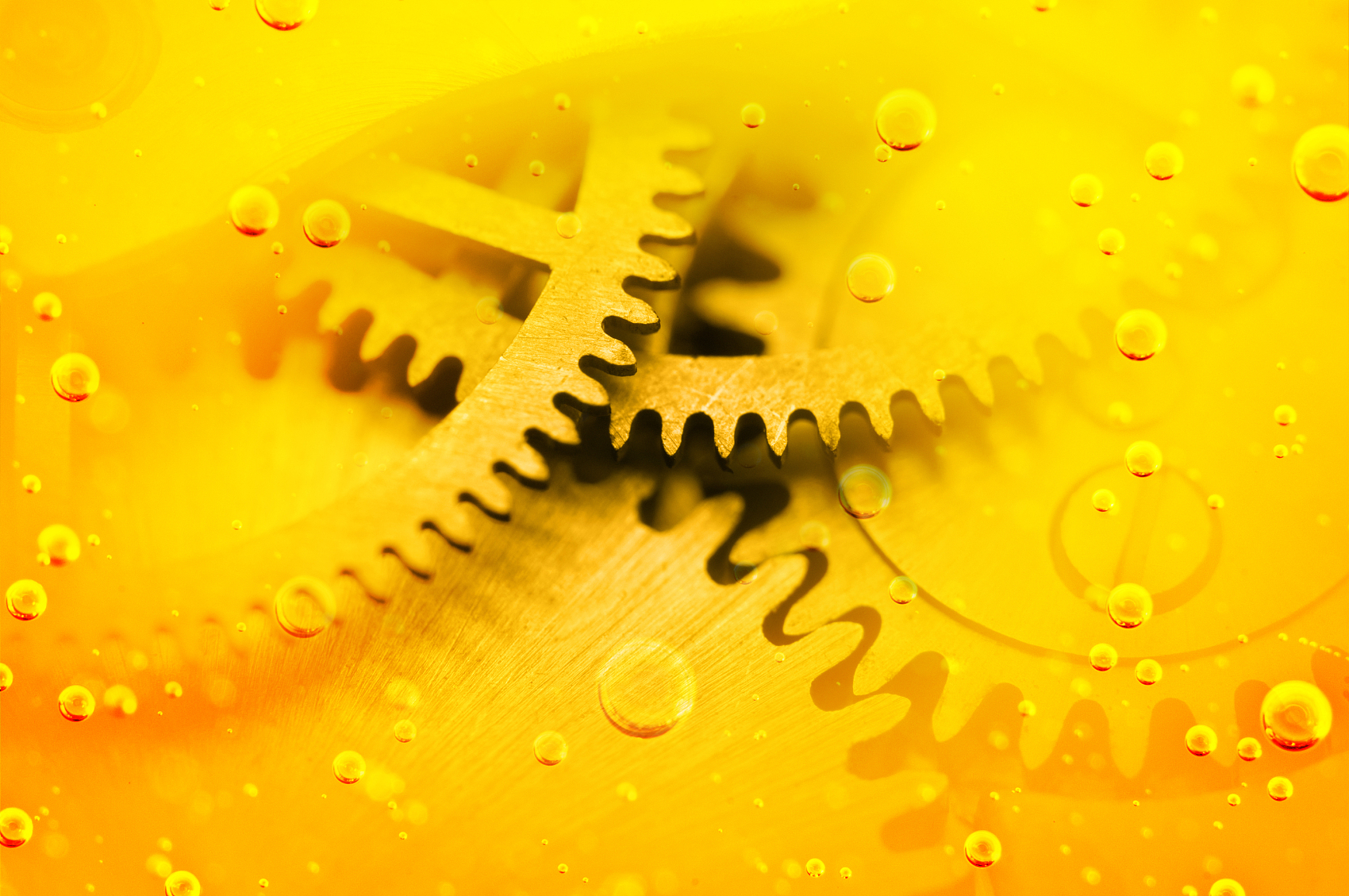
Examples of Friction Reducers for Lubricant
A friction reducer is a chemical compound that is incorporated into lubricants to reduce the friction between two moving surfaces. This reduction in friction leads to several benefits, including lower energy consumption, less wear and tear on components, and improved operational efficiency. Friction reducers are often used in high-performance lubricants for machinery such as engines, gearboxes, and industrial equipment.The primary function of a friction reducer is to create a thin layer between the moving surfaces, which prevents them from coming into direct contact. This protective layer not only reduces friction but also acts as a barrier to moisture and contaminants, which can cause damage to the surfaces.
Types of Friction Reducers
There are several types of friction reducers, each suited to different applications and operating conditions.Some of the most common types include:
Polymeric Friction Reducers
These are long-chain polymers that form a thin film on the surface of the metal. They are effective at reducing friction and improving lubrication in heavy-duty machinery, such as automotive engines and industrial compressors.
Metallic Friction Reducers
These are often made of metal particles, such as copper or molybdenum, which are suspended in the lubricant. They provide excellent wear resistance and are particularly useful in high-temperature environments.
Nano-material Friction Reducers
With the advancement of nanotechnology, nano-material friction reducers have become popular. These materials are engineered at the molecular level to create ultra-smooth surfaces and reduce friction to an exceptional degree.
Synthetic Friction Reducers
Synthetic additives, including esters and other chemical compounds, can be used to reduce friction in both high and low temperatures. They are often found in high-performance lubricants for specialized industries like aerospace and automotive.
Examples of Friciton Reducers
Friction reducers are commonly used in lubricants across various industries to reduce friction, enhance performance, and extend the life of machinery. Here are some examples of friction reducers typically found in lubricants:
1. Molybdenum Disulfide (MoS₂)
Description: Molybdenum disulfide is a solid lubricant known for its excellent ability to reduce friction under high pressure and temperature conditions. It is often used in automotive and industrial lubricants, particularly in gear oils, engine oils, and heavy-duty machinery lubricants.
Applications:
Automotive engine oils
Gear oils for heavy machinery
Industrial lubricants in high-stress applications like mining equipment
2. Graphene
Description: Graphene, a single layer of carbon atoms arranged in a hexagonal lattice, is gaining attention as a highly effective friction reducer in lubricants. It is known for its exceptional strength, thermal conductivity, and friction-reducing properties.
Applications:
High-performance motor oils
Gear lubricants
Lubricants in applications requiring extreme pressure or temperatures
3. MoDTC Molybdenum dithiocarbamate
Description: Molybdenum Dithiocarbamate MSAIL 525A MoDTC is a phosphate-free liquid organic molybdenum friction modifier, which can greatly reduce the friction coefficient of oil products, and has a variety of functions such as anti-wear and anti-oxygen, and is widely used in internal combustion engine oil, various industrial lubricants, pure oil-type metal working fluids, greases, etc.
Applications:
Synthetic engine oils
Gear oils
Hydraulic fluids
4. Zinc Dialkyldithiophosphate (ZDDP)
Description: ZDDP is a widely used additive in lubricants, known for its anti-wear properties. It works by forming a protective film on metal surfaces, reducing friction and preventing direct metal-to-metal contact, thus enhancing the performance of lubricants.
Applications:
Motor oils (particularly for high-performance and older engines)
Transmission oils
Hydraulic fluids
5. Esters (Synthetic Esters)
Description: Synthetic esters are another category of friction reducers known for their excellent lubricity. They reduce friction by providing a thin film on the surface of moving parts, which lowers the wear and tear in various types of machinery.
Applications:
Aviation lubricants
High-performance automotive oils
Industrial lubricants, particularly in compressors and turbines
6. Polymers (Polymeric Friction Reducers)
Description: Long-chain polymers can be used in lubricants to create a thin film that reduces friction. These friction reducers are effective at maintaining lubrication integrity under varying temperatures and pressures, particularly in high-load applications.
Applications:
Hydraulic fluids
Gear oils
Heavy-duty engine oils
7. Borate Esters
Description: Borate esters are used in lubricants to reduce friction and prevent wear by forming a protective film on metal surfaces. They are particularly effective in extreme pressure and high-temperature environments.
Applications:
High-performance motor oils
Industrial lubricants for metalworking processes
Gear lubricants
8. Teflon (Polytetrafluoroethylene, PTFE)
Description: PTFE, commonly known as Teflon, is a well-known friction reducer with excellent chemical stability and high lubricity. It is used in lubricants to reduce friction between moving parts, particularly in extreme conditions where other lubricants might fail.
Applications:
Heavy machinery lubricants
High-performance oils for engines and transmissions
Industrial lubricants in high-temperature applications
9. Calcium Sulfonate
Description: Calcium sulfonate is a type of detergent and dispersant that can also reduce friction when included in lubricants. It is particularly useful in marine and heavy-duty industrial applications due to its ability to perform in challenging environments.
Applications:
Marine lubricants
Industrial oils for high-load machinery
Greases used in construction and mining equipment
10. Nano-Particles (e.g., Nanodiamonds, Nanotubes)
Description: Nanotechnology has led to the development of nano-particles that are added to lubricants to drastically reduce friction. These particles, such as nanodiamonds or carbon nanotubes, are capable of filling microscopic surface imperfections, creating a smoother, more lubricated surface.
Applications:
Ultra-high-performance lubricants in aerospace and automotive industries
Lubricants for advanced machinery requiring precision and longevity
Specialty oils in high-stress, low-friction environments
These friction reducers are integrated into lubricants depending on the specific needs of the application, such as high temperature, heavy load, or long service life. By carefully selecting and adding these additives, manufacturers can optimize lubricant performance and protect machinery against wear, heat, and inefficiency.
What Are Lubricant Additives?
Lubricant additives are chemicals added to lubricants to enhance their performance and tailor their properties to specific needs. These additives can improve various aspects of lubrication, such as reducing wear, preventing corrosion, and enhancing the viscosity. Friction reducers are one of the key types of lubricant additives, designed specifically to minimize friction and reduce energy consumption.
Other common lubricant additives include:
Anti-wear agents: These additives form a protective layer on metal surfaces to reduce wear.
Corrosion inhibitors: These prevent rust and corrosion on metal components.
Viscosity index improvers: These additives help lubricants maintain their consistency across a wide range of temperatures.
How Are Friction Reducers Used in Lubricants?
Friction reducers are mixed into lubricants during the manufacturing process. Once added, they bond to the surface of the moving parts, creating a smooth, low-resistance layer that minimizes friction. This reduces the amount of heat generated during operation and helps the machinery run more smoothly.
In engines, for example, friction reducers are included in motor oil to reduce the friction between the pistons and the cylinder walls. This can result in lower fuel consumption, reduced engine wear, and extended service life for the engine.
In industrial applications, friction reducers are used in gear oils, hydraulic fluids, and other lubricants to ensure machinery operates efficiently and requires less maintenance.
How to Select Friction Reducers?
Selecting the right friction reducer for a specific application depends on several factors:
Operating Conditions
The temperature, pressure, and speed of the machinery determine which type of friction reducer is most suitable. For high-temperature applications, synthetic or metallic friction reducers may be required, while polymeric friction reducers are better for lower temperatures.
Type of Lubricant
The base lubricant (such as engine oil, gear oil, or hydraulic fluid) will influence the choice of friction reducer. Some friction reducers are compatible with specific lubricants, so it is important to choose one that works well with the intended lubricant.
Performance Requirements
If the application demands high performance under extreme conditions (e.g., racing cars or industrial machinery), then advanced friction reducers, such as nano-material or synthetic friction reducers, may be necessary.
Environmental and Regulatory Considerations
Some industries have strict environmental regulations regarding the chemicals used in lubricants. It’s crucial to choose friction reducers that are environmentally friendly and compliant with relevant standards.
Cost and Availability
Finally, cost and availability will play a role in selecting the right friction reducer. While some high-performance friction reducers may offer superior benefits, they may also be more expensive. The choice will depend on the budget and long-term goals of the operation.
Supplier of Friction Reducers
UNPChemicals is a professional lubricant additives provides high quality friction reducers and lubricant additives for global customers. If you are looking for friction reducers, feel free to contact us.