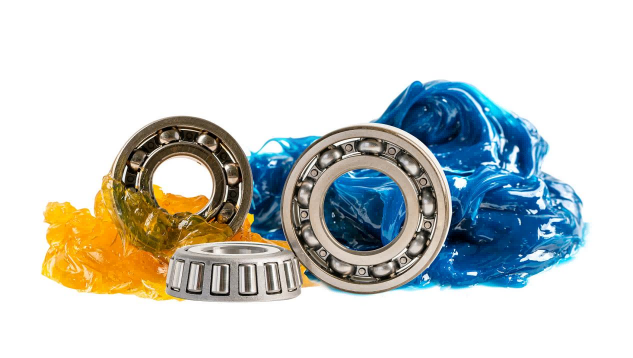
Functionalization research of grease products
What are special grease additives?
Grease additives are chemical substances added to grease to improve its performance and extend its service life, usually accounting for 0.5% to 10% of the weight of the grease. They include antioxidants, extreme pressure anti-wear agents, rust and corrosion inhibitors, friction modifiers, structural modifiers, fillers, dyes, viscosity index improvers, etc., which can effectively improve the grease's antioxidant, anti-wear, rust resistance, lubricity, colloid stability and other properties, so that the grease can better protect mechanical equipment under different working conditions and reduce maintenance costs.
What are the special grease additives from UNP Chemicals?
EPSAIL® T351: Molybdenum dibutyl dithiocarbamate EPSAIL® T351 is an advanced solid organic molybdenum extreme pressure anti-wear agent that ensures excellent antioxidant and anti-wear properties in greases and lubricants. It can serve as a complete or partial replacement for molybdenum disulfide.
EPSAIL® 8088: Inorganic extreme pressure agent EPSAIL® 8088 is a biodegradable additive containing sulfur and phosphorus elements, primarily used as an extreme pressure anti-wear agent for lubricating greases. It delivers exceptional performance in demanding applications, especially in industries like mining, construction, and heavy machinery with high load performance requirements.
EPSAIL® 8290: Thiadiazole dimer EPSAIL® 8290 is a high-performance additive that delivers exceptional extreme pressure performance and outstanding anti-wear and anti-oxidation properties when dispersed in lubricating greases. With applications that span steel plants and heavy load equipment to various high-pressure lubricating greases, It can also be used as a rubber vulcanization accelerator. EPSAIL® 8290 plays a pivotal role in promoting equipment longevity, reliability, and overall efficiency.
Functionalization research of grease products
Mechanical equipment is an important tool for industrial production, and good equipment operation depends on lubrication conditions. Lubrication refers to the use of liquids, gases, solids, etc. to separate friction surfaces to avoid direct contact between friction surfaces and reduce friction and wear. Grease is an important component of industrial lubricants. It is a plastic semi-solid lubricating material composed of thickeners and base oils. It is widely used in industries such as electronics, electricity, steel and automobiles. Due to its inherent excellent properties, grease can not only meet conventional lubrication requirements, but also has the following advantages compared with liquid lubricants (lubricating oils): good adhesion and not easy to lose; can maintain good lubrication ability under high loads; long lubrication cycle; wide applicable temperature range and working conditions; has a sealing effect. Therefore, the use of grease in machinery can simplify the mechanical lubrication system, avoid oil leakage, reduce energy consumption, and reduce environmental pollution, which is in line with the concept advocated by green chemistry.
In order to meet harsh working conditions, grease will be specially treated to improve performance to meet its use requirements. Such as adjusting functionality, adding additives, adjusting thickeners, changing base oil properties, adjusting synthesis processes, etc. Therefore, new greases have always been a hot topic of research.
The components of grease are mainly base oil, thickener and additives. From the functional classification, the main functions of grease can be divided into protection, sealing, damping, noise reduction and friction reduction.
Protection is mainly to prevent metal from contacting with air, water, acid or other corrosive gases or liquids, thereby preventing corrosion and rust on the metal surface, and playing a protective role. Some researchers added CMET® T703, T705 and T706 rust inhibitors to grease, achieving a relatively ideal protective effect, mainly because the benzotriazole in the rust inhibitor forms a chelate Cu(C6H4N3)2 with copper, which covers the surface of the copper sheet; CMET® T703 has polar groups and surfactants with asymmetric structures in its molecular structure. Its polar groups rely on Coulomb force and chemical bonds to be directional adsorbed on the oil-metal interface to form a protective film. The surfactant can adsorb and capture polar corrosive substances so that they do not contact the metal, thereby achieving a protective effect.
The function of sealing is that when grease is applied to the bearing, it can form a grease ring with a certain sealing effect, preventing dust, debris and various gases from entering the bearing. The sealing function of grease can be improved by high-viscosity base oil, thickener and adhesive. Its strong sealing is due to the high viscosity of the base oil, which leads to the high kinematic viscosity of the grease, so that it adheres strongly to the bearing surface during operation, so that a long-term shear-resistant sealing oil film is formed on the bearing surface, effectively preventing impurities from entering the bearing.
Damping performance not only plays a lubricating role, but most importantly, it can also make electronic components give people a comfortable "feel". Its mechanism is that the grease can form a uniform and stable oil film on the friction surface during operation. Through high-viscosity base oil, thickener and viscosity enhancer, the adhesion and mechanical stability of the grease are improved; the damping torque is stable under different temperature conditions, the rotation is smooth, and it can be compatible with most types of plastics, thereby improving the damping performance of the grease.
The mechanism of noise reduction is mainly that the grease forms an oil film to gradually consume the energy of vibration, or convert it into other forms of energy, thereby achieving the effect of vibration reduction and noise prevention. If the production is kept clean, the noise reduction performance of the grease can be improved by choosing a base oil with high viscosity and a thickener with short and uniform fibers. A base oil with high viscosity can produce a thicker oil film, which is easier to resist vibration; in terms of attenuating the vibration of the bearing, a grease with short soap fibers is better than a grease with long soap fibers. Since the oil film formed by this grease during work can effectively reduce the tiny alternating force caused by the elastic change of the contact surface, the vibration and noise of the grease are reduced.
The friction reduction mechanism is to form a layer of oil film on the friction surface, thereby improving the friction between the interfaces, reducing wear, and avoiding bite welding and tearing wear on the metal surface. Some researchers have used tetrafluoroethylene (PTFE) particles to improve the friction reduction performance of urea-based grease. Such nanoparticles can form a composite boundary lubrication film with the active elements of the lubricating oil on the friction surface, preventing direct contact between metals, reducing friction, and reducing wear, thereby achieving a friction reduction effect. Inorganic and organic anti-friction agents have different mechanisms of action. For example, borates can form an extremely strong oil film to prevent the abrasion of the friction pair. At the same time, they have excellent thermal stability and can still work normally at high temperatures without corroding copper. Therefore, borates are often used as grease additives for copper friction pairs. Organic functional additives are adsorbed on the surface of the friction material through active groups, and the hydrocarbon chains are facing outward to form an adsorption film. During the friction process, the friction pairs come into contact and break the oil film. The high temperature generated causes the additive molecules adsorbed on the surface of the friction material to decompose, and the active elements contained in the groups react chemically with the friction surface to form an inorganic film. Studies have shown that in low temperature environments, a small amount of tricresol phosphate can have good anti-friction properties; under the high temperature generated during the friction process, the phosphorus element in the additive reacts with the metal to form an inorganic film, which plays an anti-friction role. However, if the amount added is increased, negative effects will be produced due to excessive reaction of the phosphorus element with the metal. 2,5-dimercapto-1,3,4-thiadiazole derivatives (such as UNPChemicals' products DMTD-8, DMTD-9 and DMTD-12) are a kind of composite lithium-based grease additives. They have long carbon chains and high polarity, and are easily adsorbed on the surface of the friction pair. During the friction process, the sulfur element in the molecule reacts chemically with the surface of the friction pair to form a chemical reaction film, which covers the surface, thereby improving the extreme pressure and anti-friction properties of the grease. There are several types of friction reduction mechanisms played by inorganic functional additives. One type is that the additive particles have high surface energy and are adsorbed on the surface of the friction material to form a physical adsorption film. The elements contained in the particles react chemically during the friction process to form a new chemical reaction film to separate the friction pair. Nano-palygorskite is a short cylindrical or granular powder containing hydroxyl groups. It has a high surface energy when dispersed in grease. When it comes into contact with the friction pair, the hydroxyl active group will be adsorbed on its surface. Then, under the action of friction, the group will undergo a complex chemical reaction with the surface of the friction pair to form a self-repairing film to protect the friction pair. The composite system of graphite and layered sodium disilicate as a lithium-based grease additive reacts with the material on the surface of the friction pair under the action of friction to form a friction-reducing film. Another mechanism is that inorganic additives have a smaller size and a nearly spherical shape, which play the role of a ball and can fill the worn parts during the friction process, such as nano ZrO2 particles as a kind of anti-friction and pressure-reducing additive for lubricating materials, on the one hand, can be deposited on the friction surface to form a physical adsorption film; on the other hand, it can fill the defective parts of the friction surface and repair the surface; nano copper particles as grease additives can play a role in repairing and film-forming. On the one hand, it fills the surface defects of the friction pair and reduces the friction resistance; on the other hand, at the repaired part, it reacts with the surface material and the substances in the oil film at a sufficiently high temperature and pressure to form a physical adsorption film; another mechanism is that inorganic additives are deposited on the friction surface during the friction process to form an amorphous or amorphous film to separate the friction material, such as 1.5% LaF3 particles in lithium-based grease can improve the load-bearing capacity and sintering load of grease, and have a good self-repairing effect on the friction surface (deposition, crystallization, spreading film), which plays a role in reducing friction; CaF2, which is also a fluoride, when used as an additive for lithium-based grease, will attract some organic matter to deposit on the friction surface to form a deposition film at the beginning of friction. As the temperature of the friction surface increases or the pressure increases, some CaF2 will react with the friction surface material and the substances in the grease to form a film layer, protecting the friction pair surface. Nano-bismuth powder and ultra-fine serpentine powder composite additives as lithium-based grease additives have good tribological properties under low, medium and high loads, especially when the mass ratio is 3:1, the performance is optimal. This is because nano-bismuth powder with smaller particle size is preferentially deposited on the friction pair surface, while serpentine powder with larger particle size and lower content is deposited on the self-repairing film formed by bismuth, and the two play a role in reducing friction together.
Looking to the future, with the development of my country's equipment manufacturing industry, new functional greases will surely play an increasingly important role in defense, aerospace, automobiles, machinery and other fields. As the research progresses, several important issues still need to be paid attention to: (1) The safety of grease, research on the biodegradability and environmental degradation and toxicity of new grease; (2) Research on the self-oxidation failure mechanism of grease in the presence of catalytic media such as metal ions and metal media during interfacial lubrication; (3) The lack of research on production processes and equipment is one of the important factors restricting the production of high-quality grease in my country, and it is necessary to organize cross-disciplinary discussions and cooperative research in multiple fields to effectively improve it.
The products of UNPChemicals mentioned in this article are as follows:
CMET® T703: Heptadecenyl imidazoline succinate CMET® T703 is an oil soluble ashless antirust additive made by neutralization of alkenyl Imidazoline and dodecenyl succinic acid. This product has excellent acid neutralization ability.
DMTD-8: Thiadiazole octyl mercaptan condensate DMTD-8 is a liquid ash-free metal deactivator, which has extreme pressure and auxiliary antioxidant effects, and is widely used in various automotive and industrial lubricating oils and metal working fluids. At very low concentrations, it can effectively prevent the corrosion of active sulfur on copper and copper alloys, and its unique composition can also inhibit the corrosion of hydrogen sulfide.
DMTD-9: Thiadiazole tert-nonyl mercaptan condensate, commercially known as DMTD-9, is an organosulfur compound carrying the CAS number 91648-65-6. As a lubricant, fuel or metalworking fluid additive, it demonstrates several key features that make it valuable in a variety of industrial and automotive applications.
DMTD-12: Thiadiazole tert-dodecyl mercaptan condensate DMTD-12 is a valuable lubricant additive, known for its ashless, extreme pressure, and oxidation resistance properties. Its ability to act as a metal choice deactivator makes it an effective for preventing corrosion and enhancing the performance and protection offered by automotive and industrial lubricants and metalworking fluids.