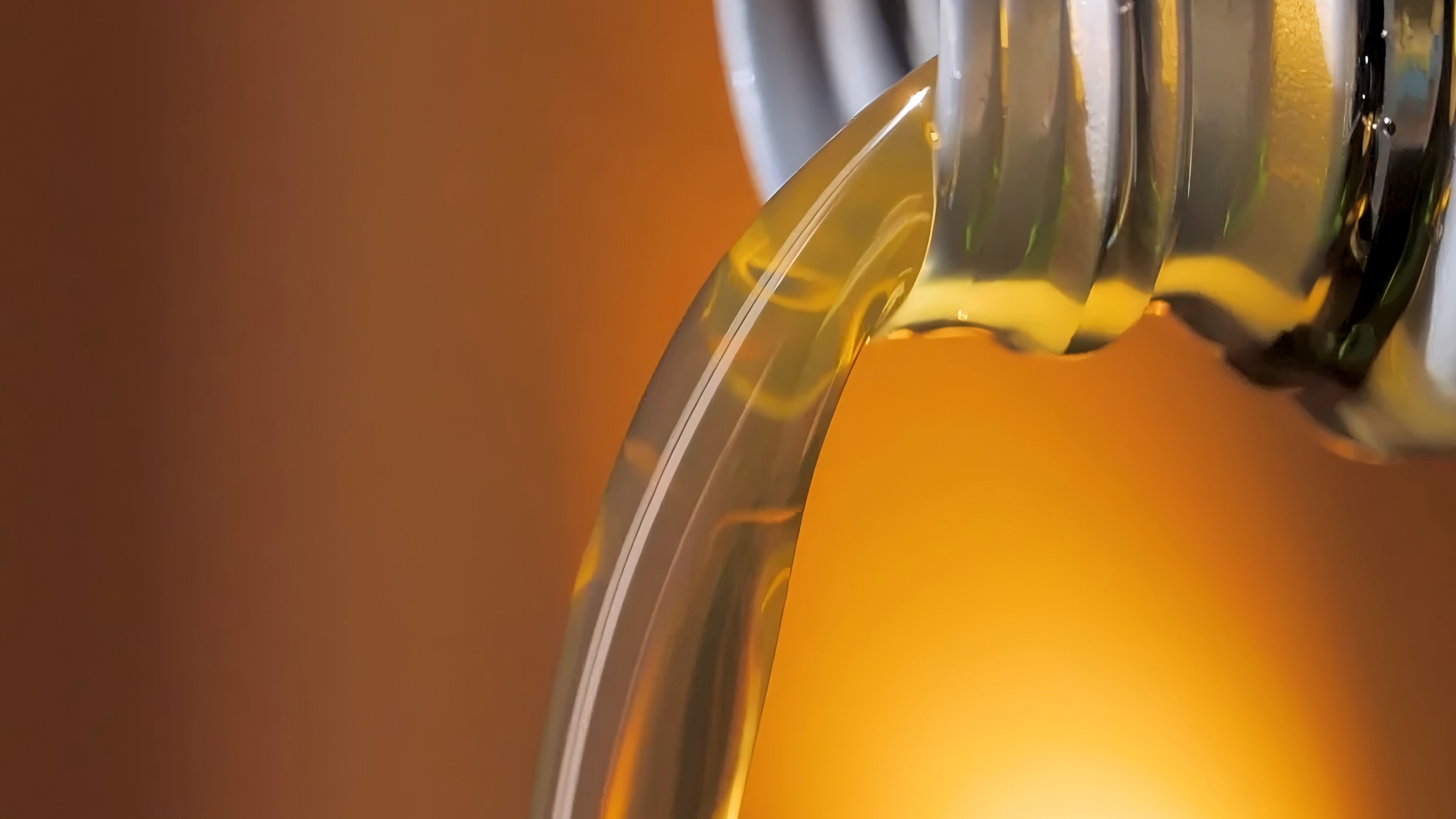
What Additives are Needed for a High-Quality Hydraulic Oil?
It all starts with friction. Friction has brought us countless conveniences. Thanks to friction, we can hold a water cup, walk freely, and control the starting and stopping of vehicles.
With the continuous development of modern industry, the "inconveniences" caused by friction are becoming more and more prominent. Friction between mechanical components leads to component wear, accelerated consumption, and shortened equipment lifespan.Thus, the traditional lubrication principle emerged - using the viscosity of the oil itself to form an oil film on the friction surface, preventing direct contact between metal components.
For a certain period, traditional lubrication has, to some extent, solved the wear problem and met the lubrication needs of equipment. However, traditional lubrication products can no longer meet the development requirements of modern industry.
With the development of industrial technology, modern equipment is becoming increasingly high - speed, high - performance, highly automated, efficient, and long - lasting. Whether it is mineral oil or synthetic oil, under high - temperature and high - pressure conditions, the generated oil film is extremely likely to be damaged. Once the oil film is damaged, the lubricating oil can no longer maintain good lubrication performance, resulting in increased wear between friction components and easy damage to the equipment.
To ensure that the oil film is not damaged, the lubricating oil tends to maintain a relatively high viscosity. This, in turn, increases the resistance between friction components, leading to increased fuel consumption, higher power consumption, shorter oil change intervals, vibration, and noise, affecting the operation of the equipment and increasing maintenance costs.
To meet the development needs of modern industry, lubricating oil additives came into being. Lubricating oil additives mainly have three functions:
First, to further enhance the performance of the base oil itself, such as antioxidants, rust inhibitors, antifoaming agents, and demulsifiers.
Second, to make up for the deficiencies in the performance of the base oil, such as pour point depressants and viscosity index improvers.
Third, to endow the base oil with new properties, such as extreme pressure agents (EP), dispersants, and metal deactivators.
With the "finishing touch" of additives, traditional lubrication products acquire different capabilities, take on a new look, and fully meet the lubrication needs of industrial equipment. This is the magic of lubricating oil additives.
The additives in hydraulic oil can be roughly divided into two categories: one is additives that improve the physical properties of the oil, such as oiliness agents, viscosity - increasing agents, antifoaming agents, and pour point depressants. The other is additives that improve the chemical properties of the oil, such as antioxidants, rust inhibitors, anti - mold agents, demulsifiers, and metal deactivators.
Oiliness Agents: Oiliness agents are substances with strong polarity. Under low - temperature and low - pressure conditions, they can adsorb on the metal surface, forming a firm adsorption film to prevent direct contact between metals, improve the strength of the oil film, and reduce metal friction and wear. Commonly used oiliness agents in hydraulic oil include oleic acid, sulfonated whale oil, sulfonated cottonseed oil, sulfonated olefin cottonseed oil, dimer acid, etc.
Anti - wear Agents: Under high - friction temperatures, the decomposition products of anti - wear agents react with the metal surface, generating a compound film with low shear stress and low melting point, preventing the contact surface from seizing or welding. The plastic deformation formed fills the uneven parts of the friction surface, increasing the contact area, reducing pressure, and minimizing wear. Anti - wear agents usually contain sulfur, phosphorus, and oxygen, and their compounds have their own characteristics. Sulfur - containing anti - wear agents react with iron under high - temperature friction conditions to form an iron sulfide film, playing an anti - wear role. Phosphorus - containing anti - wear agents, under not - too - high temperatures and relatively mild friction conditions, react with steel through the thermal decomposition products of phosphate esters to form a low - melting - point and high - plasticity phosphate mixture, thus achieving anti - wear effects. Chlorine - containing anti - wear agents generate an iron chloride film under extrusion conditions. This film has a layered structure, a low friction coefficient, is easy to shear, and has good lubrication properties. Commonly used anti - wear agents in hydraulic oil include zinc dialkyldithiophosphate, xylenyl phosphate,thiophosphate, sulfonated olefins, fluorinated paraffin.
Viscosity - increasing Agents: Viscosity - increasing agents are additives that improve the viscosity - temperature characteristics of hydraulic oil and increase the viscosity index. They are a type of high - molecular polymer. At low temperatures, they shrink and curl into tight spherical shapes in the oil, having little impact on the low - temperature viscosity. At high temperatures, they swell and stretch in the oil, increasing the viscosity and thus improving the viscosity - temperature characteristics. Commonly used viscosity - increasing agents in hydraulic oil include poly(n - butyl vinyl ether) , polyisobutylene , ethylene - propylene copolymer, polymethyl methacrylate,etc.
Antifoaming Agents: Antifoaming agents are substances that can reduce the stability of the foam adsorption film and shorten the existence time of foam. Adding antifoaming additives to hydraulic oil can reduce the surface tension, allowing bubbles to escape from the oil surface quickly and thus eliminating bubbles. Commonly used antifoaming agents in hydraulic oil include dimethyl silicone oil, polyester non - silicone antifoaming agent, metal soaps, fatty acids, etc.
Pour Point Depressants: Pour point depressants are additives that can inhibit the formation of a network of wax crystals in the oil, lower the pour point, and maintain the fluidity of the oil product. These agents change the crystal form and size of wax by adsorbing on the wax crystal surface or forming a eutectic, thereby reducing the pour point of the oil product. Commonly used pour point depressants in hydraulic oil include alkylnaphthalene, polymethyl methacrylate, α - olefin copolymer, ethylene - vinyl acetate copolymer, etc.
Antioxidants: Antioxidants are additives that are easily oxidized themselves and can form a complex film on the metal surface, isolating contact with oxygen and other corrosive substances, preventing the catalytic effect of the metal on the oxidation of the oil and the corrosive effect of the oil on the metal. Generally, using several antioxidant additives in combination can achieve better antioxidant effects. For example, the combination of sulfides and aromatic hydrocarbons can produce a synergistic effect, and the combination of free - radical terminators and oxide decomposers also has a significant synergistic effect. Commonly used antioxidants in hydraulic oil include 2,6 - di - tert - butyl - p - cresol, N,N’ - di - sec - butyl - p - phenylenediamine, N-phenyl-α- naphthylamine, sulfur - enesulfur esters, N-dialkyldithiocarbamate, aromatic bisphenols,etc.
Rust Inhibitors: Rust inhibitors are polar compounds that can form a firm and growing adsorption film on the metal surface to prevent metal rusting. Commonly used rust inhibitors in hydraulic oil include dodecenyl succinic acid, dinonylnaphthalene sulfonic acid barium, dodecenyl succinate of heptadecenyl imidazoline, etc.
Anti - mold Agents: Anti - mold agents can prevent and inhibit the growth of mold in emulsified oil. Commonly used anti - mold agents in hydraulic oil include phenolic compounds, formaldehyde compounds, salicylanilide, etc.
Demulsifiers: Demulsifiers are substances that can separate water and oil well or cause them to settle out. Commonly used demulsifiers in hydraulic oil include sulfonates and various polymers of ethylene oxide and propylene oxide.
Metal Deactivators: Metal deactivators are additives that can protect non - ferrous metals, especially the copper surface from corrosion. This agent can also increase the oxidation resistance of the oil product and inhibit and deactivate the corrosion of copper by acidic substances. There are two types of metal deactivators used in hydraulic oil: one is the film - forming type deactivator, which can form a film on the copper surface to prevent the erosion of acids, active sulfides, and corrosive extreme - pressure agents. Commonly used ones include benzotriazole, such as benzotriazole octadecylamine. The other is the active sulfur scavenger, which reacts with active sulfides to form low - corrosive or non - corrosive polysulfide compounds. Commonly used ones include alkyl polysulfide, 2,5 - dithiothiazole.
Synergistic Effects among Additives
How the Combination of Antioxidants and Corrosion Inhibitors Improves the Overall Performance of Hydraulic Oil?
In hydraulic oil, the combination of antioxidants and corrosion inhibitors can comprehensively improve the overall performance of hydraulic oil. The main function of antioxidants is to inhibit the oxidation process of hydraulic oil. When the hydraulic system is in operation, the hydraulic oil can be oxidized due to contact with air, high - temperature environments, etc., generating acidic substances and sludge. Acidic substances can reduce the quality of the oil product, and sludge can block system components. Antioxidants can capture the free radicals generated by the oxidation reaction, interrupt the oxidation chain reaction, slow down the oxidation rate, extend the service life of the hydraulic oil, and ensure the stable operation of the system.
Corrosion inhibitors form a protective film on the metal surface, isolating the contact between moisture, oxygen, and other corrosive substances and the metal, preventing the corrosion of metal components and ensuring the integrity and normal function of the metal components in the system. When the two are used in combination, antioxidants slow down the oxidation of the oil product, reducing the acidic substances generated by oxidation and reducing the risk of damage to the protective film of the corrosion inhibitor. The protective film of the corrosion inhibitor can reduce the catalytic effect of the metal on the oxidation of the oil product. This synergistic effect not only protects the quality of the hydraulic oil itself but also maintains the metal components of the system, significantly improving the overall performance of the hydraulic oil.
The Efficacy of the Combination of Antifoaming Agents and Defoamers in the Hydraulic System
In the hydraulic system, the combination of antifoaming agents and defoamers is of great significance for ensuring the normal operation of the system. The principle of action of antifoaming agents is to reduce the surface tension of the liquid and inhibit the generation of bubbles. During the processes of pumping, flowing, and spraying of the hydraulic oil, air can be mixed in to form bubbles. If these bubbles cannot be eliminated in time, the hydraulic system may experience problems such as pressure fluctuations, unstable flow rate, and increased noise. In severe cases, it may even damage system components. Antifoaming agents can effectively prevent the generation of bubbles, maintaining the continuity and stability of the hydraulic oil.
Defoamers come into play after the formation of bubbles, accelerating the bursting of bubbles. They can quickly penetrate into the liquid film of the bubbles, destroy the stability of the bubbles, and cause the bubbles to burst and disappear rapidly. Antifoaming agents and defoamers work together.
Antifoaming agents inhibit the generation of bubbles from the source, reducing the number of bubbles generated in the system. Defoamers rapidly eliminate the already - formed bubbles. This combination ensures that the oil in the hydraulic system always maintains good fluidity and pressure - transmitting performance, effectively avoiding system failures caused by bubble problems and improving the working efficiency and reliability of the hydraulic system.
The Impact of the Composite Use of Multiple Additives on the Stability of Hydraulic Oil
The composite use of multiple additives can greatly enhance the stability of hydraulic oil. Detergent - dispersants can disperse the oxidation products, impurities, etc. in the oil into small particles, preventing their aggregation and sedimentation, keeping the oil clean, and reducing the impact of impurities on stability. Anti - wear agents form a protective film on the metal surface, reducing the generation of wear debris and avoiding oil pollution and performance changes caused by wear.
Different additives cooperate with each other. Antioxidants slow down oxidation, reducing the degradation of oil performance caused by oxidation. Corrosion inhibitors protect the metal surface, reducing the catalytic effect of the metal on oil oxidation. The composite use of multiple additives forms a comprehensive protection system, enabling the hydraulic oil to maintain good stability under different working conditions and providing reliable guarantee for the stable operation of the hydraulic system.
The Price of Additives for Rust Inhibitors
The price of Additives for Rust Inhibitors depending on factors such as brand, specification, composition, and sales channels. If you are interested in Additives for Rust Inhibitors, please feel free to contact us.
Supplier of Lubricant Additives
UNPChemicals is a professional supplier of high-quality and effective Additives for Rust Inhibitors. We offer several remarkable products, namely Oleic acid imidazoline corrosion inhibitor CMET AO,N-acyl sarcosine type corrosion inhibitor CMET SO,Dodecylene succinic acid CMET T746,etc.
Oleic acid imidazoline corrosion inhibitor CMET AO is a multifunctional additive derived from imidazoline, known for its versatility in various applications, including serving as a corrosion inhibitor, dewatering agent, and emulsifier for lubricants.
N-acyl sarcosine type corrosion inhibitor CMET SO, an N-acyl sarcosine, is a corrosion inhibitor of lubricating oil, grease and fuel oil. With exceptional performance when used in combination with CMET AO, CMET SO is suitable for food-grade lubricating oil formulas and boasts good oil solubility.
Dodecylene succinic acid CMET T746 is an oil soluble ashless rust inhibitor with dodecyl succinic acid structure. The product has good oil solubility and can form a solid oil film on the metal surface, comprehensively protecting the metal from rust and corrosion.
Conclusion
This article focuses on hydraulic oil additives. It begins with the problem of equipment wear caused by friction, stating that traditional lubrication products are difficult to meet the needs of modern industry, and then introduces lubricating oil additives. These additives have the functions of enhancing the performance of the base oil, making up for its deficiencies, and endowing it with new properties.Then elaborates on two types of additives in hydraulic oil, namely those that improve physical properties and those that improve chemical properties, listing ten common additives such as oiliness agents and anti - wear agents, as well as their functions and common types. Finally, it emphasizes the synergistic effects among additives, such as the combined improvement of overall performance by antioxidants and corrosion inhibitors, the guarantee of system operation by the combination of antifoaming agents and defoamers, and the enhancement of hydraulic oil stability by the composite use of multiple additives, comprehensively demonstrating the importance of hydraulic oil additives for the stable operation of the hydraulic system.
UNPChemicals supplies various lubricating oil additives such as friction modifiers, metal deactivators, extreme pressure anti-wear agents and metal processing additives. If you're interested, please contact us.