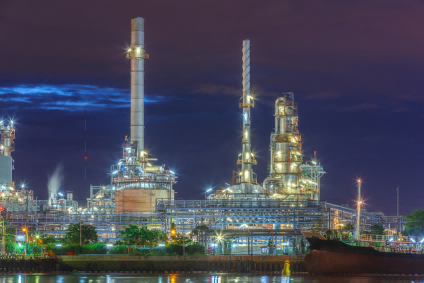
Water-Based Mud Corrosion Inhibitor: The "Guardian Angel" in Drilling Fluids
1. What is a Water-Based Mud Corrosion Inhibitor?
Water-based mud corrosion inhibitor is a chemical additive used in drilling fluids, primarily to slow down or prevent the corrosion of metal equipment and pipelines during drilling operations. Drilling fluids (mud) play a crucial role in oil and gas exploration, as they help cool the drill bit, carry rock cuttings, and stabilize the wellbore. However, water, salts, and other chemicals in the drilling fluid can cause corrosion to metal equipment, especially under high-temperature, high-pressure, and acidic conditions. Water-based mud corrosion inhibitors form a protective film on the metal surface through adsorption, effectively reducing the corrosion rate and extending the service life of the equipment.
The mechanisms of water-based mud corrosion inhibitors include the following aspects:
Adsorption: Corrosion inhibitor molecules adhere to the metal surface through physical or chemical adsorption, forming a protective film that prevents corrosive media from contacting the metal.
Electrochemical Action: Corrosion inhibitors alter the electrochemical properties of the metal surface, inhibiting the corrosion reaction.
Film Formation: Corrosion inhibitors form a dense protective film on the metal surface, preventing the penetration of corrosive media.
2. Characteristics of Water-Based Mud Corrosion Inhibitors
Water-based mud corrosion inhibitors have the following notable characteristics:
2.1 High Efficiency
Water-based mud corrosion inhibitors can achieve significant corrosion inhibition effects at very low concentrations. By forming a dense protective film, they effectively isolate the metal surface from corrosive media, significantly reducing the corrosion rate. For example, some inhibitors can achieve a corrosion inhibition efficiency of over 90% at concentrations as low as 50 ppm.
2.2 Environmental Friendliness
With increasingly stringent environmental regulations, the development of water-based mud corrosion inhibitors has focused more on environmental friendliness. Many inhibitors use biodegradable components to minimize environmental pollution. For instance, some inhibitors can rapidly degrade in natural environments without causing long-term ecological impacts.
2.3 High Temperature and Pressure Resistance
In deep and ultra-deep well drilling, drilling fluids often face extreme high-temperature and high-pressure conditions. Water-based mud corrosion inhibitors exhibit excellent thermal and chemical stability, maintaining effective corrosion inhibition performance under harsh conditions. For example, some inhibitors can remain stable at temperatures up to 200°C and pressures exceeding 100 MPa.
2.4 Multifunctionality
In addition to corrosion inhibition, water-based mud corrosion inhibitors also possess auxiliary functions such as inhibiting bacterial growth and reducing mud foam, thereby improving the overall performance of drilling fluids. For instance, some inhibitors can simultaneously inhibit the growth of sulfate-reducing bacteria, preventing microbial corrosion.
3. Classification of Water-Based Mud Corrosion Inhibitors
Water-based mud corrosion inhibitors can be classified into the following categories based on their chemical structure and function:
3.1 Imidazoline (Amino, Hydroxyethyl)
Imidazoline-based corrosion inhibitors are a widely used class of organic corrosion inhibitors, featuring an imidazoline ring and functional groups such as amino and hydroxyethyl. These inhibitors adsorb onto the metal surface, forming a dense protective film that effectively reduces corrosion. The introduction of amino and hydroxyethyl groups enhances the hydrophilicity and adsorption capacity of the inhibitors, ensuring good corrosion inhibition performance even under high-temperature and high-pressure conditions.
Molecular Formula: C₅H₈N₂ (imidazoline ring) + NH₂ (amino) + C₂H₄OH (hydroxyethyl)
Structural Features: The imidazoline ring exhibits high chemical stability, while the amino and hydroxyethyl groups enhance the molecule's hydrophilicity and adsorption capacity.
Application Case: In a deep well drilling project, the use of amino-imidazoline corrosion inhibitors reduced the corrosion rate of drill pipes by 60%, significantly improving drilling efficiency.
3.2 Imidazoline (Modified)
Modified imidazoline corrosion inhibitors are a new class of inhibitors obtained by chemically modifying traditional imidazoline molecules. Common modifications include the introduction of long-chain alkyl groups and sulfonic acid groups. These modifications not only improve the solubility and dispersibility of the inhibitors but also enhance their adsorption capacity on metal surfaces, further boosting corrosion inhibition performance.
Molecular Formula: C₅H₈N₂ (imidazoline ring) + R (long-chain alkyl) + SO₃H (sulfonic acid group)
Structural Features: Long-chain alkyl groups enhance the hydrophobicity of the inhibitor, while sulfonic acid groups improve its water solubility and dispersibility.
Application Case: In an acidic gas field development project, the use of modified imidazoline corrosion inhibitors reduced the corrosion rate of drill pipes and casings by 70%, significantly extending equipment service life.
3.3 Imidazoline (Ethoxylated)
Ethoxylated imidazoline corrosion inhibitors are obtained by introducing ethoxy chains into imidazoline molecules. The ethoxy chains significantly improve the water solubility and dispersibility of the inhibitors, allowing them to distribute more evenly in drilling fluids. Additionally, ethoxy chains enhance the adsorption capacity of the inhibitors on metal surfaces, thereby improving corrosion inhibition performance.
Molecular Formula: C5H8N2 (imidazoline ring) + (C2H4O) (ethoxy chain)
Structural Features: The length of the ethoxy chain can be adjusted as needed to optimize the water solubility and adsorption performance of the inhibitor.
Application Case: In an ultra-deep well drilling project, the use of ethoxylated imidazoline corrosion inhibitors reduced the corrosion rate of drill pipes by 60%, significantly improving drilling efficiency.
3.4 Oligomeric Ester Amine (Polyquaternary Ammonium Salt)
Polyquaternary ammonium salt corrosion inhibitors are a class of high-molecular-weight inhibitors containing multiple quaternary ammonium salt groups and ester groups. These inhibitors form a dense protective film on metal surfaces through electrostatic adsorption and chemical bonding, effectively reducing corrosion. Polyquaternary ammonium salt inhibitors exhibit excellent corrosion inhibition performance and thermal stability, making them suitable for high-temperature and high-pressure environments.
Molecular Formula: [N+(CH3)3] (quaternary ammonium salt group) + [COO](ester group)
Structural Features: The long molecular chains of polyquaternary ammonium salts enable the formation of dense protective films, while ester groups enhance the adsorption capacity of the inhibitors.
Application Case: In an acidic gas field development project, the use of polyquaternary ammonium salt corrosion inhibitors reduced the corrosion rate of drill pipes and casings by 70%, significantly extending equipment service life.
4. Applications of Water-Based Mud Corrosion Inhibitors
Water-based mud corrosion inhibitors are widely used in oil and gas exploration. Below are their main application areas and specific cases:
4.1 Deep and Ultra-Deep Well Drilling
In deep and ultra-deep well drilling, drilling fluids often face extreme high-temperature and high-pressure conditions, making metal equipment and pipeline corrosion a significant issue. Water-based mud corrosion inhibitors form dense protective films, effectively reducing the corrosion rate of metal equipment and extending its service life. For example, in an ultra-deep well drilling project, the use of ethoxylated imidazoline corrosion inhibitors reduced the corrosion rate of drill pipes by 60%, significantly improving drilling efficiency.
4.2 Acidic Gas Field Development
In acidic gas field development, corrosive gases such as hydrogen sulfide and carbon dioxide in drilling fluids severely corrode metal equipment. Water-based mud corrosion inhibitors adsorb onto metal surfaces, forming protective films that isolate the metal from corrosive gases, thereby reducing the corrosion rate. For example, in an acidic gas field development project, the use of polyquaternary ammonium salt corrosion inhibitors reduced the corrosion rate of drill pipes and casings by 70%, significantly extending equipment service life.
4.3 Offshore Drilling
In offshore drilling, saltwater and microorganisms in drilling fluids cause severe corrosion to metal equipment. Water-based mud corrosion inhibitors inhibit microbial growth and form protective films, effectively reducing the corrosion rate of metal equipment. For example, in an offshore drilling project, the use of modified imidazoline corrosion inhibitors reduced the corrosion rate of drill pipes and casings by 50%, significantly extending equipment service life.
4.4 Shale Gas Development
In shale gas development, the high salinity and high-temperature environment of drilling fluids cause severe corrosion to metal equipment. Water-based mud corrosion inhibitors form dense protective films, effectively reducing the corrosion rate of metal equipment. For example, in a shale gas development project, the use of amino-imidazoline corrosion inhibitors reduced the corrosion rate of drill pipes and casings by 65%, significantly extending equipment service life.
4.5 Other Applications
In addition to the above applications, water-based mud corrosion inhibitors are also widely used in geothermal drilling and coalbed methane development. In these fields, water-based mud corrosion inhibitors form protective films, effectively reducing the corrosion rate of metal equipment and extending its service life.
Conclusion
As an essential additive in drilling fluids, water-based mud corrosion inhibitors play a critical role in oil and gas exploration. By forming dense protective films, they effectively reduce the corrosion rate of metal equipment and extend its service life. With increasingly complex drilling environments and stricter environmental regulations, the development and application of water-based mud corrosion inhibitors will face more challenges and opportunities. In the future, with the emergence of new materials and technologies, the performance of water-based mud corrosion inhibitors will be further enhanced, providing more reliable protection for oil and gas exploration.