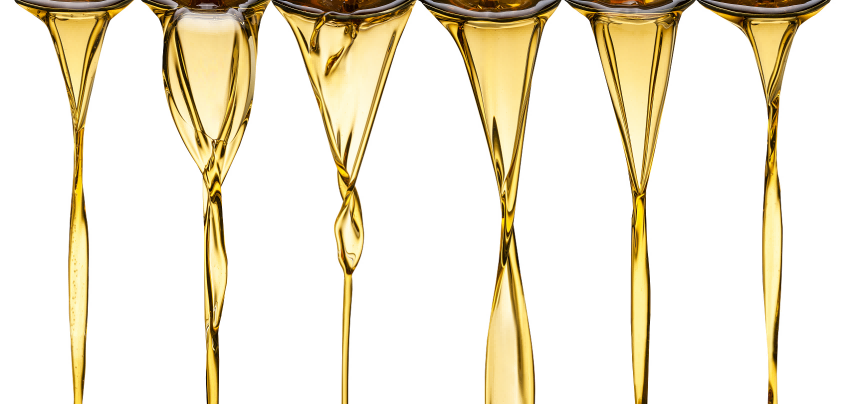
Application and development of extreme pressure anti-wear additives for lubricating oils
What are extreme pressure anti-wear additives for lubricating oils?
Extreme pressure anti-wear additives for lubricating oils are a type of additive used in lubricating oils. Their main function is to significantly reduce the wear of the friction pair surfaces under extreme working conditions such as high load, high temperature, and high speed, and prevent direct contact between metal surfaces, thereby improving the service life and operating efficiency of mechanical equipment. Extreme pressure anti-wear additives reduce the friction coefficient and disperse heat by forming a layer of chemical reaction film or physical adsorption film on the metal surface, while providing additional protection under boundary lubrication conditions to prevent abrasions, bites, and micro-motion wear caused by insufficient lubrication. Common extreme pressure anti-wear agents include compounds containing sulfur, phosphorus, and chlorine, as well as molybdenum-based compounds, which are widely used in a variety of lubricating oils such as gear oils, hydraulic oils, and engine oils to meet the lubrication needs under different working conditions.
Conventional lubricating oil extreme pressure anti-wear agent
1. Sulfur-containing extreme pressure anti-wear agent
Currently, the commonly used sulfur-containing extreme pressure anti-wear agents mainly include: sulfur-phosphoric acid nitrogen derivatives, sulfur-phosphoric acid molybdenum, sulfurized animal oil, sulfurized olefins, polysulfides, etc., among which sulfurized olefins are the most widely used. This type of additive mainly exhibits strong anti-sintering ability and good load resistance, and has an excellent compounding effect with other types of additives. Studies have shown that the difficulty of opening the C-S bond determines its extreme pressure, and the S-S bond determines its anti-wear. Generally speaking, anti-wear increases with the increase of chain length, and the initial bite load and sintering load increase significantly with the increase of the number of sulfur atoms. Under boundary lubrication conditions, sulfur-containing extreme pressure anti-wear agents undergo friction adsorption and chemical reactions with the friction surface to form a sulfur-containing inorganic film or an extreme pressure chemical reaction film of Fe2O3-FeS of more than 0.15μm in the presence of iron oxide, thereby playing an anti-scratch and anti-sintering role. It has good hydrolysis stability, high melting point, and is still effective at a high temperature of 800℃. However, people are not clear about how the various products are transformed and the interaction between them.
UNPChemicals' representative products of sulfur-containing extreme pressure anti-wear agents:
PSAIL® T307S:Ammonium thiophosphate complex esters (SPN)
PSAIL® 3530:Phosphorothioate Acrylate Derivatives is an ashless EP/AW additive with dialkyl dithiophosphate structure, especially suitable for industrial lubricating oils with FZG test requirements, such as industrial gear oil, anti-wear hydraulic oil containing ZDDP, lubricating grease and metal processing oil.
PSAIL® PS20:Tertiary dodecyl polysulfide
2. Phosphorus-containing extreme pressure anti-wear agents
The commonly used phosphorus-containing extreme pressure anti-wear agents at home and abroad are mainly: acidic dibutyl phosphite, tricresol phosphate, thiophosphate, phosphate and acidic phosphate amine salt, among which organic phosphate is the most used.
There are many varieties of phosphorus-containing extreme pressure anti-wear agents. According to the effective active elements contained, they are divided into phosphorus type, phosphorus nitrogen type and sulfur phosphorus nitrogen type. The most studied mechanism of action is phosphorus type additives. At present, it is generally believed that under friction conditions, phosphorus additives form an organic phosphate chemical reaction film on the friction surface, thus having good anti-wear properties. In phosphorus-nitrogen type additives, nitrogen elements not only have the function of inhibiting excessive corrosion of phosphorus elements, but also have the function of enhancing the lateral attraction between adsorbed molecules, enhancing the strength of the oil film, and improving the anti-wear properties. It is found that the anti-wear properties of phosphorus-nitrogen additives are not only higher than those of sulfur-containing additives, but also higher than those of sulfur-containing additives, that is, higher than sulfurized isobutylene, which has the best extreme pressure properties among sulfur agents. After reasonable compounding, on the basis of not containing sulfur, chlorine and other additives, various performance indicators completely exceed those of gear lubricants prepared with sulfur additives. Phosphorus-nitrogen type extreme pressure anti-wear additives have the characteristics of high load-bearing capacity, good compounding and excellent lubrication, as well as outstanding advantages such as simple production process and less industrial waste, and have a very broad development prospect. There are very few reports on the mechanism of action of sulfur-phosphorus-nitrogen type additives, especially the extreme pressure and anti-wear mechanism when phosphorus, nitrogen, sulfur, phosphorus and nitrogen coexist, which needs further exploration.
At present, the level of phosphorus agents in China is relatively low, and the production, compounding technology and single-agent products of phosphorus agents abroad are strictly confidential. Therefore, phosphorus agents with superior performance need to be further developed. The research and development of efficient, multifunctional, superior and biodegradable phosphorus agents (such as P-N agents and S-P-N agents), as well as the combined use of various phosphorus agents, will become the main direction of phosphorus agent development in the future.
UNPChemicals' representative products of phosphorus-containing extreme pressure and anti-wear agents:
PSAIL® 3661A/B:Tricresyl phosphate
PSAIL® 3490:PSAIL® 3490 is a specialized mixture of amine phosphate salts known for its multifunctional ashless additive characteristics. As an ashless additive, PSAIL® 3490 does not produce ash as combustion by-products, reducing engine deposits and harmful emissions. PSAIL® 3490 is a multifunctional additive, providing a range of benefits in a single product, making it highly versatile and cost-effective.
PSAIL® 2280:Amine-neutralized mixed phosphate esters is a multifunctional ashless additive structured as a phosphate ester amine salt with excellent load carrying capacity, anti-wear and corrosion protection properties. As a multifunctional additive, PSAIL® 2280 reduces the amount of anti-emulsifier and rust inhibitor and has good tribological properties, especially at higher temperatures, forming thicker boundary lubricant films. In addition, PSAIL® 2280 is widely used in metalworking fluid formulations in conjunction with sulfur carriers because of its good anti-wear properties.
3. Chlorine-containing extreme pressure and anti-wear agents
The most commonly used chlorine-containing additives in industry are chlorinated paraffin and some chlorine-containing derivatives. Chlorine-containing additives are widely used because they are cheap, have good performance, and chlorinated paraffin has good compatibility with sulfur and phosphorus. The main products produced in China are chlorinated paraffin with a chlorine content of about 42% and 52%. There has been a great development of chlorinated paraffin substitutes abroad, but the price of chlorinated paraffin substitutes is high and the extreme pressure activity is not ideal. Chlorinated paraffin is still mainly used for difficult-to-process metals. The main characteristics of chlorine-containing extreme pressure anti-wear agents are high reactivity, strong corrosiveness, and the extreme pressure anti-wear property fails when exposed to water. It decomposes into elemental chlorine or generates hydrogen chloride on the friction surface, adsorbs or reacts with the metal surface to form low-melting point films such as FeCl2 and FeCl3, and ferric chloride is easily sheared, thereby playing an extreme pressure and anti-wear role. However, ferric chloride decomposes at high temperatures, and its use temperature cannot be higher than 350℃. Due to the corrosive effect of chlorine, especially the strong corrosive effect of HCl in contact with metal surfaces, people try to reduce its dosage as much as possible, or use it in combination with other additives. However, its high activity and strong corrosive characteristics can be used in running-in to shorten the running-in time and improve the running-in effect. When the reactivity is the same, the extreme pressure performance of chlorine-based extreme pressure agents is far inferior to that of sulfur-based extreme pressure anti-wear agents. In recent years, due to increasingly stringent environmental protection requirements, chlorine agents have been gradually eliminated.
4. Organic metal salt extreme pressure anti-wear agents
Organic metal additives can be divided into zinc, molybdenum, lead, tin, antimony, titanium and other series according to the metal elements they contain.
The most commonly used metal additive is zinc dialkyl dithiophosphate (ZDDP). ZDDP is an ash-type multi-effect lubricant additive with excellent properties such as anti-oxidation, anti-wear and anti-corrosion. Since its appearance in the 1940s, it has been used as an anti-oxidation, anti-wear and anti-corrosion additive for internal combustion engine oil. So far, there is still no substance with better performance to replace it. Many scholars have analyzed the wear marks through advanced analytical instruments and found that Zn, S, P, O and Fe exist in the extreme pressure anti-wear film. From the bond energy, phosphorus belongs to phosphate, while sulfur belongs to sulfide. In recent years, Willermet found that the film is an inorganic amorphous phosphate and pyrophosphate, and some people believe that this film is an amorphous, inorganic long-chain polymer film formed by the action of iron.
Molybdenum-containing compounds occupy an important position in many lubricating materials due to their excellent tribological properties. The most commonly used molybdenum-containing compounds are: molybdenum disulfide (MoS2), oil-soluble dialkyl dithiocarbamate sulfide molybdenum oxide (MoDTC) and dialkyl dithiophosphoric acid sulfide molybdenum oxide (MoDTP). According to literature reports, dispersing MoS2 in lubricating oil can improve the tribological properties of lubricating oil, especially the anti-wear effect is more obvious under higher loads. The modified MoS2 nanoparticles have excellent friction reduction and anti-wear properties and can play a lubricating role at room temperature and medium temperature. Currently, molybdenum-containing organic compounds that can be used as lubricating grease additives are: MoDTC and MoDTP, which have better extreme pressure and anti-wear properties. In recent years, it has been found that the extreme pressure properties of highly sulfurized dithiophosphoric acid molybdenum are improved due to the increase in sulfur content. Its mechanism of action is that the sulfur-containing organic metal complex lubricant undergoes a grafting reaction with the metal matrix with the help of S atoms. Due to the increase in sulfur content, the chance of grafting reaction increases and the reaction is easy to proceed. The stronger the reaction film formed, the better the extreme pressure performance; at the same time, it is partially decomposed into MoS2 solid lubricating film, which fills the unevenness of the friction surface and relieves the friction resistance.
5. Borate extreme pressure anti-wear agent
Since Vonderveer synthesized borate additives, due to their special properties, they have been rapidly developed in recent years, and many research results have been published. Boron-type extreme pressure anti-wear agents are mainly divided into inorganic borates and organic borates. This type of additive not only has excellent extreme pressure anti-wear and friction reduction properties, but also has excellent thermal oxidation stability, and is not oxidized and denatured at higher temperatures (150°C). It has no corrosion to copper at high temperatures, has good anti-rust properties for steel, and also has good sealing adaptability, is non-toxic and odorless, and is conducive to improving the operating environment. These are the areas that phosphorus and sulfur additives cannot reach.
Many scholars have put forward different views on the extreme pressure and anti-wear mechanism of borate extreme pressure anti-wear agents, which can be summarized into two categories: deposition film formation view and boronization view. The deposition film viewpoint believes that a trace amount of borate is deposited on the friction surface through electrophoretic motion to form a deposition film. The boronization viewpoint believes that during the friction process, boron forms an interstitial compound FexBy of boron on the metal surface, and this interstitial compound can also dissolve free boron to form a solid solution, thereby forming a complex penetration layer (B/FexBy/FexOy) on the friction surface to play a role in reducing friction and anti-wear.
The tribological properties of inorganic borates are much better than those of commonly used sulfur-phosphorus extreme pressure agents, but the dispersion stability and hydrolysis stability of inorganic borate additives in oil are poor, and precipitation is easy to occur. Moreover, it is generally soluble in water but not in oil. When it comes into contact with water, the performance of borates will be reduced or consumed. When using it, it must be finely dispersed in mineral oil with the help of a dispersant, which is very inconvenient and selective.
As a lubricating oil additive, organic borates have good anti-wear and friction reduction properties, do not corrode metals, are non-toxic and odorless, but their thermal oxidation stability is obviously inferior to that of inorganic borates. Therefore, the storage stability and anti-emulsification ability of borates need to be continuously improved, and the compounding rules and compounding mechanism with other extreme pressure anti-wear additives also need to be further explored.
6. Extreme pressure anti-wear agents containing rare earth elements
Rare earths are called the "treasure house" of new materials and have attracted much attention from scientists at home and abroad. Rare earth elements are listed as key elements for the development of high-tech industries by relevant government departments in the United States, Japan and other countries. With the increasing demand for new materials, rare earths are being used more and more widely. At present, my country has achieved remarkable results in scientific research, production and application of rare earths. The important role played by rare earths in various fields of the national economy is increasingly recognized by people. Due to its unique physical and chemical properties, it has attracted widespread attention in the field of tribology. At present, a variety of organic and inorganic rare earth compounds and rare earth nanoparticles have been synthesized. Rare earth additives are difficult to dissolve in lubricating oils and are therefore widely used in greases. Studies have shown that LaF3 can increase the load-bearing capacity of lubricating grease by 10% to 100% and increase the wear life of the bonding coating by 2 to 4 times; lanthanum and cerium fluorides can improve the extreme pressure and anti-wear properties of ester oils; most rare earth oxides have better friction and wear properties at high temperatures than at low temperatures. Rare earth complexes have good anti-wear and friction reduction properties as grease additives. The extreme pressure properties of rare earth complexes without active elements are equivalent to ZDDP; while the extreme pressure properties of rare earth complexes containing active elements are better than ZDDP. Oil-water soluble rare earth complexes show better anti-wear and friction reduction properties in water than in grease. Rare earth trifluorides (such as La-Gd) and mixed rare earth fluorides can improve the anti-wear, extreme pressure and anti-scratch capabilities of lithium-based greases to varying degrees. In recent years, the research on rare earth nanoparticles has received increasing attention, and some organic-modified nano rare earth compounds such as LaF3 have shown excellent extreme pressure, anti-wear and friction reduction properties. Various research results show that rare earth compounds have an underestimated development potential as lubricating additives. The synthesis of new rare earth organic complex additives with good oil solubility, high temperature resistance, low pollution and multifunctionality is the research and development trend of rare earth lubricating materials in the future.
Rare earth compounds have excellent anti-wear and friction reduction properties. Many scholars believe that there are two main factors: on the one hand, a rare earth friction diffusion layer is formed on the friction surface, which increases the hardness of the friction surface and enhances the wear resistance; on the other hand, a multiphase surface lubricating protective film containing rare earth elements is generated on the friction surface, which improves the friction reduction performance. It is also proposed that the lubrication performance of rare earth compounds is related to the size of the lattice constant C of the hexagonal rare earth metal. The longer the C axis, the better the lubricity.
7. Nitrogen-containing heterocyclic compounds and their derivatives as lubricating oil additives
Among nitrogen-containing heterocyclic compounds, such as benzotriazole derivatives, alkyl-substituted imidazolines, 2,5-diyl-1,3,4-thiadiazole and its derivatives are well-known lubricating oil rust inhibitors, antioxidants, dispersants and preservatives. According to the structure of the heterocyclic nucleus, nitrogen-containing heterocyclic derivative multifunctional lubricating oil additives can be roughly summarized into several categories: thiadiazole derivatives, thiazole derivatives, benzotriazole derivatives, oxazoline and thiazoline, imidazoline derivatives, pyridine and diazine and s-triazine derivatives, etc. Each additive has the performance of one or several additives. In addition, the introduction of extreme pressure and anti-wear active elements and functional groups with dispersing properties into nitrogen-containing heterocyclic compounds can prepare derivatives of multifunctional nitrogen-containing heterocyclic compounds. Some derivatives also have good extreme pressure and anti-wear properties. It is learned from the literature that derivatives containing hydroxyalkyl substituted imidazoline, oxazoline and thiazoline can reduce the friction coefficient of lubricating oil by 9% to 50%, and have good high temperature anti-wear and corrosion resistance. Borated imidazoline and oxazoline derivatives have better friction reduction and anti-wear effects on four-ball machines than borate esters. According to literature reports, some nitrogen-containing heterocyclic derivatives containing elemental sulfur in different bonding forms in the heterocyclic parent nucleus have excellent friction and wear properties on four-ball machines, and their friction and wear properties are better when the substituent aromatic ring contains chlorine or methoxy. This is an excellent extreme pressure multifunctional lubricant additive; analysis shows that these heterocyclic derivatives containing nitrogen and sulfur atoms decompose and react chemically with the metal surface during the friction process to form a carbon and sulfur-rich surface film. When chlorine substituents exist, although the atomic concentration of chlorine in the friction surface film is relatively low, its role cannot be ignored. In addition, N-alkylthiomethylbenzene triazole has good memory anti-wear and thermal oxidation stability and anti-corrosion ability, which exceeds the various properties of ZDDP. Its mechanism of action is a layer of sulfur-rich friction reaction film on the surface. Nitrogen-containing heterocyclic compounds and their derivatives used as lubricant additives have good extreme pressure anti-wear and friction reduction properties and high thermal stability, as well as good antioxidant and corrosion resistance. They can meet the special requirements of mechanical equipment and the environment, and therefore have broad application prospects.
Although there have been some research reports and some insights on the friction and wear mechanism of nitrogen-containing heterocyclic compounds and their derivatives in recent years, they are still not very in-depth and systematic, or the role of nitrogen-containing heterocyclic compounds is not very clear, so more in-depth and extensive experimental research in this area should be strengthened.
Summary
1. Sulfur, phosphorus, chlorine and other additives are still the main additives of extreme pressure anti-wear agents in the near future. The research on compounding technology with other additives will be one of the important research topics for tribologists in various countries.
2. Environmental issues have become global issues. With the enhancement of people's survival values and the development of science and technology, people have higher and higher requirements for environmental quality. The development of environmentally friendly lubricants is a sustainable development system project and a supplementary research direction for the oil energy crisis. From the development trend, new environmentally friendly additives will inevitably replace environmentally harmful additives.