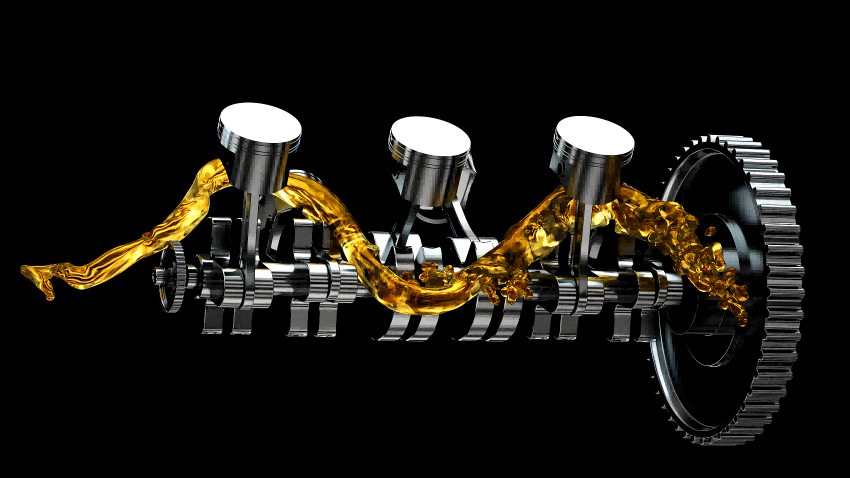
Lubricant Additives - Friction Modifiers
What are Lubricant Additives?
Lubricant additives are materials blended into lubricants to enhance or impart specific properties to the lubricant or to mitigate or eliminate certain detrimental effects. As modern machinery operates under increasingly demanding conditions, the requirements for lubricants have become more stringent, often necessitating multifunctional capabilities. This has made additives an essential component of lubricants.
Additives can be categorized into three main functions:
1. Protecting the lubricated surface
2. Improving lubricant performance
3. Protecting the lubricant itself
They can be further classified as:
1. Protecting the lubricated surface : Includes oiliness agents, anti-wear/extreme pressure agents, detergents/dispersants, and rust/corrosion inhibitors.
2. Improving lubricant performance : Includes viscosity index improvers, pour point depressants, emulsifiers and demulsifiers, tackifiers, and seal swell agents.
3. Protecting the lubricant itself : Includes antioxidants, metal deactivators, antifoam agents, and antimicrobial agents (for emulsions).
What are Friction Modifiers?
Friction modifiers, also known as oiliness agents, are additives typically used in lubricating oils, greases, or other lubricating materials. Their primary function is to reduce the coefficient of friction by forming a thin film on the friction surface or altering the surface's physicochemical properties, thereby minimizing energy loss and wear. These additives significantly enhance the efficiency of mechanical systems, extend equipment lifespan, and in some cases, reduce noise and vibration. Friction modifiers are widely used in automotive engine oils, industrial gear oils, hydraulic fluids, and other applications, making them an indispensable component of modern lubrication technology.
Classification of Friction Modifiers
1. Animal and Vegetable Oils :
These oils exhibit excellent friction-reducing and adhesive properties but have poor oxidation stability, limited solubility in mineral oils, and scarce resources. They are primarily used in rolling equipment, with a trend toward replacing them with alternatives.
2. Fatty Acids and Their Derivatives :
Fatty acids such as stearic acid and oleic acid are effective friction modifiers, particularly in reducing static friction coefficients and preventing stick-slip phenomena at low speeds. They exhibit synergistic effects when used with benzotriazole. However, their drawbacks include poor oil solubility and corrosiveness, which can be mitigated by using fatty alcohols and esters.
3. Sulfurized Fats :
These contain sulfur in their molecular structure, enabling them to form both physical and chemical adsorption films, providing anti-wear and extreme pressure properties. Examples include sulfurized whale oil and sulfurized cottonseed oil, used in cutting oils, spindle oils, and way oils. Sulfurized fats can also serve as anti-wear/extreme pressure agents.
4. Dimer Acids :
Known for their low-temperature performance and solubility in hydrocarbons, dimer acids are used in rolling oils.
Other friction modifiers include octadecylamine, butyl oleate, sulfurized olefins, cottonseed oil, and benzotriazole fatty acid amine salts.
UNPChemical's Friction Modifiers
UNPChemicals is a professional and trusted supplier of high-quality friction modifiers tailored to your workflows and products. If you are seeking high-performance friction modifier solutions, feel free to contact us.
- Molybdenum Dithiophosphate (MoDTP) MSAIL® 300L : A liquid organic molybdenum friction modifier containing sulfur and phosphorus, it significantly reduces the friction coefficient of oil products and offers extreme pressure, anti-wear, and antioxidant properties. It is widely used in internal combustion engine oils, industrial lubricants, metalworking fluids, and greases.
- Molybdenum Dithiocarbamate MSAIL® 525A MoDTC : A phosphate-free liquid organic molybdenum friction modifier that effectively reduces friction coefficients and provides anti-wear and antioxidant functions. It is used in internal combustion engine oils, industrial lubricants, metalworking fluids, and greases.
- Organomolybdenum Complex (S/P-free) MSAIL® 8550 : A versatile and environmentally friendly lubricant additive with exceptional friction-reducing properties, superior performance when combined with sulfur additives, and antioxidant synergism. It is ideal for internal combustion engine oils, industrial lubricants, metalworking fluids, and greases.
- Nitrogen-containing Boric Acid Esters FMET® 2890 : An ashless friction modifier free of sulfur and phosphorus, offering excellent friction reduction, wear resistance, and corrosion inhibition. It is widely used in internal combustion engine oils, industrial lubricants, metalworking fluids, and greases.
Mechanism of Friction Modifiers
Friction modifiers primarily reduce friction or adjust the friction-speed curve and the ratio of static to dynamic friction coefficients under mixed lubrication conditions.
Figure 1: Friction Modifier Molecule
Friction modifiers are typically long-chain organic compounds with more than 10 carbon atoms, featuring a highly polar group at one end, such as fatty acids, alcohols, amines, or esters. The polar group of the friction modifier molecule adsorbs onto the metal surface via van der Waals forces or chemical bonds, while the hydrocarbon chain extends into the lubricant. At sufficient concentrations, these molecules form densely packed, parallel layers perpendicular to the metal surface, with adjacent hydrocarbon chains attracting each other laterally, promoting dense molecular arrangement. Multiple layers of adsorbed molecules can form, with the thickness of the adsorbed film depending on the strength of the polar groups.
Figure 2: Lubricating Film on the Lubricated Surface
The diagram illustrates hydrodynamic lubricating films and adsorbed friction modifier layers on two lubricated surfaces. Outside the metal crystal surface lies an oxide layer, followed by an oxide-rich layer and an adsorption layer. The hydrocarbon chains are represented by long dashes, and polar groups by small dots. The weak attraction between methyl groups and methylene groups within and between molecules allows the multilayer film to withstand high pressures while remaining easily shearable, akin to sliding a deck of cards.
Adsorption is a dynamic process, with polar molecules on the metal surface repeatedly adsorbing and desorbing during relative sliding. Adsorption is exothermic, with adsorption heat indicating the strength of adsorption. Higher adsorption heat results in more stable films. As temperature rises, the adsorption equilibrium shifts toward desorption, weakening the film.
Adsorption can be classified into physical and chemical adsorption:
- Physical Adsorption : Relies on van der Waals forces, with adsorption heat ranging from 8.4 to 42 kJ/mol. It is reversible.
Figure 3: Physical Adsorption Model
- Chemical Adsorption : Involves a chemical reaction between the metal surface and the adsorbate, forming a strong monolayer. The adsorption energy includes chemical bond energy, with adsorption heat ranging from 42 to 420 kJ/mol. Chemical adsorption is less reversible and more stable, capable of withstanding higher loads and temperatures.
Figure 4: Chemical Adsorption Model
As temperature increases, desorption becomes dominant. At a critical temperature, the adsorbed film can completely detach. For physical adsorption, this temperature is the melting point of the adsorbed compound; for chemical adsorption, it is the melting point of the adsorbed metal soap. Soap melting points are generally below 200°C, limiting the use of oiliness agents. Above 200°C, friction modifiers lose effectiveness, and anti-wear/extreme pressure agents are required to protect the metal surface.
Figure 5: Schematic Diagram of Asperities Shearing the Friction Modifier Molecular Layer
The diagram also shows a multilayer adsorbed film being sheared by a surface asperity at a weak plane, such as between methyl groups of adjacent molecules. After shearing, the film quickly reforms due to strong directional forces, allowing the surface to withstand repeated shear. However, the time interval between shear events must exceed the time required for film regeneration.
The thickness and effectiveness of the adsorbed film depend on several factors:
1. Polarity of the Group : Stronger polarity results in thicker films. Adsorption efficacy decreases in the order: amine > acid > alcohol > ester.
2. Chain Length : Longer hydrocarbon chains yield thicker films.
3. Molecular Shape : Slender molecules allow more adsorption per unit area, forming tougher films.
4. Base Oil Chain Length : Indirectly affects film toughness; films are tougher when adsorbed and base oil molecules have similar chain lengths.
5. Friction Modifier Concentration : Higher concentrations enhance friction reduction, but the effect plateaus beyond a certain point. Optimal concentration is typically between 0.5% and 1%.
6. Temperature : High temperatures intensify desorption, weakening the film. At the critical temperature, the film detaches completely.
7. Metallurgical Factors : Greater metal surface adsorption results in tougher films. Surface energy, oxide layers, and alloy composition also influence adsorption. For example, stainless steel and titanium are harder to lubricate due to their oxide layers but can be improved via anodizing.
8. Impurities : Impurities can reduce film thickness by competing for adsorption sites. Aromatic molecules and oxidation products, for instance, can hinder friction modification. Lubricant formulations must be carefully balanced to achieve optimal performance.