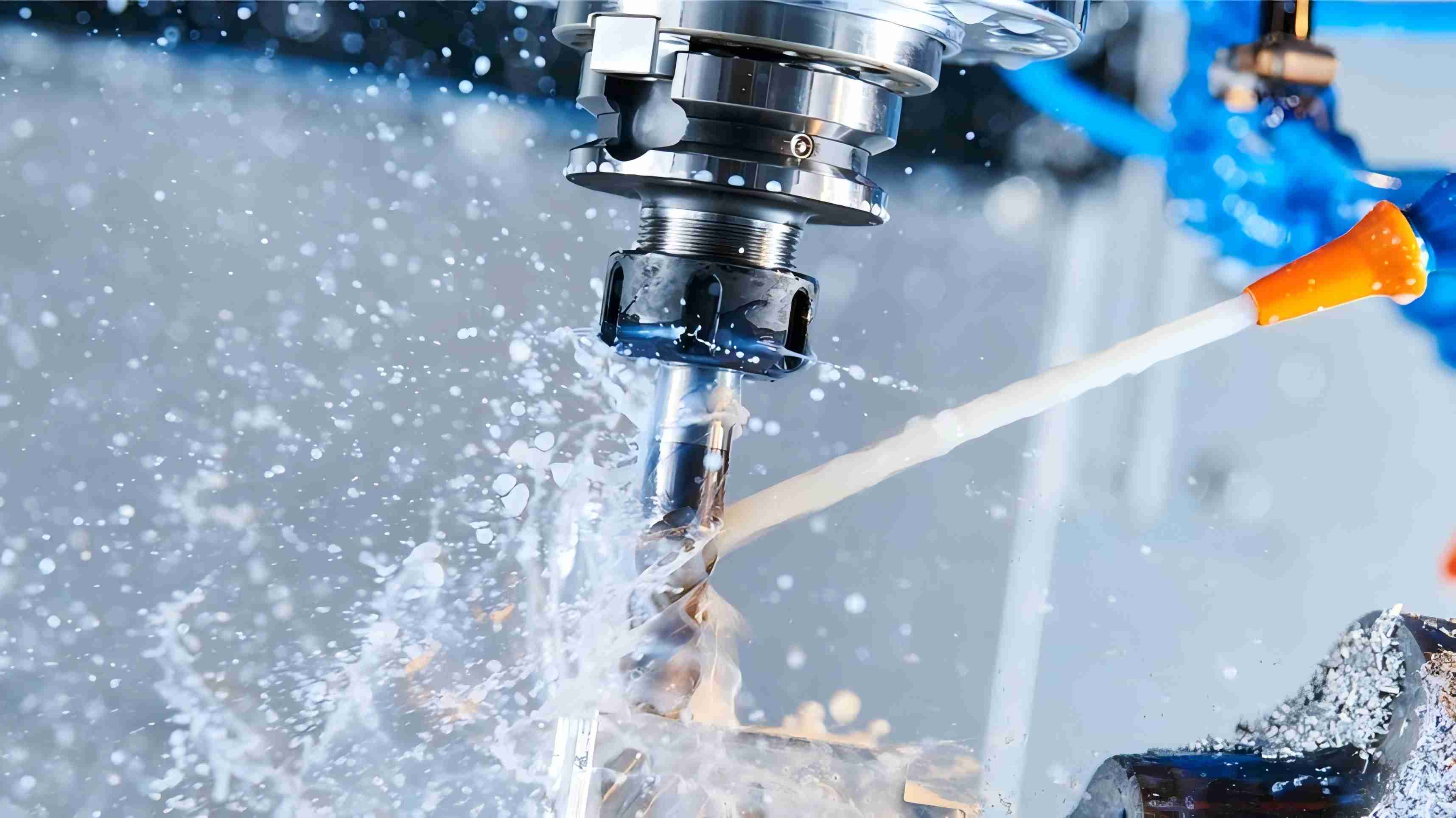
Phosphorus - based Lubricant Additives: Performance, Types and Applications
In the modern industrial system, lubricant additives play a pivotal role as key components for enhancing the performance of lubricants and meeting the complex operating conditions of various mechanical equipment. Among them, phosphorus - based lubricant additives occupy an indispensable position in the lubricant field due to their unique chemical structures and diverse performance characteristics.
Types and Characteristics of Phosphorus - based Lubricant Additives
Acidic Phosphite and Its Derivative Additives
The earliest phosphorus - containing additive used in gear oils is acidic phosphite, with acidic di - n - butyl phosphite being a typical representative. This type of additive has excellent extreme - pressure and anti - wear properties, which can play a key role on the metal friction surface and effectively reduce wear. However, its hydrolytic stability and thermal oxidation stability are poor, and its performance is prone to degradation under harsh environments such as high temperatures and humidity.
To overcome these drawbacks, a series of structural optimization designs have been carried out based on acidic phosphite, resulting in the derivation of various additives with better performance:
-Long - chain Acidic Phosphite: By increasing the alkyl carbon chain of acidic phosphite, its hydrolytic stability and thermal oxidation stability can be significantly improved. The long - chain structure increases the steric hindrance of the molecule, reduces the active sites of hydrolysis and oxidation reactions, and thus enhances the stability of the additive in complex environments.
-Neutral Phosphite: Obtained by further esterifying acidic phosphite, although there is a slight sacrifice in extreme - pressure performance, its hydrolytic stability and thermal oxidation stability have been greatly improved. This characteristic makes neutral phosphite advantageous in lubrication scenarios with high requirements for stability.
-Sulfurized (Phosphite): Sulfurizing (phosphite) can effectively improve its extreme - pressure and anti - wear properties. The sulfurization process introduces sulfur - containing active groups, which can undergo chemical reactions on the friction surface to form a more tenacious protective film, enhancing the performance of the additive under high - load working conditions.
-Amidated (Phosphite) and Acidic Thiophosphate: After amidation of acidic (phosphite) and acidic thiophosphate, their hydrolytic stability and thermal oxidation stability are improved to a certain extent. The introduction of amino groups changes the electron - cloud distribution of the molecule and enhances the molecule's resistance to hydrolysis and oxidation.
-Re-esterified (Phosphite) and Acidic Thiophosphate: The re - esterification reaction can significantly improve the hydrolytic stability and thermal oxidation stability of phosphorus - containing additives. Through the construction of the re - ester structure, the stability of the molecule is enhanced, enabling it to maintain good performance under various working conditions.
-Acidic Phosphonate: Acidic phosphite is pyrolyzed to form acidic phosphonate, and its extreme - pressure performance is significantly improved. After further amidation treatment of acidic phosphonate, its hydrolytic stability and thermal oxidation stability are further improved, enabling it to play a good role in various lubrication scenarios.
Other Common Phosphorus - based Additives
-Phosphate Ester: Among phosphate esters, tricresyl phosphate is widely used and has a history of more than forty years. It has good anti - wear properties and low corrosiveness and is often used in fields with extremely high requirements for lubrication performance, such as aviation engine oils and anti - wear hydraulic oils. In the high - temperature and high - load working environment of aviation engines, tricresyl phosphate can provide reliable lubrication protection for engine components and ensure the stable operation of the engine.
-Acidic Phosphate Ester: Such as 2 - dodecyl acidic phosphate ester and 2 - octadecyl acidic phosphate ester, etc., are significantly superior to tricresyl phosphate and can greatly improve the extreme - pressure or anti - wear properties of base oils. Acidic phosphate esters have strong adsorption ability and high reactivity on the metal surface, which makes them perform outstandingly in anti - seizure load. However, it should be noted that acidic phosphate esters may trigger corrosion reactions, leading to increased wear on the metal surface. In practical applications, their dosage and usage conditions need to be carefully controlled.
-Acidic Phosphate Ester Amine Salt (Phosphorus - Nitrogen Agent): This type of additive is prepared by reacting a suitable acidic phosphate ester with a corresponding nitrogen - containing compound. Representative products include acidic phosphate dodecylamine salt and octadecylamine salt. It not only has excellent extreme - pressure and anti - wear properties but also has good corrosion resistance, rust prevention, and oxidation resistance. In practical applications, acidic phosphate ester amine salts can provide comprehensive lubrication protection for mechanical equipment and extend the service life of the equipment.
-Thiophosphate Ester Amine Salt (Sulfur - Phosphorus - Nitrogen Agent): It includes dialkyl dithiophosphate ester amine salt and dialkyl dithiophosphate re - ester amine salt. Dialkyl dithiophosphate ester amine salt has multiple properties such as extreme - pressure, anti - wear, anti - oxidation, and rust prevention; dialkyl dithiophosphate re - ester amine salt undergoes secondary phosphorylation during the preparation process, has a higher sulfur - phosphorus ratio, and has more excellent extreme - pressure and anti - wear properties, thermal stability, and rust - prevention properties, and is widely used in various gear oils. In the lubrication of vehicle gearboxes, dialkyl dithiophosphate re - ester amine salt can effectively resist the wear caused by high loads and high - speed operation between gears and ensure the normal operation of the gearbox.
-Boron - Phosphorus - Nitrogen Anti - wear Agent: In recent years, research has shown that the introduction of boron elements into anti - wear agents has a significant effect. This type of additive has good oil solubility, corrosion resistance, and extreme - pressure and anti - wear properties. The phosphorus element can be derived from organic or inorganic acids, and the boron element is derived from boric acid or organic borate esters. The synergistic effect of phosphorus and boron further enhances the anti - wear performance of the additive, and it has broad application prospects in fields such as metal cutting fluids.
Functions and Mechanisms of Phosphorus - based Lubricant Additives
Diversity of Action Mechanisms
The action mechanisms of phosphorus - containing compounds are extremely complex, and there are currently multiple viewpoints:
-Traditional Chemical Polishing Theory: The traditional view holds that phosphorus - containing compounds decompose under the instantaneous high temperature at the convex points of the friction surface, react chemically with iron to form iron phosphide, and iron phosphide forms a eutectic alloy with a low melting point with iron. These eutectic alloys flow to the concave parts, making the friction surface smooth and thus preventing wear. This process is called chemical polishing.
-Film - forming Theory under Boundary and Extreme - pressure Conditions: Under boundary lubrication conditions, phosphides are first adsorbed on the iron surface, and then the C - O bond breaks to form an organo - iron phosphite or iron phosphate film, which plays an anti - wear role; under extreme - pressure conditions, the organo - iron phosphate film further reacts to form an inorganic iron phosphate reaction film, effectively preventing direct contact between metals and thus playing an extreme - pressure protection role.
-Relationship between Hydrolytic Stability and Extreme - pressure Anti - wear Properties: Some believe that the extreme - pressure and anti - wear properties of phosphorus - based extreme - pressure and anti - wear agents are closely related to their hydrolytic stability. Generally, those with good anti - hydrolysis performance have relatively poor extreme - pressure properties. Among phosphorus - based extreme - pressure and anti - wear agents, hypophosphite esters and phosphonate esters have the worst extreme - pressure properties because the C - P bond of hypophosphite esters and phosphonate esters is more stable than the C - O - P bond of phosphate esters. Among phosphate esters, acidic phosphate esters have better anti - seizure performance than neutral phosphate esters due to their strong adsorption force and high reactivity on the metal surface. Overall, the order of extreme - pressure performance is: phosphate ester amine salt > phosphate amide > phosphite > acidic phosphate ester > phosphate ester > phosphonate ester > hypophosphite ester.
Factors Affecting Performance
-Material and Catalytic Effect: The formation rates of lubricating films formed by phosphorus - containing additives on different material surfaces are significantly different. In the high - temperature vaporization dissociation test at 500 - 800°C, the adsorption film on the iron surface grows faster, and the film is thicker than that on nickel and quartz surfaces. This is because iron and iron oxide play a catalytic effect in the film - formation process.
-Relationship between Thermal Stability and Anti - wear Properties: There is a subtle relationship between the thermal stability and anti - wear properties of phosphorus - based extreme - pressure and anti - wear agents. Generally, the worse the thermal stability, the better the anti - wear properties, but the durability of anti - wear will decline, and the consumption rate of the additive will also accelerate. Thermal stability mainly depends on the alkyl structure in the molecule. Aryl groups have the best thermal stability, followed by secondary and primary alkyl groups. When there are multiple substituents on the β - carbon of the alkyl group, its thermal stability increases.
-Synergistic Effect: Usually, phosphorus - containing agents are used in combination with sulfur - containing agents because sulfur - containing agents can effectively improve the strength and toughness of the formed lubricating film. Through their synergistic effect, the comprehensive performance of lubricants under complex working conditions is improved.
Applications and Characteristics of Phosphate Esters in the Metal Processing Industry
Basic Characteristics
In the metal processing field, lubrication and cooling play a key role in improving processing efficiency and ensuring product quality. With the continuous progress of industrial technology, the performance requirements for metal processing fluids are becoming increasingly stringent. Phosphate ester extreme - pressure agents, as a new type of additive, have been widely used in metal processing fluids due to their unique performance advantages.
-Excellent Extreme - pressure Performance: Phosphate esters can form a firm lubricating film on the metal surface, which can effectively prevent direct contact and wear between metals. Even under harsh processing conditions such as high loads and high speeds, they can provide reliable lubrication protection for metal processing.
-Good Water - solubility and Stability: Phosphate esters have good water - solubility and can fully integrate with other components in metal processing fluids to form a uniform and stable lubrication system. This characteristic ensures the stability of metal processing fluids during storage and use and avoids performance degradation caused by component separation.
Application Advantages
-Improve Processing Efficiency: Phosphate ester extreme - pressure agents can effectively reduce the friction coefficient during metal processing, reduce cutting force and cutting heat. This not only reduces tool wear but also improves cutting speed and processing accuracy. At the same time, the existence of the lubricating film helps to dissipate the heat generated during the processing process in a timely manner, avoiding workpiece deformation or cracking due to overheating, thereby improving processing efficiency and product quality.
-Protect Machine Tools and Tools: The lubricating film formed by it can isolate the metal surface from contact with the external environment such as air and moisture, preventing machine tools and tools from corrosion and oxidation. In addition, phosphate ester extreme - pressure agents can effectively prevent metal chips from adhering to the tool during the cutting process, reduce the difficulty of tool cleaning, extend the service life of the tool, and reduce the costs of tool replacement and machine - tool maintenance.
-Environmental Protection and Energy Conservation: Compared with traditional oily metal processing fluids, phosphate ester extreme - pressure agents have better environmental performance. They do not contain oil components, produce less waste during use, and are easy to handle. At the same time, due to their excellent extreme - pressure performance, the amount and replacement frequency of cutting fluids can be reduced, reducing production costs and energy consumption, which meets the requirements of modern industry for environmental protection and energy conservation.
-Strong Adaptability: Phosphate ester extreme - pressure agents are suitable for the processing of various metal materials, including stainless steel, alloy steel, cast iron, etc. At the same time, they are also suitable for different processing methods and processing conditions, such as turning, milling, grinding, etc. This wide adaptability makes phosphate ester extreme - pressure agents have broad application prospects in the metal processing field and can meet the processing needs of different industries and different processes.
Phosphorus - based lubricant additives play a crucial role in modern industrial lubrication with their rich and diverse types, unique action mechanisms, and wide application fields. Especially the application of phosphate esters in the metal processing industry provides strong support for improving metal processing efficiency, ensuring product quality, and achieving environmental protection and energy - saving goals. With the continuous development of materials science and industrial technology, the performance of phosphorus - based lubricant additives will be continuously optimized, and their application fields will be further expanded, making greater contributions to promoting industrial progress.
The Price of Lubricant Additives
The price of Lubricant Additives depending on factors such as brand, specification, composition, and sales channels. If you are interested in Lubricant Additives, please feel free to contact us.
Supplier of Lubricant Additives
UNPChemicals is a professional supplier of high-quality and effective Lubricant Additives. We offer several remarkable products, namely Amine-neutralized mixed phosphate esters PSAIL 2280,Amine-neutralized hexyl phosphate PSAIL 3490,Phosphorothioate Acrylate Derivatives PSAIL 3530,etc.
Amine-neutralized mixed phosphate esters PSAIL 2280 is a multifunctional ashless additive structured as a phosphate ester amine salt with excellent load carrying capacity, anti-wear and corrosion protection properties. As a multifunctional additive, PSAIL 2280 reduces the amount of anti-emulsifier and rust inhibitor and has good tribological properties, especially at higher temperatures, forming thicker boundary lubricant films. In addition, PSAIL2280 is widely used in metalworking fluid formulations in conjunction with sulfur carriers because of its good anti-wear properties.
Amine-neutralized hexyl phosphate PSAIL 3490 is a specialized mixture of amine phosphate salts known for its multifunctional ashless additive characteristics. As an ashless additive, PSAIL 3490 does not produce ash as combustion by-products, reducing engine deposits and harmful emissions. PSAIL 3490 is a multifunctional additive, providing a range of benefits in a single product, making it highly versatile and cost-effective.
Phosphorothioate Acrylate Derivatives PSAIL 3530 is an ashless EP/AW additive with dialkyl dithiophosphate structure, especially suitable for industrial lubricating oils with FZG test requirements, such as industrial gear oil, anti-wear hydraulic oil containing ZDDP, lubricating grease and metal processing oil.
Professional Lubricant Additive Manufacturer
UNPChemicals, aka Luoyang Pacific United Petrochemical Co., Ltd., focuses on the application and development of special lubricating grease additives such as MODTC, MODTP, molybdenum amide, thiadiazole metal deactivators, and phosphate esters. With nearly 30 products in seven series, including extreme pressure anti-wear additives and special grease additives, it is a global manufacturer of special lubricating grease additives and a national high-tech enterprise with great influence and leading role in the industry. If you are looking for Lubricant Additive or technical information, feel free to contact UNPChemicals.