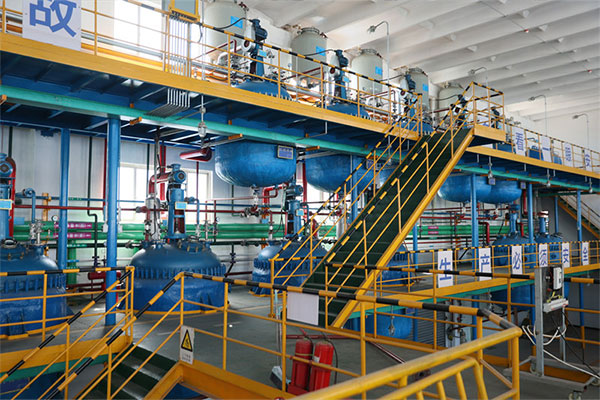
The Impact of Lubricant Additives on Lubricant Quality
In the grand landscape of modern industry and daily life, lubricants hold an indispensable and crucial position. Whether it is the high - speed operation of automobile engines, the efficient work of industrial machinery and equipment, the precise operation of precision instruments, or the smooth running of daily household appliances, they all rely on the silent assistance of lubricants. It is like an all - around guardian, not only effectively reducing friction between components, minimizing wear, and extending the service life of equipment, but also possessing multiple key functions such as cooling, sealing, and rust prevention. The quality of lubricants largely depends on the various additives contained therein.
Main Types of Lubricant Additives
Detergent - Dispersants
Detergent - dispersants are like the "cleaning guards" in lubricants. They are mainly composed of polar groups and non - polar groups in a delicate combination. Their common chemical compositions include sulfonates, alkylphenates, salicylates, etc. Their working principle is quite ingenious. The polar groups are like sensitive "adsorbers", which can firmly adhere to the metal surface and impurity particles in the oil. The non - polar groups, on the other hand, are like extended "tentacles", stretching into the oil to evenly disperse the impurity particles in the oil, effectively preventing them from aggregating to form large - particle precipitates, thus constantly maintaining the cleanliness of the lubricant and the clean environment inside engines and other equipment.
Anti-wear Additives
Among numerous anti - wear additives, zinc dialkyldithiophosphate (ZDDP) can be regarded as a "star player". When the equipment is under extreme working conditions of high temperature and high pressure, it is like a loyal "protective messenger". It will undergo a magical chemical reaction on the metal surface, rapidly forming a protective film with low shear strength. This protective film is like a solid barrier, which can significantly reduce the friction coefficient between metal surfaces, greatly minimize wear, and ensure the long - term and stable operation of the equipment.
Antioxidants
Antioxidants are like the "youth preservatives" of lubricants and can be subdivided into phenolic types, amine types, etc. Phenolic antioxidants are like "free - radical hunters". By providing hydrogen atoms, they can precisely capture the free radicals generated during the oxidation process of the oil and decisively terminate the oxidation chain reaction. Amine - type antioxidants, on the other hand, are like "stability creators". They mainly react with free radicals to form stable compounds, thus effectively slowing down the oxidation rate of the oil and greatly extending the service life of the lubricant.
Rust Inhibitors
Rust inhibitors are like the "rust - proof armors" of metals. Their components are diverse, and common ones include petroleum sulfonates, carboxylic acid and its derivatives, etc. They are like highly skilled "craftsmen", capable of carefully creating a dense adsorption film on the metal surface. This film is like an indestructible shield, which can completely isolate the contact between moisture, oxygen, and other corrosive substances and the metal, providing comprehensive rust protection for the metal.
Anti-foaming Agents
Anti - foaming agents are like the "foam - eliminating warriors" in lubricants. They are generally composed of silicone compounds, etc. Their unique chemical properties endow them with extremely low surface tension. Once foam is generated in the lubricant, it is like a quick - reacting "firefighter", which can spread to the surface of the foam at a very fast speed, instantly reduce the surface tension of the foam film, and cause the foam to burst rapidly, thus avoiding the adverse effects of foam on the performance of the lubricant.
Specific Impacts of Each Additive on Lubricant Quality
Impact on Lubricating Performance
Anti-wear additives are undoubtedly the "main force" in improving lubricating performance. By carefully constructing a protective film on the metal surface, it successfully changes the friction mode between metals from direct contact to indirect contact, like laying a "smooth track" between metal components, greatly enhancing the durability of lubrication. Detergent - dispersants, like "environmental guardians", ensure the consistent stability of the lubricating effect by keeping the lubricating surface clean and promptly removing impurity particles that may damage the lubricating film, making the equipment operate more smoothly.
Impact on Oxidation Stability
Antioxidants are the "key guardians" in retarding the oxidation of oil and can effectively inhibit the deterioration process of the oil. There is also a wonderful synergistic effect between different types of antioxidants. For example, when phenolic and amine - type antioxidants work together, it is like a "relay race". They can precisely capture free radicals at different stages of oil oxidation, comprehensively and deeply strengthening the oxidation stability of the lubricant. This not only extends the service life of the lubricant but also significantly reduces the frequency of oil replacement, saving costs for users.
Impact on Rust - proof Performance
Rust inhibitors can firmly play an important role in preventing metal rust in various complex environments, whether it is a humid atmosphere or an environment with acid - base corrosion. At the same time, the compatibility between rust inhibitors and other additives is like a "tacit test". If the compatibility is good, all additives can cooperate with each other like a closely - knit team to jointly enhance the rust - proof effect. Conversely, it may be like a scattered mess, not only weakening the rust - proof ability but also affecting other properties, resulting in a decline in overall performance.
Impact on Oil Cleanliness
Detergent - dispersants are like "cleaning masters", having a powerful ability to disperse sludge, carbon deposits, and other impurities. It can skillfully disperse these stubborn impurities into tiny particles, making them evenly suspended in the lubricant. Subsequently, with the help of the filtering function of the filter, the impurities can be easily removed, thus constantly maintaining the cleanliness of the oil. Anti - foaming agents, like "prevention experts", contribute to maintaining the cleanliness of the oil indirectly by preventing the generation of foam and avoiding a series of problems such as local high temperature and accelerated oxidation of the oil caused by foam.
Impact on Low - temperature Fluidity
Pour point depressants are like the "flow guides" of lubricants in low - temperature environments. They can skillfully change the crystal form of paraffin in the lubricant, like a "stylist", carefully inhibiting the formation of a complex network structure of paraffin, thus effectively reducing the pour point of the lubricant and significantly improving its low - temperature fluidity. In cold low - temperature environments, other additives such as detergent - dispersants and antioxidants will also cooperate with the pour point depressant like close "partners" to ensure that the lubricant can be smoothly delivered to various lubrication parts and guarantee the normal operation of the equipment at low temperatures.
Comprehensive Impact of Interactions between Additives on Lubricant Quality
Positive Impacts Brought by Synergistic Effects
There are often wonderful synergistic effects between different additives, like a wonderful "chemical reaction". For example, when detergent - dispersants and anti - wear additives work together, detergent - dispersants are responsible for promptly dispersing metal debris and other impurities generated by wear, preventing them from causing secondary damage to the equipment, while anti - wear additives focus on protecting the metal surface. The two complement each other and jointly improve the overall performance of the equipment. Another example is that when antioxidants and anti - wear additives cooperate closely, antioxidants create a stable oil environment for anti - wear additives by retarding the oxidation of the oil, enabling them to function better. Together, they extend the service life of the equipment and provide a solid guarantee for the stable operation of the equipment.
Possible Antagonistic Effects and Countermeasures
However, additives do not always "coexist harmoniously". Sometimes, antagonistic effects may occur, like "disharmonious notes". For example, some rust inhibitors and anti - wear additives may undergo unexpected chemical reactions, resulting in the formation of precipitates, like ripples on a calm lake, reducing the performance of the lubricant. To deal with this situation, in the formula design stage, we need to be like a rigorous "scientist", conduct sufficient experiments and research, carefully select additive combinations with good compatibility, and strictly control the addition sequence and proportion of additives to ensure that the performance of the lubricant is always in the best state.
Impact of Additive Selection and Use on Lubricant Quality Importance of Correct Additive Selection
According to the working conditions, characteristics of the equipment, and specific requirements for lubricant performance, accurately selecting suitable additives is as crucial as tailoring a "special equipment" for the equipment. For example, in the field of industrial equipment with high temperature, high pressure, and high load, just as a battlefield needs powerful weapons, additives with excellent anti - wear and antioxidant properties must be selected to ensure the stable operation of the equipment in harsh environments. For equipment operating in a humid environment, like a house in a humid climate needs a solid roof, special attention should be paid to the selection of rust inhibitors. Only by choosing the right additives can the performance advantages of the lubricant be fully unleashed and perfectly meet the operating requirements of the equipment.
Control of Additive Dosage
The dosage of additives is not a case of "the more the better". Instead, it needs to be precisely controlled, just like mastering the amount of seasonings in cooking. Too few additives are like a stove with insufficient firepower, unable to fully exert their due effects, resulting in a significant reduction in lubricant performance. Excessive additives, on the other hand, may be like excessive seasonings spoiling the taste of a dish, triggering adverse reactions between additives, such as the formation of precipitates and a decrease in the transparency of the oil, which instead has a negative impact on the quality of the lubricant. Therefore, additives must be added strictly according to the specified proportion, just like following an accurate recipe, to ensure that the lubricant performance is optimized.
The Price of Lubricant Additives
The price of Lubricant Additives depending on factors such as brand, specification, composition, and sales channels. If you are interested in Lubricant Additives, please feel free to contact us.
Supplier of Lubricant Additives
UNPChemicals is a professional supplier of high-quality and effective Lubricant Additives. We offer several remarkable products, namely Amine-neutralized hexyl phosphate PSAIL 3490,Amine-neutralized mixed phosphate Esters PSAIL 2280,Phosphorothioate acrylate derivatives PSAIL 3530,etc.
Amine-neutralized hexyl phosphate PSAIL 3490 is a specialized mixture of amine phosphate salts known for its multifunctional ashless additive characteristics. As an ashless additive, PSAIL 3490 does not produce ash as combustion by-products, reducing engine deposits and harmful emissions. PSAIL 3490 is a multifunctional additive, providing a range of benefits in a single product, making it highly versatile and cost-effective.
Amine-neutralized mixed phosphate esters PSAIL 2280 is a multifunctional ashless additive structured as a phosphate ester amine salt with excellent load carrying capacity, anti-wear and corrosion protection properties. As a multifunctional additive, PSAIL 2280 reduces the amount of anti-emulsifier and rust inhibitor and has good tribological properties, especially at higher temperatures, forming thicker boundary lubricant films. In addition, PSAIL2280 is widely used in metalworking fluid formulations in conjunction with sulfur carriers because of its good anti-wear properties.
Phosphorothioate Acrylate Derivatives PSAIL 3530 is an ashless EP/AW additive with dialkyl dithiophosphate structure, especially suitable for industrial lubricating oils with FZG test requirements, such as industrial gear oil, anti-wear hydraulic oil containing ZDDP, lubricating grease and metal processing oil.
Conclusion
The impact of lubricant additives on lubricant quality is extensive and profound, like a closely woven net covering key areas such as lubricating performance, oxidation stability, rust - proof performance, cleanliness, and low - temperature fluidity. Different types of additives are like "professional teams" with their own responsibilities, comprehensively improving the quality of lubricants from various angles to meet the operating requirements of different equipment under various complex working conditions. At the same time, the synergistic and antagonistic effects between additives always remind us that in the process of formula design and use, we should be like a cautious "navigator", carefully planning and operating with caution. Looking to the future, with the rapid development of industrial technology and the increasing requirements for equipment performance, lubricant additives will surely move towards a more efficient, environmentally friendly, and multi - functional direction, injecting a continuous and powerful impetus into the improvement of lubricant quality and providing a more solid guarantee for the development of modern industry and daily life.
UNPChemicals supplies various lubricating oil additives such as friction modifiers, metal deactivators, extreme pressure anti-wear agents and metal processing additives. If you're interested, please contact us.