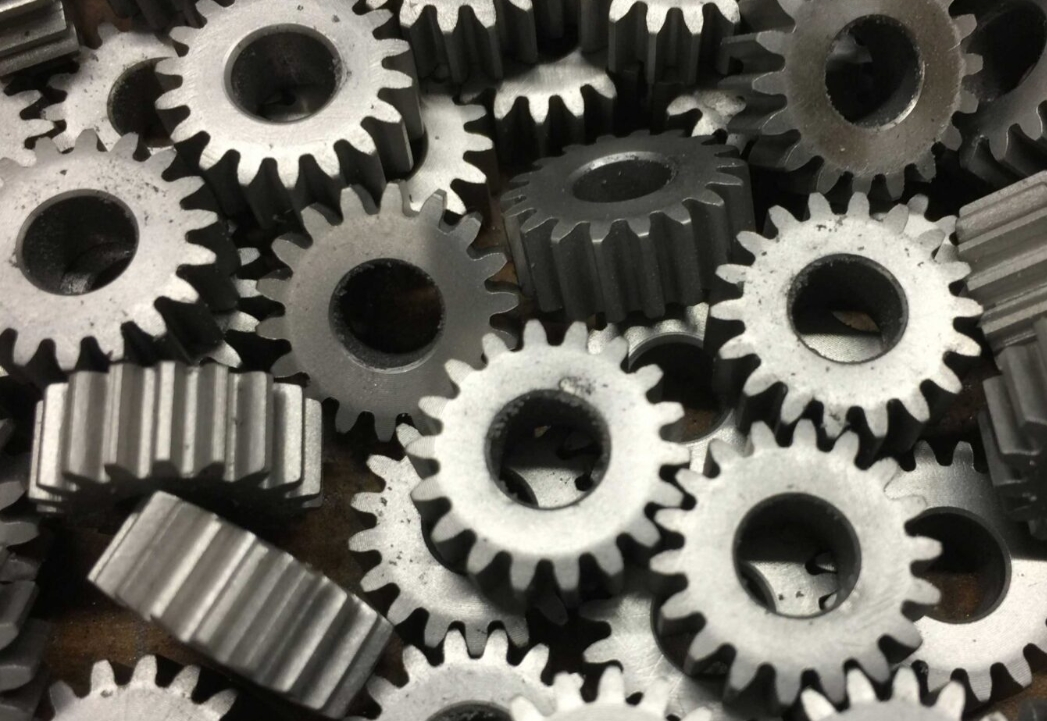
Phosphorus-Based Extreme Pressure Anti-Wear Additives- Core Technology and Application Analysis
Phosphorus-Based Extreme Pressure Anti-Wear Additives: Core Technology and Application Analysis for High-Performance Lubrication
In the field of lubricant additives, phosphorus-based extreme pressure (EP) anti-wear additives have become an indispensable core component of industrial lubrication technology due to their unique anti-wear properties and wide range of applications. As mechanical equipment evolves towards higher load, higher precision, and more demanding operational conditions, the requirements for extreme pressure anti-wear performance in lubricants are becoming increasingly stringent.
What is an Extreme Pressure Anti-Wear Additive?
Extreme pressure (EP) anti-wear additives are chemical substances specifically added to lubricants to effectively prevent direct metal-to-metal contact under high temperature, high pressure, and heavy load conditions, thereby reducing friction and wear. The primary function of these additives is to enhance the load-carrying capacity of lubricants under extreme conditions, protect metal surfaces from wear and corrosion, and extend the service life of mechanical equipment.
Mechanism of Phosphorus-Based Extreme Pressure Anti-Wear Additives
Phosphorus-based extreme pressure anti-wear additives work through chemical adsorption and tribochemical reactions to form a high-strength protective film on metal surfaces, reducing friction and wear while preventing scuffing. The process can be divided into three stages:
1. Adsorption Stage: Phosphorus compounds preferentially adsorb onto the metal surface, forming an initial protective layer.
2. Hydrolysis Reaction: Under high temperature and pressure conditions, phosphoric esters hydrolyze to generate acidic phosphoric esters, which further react with metals to form organic metal phosphate films.
3. Extreme Pressure Film Formation: Under extreme pressure, inorganic phosphorous metal films are formed, significantly enhancing the load-carrying capacity of the lubricant.
Working Principle of Extreme Pressure Anti-Wear Additives
Extreme pressure anti-wear additives in lubricants work by forming a high-strength protective film on metal surfaces. This protective film, under high pressure, low speed, or high load conditions, effectively prevents direct metal-to-metal contact, avoiding heat generation, wear, and material loss caused by friction. The additives chemically bond with the metal surface, creating a durable, wear-resistant composite film that enhances the extreme pressure performance of the lubricant.
Key Characteristics of Phosphorus-Based Extreme Pressure Anti-Wear Additives
1. High Anti-Wear Performance
Phosphorus-based additives perform exceptionally well in moderate to low-pressure boundary lubrication environments.
2. Thermal and Hydrolytic Stability
Phosphoric esters maintain chemical stability at high temperatures, making them suitable for high-temperature applications such as engine oils and compressor oils.
3. Environmental Compatibility
Phosphorus-based additives, such as amine-neutralized phosphates, avoid metal residue issues and meet the modern lubricant trend towards low ash content.
4. Multi-Effect Synergy
Phosphorus-based additives are often blended with elements like sulfur and zinc to enhance the performance of individual components. For example, phosphorus anti-wear agents used in conjunction with sulfur compounds provide both anti-wear and extreme pressure properties.
Core Application Areas of Phosphorus-Based Extreme Pressure Anti-Wear Additives
1. Industrial Gear Oils
Phosphorus-based additives excel in heavy-duty gear oils. Designed for industrial gear oils, they can withstand extreme pressures and extend equipment lifespan.
2. Metalworking Fluids
In water-based or oil-based metalworking fluids, phosphorus-based additives provide efficient lubrication and cooling during processes such as cutting and drawing.
3. Anti-Wear Hydraulic Oils
Amine-neutralized phosphoric esters offer long-lasting anti-wear protection in hydraulic systems while preventing sludge formation and maintaining system cleanliness.
Key Considerations for Selecting Extreme Pressure Anti-Wear Additives
When selecting extreme pressure anti-wear additives for lubricants, it is recommended to choose additives based on the specific operational environment and load requirements of the equipment. For high-load equipment, heavy-duty trucks, and construction machinery in demanding conditions, higher-performance EP anti-wear additives are needed to ensure optimal protection.
Why choose UNPChemicals extreme pressure anti-wear additives for lubricating oil?
UNPChemicals, aka Luoyang Pacific United Petrochemical Co., Ltd., focuses on the application and development of special lubricating grease additives such as MODTC, MODTP, molybdenum amide, thiadiazole metal deactivators, and phosphate esters.EP/AW additives With nearly 30 products in seven series, including extreme pressure anti-wear agents and special grease additives, it is a global manufacturer of special lubricating grease additives and a national high-tech enterprise with great influence and leading role in the industry.
As a leader in the field of lubricating oil additives, we are committed to the development of highly efficient and environmentally friendly extreme pressure anti-wear agents for lubricating oil. We combine advanced technology and years of industry experience to provide extreme pressure antiwear agents that can maintain stable performance under the most demanding working conditions, helping customers reduce equipment maintenance costs, improve equipment operation efficiency, and help enterprises achieve higher economic benefits.
If you are looking for EP/AW additives or technical information, feel free to contact UNPChemicals.