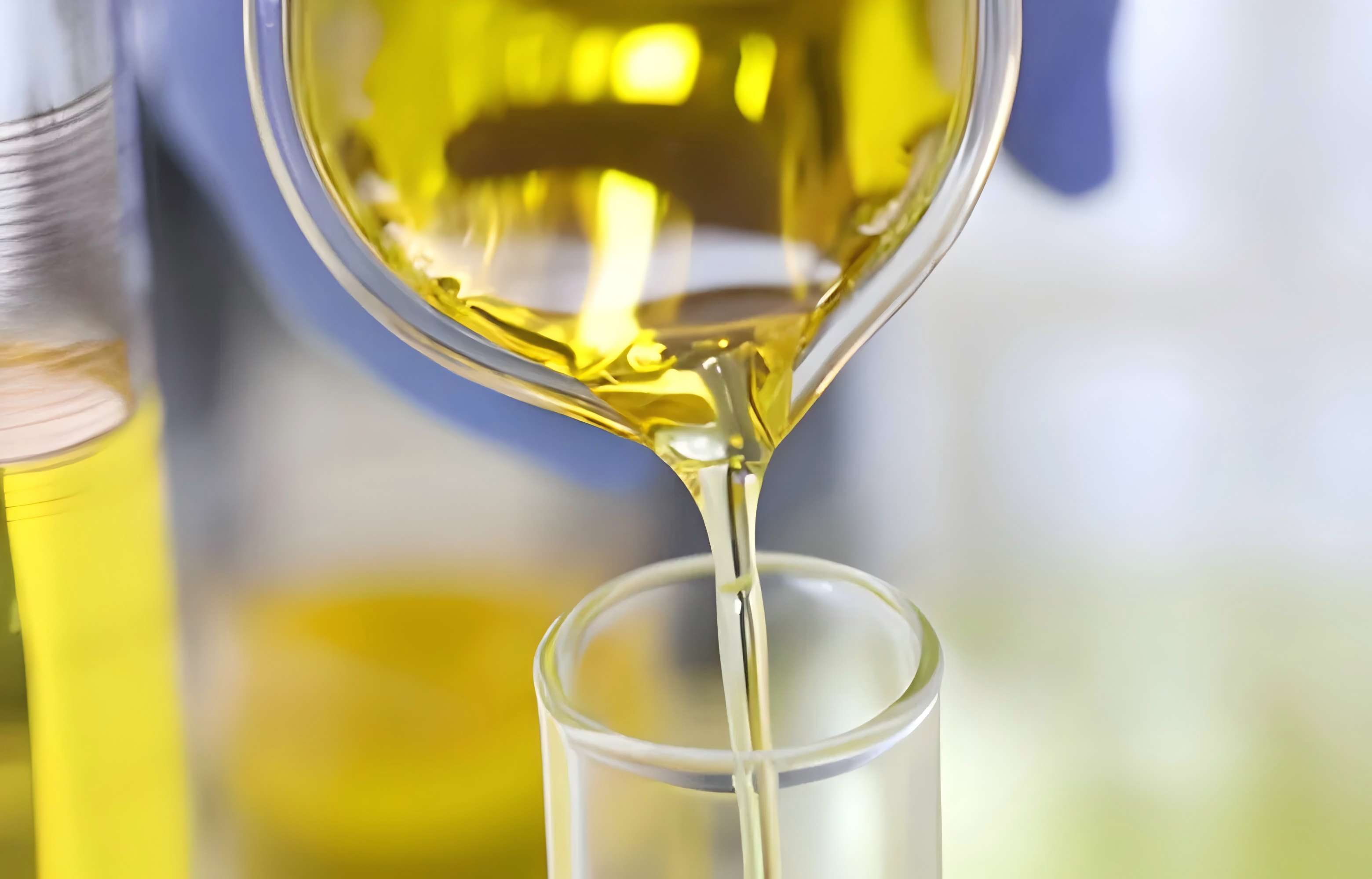
Wear Resistance Protection in Hydraulic Systems: The Role of Additive Compounds
Hydraulic systems, with their significant advantages such as high power density, fast response speed, and high control accuracy, have been widely applied in the industrial field. They cover numerous industries including construction machinery, metallurgy, mining, aerospace, and more. However, during the actual operation process, the components of hydraulic systems will inevitably experience wear. Wear not only reduces the working efficiency of the hydraulic system and increases energy consumption but also, in severe cases, can lead to system failures, affecting the normal progress of production. Therefore, how to effectively improve the wear resistance performance of hydraulic systems has become a crucial issue that urgently needs to be solved in the industry. Among the many solutions, the use of wear resistance protection additive compounds is an economical, efficient, and widely applied method. This article will conduct an in-depth discussion on the role of additive compounds in wear resistance protection within hydraulic systems.
Types of Wear of Hydraulic Components
(1) Abrasive Wear
In hydraulic systems, the entry of solid particles into the mating clearances of hydraulic components will cause abrasive wear. These solid particles have a wide range of sources. They may be impurities such as metal chips and molding sands remaining during the system assembly process, or they may be dust and sediment mixed into the hydraulic oil during the storage, transportation, and use of the oil. Additionally, they could be metal particles generated due to friction, corrosion, and other reasons within the internal components of the system. When these particles circulate with the hydraulic oil in the system, they will act like sandpaper, scratching the surfaces of components such as hydraulic pumps, hydraulic valves, and hydraulic cylinders, causing the surface material to gradually peel off and forming abrasive wear. For example, in the hydraulic systems of mining machinery, due to the harsh working environment, a large amount of dust easily enters the system, making abrasive wear one of the main causes of failure of hydraulic components.
(2) Adhesive Wear
When the two relatively moving surfaces of hydraulic components come into direct contact under pressure, and the local pressure at the contact points exceeds the yield strength of the material, adhesive wear will occur. When the hydraulic system starts, stops, or experiences significant load changes, components such as the plunger and cylinder block of the hydraulic pump, and the valve core and valve seat of the hydraulic valve are prone to experience a brief state of dry friction or boundary lubrication. At this time, the risk of adhesive wear will increase significantly. Adhesive wear will cause damage such as scratches, scuffing, and galling on the surface of the components, seriously affecting the mating accuracy and service life of the components.
(3) Fatigue Wear
During the operation of the hydraulic system, the hydraulic components are subjected to periodic alternating loads. For example, the plunger of the hydraulic pump will be subjected to repeated pressure shocks during the oil suction and oil discharge processes; the piston rod of the hydraulic cylinder will be subjected to periodic tensile and compressive loads during the expansion and contraction processes. Long-term exposure to alternating loads will cause the material on the surface of the components to generate fatigue cracks. As the cracks continue to expand and connect, it will eventually lead to the spalling of the material, forming fatigue wear. Fatigue wear usually occurs on the surface or subsurface of hydraulic components. It is a progressive form of wear that is not easily detectable in the initial stage, but once it develops to a certain extent, it will have a serious impact on the performance of the hydraulic system.
(4) Corrosive Wear
Moisture, acidic substances in the hydraulic oil, and oxygen in the air, etc., will undergo chemical reactions with the metal surface of the hydraulic components, leading to corrosive wear. Moisture will cause the metal surface to rust, reducing the surface finish and hardness, thereby accelerating wear. Acidic substances will react with the metal to form corrosion products. These products will peel off from the metal surface under the scouring action of the hydraulic oil, further intensifying the wear. In addition, some hydraulic systems operate in high-temperature and high-humidity environments, or use unsuitable hydraulic oils, all of which will increase the risk of corrosive wear.
Functions of Hydraulic Oil Additive Compounds: Providing Wear Resistance Protection
(1) The Role of Anti-wear Agents
Anti-wear agents are one of the main components of wear resistance protection additive compounds. Their function is to form a protective film on the metal surface of hydraulic components, reducing the friction coefficient between the components and minimizing wear. Common anti-wear agents include organic phosphates, sulfur-phosphorus type extreme pressure anti-wear agents, etc. Organic phosphates can undergo chemical reactions on the metal surface to form a chemically adsorbed film. This film has good lubrication performance and anti-wear performance, which can effectively isolate the metal surface and reduce direct contact and friction. Sulfur-phosphorus type extreme pressure anti-wear agents will react with the metal surface under high-temperature and high-pressure conditions to generate chemical reaction films such as sulfides and phosphides. These films have high hardness and wear resistance and can withstand large loads, thus protecting the metal surface from wear.
(2) The Role of Extreme Pressure Agents
When the hydraulic system is under high load and high pressure, ordinary anti-wear agents may not be able to provide sufficient protection. At this time, extreme pressure agents play an important role. Extreme pressure agents usually contain active elements such as chlorine, sulfur, and phosphorus. Under extreme pressure conditions, these active elements will undergo chemical reactions with the metal surface to form an extreme pressure lubricating film. This film has high compressive strength and shear resistance and can withstand extremely high pressure instantaneously, preventing the metal surface from sticking and scuffing. For example, in the hydraulic systems of construction machinery, when the equipment is performing heavy-duty operations, extreme pressure agents can ensure that the hydraulic components can still maintain a good lubrication state under extreme working conditions, reducing wear.
(3) The Role of Detergent Dispersants
Detergent dispersants also play an indispensable role in wear resistance protection additive compounds. They can prevent impurities, dirt, and oxidation products in the hydraulic oil from depositing on the surface of hydraulic components, keeping the component surface clean. Detergent dispersants disperse these impurities in the hydraulic oil through adsorption, solubilization, and dispersion, making it difficult for them to form deposits. This not only reduces the occurrence of abrasive wear but also ensures the fluidity and heat transfer performance of the hydraulic oil, improving the overall performance of the hydraulic system. At the same time, detergent dispersants can also inhibit the oxidation and deterioration of the hydraulic oil, extending the service life of the hydraulic oil.
(4) The Role of Antioxidants
During the use of hydraulic oil, it will undergo oxidation reactions with oxygen in the air, generating oxidation products such as acidic substances, gums, and asphaltenes. These oxidation products will reduce the lubrication performance of the hydraulic oil and accelerate the wear of the components. Antioxidants can inhibit the oxidation reaction of the hydraulic oil and delay the generation of oxidation products. Antioxidants are divided into primary antioxidants and secondary antioxidants. Primary antioxidants interrupt the oxidation chain reaction by capturing free radicals, thus preventing the oxidation process. Secondary antioxidants decompose hydroperoxides, converting them into harmless substances and preventing hydroperoxides from further decomposing to generate free radicals and triggering new oxidation reactions. The addition of antioxidants can effectively extend the service life of the hydraulic oil and reduce the wear of components caused by the oxidation of the hydraulic oil.
Compatibility of Hydraulic Oil Additive Compounds with Materials
(1) Compatibility with Metal Materials
Most components in hydraulic systems are made of metal materials, such as cast iron, carbon steel, alloy steel, copper alloy, etc. Various additives in the wear resistance protection additive compounds must have good compatibility with these metal materials and should not cause corrosion or other adverse effects on the metal materials. For example, some sulfur-containing extreme pressure agents may undergo a corrosion reaction when in contact with copper alloy, leading to the damage of copper alloy components. Therefore, when selecting additive compounds, it is necessary to fully consider their compatibility with the metal materials in the system to ensure that the additive compounds will not cause damage to the metal components.
(2) Compatibility with Sealing Materials
Sealing materials play an important role in preventing hydraulic oil leakage in hydraulic systems. Common sealing materials include rubber, plastic, etc. Additives in the wear resistance protection additive compounds may affect the performance of the sealing materials, causing the sealing materials to expand, contract, harden, or soften, thus affecting the sealing performance. For example, certain organic solvents may cause rubber seals to expand and deform, reducing their sealing effect. Therefore, when selecting additive compounds, it is necessary to ensure their good compatibility with the sealing materials in the system to avoid a decrease in sealing performance and the occurrence of hydraulic oil leakage due to the use of additive compounds.
(3) Compatibility with Coating Materials
In order to improve the wear resistance and corrosion resistance of hydraulic components, the surfaces of some hydraulic components are coated with various coatings, such as chrome plating layers, nitriding layers, ceramic coatings, etc. Additives in the wear resistance protection additive compounds need to have good compatibility with these coating materials and should not damage the integrity and performance of the coatings. For example, certain acidic additives may corrode the chrome plating layer, causing the coating to peel off and reducing the wear resistance of the components. Therefore, when using additive compounds, it is necessary to fully consider their compatibility with the coating materials to ensure that the additive compounds will not cause damage to the coatings.
In conclusion, the components in hydraulic systems will encounter various types of wear during the working process, and these types of wear seriously affect the performance and service life of the hydraulic systems. The use of wear resistance protection additive compounds is an effective means to improve the wear resistance performance of hydraulic systems. Components such as anti-wear agents, extreme pressure agents, detergent dispersants, and antioxidants in the additive compounds provide comprehensive wear resistance protection for hydraulic components by forming protective films on the metal surface, inhibiting oxidation reactions, and dispersing impurities. At the same time, when selecting and using additive compounds, it is necessary to fully consider their compatibility with various materials in the hydraulic system to ensure that the additive compounds will not cause damage to the system components.
With the continuous development of industrial technology, the working conditions of hydraulic systems are becoming more and more demanding, and the requirements for wear resistance protection are also getting higher and higher. In the future, it is necessary to further develop high-performance and multi-functional wear resistance protection additive compounds to meet the needs of hydraulic systems in different industries and under different working conditions. At the same time, strengthen the research on the action mechanism of additive compounds and their compatibility with materials to provide a more scientific basis for the rational selection and use of additive compounds, so as to better protect hydraulic systems and improve the efficiency and reliability of industrial production.
The Price of Hydraulic Oil Additives Package
The price of Hydraulic Oil Additives Package varies depending on factors such as brand, specification, composition, and sales channels. If you are interested in Hydraulic Oil Additives Package, please feel free to contact us.
Supplier of Hydraulic Oil Additives Package
UNPChemicals is a professional supplier of high-quality and effective Hydraulic Oil Additives Package. We offer several remarkable products, namely High zinc hydraulic oil additives UNP AH502A,Low Zinc Hydraulic Oil Additives UNP AH502B,Zinc-free Hydraulic Oil Additives UNP AH502C,etc.
High zinc hydraulic oil additives UNP AH502A are a type of chemical additive used in hydraulic oils that contain high levels of zinc dialkyldithiophosphate (ZDDP). ZDDP is a well-known anti-wear agent that also provides antioxidant, anti-corrosion, and anti-foam properties. The zinc in these additives plays a crucial role in forming a protective film on metal surfaces within the hydraulic system, thereby reducing wear and extending the life of the system components.
Low Zinc Hydraulic Oil Additives UNP AH502B are a class of advanced lubricant additives designed to enhance the performance of hydraulic oils with reduced zinc content.These additives are formulated to provide a balance of anti-wear,extreme pressure,and antioxidant properties,making them suitable for modern hydraulic systems that demand high performance with lower environmental impact.
Zinc-free Hydraulic Oil Additives UNP AH502C are a new class of environmentally friendly lubricant additives designed for hydraulic systems.These additives are formulated to provide the same level of performance as traditional zinc-containing additives but without the heavy metal content,reducing the environmental impact of hydraulic fluids.
Professional Lubricant Additive Manufacturer
UNPChemicals,aka Luoyang Pacific United Petrochemical Co., Ltd., focuses on the application and development of special lubricating grease additives such as MODTC, MODTP, molybdenum amide, thiadiazole metal deactivators, and phosphate esters. With nearly 30 products in seven series, including extreme pressure anti-wear additives and special grease additives, it is a global manufacturer of special lubricating grease additives and a national high-tech enterprise with great influence and leading role in the industry. If you are looking for Lubricant Additive or technical information, feel free to contact UNPChemicals.