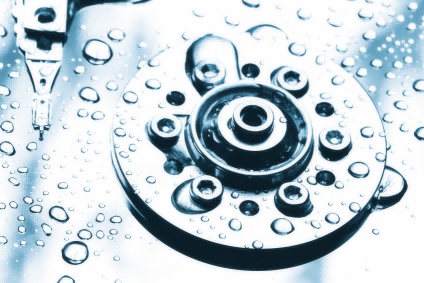
Factors affecting metal corrosion and metal rust inhibitors
What is metal corrosion?
Metal corrosion refers to the process in which metal undergoes chemical or electrochemical reactions under the action of surrounding media (such as air, water, acid, alkali, salt solution, etc.), resulting in the gradual destruction, loss or change of its surface properties. Corrosion is known as rust, which destroys the gloss and beauty of the material and shortens its service life. Corrosion is one of the main ways in which metals fail and is widely present in our lives. For example, rust on the body panels of cars and rust on commonly used steel products and tools outdoors are very common phenomena. Not only steel, but corrosion is also common in other materials such as ceramics, plastics and rubber. Almost all environments are corrosive to a certain extent, which is one of the main reasons for material failure and will cause significant economic losses.
Factors affecting metal corrosion
Metal corrosion is mainly affected by its own characteristics and the environment in which it is located.
Properties of metals
Position in EMF: The position of a metal in the electrochemical sequence (Electromotive Force Series, referred to as the EMF series) determines its tendency to corrode relative to other metals. The closer the position is, the easier it is to become an anode and suffer corrosion. Anode to cathode area ratio: The relative area ratio of the anode and cathode parts of the metal will affect the corrosion rate. A large area ratio usually means a high corrosion rate. Metal purity: The purity of the metal affects its electrochemical properties. Impurities may cause local corrosion or accelerate overall corrosion. Physical properties: The physical properties of the metal, such as the crystal structure and mechanical properties, also indirectly affect the corrosion behavior. Surface film characteristics: The protective film formed on the metal surface can prevent corrosion, but the nature, integrity and stability of the film determine its anti-corrosion effect. Product solubility: The solubility of metal corrosion products affects the corrosion process. When the solubility is low, the corrosion products may be deposited on the metal surface, affecting subsequent corrosion. Volatile corrosion products: Volatile products are produced during the corrosion process of some metals. These products may further affect the corrosion environment or accelerate the corrosion process.
Environmental factors
Temperature: Temperature is a key factor affecting the corrosion rate. Usually, an increase in temperature will accelerate the corrosion reaction. Air humidity: When the humidity is high, a water film is easily formed on the metal surface, providing an electrolyte environment for corrosion. Impurities in water: Dissolved substances in water, such as salts, acids, alkalis, etc., may affect the corrosion behavior of metals. Atmospheric suspended particles: Suspended particles in the air may settle on the metal surface, forming local cells and accelerating corrosion. pH value: The pH of the environment has a significant effect on the corrosion of metals, and different metals have different sensitivities to pH values. Dissolved gases and salts: Gases (such as oxygen, carbon dioxide, etc.) and salts dissolved in the environment will change the electrochemical properties of the corrosive environment. Conductivity: The conductivity of the corrosive medium determines the ability of the current to flow between the metal and the environment, thereby affecting the corrosion rate. Oxygen concentration difference cell: The concentration difference of oxygen in the environment can form an oxygen concentration difference cell, leading to local corrosion. Process steam flow rate: In some process processes, the steam flow rate may affect the corrosion behavior of the metal surface. Electrode polarization: The polarization phenomenon of the electrode during the corrosion process will change the electrochemical properties of the metal and affect the corrosion rate and mechanism.
What are rust inhibitors and corrosion inhibitors?
Rust inhibitors and corrosion inhibitors are special chemicals that, when added to a specific environment at low concentrations, can significantly reduce the corrosion of metals, effectively reduce potential risks, and prevent metals from being damaged by pitting corrosion. In addition, it can also reduce the acid smoke produced when the acid reacts with the alkaline metal during the pickling process, thereby reducing the acid consumption. This protection mechanism is mainly through the inhibitor forming an adsorption layer on the metal surface as a barrier, or by delaying the cathode, anode reaction or both, thereby effectively slowing down the corrosion process. After introducing this type of corrosion inhibitor into the system, the reduction in the corrosion process or metal oxidation rate is mainly attributed to the presence of the corrosion inhibitor. Corrosion inhibitors are not only easy to apply, but also have the advantage of in-situ application, that is, they work directly on the metal surface without causing significant interference to the overall process. Therefore, the use of corrosion inhibitors has become an efficient and practical method to combat metal corrosion and is widely regarded as one of the best means to protect metal materials.
Rust and corrosion inhibitors are chemical substances or compounds that can prevent or slow down metal corrosion when present in the environment (medium) in an appropriate concentration and form. It forms a protective film on the metal surface, blocking the contact between the corrosive medium and the metal surface, thereby inhibiting the occurrence of corrosion reactions. The mechanism of action of corrosion inhibitors mainly includes adsorption film formation, chemical passivation and electrochemical inhibition. They are widely used in the oil, gas, chemical, metallurgy, water treatment and other industries to protect metal equipment and pipelines.
Based on the protection mode of metals, corrosion inhibitors are divided into the following categories:
1 Chemical corrosion inhibitors
Chemical corrosion inhibitors are a class of substances with significant equilibrium potential (redox or electrode potential) and low overpotential. They form a passivation film on the metal surface, thereby significantly reducing the corrosion rate. Common chemical passivators include nitrites (used in antifreeze cooling water systems), chromates (commonly used in circulating cooling water), and zinc molybdate (as an inhibitory pigment in paint).
2 Adsorption corrosion inhibitors
Adsorption corrosion inhibitors are one of the most widely used categories of corrosion inhibitors. They are mainly composed of organic compounds that can be adsorbed on the metal surface and play a protective role on the entire surface (including cathode and anode areas) through a covering effect. This type of corrosion inhibitor usually has similar effects on cathode and anode reactions, but in specific cases, their effects may be different. They are often used in the pickling process of hot-rolled products to remove oxide scales, so they are also called pickling inhibitors. Typical adsorption inhibitors include compounds containing lone pairs of electrons, such as amines, nitrogen atoms in quinolines, sulfur atoms in thio compounds, and oxygen atoms in aldehydes.
3 Film-forming inhibitors
Unlike adsorption inhibitors, film-forming inhibitors prevent corrosion by forming a blocking or barrier film in addition to the inhibiting substance itself. Such materials usually have a specific effect on the cathode or anode. Zinc and calcium salts are typical representatives of cathodic film-forming inhibitors, while benzoates are a common choice for anodic film-forming inhibitors, especially in marine applications.
4 Vapor-phase inhibitors
Vapor-phase inhibitors, also known as volatile inhibitors, are used to prevent atmospheric corrosion of metals in enclosed spaces (such as packages). They have a low vapor pressure, and the vapor is able to contact and adsorb on the metal surface, and then release protective ions with corrosion-inhibiting properties through hydrolysis. Dicyclohexylamine chromate and benzotriazole are commonly used vapor-phase inhibitors for protecting copper, while phenylthiourea and cyclohexylamine chromate are used to protect brass. Dicyclohexylamine nitrite is suitable for the protection of ferrous and non-ferrous metal parts.
5 Volatile Corrosion Inhibitors
Volatile corrosion inhibitors (VCIs) protect metals by volatilizing from the source to the site of corrosion in a closed environment. However, if the corrosion products themselves are volatile, they will volatilize once formed, exposing the underlying metal surface and subjecting it to further attack, thereby initiating rapid and sustained corrosion. For example, molybdenum oxide (MoO3) is a volatile corrosion product. In closed steam processes (such as shipping containers), volatile solids of salts such as dicyclohexylamine, cyclohexylamine, and hexamethyleneamine are often used as volatile corrosion inhibitors.
6 Synergistic Corrosion Inhibitors
Synergistic corrosion inhibitors are commonly used in cooling water systems to achieve better corrosion protection by combining different types of corrosion inhibitors (such as anodic and cathodic corrosion inhibitors). Common synergistic inhibitors include chromate phosphates, polyphosphate silicates, zinc tannins, and zinc phosphates.
7 Precipitation Corrosion Inhibitors
Precipitation corrosion inhibitors provide a protective film by forming a precipitate on the metal surface. Silicates and phosphates are common representatives of this type of corrosion inhibitor. For example, sodium silicate is widely used in household water softeners to prevent metals from rusting.
8 Green Corrosion Inhibitors
The definition of "environmentally friendly" or "green" corrosion inhibitors has not yet been clearly and universally recognized. However, with the increasing concern for human health and environmental safety, corrosion inhibition research has gradually shifted to the use of environmentally friendly compounds, such as plant extracts and expired non-toxic drugs. The organic components of these compounds, such as amino acids, alkaloids, pigments and tannins, have been studied as green alternatives to traditional toxic and hazardous compounds. Due to their advantages such as biodegradability, environmental friendliness, low cost and easy availability, extracts and products from many common plants and medicinal plants have been widely studied as corrosion inhibitors for various metals and alloys under different environmental conditions.
Rust Inhibitors Supplier
UNPChemicals is a professional and trusted Rust Inhibitors supplier manufacturing high quality and range of Rust Inhibitors according to your workflows and products. If you are looking for high performance Rust Inhibitors solution, feel free to contact us.
UNPChemical's Rust Inhibitor Products:
CMET® T746:Dodecylene succinic acid is an oil soluble ashless rust inhibitor with dodecyl succinic acid structure. The product has good oil solubility and can form a solid oil film on the metal surface, comprehensively protecting the metal from rust and corrosion.
CMET® AO:Oleic acid imidazoline corrosion inhibitor is a multifunctional additive derived from imidazoline, known for its versatility in various applications, including serving as a corrosion inhibitor, dewatering agent, and emulsifier for lubricants.
CMET® SO:N-acyl sarcosine type corrosion inhibitor, an N-acyl sarcosine, is a corrosion inhibitor of lubricating oil, grease and fuel oil. With exceptional performance when used in combination with CMET® AO, CMET® SO is suitable for food-grade lubricating oil formulas and boasts good oil solubility.