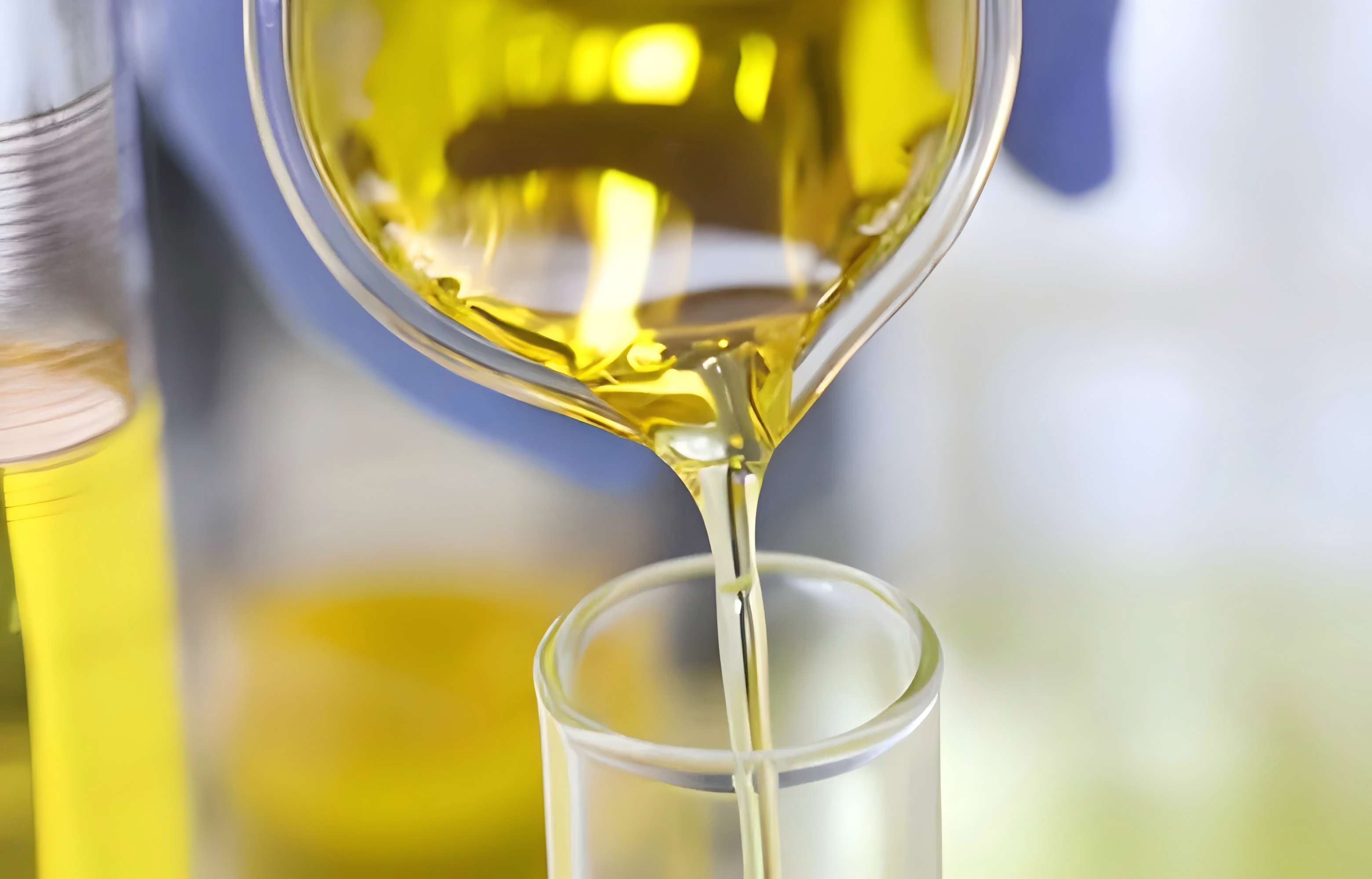
The Environmental Performance of Anti-wear Hydraulic Oil Additive Packages
With the continuous advancement of the global industrialization process, the hydraulic system, as the core power transmission unit of industrial equipment, directly affects the production efficiency of the manufacturing industry through its operational efficiency and reliability. The anti-wear hydraulic oil additive package, as a crucial component of hydraulic oil, can significantly enhance the comprehensive performance of hydraulic oil by synergistically adding various functional additives (such as anti-wear agents, antioxidants, rust inhibitors, etc.), meeting the usage requirements of complex working conditions such as high pressure, high speed, and high temperature. However, traditional anti-wear hydraulic oil additive packages commonly contain compounds of elements such as sulfur, phosphorus, and zinc (such as zinc dialkyldithiophosphate, ZDDP). After the hydraulic oil is discarded, these components are likely to cause soil pollution, eutrophication of water bodies, and even pose potential hazards to the ecosystem and human health through the food chain.
With the enhancement of global environmental protection awareness and the deepening of the concept of sustainable development, environmental protection regulations for industrial lubricants in various countries are becoming increasingly strict. Policy documents such as the EU's Registration, Evaluation, Authorization and Restriction of Chemicals (REACH), the US Environmental Protection Agency (EPA)'s Toxic Substances Control Act (TSCA), and China's Action Plan for Water Pollution Prevention and Control have all put forward clear requirements for the content of harmful substances, biodegradability, and ecotoxicity in lubricants. In this context, the environmental performance of anti-wear hydraulic oil additive packages has become one of the core research and development directions in the industry. Improving the environmental performance of additive packages is not only an inevitable choice to respond to the global trend of green manufacturing but also a crucial link in promoting the low-carbon transformation of the hydraulic system industry chain and building a circular economic system.
I. The Formulation and Requirements of Environmental Standards for Hydraulic Oil Additive Packages
(1) International Environmental Standard Systems
1. The EU REACH Regulation and CLP Classification
Since the implementation of the EU REACH regulation in 2007, it has strictly regulated more than 190 substances of very high concern (SVHC) in lubricants, including components that may be contained in traditional additive packages such as short-chain chlorinated paraffins and phthalate plasticizers. According to the Classification, Labelling and Packaging of Substances and Mixtures (CLP) regulation, anti-wear hydraulic oil additive packages need to be classified for ecotoxicity. It is required that their acute aquatic toxicity (LC50/EC50) is greater than 100 mg/L, and the biodegradation rate reaches more than 60% within 28 days (OECD 301B standard). In addition, the EU's Ecodesign Directive for Industrial Lubricants (EC 1272/2008) further stipulates that hydraulic oil additive packages used in food contact equipment shall not contain substances such as nitrosamines and heavy metals (such as lead, cadmium, mercury).
2. US ASTM and EPA Standards
The D6046 standard formulated by the American Society for Testing and Materials (ASTM) clearly defines the test method for the biodegradability of hydraulic oil. It requires that the hydraulic oil formulated with environmentally friendly additive packages has a biodegradation rate of not less than 60% within 21 days. The US Environmental Protection Agency (EPA)'s Environmentally Preferable Purchasing (EPP) program recommends the use of additive packages based on renewable raw materials, and their bio-based content should reach more than 20% of the total mass. For marine environment-sensitive areas (such as ship hydraulic systems), the US Navy standard MIL-H-5606F prohibits the use of additive package components containing chlorine and fluorine to reduce pollution to the marine ecosystem.
(2) Domestic Environmental Standards and Industry Specifications
1. National Standards and Mandatory Requirements
China's GB/T 30515-2014 "Determination of Biodegradability of Lubricants - Carbon Dioxide Evolution Method" is equivalent to the OECD 301B standard, stipulating that the biodegradation rate of environmentally friendly anti-wear hydraulic oil additive packages should be ≥ 60%. Although GB 30981-2020 "Limit of Harmful Substances in Industrial Protective Coatings" is aimed at the coating field, it indirectly promotes the reduction of volatile organic compounds (VOC) emissions in hydraulic oil additive packages, requiring that the content of solvents such as benzene, toluene, and xylene in the additive packages is ≤ 5%. In addition, GB/T 2433-2001 "Determination of Sulfur Content in Additives and Lubricating Oils Containing Additives" strictly restricts the use of sulfur-based anti-wear agents, and additive packages with a sulfur content exceeding 1.5% have gradually been phased out of the market.
2. Industry Standards and Green Certification
The NB/SH/T 0916-2015 "Environmentally Friendly Hydraulic Oil" standard issued by the China Petroleum and Chemical Industry Federation puts forward higher requirements for the ecological indicators of additive packages: the acute aquatic toxicity (fish) LC50 > 1000 mg/L, the algae growth inhibition rate (72h) < 50%, and it does not contain endocrine-disrupting substances such as APEO (alkylphenol ethoxylates). The China Environmental Labeling Product Certification (CEC) requires that the production process of additive packages complies with the clean production standard, and the energy consumption and water consumption are respectively 15% and 20% lower than the industry average level.
(3) The Promoting Role of Standards in the Industry
The refinement of environmental standards has prompted additive package manufacturers to increase their research and development investment, driving the transformation of the technical route from "end-of-pipe treatment" to "source reduction". For example, due to the high phosphorus content and poor biodegradability of traditional phosphorus-containing anti-wear agents (such as TCP, tricresyl phosphate), their usage in the EU market has decreased by 70%, and they have been replaced by phosphorus-free anti-wear agents (such as borate esters and dimer acid derivatives). At the same time, the international trend of standards forces domestic enterprises to establish a full-life-cycle environmental management and control system, achieving full-chain upgrades from raw material procurement (screening renewable resources), production processes (promoting closed-circuit cooling technology) to product testing (equipped with high-precision instruments such as LC-MS/MS).
II. The R&D Progress of Environmentally Friendly Anti-wear Hydraulic Oil Additive Packages
(1) The Construction of Zinc-free and Phosphorus-free Formulation Systems
1. The Application of New Anti-wear Agents
Traditional ZDDP anti-wear agents contain zinc elements, which are likely to form heavy metal residues after the oil is discarded. Currently, the industry has developed two types of zinc-free anti-wear agents:
Borate Compounds: Through molecular structure design (such as nitrogen-containing heterocyclic borate esters), a chemical adsorption film is formed on the metal surface. The anti-wear performance is better than that of ZDDP (the four-ball test wear scar diameter ≤ 0.45 mm), and it does not contain sulfur, phosphorus, or zinc elements. The biodegradation rate can reach 75% (OECD 301F). For example, after the complexing of propylene glycol borate and oleic acid, the wear resistance life under the working conditions of 100°C and 10MPa is 20% longer than that of the traditional formulation.
Organomolybdenum Compounds: Molybdenum dialkyldithiocarbamate (MoDTC) and fatty acid molybdate salts fill the micro-pits on the metal surface by releasing MoS2 nanoparticles to achieve the "self-healing" function. The friction coefficient of this type of anti-wear agent can be reduced to 0.08 (the traditional ZDDP is 0.12), and the sulfur content < 0.5%, with no risk of heavy metal residues.
2. Phosphorus-free Rust Prevention and Antioxidation Systems
Traditional rust inhibitors (such as sodium petroleum sulfonate) and antioxidants (such as 2,6-di-tert-butyl-p-cresol, BHT) do not contain phosphorus, but they have poor biodegradability. New formulations adopt:
Tricarboxylic Acid Derivatives: Such as tributyl citrate, it inhibits rust by chelating metal ions. The rust prevention performance reaches Class A of the GB/T 11143 standard (no rust within 48h), and the biodegradation rate > 80%.
Natural Antioxidants: Carnosic acid in rosemary extract has a phenolic hydroxyl structure, and its antioxidant effect is better than that of BHT (the oxidation induction time is extended by 30%), and it is non-toxic (LD50 > 5000 mg/kg).
(2) The Development and Application of Bio-based Raw Materials
1. The Esterification Modification of Renewable Fatty Acids
Oleic acid and linoleic acid extracted from soybean oil and rapeseed oil are used to prepare multifunctional additives through epoxidation and amidation reactions:
Bio-based Anti-wear Agents: The film formation speed of oleic acid polyethylene glycol ester in the steel-steel friction pair is 15% faster than that of the mineral oil-based one, and it can be decomposed by Pseudomonas microorganisms. The biodegradation rate within 28 days reaches 82% (ISO 14593).
Bio-based Emulsifiers: Castor oil polyoxyethylene ether (EL-40) is used as the emulsifying component of water-based hydraulic fluid additive packages. The HLB value (hydrophilic-lipophilic balance value) can reach 12-14, the emulsification stability > 6 months, and the ecotoxicity (algae EC50) > 2000 mg/L.
2. The Functional Utilization of Phytosterols
β-Sitosterol extracted from corn germ oil can be used as an antifoaming agent and a viscosity index improver after chemical modification:
Antifoaming Performance: The surface tension of sterol derivatives (28 mN/m at 25°C) is lower than that of traditional silicone antifoaming agents (32 mN/m), and the foam elimination time is shortened by 40%, with no risk of silicon residue pollution.
Viscosity Stability: The viscosity-temperature coefficient (VIT) of sterol ester polymers ≤ 0.02, and the viscosity index of hydraulic oil remains > 150 within the temperature range of -20°C to 120°C, reducing the usage of mineral oil-based polymers.
(3) Low Volatility and Low Toxicity Design
1. The Optimization of the Solvent System
Aromatic solvents commonly used in traditional additive packages (such as toluene and xylene) have strong volatility and are neurotoxic. New formulations adopt:
High-boiling Aliphatic Solvents: Dibutyl sebacate (boiling point 274°C) is used as the carrier solvent. The volatile organic compound (VOC) emissions are 60% lower than those of aromatic solvents, and the acute oral toxicity (LD50) > 5000 mg/kg (belonging to the practically non-toxic grade).
Water-based Technology: For water-ethylene glycol type hydraulic fluid additive packages, oil-soluble additives are encapsulated in amphiphilic polymer capsules through nanodispersion technology to achieve stable dispersion in the water phase, avoiding the use of organic solvents and resulting in zero VOC emissions.
2. The Control of Toxic Risk Substances
For potential carcinogens such as nitrosamines and polycyclic aromatic hydrocarbons (PAHs), GC-MS/MS is used for trace detection during the R&D process to ensure:
The nitrosamine content < 20 μg/kg (required by the EU toy safety standard EN 71-9);
The total PAHs content < 10 mg/kg (German GS certification standard). For example, by screening amine compounds without nitrosamine precursors (such as diethanolamine replacing morpholine), the generation path of nitrosamines is cut off from the source.
(4) The Integration of Nanotechnology and Green Chemistry
1. The Synergistic Effect of Nanoparticles
Adding nanoscale titanium dioxide (TiO2, particle size 20-50 nm) to the additive package can produce dual environmental benefits:
Photocatalytic Degradation: TiO2 catalytically decomposes the organic pollutants in the hydraulic oil under ultraviolet light, increasing the biodegradation rate of the waste oil by 15%;
Reducing the Dosage of Additives: The high specific surface area characteristics of nanoparticles reduce the dosage of anti-wear agents by 30%, while maintaining the same anti-wear performance (the wear scar diameter error < 5%).
2. Green Synthesis Processes
Technologies such as microwave-assisted synthesis and enzymatic esterification are used to reduce energy consumption and pollution:
The reaction time for synthesizing borate esters by the microwave method is shortened from 4 hours of traditional heating to 30 minutes, the energy consumption is reduced by 40%, and the by-products are reduced by 60%;
The conversion rate of synthesizing bio-based lubricants by lipase catalysis > 95%, without the need for acid-base catalysts, and the wastewater discharge is reduced by 80%.
III. The Test and Evaluation Methods for the Environmental Performance of Hydraulic Oil Additive Packages
(1) Biodegradability Performance Testing
1. The Carbon Dioxide Evolution Method (OECD 301B)
The additive package sample and the activated sludge inoculum are placed in a closed reactor and cultured for 28 days at 25°C in the dark. This method can accurately reflect the mineralization ability of microorganisms on the additive package and is an internationally recognized authoritative test standard.
2. The Closed Bottle Test (OECD 301D)
The additive package (concentration 100 mg/L) and the inoculated microorganisms are added to sterile distilled water. After 28 days of cultivation, the dissolved oxygen consumption is measured, and the biodegradation rate is calculated. This method is suitable for the rapid screening of water-based additive packages, and the detection cycle is 50% shorter than that of the CO2 method.
(2) Ecotoxicity Evaluation
1. The Acute Fish Toxicity Test (OECD 203)
Using zebrafish (Danio rerio) as the test organism, it is exposed to different concentrations of the additive package solution for 96 hours, and the median lethal concentration (LC50) is recorded. The LC50 of environmentally friendly additive packages needs to be > 1000 mg/L, indicating low toxicity to aquatic organisms.
2. The Algae Growth Inhibition Test (OECD 201)
Chlorella vulgaris is cultured in the BG11 medium containing the additive package, and the change in the chlorophyll a content within 72 hours is measured, and the median effective concentration (EC50) is calculated. The EC50 of high-quality additive packages > 100 mg/L, and the algae growth inhibition rate < 20%.
(3) Chemical Residue and Toxic Substance Detection
1. Heavy Metal Content Analysis
Inductively coupled plasma mass spectrometry (ICP-MS) is used to determine elements such as lead, cadmium, and mercury in the additive package, and the detection limit can reach 0.1 μg/kg to ensure compliance with the requirements of GB 31604.49-2016 "National Food Safety Standard" for lubricants in contact with food equipment.
2. Screening of Nitrosamines and PAHs
Gas chromatography-tandem mass spectrometry (GC-MS/MS) is used for the qualitative and quantitative analysis of 13 nitrosamines and 18 PAHs, with the minimum detection concentrations of 0.5 μg/kg and 1.0 μg/kg respectively, meeting the strict control requirements of the EU REACH regulation.
(4) The Synergistic Evaluation of Functionality and Environmental Performance
In the ASTM D2714 hydraulic oil anti-wear performance test (vane pump test), the changes in the wear scar diameter and the biodegradation rate are monitored simultaneously, and a "performance-environmental protection" dual-index evaluation model is established. For example, after a 100-hour test, a new type of additive package has a wear scar diameter of 0.42 mm (better than the standard value of 0.50 mm), and at the same time, the biodegradation rate reaches 78%, achieving a simultaneous improvement in anti-wear performance and environmental performance.
IV. Conclusion
Improving the environmental performance of anti-wear hydraulic oil additive packages is the core path for implementing the sustainable development strategy in the industrial lubricant field. From the driving force of environmental standards to the independent innovation of R&D technologies, the industry has formed a development system of "standard leading - technological breakthrough - testing improvement". In the future, with the advancement of the global carbon neutrality goal and the deepening of the concept of green chemistry, the R&D of environmentally friendly additive packages will show three major trends: First, the raw material system will transform towards "fully bio-based". Through technologies such as genetic engineering to improve plant oils and the development of microbial synthetic lubricants, the entire chain from the production to the disposal of additive packages will achieve low-carbonization. Second, the functional design will pursue "high efficiency and low consumption". With the help of molecular simulation technologies (such as density functional theory, DFT), the additive structure will be precisely optimized to improve core performance such as anti-wear and antioxidant properties while reducing the dosage. Third, the evaluation system will tend towards "multidimensional integration". Combining life cycle assessment (LCA) with real-time online monitoring technologies, a full-cycle environmental protection database covering production energy consumption, usage efficiency, and waste disposal will be established.
Although the current manufacturing cost of environmentally friendly additive packages is 15%-20% higher than that of traditional products, with the scale of production and technological maturity, the cost gap will gradually narrow. It can be predicted that under the joint promotion of policy guidance, market demand, and technological innovation, the environmental performance of anti-wear hydraulic oil additive packages will become the core barrier of industry competition, helping the global industrial lubrication field achieve the ultimate goal of "green manufacturing".
The Price of Hydraulic Oil Additives Package
The price of Hydraulic Oil Additives Package varies depending on factors such as brand, specification, composition, and sales channels. If you are interested in Hydraulic Oil Additives Package, please feel free to contact us.
Supplier of Hydraulic Oil Additives Package
UNPChemicals is a professional supplier of high-quality and effective Hydraulic Oil Additives Package. We offer several remarkable products, namely High zinc hydraulic oil additives UNP AH502A,Low Zinc Hydraulic Oil Additives UNP AH502B,Zinc-free Hydraulic Oil Additives UNP AH502C,etc.
High zinc hydraulic oil additives UNP AH502A are a type of chemical additive used in hydraulic oils that contain high levels of zinc dialkyldithiophosphate (ZDDP). ZDDP is a well-known anti-wear agent that also provides antioxidant, anti-corrosion, and anti-foam properties. The zinc in these additives plays a crucial role in forming a protective film on metal surfaces within the hydraulic system, thereby reducing wear and extending the life of the system components.
Low Zinc Hydraulic Oil Additives UNP AH502B are a class of advanced lubricant additives designed to enhance the performance of hydraulic oils with reduced zinc content.These additives are formulated to provide a balance of anti-wear,extreme pressure,and antioxidant properties,making them suitable for modern hydraulic systems that demand high performance with lower environmental impact.
Zinc-free Hydraulic Oil Additives UNP AH502C are a new class of environmentally friendly lubricant additives designed for hydraulic systems.These additives are formulated to provide the same level of performance as traditional zinc-containing additives but without the heavy metal content,reducing the environmental impact of hydraulic fluids.
Professional Lubricant Additive Manufacturer
UNPChemicals,aka Luoyang Pacific United Petrochemical Co., Ltd., focuses on the application and development of special lubricating grease additives such as MODTC, MODTP, molybdenum amide, thiadiazole metal deactivators, and phosphate esters. With nearly 30 products in seven series, including extreme pressure anti-wear additives and special grease additives, it is a global manufacturer of special lubricating grease additives and a national high-tech enterprise with great influence and leading role in the industry. If you are looking for Lubricant Additive or technical information, feel free to contact UNPChemicals.