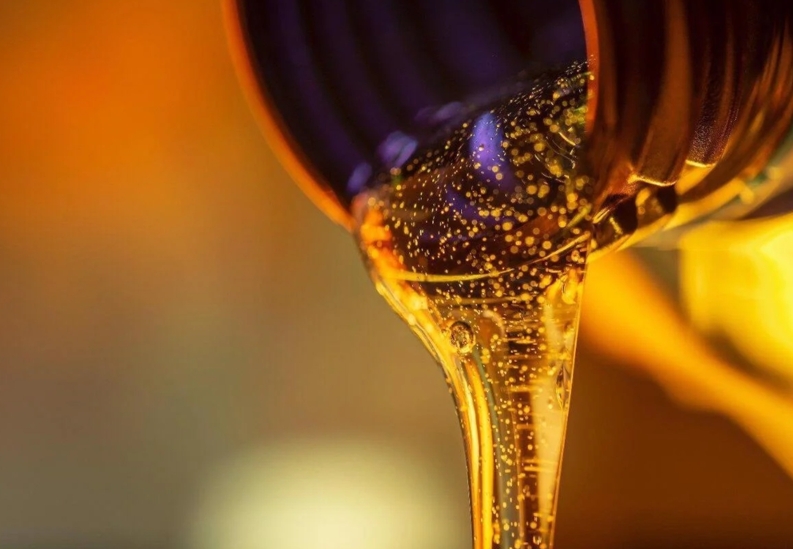
The role of metal deactivators in the lubricant industry
Comprehensive Overview of Metal Deactivators
Metal deactivators, also known as metal passivators, are crucial chemical additives designed to prevent oxidative degradation and extend the lifespan of materials susceptible to damage from metal ions. These additives are widely utilized in industries such as automotive, electrical, and polymer manufacturing, where metal ions like copper and iron can accelerate the deterioration of products. This article delves into the essential aspects of metal deactivators, including their advantages, functionality, importance in lubricating oils, types, effects, application scenarios, and considerations when selecting them.
What Are Metal Deactivators?
Metal deactivators are specialized additives that neutralize the catalytic activity of metal ions, such as copper and iron, which can promote oxidation reactions. These metal ions often accelerate the degradation of lubricants, fuels, and plastics. By binding to the metal ions and forming stable complexes, metal deactivators prevent these harmful reactions and significantly reduce the risk of oxidation, thus preserving the integrity of the materials.
Advantages of Using Metal Deactivators
The application of metal deactivators provides numerous benefits, including:
• Extended Product Lifespan: By preventing oxidation, these additives help extend the life of lubricants, fuels, and polymers.
• Improved Performance: Metal deactivators maintain the efficiency of mechanical systems, ensuring optimal performance of lubricants and fuels.
• Cost Savings: By reducing the frequency of degradation, metal deactivators decrease the need for maintenance and replacement, resulting in long-term cost savings.
• Prevention of Corrosion and Wear: These additives also help reduce corrosion and wear in metal parts by inhibiting metal-catalyzed oxidation.
Key Features of Metal Deactivators
Metal deactivators are engineered to have specific features that make them highly effective and reliable in various industrial applications:
• High Specificity: These additives selectively bind with specific metal ions, preventing unwanted interactions with other materials.
• Thermal Stability: Many metal deactivators are designed to endure high temperatures, making them suitable for use in demanding, high-heat environments.
• Compatibility: These additives are compatible with a wide variety of base materials, ensuring that they do not alter the essential properties of the systems in which they are used.
• Non-corrosive: Metal deactivators do not contribute to the corrosion of metal parts, making them essential for use in mechanical systems.
Importance in Lubricating Oils
In lubricating oils, metal deactivators are especially important because they help maintain the quality and performance of the oil, particularly in systems with metallic components prone to oxidation. They are vital in high-performance engines and hydraulic systems, where stability is critical under fluctuating and high-temperature conditions. The presence of metal deactivators ensures that lubricating oils retain their protective properties throughout their life cycle, safeguarding engine parts and ensuring the smooth operation of mechanical systems.
Effects Achieved by Metal Deactivators
Metal deactivators provide several key benefits:
• Fluid Stabilization: They significantly improve the stability of lubricants, fuels, and other fluids, preventing oxidative degradation.
• Byproduct Prevention: By inhibiting oxidation, these additives reduce the formation of harmful byproducts such as acids, sludges, and varnishes.
• Enhanced Safety and Reliability: Stable fluids result in safer and more reliable operation of mechanical and electrical systems.
Application Areas of Metal Deactivators
Metal deactivators are used across a wide range of industries:
• Automotive: To protect engine oils and transmission fluids from metal-catalyzed oxidation.
• Electrical: In transformer oils, where copper ions can lead to degradation.
• Plastics and Rubber: To prevent oxidation during processing and enhance the longevity of finished products.
Considerations for Selecting Metal Deactivators
When choosing a metal deactivator, several factors should be taken into account:
• Target Metal: Identify the primary metal ions in the system to ensure the deactivator is effective.
• Compatibility and Stability: The deactivator should be compatible with the system's materials and remain stable under operating conditions.
• Environmental and Safety Compliance: Select additives that comply with environmental regulations and safety standards.
Metal deactivators are indispensable additives that significantly enhance the stability, performance, and longevity of products exposed to metal ions. By effectively neutralizing the catalytic effects of these ions, metal deactivators help prevent oxidation, corrosion, and wear, offering crucial benefits across multiple industries. Proper selection and application of these additives are vital to maximizing their benefits and ensuring the longevity and efficiency of the systems in which they are used.
Professional lubricant additive metal deactivator manufacturer UNPChemicals in China
UNPChemicals, also known as Luoyang United Pacific Petrochemical Co., Ltd. (LPUPC), focuses on the application and development of special lubricating grease additives such as MODTC, MODTP, molybdenum amide, thiadiazole metal deactivators, and phosphate esters. With nearly 30 products in seven series, including extreme pressure anti-wear agents and special grease additives, it is a global manufacturer of special lubricating grease additives and a national high-tech enterprise with great influence and leading role in the industry. If you are interested in lubricant additive metal deactivator products, feel free to contact UNPC chemicals.