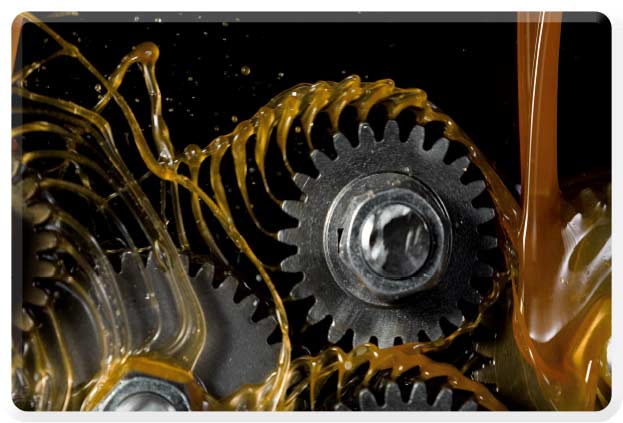
The most important property of lubricants - lubricity
What is Friction Modifiers in lubricating oil additives?
Friction modifiers are a crucial component within lubricating oil additives. They are chemical substances specifically designed to modify the frictional characteristics between two surfaces in contact. In essence, they work to minimize the resistance that occurs when different mechanical parts move against each other. These modifiers can be either organic or inorganic compounds, with each type possessing unique molecular structures and properties that enable them to interact with the metal surfaces at a microscopic level. For instance, some common organic friction modifiers contain long hydrocarbon chains that can adsorb onto the metal, creating a slippery layer. This layer acts as a buffer, reducing the direct contact and subsequent friction between the mating surfaces, which is vital for the smooth operation of various machinery, ranging from automotive engines to industrial gearboxes.
Features of Friction Modifiers in lubricating oil additives
One prominent feature of friction modifiers is their ability to form a tenacious yet flexible film on the friction surfaces. This film has excellent adhesion properties, ensuring it remains intact even under high pressure and shear forces. It is also thin enough not to interfere with the precise fit of mechanical components but thick enough to provide effective lubrication. Another characteristic is their compatibility with other additives in the lubricant formulation. Friction modifiers must coexist harmoniously with anti-wear agents, antioxidants, and detergents, among others, to achieve comprehensive performance enhancement. They are often formulated to have a wide temperature range of effectiveness, maintaining their lubricating capabilities from extremely cold startup conditions to the high temperatures generated during continuous operation. Additionally, many modern friction modifiers are designed to be environmentally friendly, with low toxicity and biodegradability, meeting the stringent requirements of today's sustainable industrial and automotive sectors.
The most important property of lubricants - lubricity
Lubrication is the primary means to reduce friction and wear. Therefore, the most important property of lubricating greases and all other lubricants is their lubricity. The lubricity of lubricating greases is manifested as oilness, antiwear property, and extreme pressure. Among the three manifestations of lubricity, "oilness" is actually quite difficult to describe and not easy to quantify qualitatively or quantitatively. For example, some people say that soybean oil looks "oilier" than peanut oil, but this is just a perception of appearance. The author believes that "oilness" should be more reflected in its adhesiveness and self-healing ability, enabling the oil film it forms to adhere firmly to the metal surface and not easily break; once the oil film is damaged, it also has the ability to self-heal and recover. Therefore, "oilness" is defined as the adsorption capacity of lubricating oil on the metal surface. When oiliness additives are added to the oil, they can form a directional adsorption film on the metal surface, thus improving the friction performance.
Initially, animal and vegetable fats and oils were commonly used to improve the lubricity of oil products, so they were called oiliness agents. Later, it was discovered that some other compounds could also improve the lubricity of oil products. Therefore, substances that can reduce the friction coefficient of the friction surfaces are now collectively referred to as friction modifiers. The main function of lubricating greases is to reduce the friction coefficient and wear. The lubrication states between two friction surfaces can be divided into fluid lubrication, mixed lubrication, and boundary lubrication. The thickness of the oil film and the friction coefficient are different under different lubrication states. The oil film in fluid lubrication is the thickest, while that in boundary lubrication is the thinnest. The friction coefficient in fluid lubrication is the smallest, ranging from 0.001 to 0.006, and that in boundary lubrication is the largest, which can be greater than 0.5. The most ideal lubrication state is fluid lubrication. When the contact pressure of the friction surface is low, the sliding speed is high, and the friction surface is completely separated by the fluid, this is the fluid lubrication state; there is a certain thickness of intact oil film between the friction surfaces, which changes the solid friction between the friction surfaces into fluid friction. The magnitude of the friction coefficient only depends on the viscosity of the fluid, so its friction coefficient is the smallest and the lubrication effect is the best. The vast majority of lubrication states are in the mixed lubrication state. The so-called mixed state means that fluid lubrication and boundary lubrication coexist. In this state, the thickness of the lubricating oil film is similar to the integral average value of the maximum height points (relative to the surface) on the micro-asperities protruding from the mating surfaces. The two metal surfaces are relatively close, and occasional metal-to-metal contact occurs. To reduce metal-to-metal contact, the two metal surfaces must be separated and the strength of the fluid oil film maintained. At this time, friction modifiers generally need to be added to the oil product.
The functions of friction modifiers in lubricating oil additives
Friction modifiers are usually applied in the boundary lubrication state to reduce the friction coefficient and improve lubricity. Friction modifiers all contain polar groups and have a strong affinity for metal surfaces. Through their polar groups, they are powerfully adsorbed onto the metal surface, forming a protective film to separate the metals and prevent their direct contact, thus achieving the effect of reducing friction and wear. The adsorption of friction modifiers on the metal surface belongs to physical adsorption, and physical adsorption is reversible. When the temperature rises to a certain extent, the physical adsorption film will desorb. Different friction modifiers have different lower temperature limits for desorption; it is generally believed that the desorption temperatures of aliphatic amines and aliphatic amides are relatively high. Meanwhile, the friction reduction effect of friction modifiers is related to the position of the polar groups; the most suitable position of the polar groups is at the end of the long-chain hydrocarbon. The polar group ends of the long-chain friction modifier molecules will be vertically adsorbed on the metal surface, and their hydrocarbon moieties will also stand upright in the oil. If the position of the polar group moves forward, the polar group of the molecule will not be able to adsorb vertically, which will hinder the dense adsorption of oiliness agents, resulting in a discontinuous and non-compact oil film. In addition, the longer the hydrocarbon chain, the greater the thickness of the adsorption film and its strength.
The application of Friction Modifiers in lubricating oil additives
Automotive industry: In engines, transmission systems, and axles, friction modifiers are indispensable. They contribute to better engine performance, smoother gear shifting, and reduced wear on drivetrain components. In hybrid and electric vehicles, where energy efficiency is even more critical due to battery limitations, these modifiers help optimize the operation of electric motors and associated mechanical parts.
Industrial machinery: From heavy-duty construction equipment to delicate manufacturing tools, lubricants with friction modifiers are used to enhance the efficiency and longevity of machinery. In metalworking processes, such as machining and forging, they ensure accurate and smooth operation of cutting tools and dies, improving the quality of finished products.
Aerospace sector: Aircraft engines and landing gear systems demand extremely reliable lubrication. Friction modifiers are carefully selected to meet the stringent requirements of high-altitude, low-temperature, and high-load conditions. They help reduce fuel consumption during flight and ensure the safe and smooth operation of critical aerospace components.
The classification of friction modifiers
Organic friction modifiers: These are typically based on fatty acids, esters, and amides. Fatty acid-based modifiers, like oleic acid derivatives, are widely used due to their excellent adsorption properties on metal surfaces. They form a monolayer that provides effective lubrication, especially at low to moderate loads. Ester-based modifiers offer good thermal stability and are suitable for applications where higher temperatures are involved. Amide-based friction modifiers are known for their strong adhesion and ability to withstand shear forces, making them ideal for heavy-duty applications.
Inorganic friction modifiers: Graphite, molybdenum disulfide, and boron nitride are common examples. Graphite has a layered structure that allows it to slide easily between surfaces, providing excellent lubrication, especially in dry or boundary lubrication conditions. Molybdenum disulfide forms a robust film that can withstand high pressures and is often used in extreme-pressure applications, such as in mining and off-road equipment. Boron nitride offers high thermal conductivity and good chemical stability, making it suitable for use in high-temperature environments like those found in some industrial furnaces.
Nanoparticle-based friction modifiers: With the advancement of nanotechnology, nanoparticles such as copper nanoparticles, titanium dioxide nanoparticles, and carbon nanotubes have emerged as innovative friction modifiers. These nanoparticles can penetrate microcracks and pores on the metal surface, enhancing the lubricating effect. They also have unique mechanical and chemical properties that can further improve the performance of lubricants, such as increased hardness and reactivity, leading to better wear resistance and friction reduction.
The Price of friction modifiers in lubricating oil additives
The price of friction modifiers in lubricating oil additives varies depending on factors such as brand, specification, composition, and sales channels. If you are interested in friction modifiers, please feel free to contact us.
Supplier of friction modifiers in lubricating oil additives
UNPChemicals is a professional supplier of high-quality and effective friction modifiers in lubricating oil additives. We offer several remarkable products, namely Molybdenum dithiophosphate MSAIL 300L MoDTP, Molybdenum dithiocarbamate MSAIL 525A MoDTC,Organomolybdenum complex S/P free MSAIL 8550 and Nitrogen-containing boric acid esters FMET 2890.
Molybdenum Dithiophosphate (MoDTP) MSAIL 300L as a liquid organic molybdenum friction modifier containing sulfur and phosphorus, it can greatly reduce the friction coefficient of oil products, and has multiple functions such as extreme pressure, anti-wear and anti-oxidation. It is widely used in internal-combustion engine oil, various industrial lubricants, pure oil metalworking fluid, grease, etc.
Molybdenum Dithiocarbamate MSAIL 525A MoDTC is a phosphate-free liquid organic molybdenum friction modifier, which can greatly reduce the friction coefficient of oil products, and has a variety of functions such as anti-wear and anti-oxygen, and is widely used in internal combustion engine oil, various industrial lubricants, pure oil-type metal working fluids, greases, etc.
Organomolybdenum complex (S/P free) MSAIL 8550 is a highly versatile and environmentally friendly lubricant additive belonging to the Organomolybdenum complex class. Its exceptional friction reduction properties, superior performance when combined with sulfur additives, and antioxidation synergism make it an ideal choice for a wide range of applications. Mainly used for internal-combustion engine oil, various industrial lubricating oils, pure oil metalworking fluid and lubricating grease.
Nitrogen-containing boric acid esters FMET 2890 is an ashless friction modifier that does not contain sulfur or phosphorus. It has excellent friction reduction, wear resistance, and corrosion inhibition performance. It is widely used in internal-combustion engine oil, various industrial lubricants, pure oil metalworking fluid, grease, etc.
Conclusion
Friction modifiers are crucial in lubricating oils. They modify frictional characteristics, have good characteristics to handle complex conditions and meet environmental needs, shine in boundary lubrication, are widely applied in multiple industries, and work with other properties to optimize lubrication and improve mechanical equipment's performance in different lubrication states.
UNPChemicals supplies various lubricating oil additives such as friction modifiers, metal deactivators, extreme pressure anti-wear agents and metal processing additives. If you're interested, please contact us.