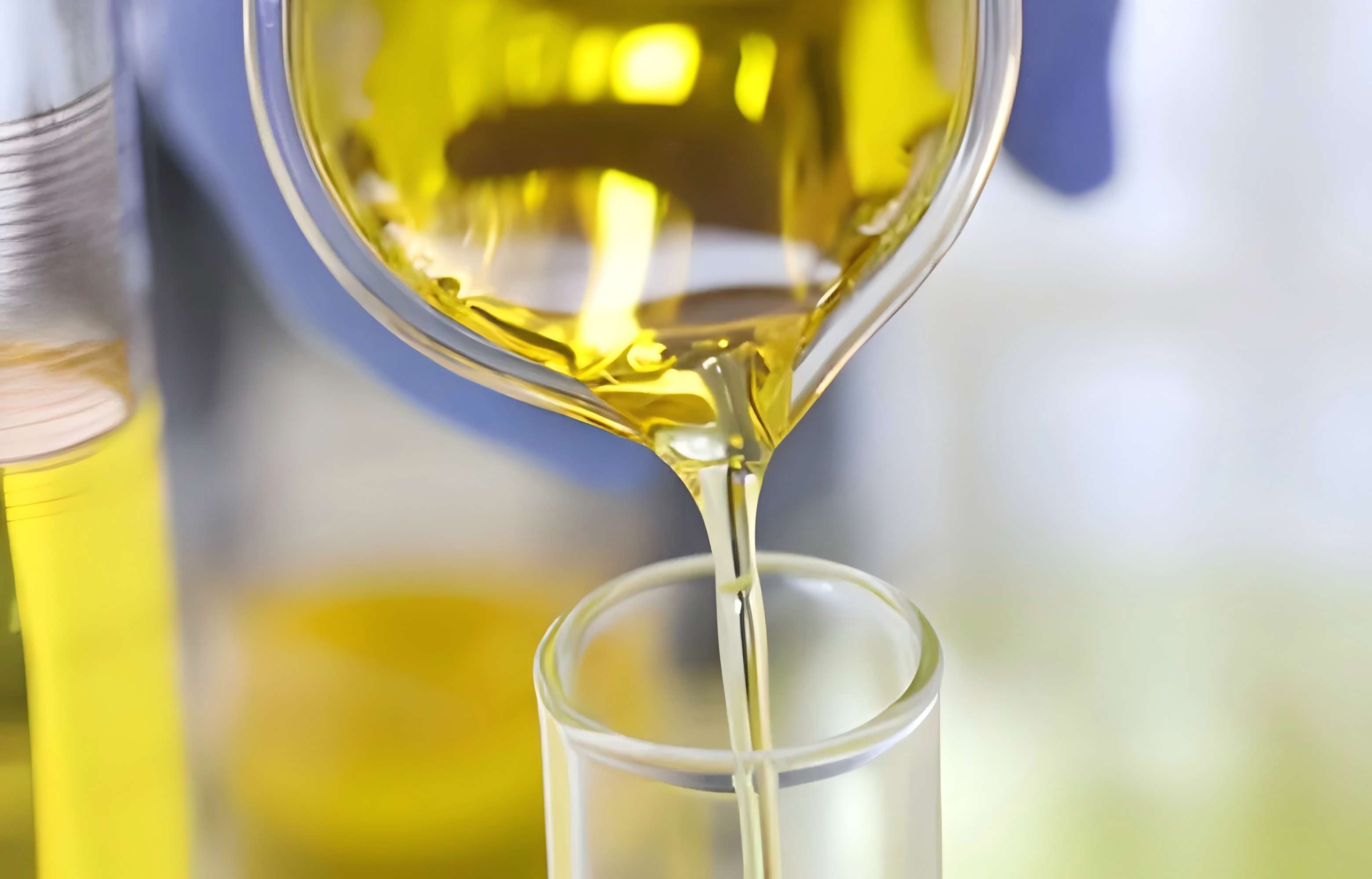
Turbine Oil: A Comprehensive Analysis of Characteristics, Hazards and Maintenance
I. Overview of Turbine Oil
Turbine oil (Turbine Oil) is a lubricating oil specifically designed for rotating power equipment such as steam turbines, gas turbines, and hydraulic turbines. It has functions such as lubrication, cooling, sealing, and rust prevention. Its base oil is usually deeply refined mineral oil or synthetic oil (such as PAO, ester oil), and composite additives such as antioxidants, rust inhibitors, and demulsifiers are added to meet the performance requirements under high-temperature, high-pressure, and high-speed working conditions. The core indicators of turbine oil include viscosity index, oxidation stability, demulsibility, air release property, and corrosion resistance.
II. Hazards of Turbine Oil Deterioration
If the turbine oil deteriorates during use, the following serious problems will occur:
1. Decrease in lubrication performance: Impurities in the oil (such as metal particles and dust) or moisture will damage the continuity of the oil film, resulting in increased wear of the friction pairs, and even causing the burning of the bearing bushes.
2. Equipment corrosion: Moisture and acidic oxidation products (such as organic acids) will corrode metal components, especially bearings and seals made of copper and lead alloy materials.
3. Generation of sludge and sediment: The gums and asphaltenes formed after the oxidation of the oil will block the filter screen and the oil circuit, affecting the circulation efficiency of the oil.
4. Foaming and cavitation: Oils with poor air release properties are prone to generate foam, resulting in pump cavitation, unstable oil pressure, and in severe cases, causing cavitation damage.
5. Decrease in insulation performance: Moisture and pollutants will reduce the dielectric strength of the oil, threatening the electrical safety of the generator set.
III. Factors and Prevention Measures of Water Infiltration in Turbine Oil
(1) Analysis of the Causes of Water Infiltration
1. Failure of the sealing system: Poor sealing of the steam turbine shaft seal, oil tank breather valve, or pipeline joints will lead to the infiltration of water vapor or condensed water.
2. Large operating temperature difference: When the unit starts and stops frequently or the environmental humidity is high, moisture is likely to condense on the inner wall of the oil tank.
3. Leakage of the cooler: Corrosion of the pipe wall of the oil cooler or aging of the sealing gasket will cause the cooling water to mix into the oil system.
4. Improper maintenance operation: Failure to strictly filter when refilling the oil or failure to drain the oil tank regularly.
(2) Measures to Prevent Water Infiltration
1. Optimize the sealing design: Adopt structures such as double-lip seals and labyrinth shaft seals, and regularly check the status of the sealing parts.
2. Control the operating environment: Install a dehumidification device to keep the ventilation system of the oil tank dry.
3. Strengthen equipment monitoring: Install an online moisture sensor to monitor the moisture content in the oil in real time (usually required to be ≤ 0.1%).
4. Standardize the maintenance process: Use a vacuum oil filter to dehydrate regularly, and detect the moisture index of the new oil before refilling.
IV. Causes, Hazards and Prevention of Turbine Oil Emulsification
(1) Formation Mechanism of Emulsification
When the moisture content in the oil exceeds the standard (> 0.1%) and there is mechanical shear force, water molecules combine with polar substances in the oil (such as oxidation products and metal soaps) to form a stable oil-in-water (O/W) or water-in-oil (W/O) emulsion.
(2) Hazards of Emulsification
1. Lubrication failure: The viscosity of the emulsion is abnormal, the bearing capacity of the oil film decreases, and the wear of the bearing is accelerated.
2. Accelerated oxidation: Moisture acts as a catalyst to promote the oxidation of the oil to produce acidic substances.
3. System blockage: The emulsion adheres to the filter screen and valves, hindering the smooth flow of the oil circuit.
4. Increased rusting: The free water in the emulsion directly contacts the metal surface, inducing rusting.
(3) Measures to Prevent Emulsification
1. Select oils with high demulsibility: Select products with a demulsification time (ASTM D1401) ≤ 30 minutes.
2. Add demulsifiers: Compounds such as polyethers can break the water-oil interface film and accelerate the separation of oil and water.
3. Optimize the system design: Set an inclined bottom or a conical bottom in the oil tank to facilitate the sedimentation and discharge of water.
4. Strengthen daily management: Regularly carry out centrifugal separation or vacuum dehydration treatment.
V. Selection Strategy of Turbine Oil Additives
Turbine oil additives need to be comprehensively selected according to the equipment working conditions, the type of base oil of the oil, and environmental protection requirements:
1.Antioxidants: Amine-based (such as diphenylamine) or phenol-based (such as 2,6-di-tert-butyl-p-cresol) antioxidants are preferably selected to extend the service life of the oil.
2.Rust inhibitors: Sulfonate-based (such as barium petroleum sulfonate) rust inhibitors have a significant rust prevention effect on iron-based metals, and carboxylic acid-based rust inhibitors are suitable for multi-metal systems.
3.Demulsifiers: Polyether-based (such as ethylene oxide-propylene oxide copolymer) demulsifiers can quickly break the emulsion.
4.Antifoaming agents: The addition amount of silicone-based or acrylate-based antifoaming agents needs to be controlled (usually ≤ 10 ppm) to avoid affecting the air release property.
5.Extreme pressure anti-wear agents: In heavy-duty working conditions, ashless organic molybdenum compounds (such as MoDTC) can be added to balance environmental protection and performance.
Notes:
- The additives need to be compatible with the base oil to avoid precipitation or delamination.
- The composite formula needs to be verified for synergistic effects through bench tests.
- Comply with environmental protection regulations (such as REACH in the European Union) and limit the content of sulfur, phosphorus, and chlorine elements.
Conclusion
The maintenance of turbine oil is the key to ensuring the efficient operation of the unit. By strictly monitoring the oil quality, optimizing the sealing system, and rationally selecting additives, the oil change cycle can be significantly extended (usually up to 5-8 years), and the equipment failure rate can be reduced. In the future, with the development of synthetic oil technology, nano-additives, and intelligent monitoring systems, the performance and management of turbine oil will reach a higher level, providing more reliable lubrication support for the energy and power industry.
The Price of Turbine Oil Additives Package
The price of Turbine Oil Additives Package varies depending on factors such as brand, specification, composition, and sales channels. If you are interested in Turbine Oil Additives Package, please feel free to contact us.
Supplier of Turbine Oil Additives Package
UNPChemicals is a professional supplier of high-quality and effective Turbine Oil Additives Package. We offer several remarkable products, namely Turbine Oil Additives UNP TB602,etc.
Turbine Oil Additives UNP TB602are a sophisticated blend of compounds designed to enhance the performance and longevity of turbine oils used in a variety of industrial applications.These additives are carefully formulated to address the specific challenges of high-temperature,high-pressure environments common in steam,gas,and hydro turbines.
Professional Lubricant Additive Manufacturer
UNPChemicals, aka Luoyang Pacific United Petrochemical Co., Ltd., focuses on the application and development of special lubricating grease additives such as MODTC, MODTP, molybdenum amide, thiadiazole metal deactivators, and phosphate esters. With nearly 30 products in seven series, including extreme pressure anti-wear additives and special grease additives, it is a global manufacturer of special lubricating grease additives and a national high-tech enterprise with great influence and leading role in the industry. If you are looking for Lubricant Additive or technical information, feel free to contact UNPChemicals.