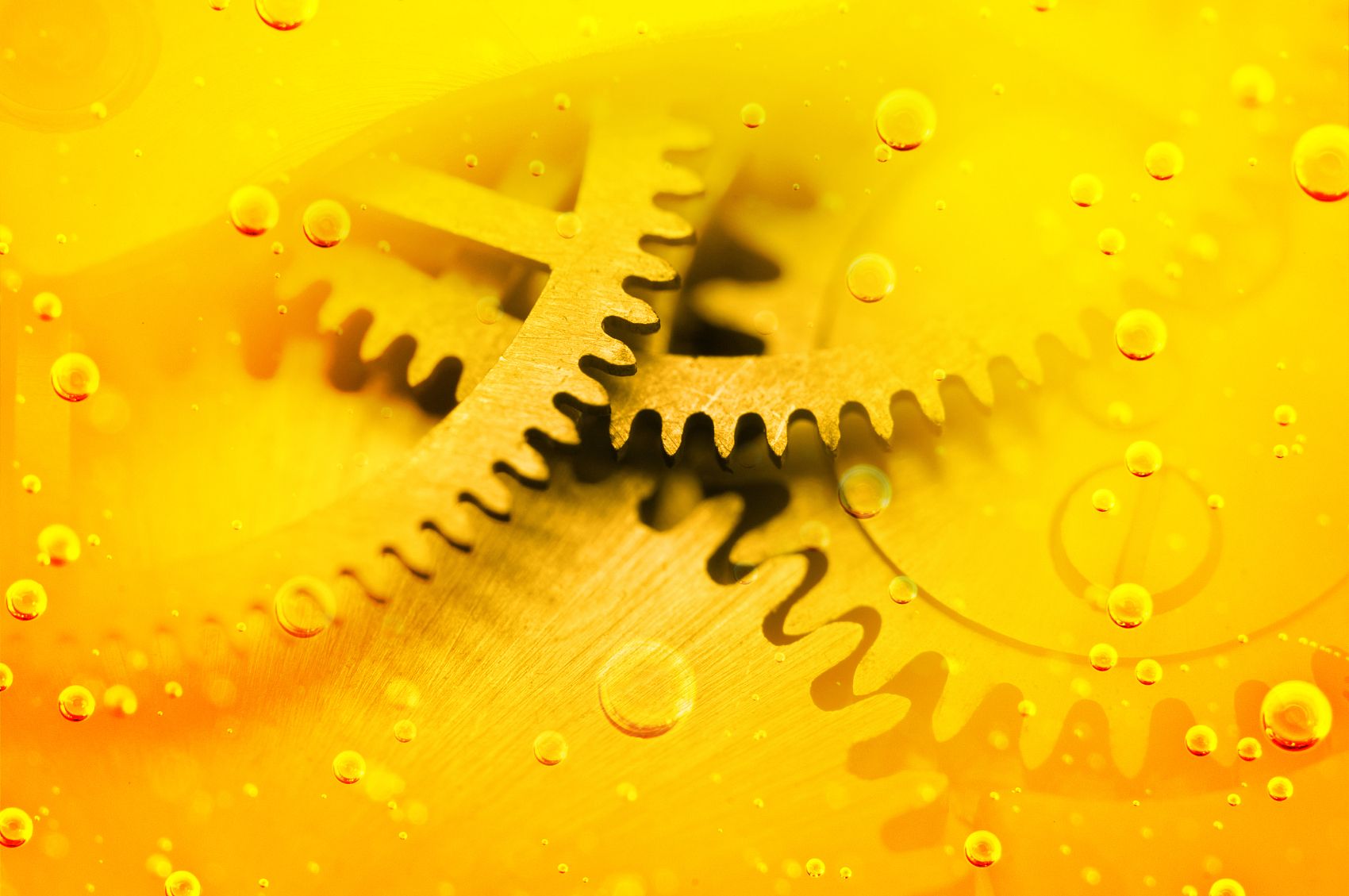
The Scientific Principles of Lubricant Additive Packages
The Interaction between Additive Packages and Base Oils
Lubricant additive packages are an important component of lubricants, and their formulation design is based on complex chemical and physical scientific principles. The interaction between additive packages and base oils is the core of the formulation design, directly determining the performance and service life of the lubricant. Base oils are typically composed of mineral oils, synthetic oils, or bio-based oils and have basic lubricating capabilities. However, their performance often cannot meet the requirements of modern mechanical equipment under high-temperature, high-pressure, or complex working conditions. Through the interaction with base oils, additive packages significantly enhance the anti-wear, anti-oxidation, anti-corrosion, and cleaning and dispersing properties of the lubricant.
The interaction between additive packages and base oils is mainly reflected in the following aspects:
Solubility: Additive packages need to have good solubility in base oils to ensure their uniform distribution and effective function. If the solubility is insufficient, it may lead to the precipitation or stratification of additive packages, reducing the overall performance of the lubricant.
Stability: Chemical reactions between additive packages and base oils should be minimized as much as possible to maintain the stability of the lubricant during long-term use. Adverse reactions may generate by-products, affecting the function of the lubricant.
Synergistic Effect: Certain components within additive packages and between additive packages and base oils can produce a synergistic effect, thereby enhancing the comprehensive performance of the lubricant. For example, the combination of anti-wear agents and anti-oxidants may simultaneously improve the wear resistance and durability of the lubricant.
Through in-depth research on the interaction between additive packages and base oils, formulation designers can better select and optimize the components of additive packages to ensure that the lubricant meets specific usage requirements.
Chemical Mechanisms: The Action Mechanisms of Additive Packages
Lubricant additive packages are composed of a variety of chemical substances, and their action mechanisms cover multiple aspects such as friction modification, corrosion inhibition, anti-oxidation, and cleaning and dispersion. The following is a detailed analysis of these mechanisms:
Friction Modification
Friction modifiers form a protective film on the friction surface to reduce the friction coefficient and minimize the wear of mechanical components. Common friction modifiers include organic molybdenum compounds and phosphates. For example, organic molybdenum compounds decompose under high-temperature and high-pressure conditions to form molybdenum disulfide (MoSâ‚‚). Molybdenum disulfide has a layered structure and can form a low-shear-strength film on the friction surface, effectively reducing friction and wear. This mechanism is particularly important under high-load working conditions.
Corrosion Inhibition
Corrosion inhibitors prevent corrosion by adsorbing on the metal surface to form a protective layer, preventing corrosive media (such as moisture and oxygen) from coming into direct contact with the metal. Common corrosion inhibitors include sulfonates and amine compounds. Sulfonates can form stable chemical bonds with the metal surface to construct a dense protective film, effectively isolating external corrosion factors. This mechanism is crucial for protecting mechanical components in wet or acidic environments.
Anti-oxidation
Anti-oxidants delay the oxidation process of the lubricant and extend its service life by capturing free radicals or decomposing peroxides. Common anti-oxidants include phenolic compounds and amine compounds. For example, phenolic anti-oxidants can provide hydrogen atoms to react with free radicals, neutralize their activity, and thus block the progress of the oxidation chain reaction. This mechanism is particularly critical for lubricants operating under high-temperature conditions, as high temperatures will accelerate the oxidation reaction.
Cleaning and Dispersion
Cleaning and dispersants prevent the deposition and aggregation of dirt particles by adsorbing on their surfaces, maintaining the cleanliness of the lubricant. Common cleaning and dispersants include sulfonates and amide compounds. Sulfonates have polar groups that can attach to dirt particles, keeping them suspended in the lubricant and preventing the formation of deposits on the mechanical surface. This mechanism is particularly important in internal combustion engine oils, as combustion products may generate a large amount of dirt.
The above action mechanisms indicate that additive packages significantly enhance multiple properties of the lubricant through specific chemical reactions and physical adsorption processes. Formulation designers need to select appropriate components of additive packages according to the specific application of the lubricant.
Formulation Challenges: Compatibility Issues and Technical Difficulties
The formulation design of lubricant additive packages faces many challenges, among which compatibility issues are one of the core factors. There must be good compatibility between the components of additive packages and between additive packages and base oils. Otherwise, it may lead to a decline in the performance of the lubricant or even failure. In addition, formulation design also needs to solve multiple technical difficulties to ensure the applicability of the lubricant under different working conditions.
Compatibility Issues
Compatibility issues can be divided into two aspects: chemical compatibility and physical compatibility:
Chemical Compatibility: There should be no adverse chemical reactions between the components of additive packages and between them and base oils. For example, certain anti-oxidants may react with anti-wear agents, generating precipitation or losing their original activity, thus reducing the performance of the lubricant. In formulation design, the chemical stability of each component needs to be verified through experiments to avoid such problems.
Physical Compatibility: Additive packages should maintain good solubility and stability in base oils, avoiding stratification or precipitation. For example, certain polymer additive packages may precipitate under low-temperature conditions, affecting the low-temperature fluidity of the lubricant. To ensure physical compatibility, it is necessary to adjust the structure of additive packages or add solubilizers.
Technical Difficulties
The technical difficulties in formulation design include the following aspects:
Balancing Performance: Lubricants need to have multiple properties such as anti-wear, anti-oxidation, and anti-corrosion simultaneously, and the effects of different additive packages may interact with each other. For example, excessive addition of anti-wear agents may weaken the effect of cleaning and dispersants, leading to dirt deposition. Formulation design needs to find the best balance among these properties.
Adaptability: Lubricants need to adapt to different working conditions and environments, such as high-temperature and high-pressure, low-temperature fluidity, or frequent starts and stops. The formulation of additive packages needs to have both universality and specificity to meet diverse application requirements. For example, internal combustion engine oils need to deal with the challenges of high-temperature oxidation and low-temperature starting simultaneously.
Cost Control: The cost of additive packages is an important factor in lubricant production. High-performance additive packages (such as certain synthetic anti-oxidants) are usually expensive. Formulation design needs to balance performance and cost to ensure the market competitiveness of the product.
To solve these challenges, it is necessary to rely on scientific experimental methods and theoretical analysis, such as optimizing the formulation ratio through orthogonal experiments or using molecular simulation technology to predict the compatibility of additive packages.
The Importance of Scientific Principles in Optimizing the Performance of Additive Packages
Scientific principles are the foundation of the formulation design of lubricant additive packages, directly guiding the selection, formulation ratio, and optimization process of additive packages. Only by deeply understanding the interaction between additive packages and base oils, the action mechanisms of additive packages, and the technical challenges in formulation design can we develop lubricant products with excellent performance, stability, and reliability.
The specific applications of scientific principles in formulation design include:
Selecting Appropriate Components of Additive Packages: According to the usage environment and performance requirements of the lubricant, select additive packages with specific action mechanisms. For example, under high-temperature working conditions, phenolic compounds with strong anti-oxidation performance should be preferentially selected.
Optimizing the Formulation Ratio of Additive Packages: Determine the best formulation ratio of each component through experiments and theoretical analysis. For example, use orthogonal experimental design to optimize the ratio of anti-wear agents and cleaning and dispersants to achieve the best combination of performance.
Solving Compatibility Issues: Improve the solubility and stability of additive packages in base oils by adjusting their structure or adding additives. For example, introducing solubilizers can improve the low-temperature compatibility of polymer additive packages.
Promoting Formulation Innovation: Develop new components and formulations of additive packages based on scientific principles to meet market demands. For example, research and develop environmentally friendly additive packages to reduce the potential environmental impact of lubricants.
The Price of Additive Packages
The price of Additive Packages varies depending on factors such as brand, specification, composition, and sales channels. If you are interested in Additive Packages, please feel free to contact us.
Supplier of Additive Packages
UNPChemicalsis a professional supplier of high-quality and effective Additive Packages. We offer several remarkable products, namely Industrial Gear Oil Additives UNP IG402A,High extreme pressure (EP) type industrial gear oil additive packages UNP IG402B,Low-Odor Type Industrial Gear Oil Additive Package UNP IG402C,etc.
Industrial Gear Oil Additives UNP IG402A are a specialized class of compounds designed to enhance the performance of gear oils in various industrial applications.These additives are carefully formulated to provide a combination of properties that improve the efficiency,longevity,and reliability of gear systems.
High extreme pressure (EP) type industrial gear oil additive packages, like UNP IG402B, are specialized blends of chemical compounds designed to enhance the performance of base oils used in industrial gear lubricants. These packages are formulated to provide exceptional protection under conditions where gears experience heavy loads, high pressures, and potential metal-to-metal contact.
The Low-Odor Type Industrial Gear Oil Additive Package UNP IG402C is a specialized blend of chemical additives designed to enhance the performance of industrial gear oils while minimizing the strong odors typically associated with traditional gear oil additives, particularly those containing sulfur-based extreme pressure (EP) agents. This additive package is mixed with base oils (mineral or synthetic) to create gear lubricants that protect industrial gearboxes under demanding conditions, such as high loads and temperatures, while being more user-friendly in terms of smell—ideal for environments where odor control is a priority.
Professional Lubricant Additive Manufacturer
UNPChemicals, aka Luoyang Pacific United Petrochemical Co., Ltd., focuses on the application and development of special lubricating grease additives such as MODTC, MODTP, molybdenum amide, thiadiazole metal deactivators, and phosphate esters. With nearly 30 products in seven series, including extreme pressure anti-wear additives and special grease additives, it is a global manufacturer of special lubricating grease additives and a national high-tech enterprise with great influence and leading role in the industry. If you are looking for Lubricant Additive or technical information, feel free to contact UNPChemicals.