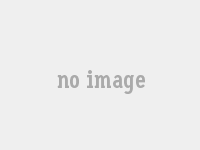
The Guardians in Lubricants: Friction Modifiers and Anti-Wear Additives
Friction modifiers and mild anti-wear agents are critical components in lubricants. By introducing polar molecules, these additives minimize the potential for slight surface contact that can occur in various machine designs, including sliding and rolling mechanisms. Also known as boundary lubrication additives, friction modifiers and anti-wear agents are essential for improving lubricant performance. Commonly used materials for this purpose include esters, natural and synthetic fatty acids, and solid materials such as graphite and molybdenum disulfide.
What are Friction Modifiers and Anti-Wear Additives?
Friction modifiers and anti-wear agents help reduce the friction and wear between metal surfaces under conditions where hydrodynamic lubrication cannot be maintained. In such instances, these additives come into play, preventing excessive wear and extending the life of the machinery. They are essential for enhancing the longevity and efficiency of industrial equipment, engines, and other mechanical systems.
Friction modifiers, in particular, aim to reduce friction in lightly loaded conditions where boundary lubrication exists. By forming a protective molecular layer on the metal surfaces, friction modifiers reduce the direct metal-to-metal contact. Meanwhile, anti-wear agents come into play in more severe conditions where heavier loads or shock forces may be present, preventing further damage to the equipment.
Mechanism of Action of Friction Modifiers and Anti-Wear Agents
These additives operate through molecules with polar ends (heads) and oil-soluble ends (tails). When the lubricant is put into operation, the polar end of the molecule seeks out and attaches to the metal surface. If you could observe these molecules on the surface, you'd find them arranged like fibers on a carpet, standing vertically side by side. As long as the frictional contact remains light, these molecules can act as a buffer when the coated surfaces come into contact with each other. However, when the contact becomes more severe, these molecules can be scrubbed away, losing the potential benefits of the additive.
Anti-wear additives are chosen when designers anticipate more severe surface contact, such as in cases of shock loading. In these scenarios, a more robust friction modifier, known as an anti-wear agent, is needed. A common example of such an additive is zinc dialkyldithiophosphate (ZDDP). When the reaction energy (temperature) becomes high enough, ZDDP reacts with the metal surface to form a protective reaction layer. This sacrificial layer provides surface protection and significantly reduces wear.
The Use of Extreme Pressure (EP) Chemicals
As load and metal-to-metal contact increase, so does the intensity of the additives and reaction process. This brings us to the use of sulfur- and phosphorus-based extreme pressure (EP) chemicals. EP additives form organic metal salts on the load-bearing surface, acting as sacrificial films to prevent corrosive surface damage. EP additives are essential for machines operating under extreme pressure conditions where conventional lubricants are not enough to protect against wear.
There are two main categories of EP additives: those that are temperature-dependent and those that are not. The most common temperature-dependent types include boron, chlorine, phosphorus, and sulfur compounds. When extreme pressure causes the temperature to rise, these additives are activated by reacting with the metal surface. The chemical reactions between the additives and the metal surface are driven by the heat generated from friction.
Similar to rubbing your hands together, when metal surfaces come into contact with each other, the friction and pressure generate heat. As these additives react with the metal surface, new compounds such as iron chloride, iron phosphate, and iron sulfide are formed, depending on the additive being used. These metal salts produce a thin chemical film, acting like soap, forming a barrier that reduces friction, wear, and metal scuffing while eliminating the possibility of welding.
Product Recommendation: FMET 2890 Friction Modifier
FMET 2890 is a high-performance ashless friction modifier, standing out due to its environmentally friendly formulation that contains no sulfur or phosphorus. This advanced additive offers exceptional benefits such as reducing friction, wear protection, and corrosion inhibition, making it an ideal choice for a wide range of applications. FMET 2890 is widely used in internal combustion engine oils, industrial lubricants, neat oil metalworking fluids, and greases to enhance efficiency and performance.
Key Features of FMET 2890
Ashless Formulation: FMET 2890 features an ashless, sulfur- and phosphorus-free composition, providing an environmentally friendly alternative to traditional additives. This ashless formulation helps reduce the environmental impact of the lubricant and ensures compliance with increasingly stringent environmental regulations.
Friction Reduction: By significantly lowering the coefficient of friction in lubricants, FMET 2890 enhances the performance of the lubricant. This feature optimizes the efficiency and energy consumption of various applications, reducing the operating temperature and wear on machinery and components.
Wear Resistance: FMET 2890 provides excellent wear resistance, preventing wear in high-pressure, high-load, and abrasive conditions. This feature helps prolong component life and reduce maintenance costs.
Corrosion Inhibition: It offers excellent corrosion inhibition properties, preventing rust and corrosion on metal surfaces in contact with the lubricant. This characteristic further improves the lifespan of components and the reliability of the overall system.
Functionality of FMET 2890
Friction Modification: By lowering the coefficient of friction in lubricants, FMET 2890 minimizes mechanical friction between moving parts, thereby reducing energy consumption and wear.
Wear Protection: FMET 2890 provides outstanding wear resistance, protecting lubricated parts and components from damage caused by high loads, severe abrasive environments, and extreme temperatures.
Corrosion Inhibition: FMET 2890 effectively inhibits corrosion by forming a protective layer on metal surfaces that come into contact with the lubricant. This layer prolongs the life of components and ensures reliable operation.
Applications of FMET 2890
Internal Combustion Engine Oils: Its friction-reducing and wear-resistant properties significantly improve the performance of gasoline and diesel engine oils, thereby enhancing fuel efficiency, reducing emissions, and extending engine life.
Industrial Lubricants: FMET 2890 is suitable for use in various industrial lubricants used in machinery and equipment. It offers friction modification, wear protection, and corrosion inhibition, ensuring optimal performance throughout the lubricant's lifespan.
Neat Oil Metalworking Fluids: This additive can be used in neat oil metalworking fluids to improve performance during cutting, grinding, and forming operations by reducing friction and wear. This leads to extended tool life, improved workpiece quality, and overall productivity.
Greases: FMET 2890 can be incorporated into greases, offering improved friction reduction, wear protection, and corrosion inhibition properties. These characteristics are particularly beneficial in heavy-load applications where optimal lubricant performance is critical.
Conclusion
In summary, friction modifiers and anti-wear agents play a crucial role in the effectiveness and longevity of lubricants. Their ability to reduce friction, wear, and corrosion helps ensure that machines and engines operate efficiently and last longer. FMET 2890, with its ashless, sulfur- and phosphorus-free formulation, offers a sustainable and high-performance solution for various lubrication needs. Its ability to reduce friction and wear, coupled with its corrosion inhibition properties, makes it an ideal choice for applications ranging from internal combustion engines to industrial machinery. By incorporating friction modifiers like FMET 2890 into lubrication solutions, industries can optimize equipment performance, reduce environmental impact, and lower operational costs.
Supplier Recommendation: Luoyang United Pacific Petrochemical Co., Ltd.
For a comprehensive product solution and top-tier technical support, Luoyang United Pacific Petrochemical Co., Ltd. (LPUPC) offers friction modifiers and anti-wear additives tailored to your needs.
Contact Information:
Address: Luoyang United Pacific Petrochemical Co., Ltd. (LPUPC)
Phone: +86 16638830202
Email: sales@unpchemicals.com
LPUPC provides extensive product solutions to help you find the right metal passivation solution for your needs.