, the color will be darker. The principle is quite simple, that is, whether the finished product still contains double bonds or other color-developing groups. There is no good or bad color. The key is to see which aspect of the performance you need, or it is a balanced body. For color issues, please refer to the base oil color article at the end of the article. The principle is the same.
Table 1 Performance comparison table
Solubility and polarity
A<B< C. This is also mainly affected by the base oil. Don't underestimate this solubility. Many of them are greatly discounted because of the poor dissolution effect of additives.
Viscosity
This is also mainly caused by the base oil. Generally speaking, A<B<C
Polymerization degree
This is mainly reflected in the control of raw materials and vulcanization process. For the results, there are two extremes. One is that the light-colored, fully saturated sulfides we need are closer to the oil additive route, and the other is that we need dark sulfides, which are closer to high extreme pressure. But no matter which line, the most important thing is that rubber-like substances cannot be formed. In this way, the approximate order of polymerization stability is A<B<C.
Oxidation stability and storage stability
The oxidation stability is opposite to the polymerization degree. The easier it is to polymerize in the later stage, the weaker the oxidation stability, so the order is A>B>C
Application
Sulfur additives are used as the seasoning package with the banner, which is definitely widely used, but the main ones are metalworking oil, gear oil, grease, guide rail oil and tractor multi-functional oil.
Finally, it should be stated that the use of single sulfur-containing additives alone is becoming less and less, and more additives are needed for use. And sometimes in order to balance many properties, we often mix several raw materials for use, which is also for balance.
UNPChemicals sulfur family of extreme pressure anti-wear agents
UNPChemicals produces various types of extreme pressure anti-wear agents, mainly including phosphate esters and sulfur-based extreme pressure anti-wear agents. The products can be used in automotive oils, industrial oils, greases, metalworking oils and other fields. The following table shows some sulfur-based extreme pressure anti-wear agents from UNPChemicals.
Product name | Composition | CAS NO. |
PSAIL 3530 | 268567-32-4 | |
PSAIL T309 | Triphenyl thiophosphate (T309) | 597-82-0 |
PSAIL 2110 | Liquid triphenyl thiophosphate | 126019-82-7 |
PSAIL T323 | Dialkyl dithiocarbamate (T323) | 10254-57-6 |
PSAIL PS20 | Tertiary dodecyl polysulfide | 68425-15-0 |
PSAIL PS32 | Tertiary dodecyl polysulfide | 68425-15-0 |
Professional Lubricant Additive Manufacturer
UNPChemicals, aka Luoyang Pacific United Petrochemical Co., Ltd., focuses on the application and development of special lubricating grease additives such as MoDTC, MoDTP, molybdenum amide, thiadiazole metal deactivators, and phosphate esters. With nearly 30 products in seven series, including extreme pressure anti-wear agents and special grease additives, it is a global manufacturer of special lubricating grease additives and a national high-tech enterprise with great influence and leading role in the industry.