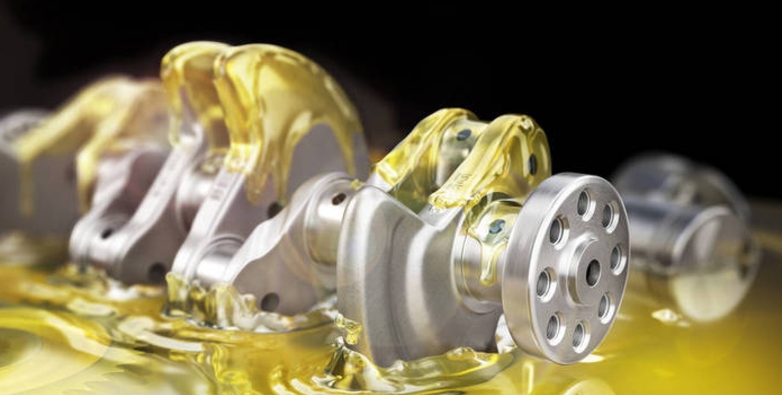
What Additives Are Found in Hydraulic Oil?
Hydraulic oil plays a crucial role in industrial and machinery applications, providing a wide range of essential functions such as power transmission, cooling, sealing, protection against wear, friction reduction, rust and corrosion prevention, and ensuring the system remains free from sludge, deposits, and varnish. These capabilities are largely enabled by the carefully formulated additives present in hydraulic oils. In this article, we’ll explore the types and functions of hydraulic oil additives, focusing on zinc-based demulsifying hydraulic fluids.
What Are Hydraulic Oil Additives?
Hydraulic oil additives are chemical compounds mixed with base oils to enhance their natural properties and impart specific performance characteristics. Without additives, base oils lack the necessary qualities to perform efficiently in demanding environments. Additives address these shortcomings, enabling hydraulic fluids to withstand extreme pressures, resist degradation, and protect machinery from wear and tear.
In hydraulic systems, additives are essential for ensuring operational reliability and extending the life of both the fluid and the equipment. They provide benefits such as:
Reducing Wear and Tear: Additives create a protective film on metal surfaces, preventing direct contact and minimizing wear.
Improving Thermal Stability: By resisting oxidation and heat-induced degradation, additives maintain oil performance under high temperatures.
Controlling Contamination: Detergent and dispersant additives help keep the system clean by preventing sludge and varnish buildup.
Preventing Corrosion and Rust: Inhibitors form a protective barrier against water and oxygen, reducing the risk of rust.
Enhancing Compatibility: Additives ensure the oil works seamlessly with seals, gaskets, and other system components.
Types of Hydraulic Oil Additives
Hydraulic systems are used across a wide range of industries, from construction and manufacturing to aviation and agriculture. As a result, hydraulic oil formulations vary depending on the specific application. Some of the most common types of hydraulic oils include:
Zinc-Based Hydraulic Fluids: Known for their excellent anti-wear properties, zinc-based fluids are widely used in industrial applications.
Zinc-Free Hydraulic Fluids: These are designed for environments where zinc could pose environmental or compatibility concerns.
Biodegradable Hydraulic Fluids: Used in environmentally sensitive areas, these fluids break down naturally and minimize ecological impact.
Fire-Resistant Hydraulic Fluids: Essential for high-temperature or hazardous applications, these fluids reduce the risk of fire.
Water-Emulsion Fluids: These are a mixture of water and oil, offering good fire resistance while maintaining lubrication properties.
Demulsifying Fluids: These separate water from oil, ensuring consistent performance in the presence of water contamination.
For this discussion, we will focus on zinc-based demulsifying hydraulic fluids, which are among the most commonly used in industrial applications due to their superior anti-wear and water-separation properties.
Common Types of Hydraulic Oil Additives
Hydraulic oil formulations typically include a combination of the following additive types:
1. Anti-Wear Additives
Anti-wear additives are among the most critical components in hydraulic oils. These additives form a protective film on metal surfaces, reducing wear and extending the life of pumps, valves, and other components.
Key Compound: Zinc dialkyldithiophosphate (ZDDP), a zinc-based additive, is widely used due to its effectiveness in high-pressure applications.
Function: Protects against scuffing, galling, and metal-to-metal contact, especially under extreme pressures.
2. Oxidation Inhibitors
Oxidation can lead to the formation of sludge, varnish, and acidic by-products, which can degrade hydraulic oil and damage system components. Oxidation inhibitors slow this process.
Key Compound: Phenolic and aminic antioxidants are commonly used to enhance thermal stability.
Function: Extends oil life and maintains system cleanliness by preventing oil thickening and deposit formation.
3. Rust and Corrosion Inhibitors
Hydraulic systems often encounter water contamination, which can lead to rust and corrosion of metal surfaces. These inhibitors form a barrier to protect against water and oxygen exposure.
Key Compound: Alkylsuccinic acids and amine-based inhibitors are frequently employed.
Function: Prevents rusting of ferrous metals and protects copper alloys from corrosion.
4. Demulsifiers
Water contamination is a common issue in hydraulic systems. Demulsifying additives promote the separation of water from oil, allowing water to be drained from the system easily.
Key Compound: Polymer-based demulsifiers.
Function: Maintains consistent oil performance and protects against rust and corrosion caused by water.
5. Friction Modifiers
Friction modifiers reduce internal friction within the system, improving efficiency and reducing energy consumption.
Key Compound: Organic friction modifiers (OFMs) and molybdenum compounds.
Function: Enhances lubrication to improve the overall performance of hydraulic systems.
6. Anti-Foam Additives
Foaming can reduce the effectiveness of hydraulic oils by impairing lubrication and causing erratic system performance. Anti-foam additives prevent the formation of foam and ensure smooth operation.
Key Compound: Polysiloxanes and organic surfactants.
Function: Minimizes foam formation and enhances oil stability.
7. Viscosity Index Improvers
Temperature fluctuations can significantly impact the viscosity of hydraulic oil. Viscosity index improvers ensure the oil maintains its viscosity across a wide temperature range.
Key Compound: Polymethacrylates (PMAs) and styrene-diene copolymers.
Function: Ensures consistent hydraulic performance in both hot and cold conditions.
8. Detergents and Dispersants
These additives work together to keep the hydraulic system clean by preventing sludge and varnish buildup.
Key Compound: Calcium sulfonates and succinimide dispersants.
Function: Breaks down deposits and keeps contaminants suspended in the oil.
Why Zinc-Based Demulsifying Fluids?
Zinc-based demulsifying hydraulic fluids offer a combination of superior anti-wear performance and effective water separation. These properties make them ideal for applications where water contamination is likely, such as in outdoor or marine environments.
Advantages:
Excellent anti-wear protection for prolonged equipment life.
Effective water separation for maintaining oil purity.
Good compatibility with a wide range of seals and materials.
Applications:
Industrial machinery.
Marine and offshore equipment.
Mobile hydraulic systems.
UNPChemicals: A Leader in Hydraulic Oil Additive Production
UNPChemicals is a globally recognized producer of high-quality hydraulic oil additives. With decades of experience and a commitment to innovation, the company provides tailored solutions to meet the needs of various industries.
Product Portfolio
UNPChemicals offers a comprehensive range of additive packages, including:
Zinc-based anti-wear additives.
Multi-functional additive packages for biodegradable fluids.
Fire-resistant fluid formulations.
Custom solutions for specific industrial applications.
Commitment to Sustainability
As environmental regulations tighten, UNPChemicals is at the forefront of developing eco-friendly hydraulic oil additives. Their biodegradable and zinc-free additive technologies align with global sustainability goals, ensuring optimal performance with minimal environmental impact.
Research and Development
The company invests heavily in R&D to develop advanced additive technologies. Their state-of-the-art testing facilities ensure that every product meets or exceeds industry standards.
Conclusion
Hydraulic oil additives are vital for ensuring the efficiency, reliability, and longevity of hydraulic systems. From anti-wear agents to demulsifiers, each additive plays a crucial role in addressing the challenges of modern hydraulic applications. Zinc-based demulsifying fluids remain a popular choice for their robust performance, particularly in demanding industrial environments.
With companies like UNPChemicals leading the way in additive innovation, the future of hydraulic oils promises even greater advancements in efficiency, sustainability, and versatility. For industries seeking high-performance solutions, understanding and selecting the right hydraulic oil additives is an investment in long-term success.