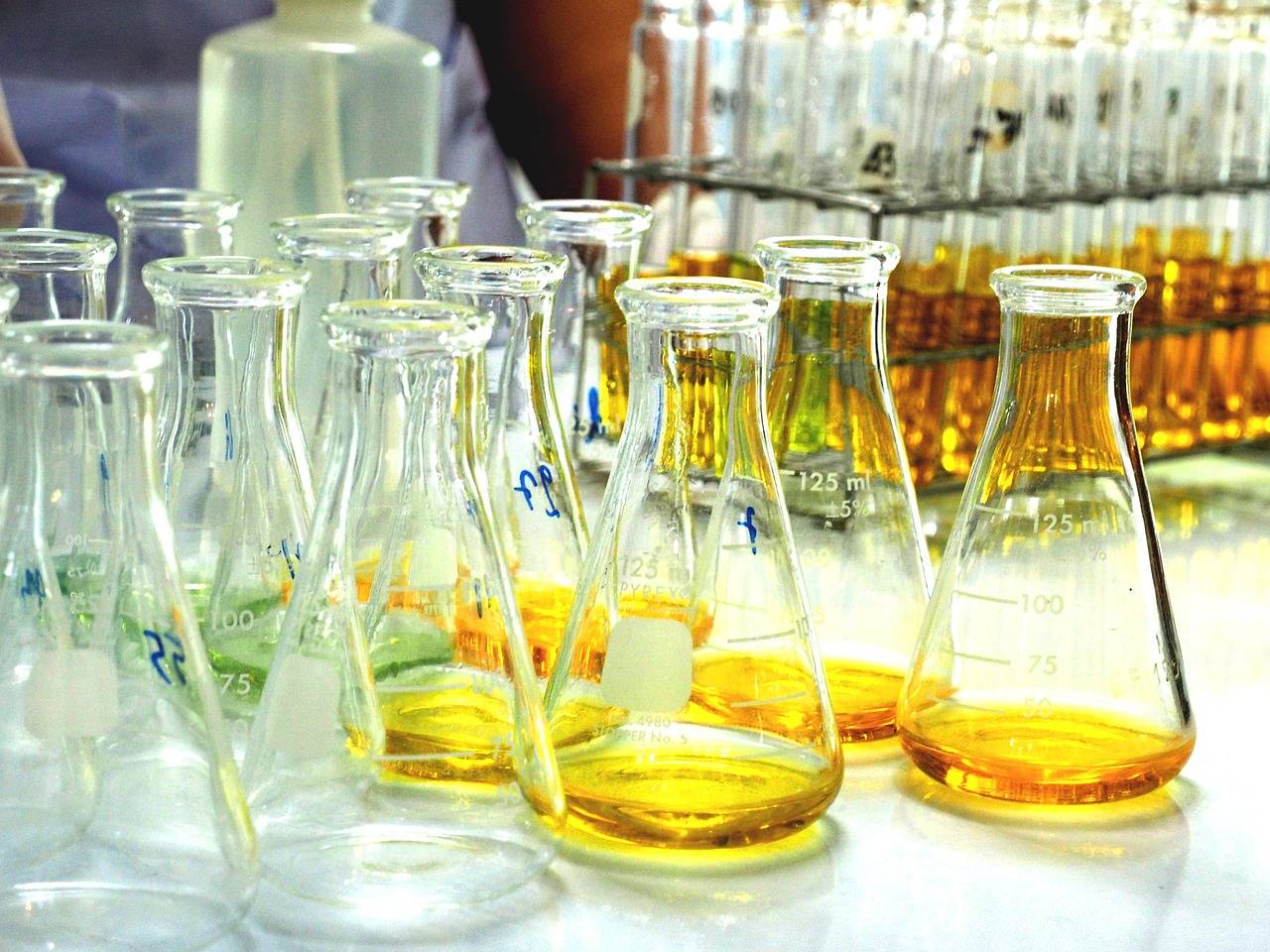
Performance Evaluation of Anti-wear Hydraulic Oil Additive Concentrates
Anti-wear hydraulic oil additive concentrates are a crucial component of hydraulic systems. The quality of their performance is directly related to the operational stability, reliability, and service life of hydraulic equipment. Conducting a comprehensive, scientific, and accurate performance evaluation is the core link to ensure that product quality meets the usage requirements and to achieve effective quality control. In the field of industrial production, numerous pieces of equipment highly rely on hydraulic systems for power transmission and control. From the excavation operations of construction machinery to the precision machining of machine tools, from the operation of large rolling mills in the metallurgical industry to the hydraulic propulsion systems of ships, even the slightest difference in the performance of anti-wear hydraulic oil additive concentrates may trigger operational failures of the equipment. This, in turn, can affect production efficiency, increase maintenance costs, and even pose potential safety hazards. Therefore, establishing a complete and scientific performance evaluation system is of inestimable significance for ensuring product quality and promoting the healthy development of the industry.
Test Methods for the Anti-wear Performance of Anti-wear Hydraulic Oil Additive Concentrates
The four-ball test is a widely used method for testing the anti-wear performance. Its basic principle is to simulate the friction environment under actual working conditions. Four steel balls are placed in a specific test device. Three of the steel balls are fixed in an oil box in an equilateral triangle arrangement, and the other steel ball is installed on a rotatable main shaft, maintaining point contact with the three steel balls below. During the test, the main shaft drives the upper steel ball to rotate at a high speed, and a certain load is applied to it, causing relative motion and friction between the steel balls. At this time, the anti-wear hydraulic oil additive concentrate forms an oil film between the steel balls, providing lubrication and protection.
During the test, different test conditions are usually set, such as different loads, rotational speeds, and test durations. The anti-wear performance of the anti-wear hydraulic oil additive concentrate is evaluated by observing and measuring parameters such as the wear scar diameter and wear volume of the steel balls after the test. The smaller the wear scar diameter, the stronger the load-bearing capacity of the oil film formed by the anti-wear hydraulic oil additive concentrate on the surface of the steel balls, which can effectively resist friction and wear and protect the metal surface. The wear volume, on the other hand, reflects the degree of wear from another perspective. The smaller the wear volume, the better the anti-wear effect of the anti-wear hydraulic oil additive concentrate.
The four-ball test has advantages such as relatively simple operation, a short test cycle, and intuitive test results. It can quickly screen and compare anti-wear hydraulic oil additive concentrates with different formulations, providing important data support for product research and development and quality control. However, this method also has certain limitations. It is only a simulation test, and there are differences between it and the complex working conditions in actual hydraulic systems. It cannot fully and realistically reflect the anti-wear performance of anti-wear hydraulic oil additive concentrates in actual use.
Test Methods for the Antioxidant Performance of Anti-wear Hydraulic Oil Additive Concentrates
The rotating pressure vessel oxidation test (RPVOT), also known as the rotating oxygen bomb method, is a commonly used means to evaluate the antioxidant performance of anti-wear hydraulic oil additive concentrates. The antioxidant performance is of vital importance for anti-wear hydraulic oil additive concentrates because during the operation of the hydraulic system, the oil will come into contact with oxygen in the air and is prone to oxidation reactions due to factors such as high temperature and metal catalysis. Oxidation reactions will cause the oil to deteriorate, generating acidic substances, gums, and precipitates, etc. This not only reduces the lubricating performance of the oil but also corrodes the metal components in the hydraulic system, shortening the service life of the equipment.
The test principle of the rotating oxygen bomb method is based on the characteristic that the oil reacts with oxygen under high temperature and high pressure. During the test, a certain amount of anti-wear hydraulic oil additive concentrate sample is filled into a specially designed oxygen bomb. The oxygen bomb is filled with oxygen at a certain pressure, and then the oxygen bomb is placed in an oil bath at a specified temperature and rotated at a certain rotational speed. During the rotation, the oil comes into full contact with oxygen, accelerating the progress of the oxidation reaction. As the oxidation reaction continues, the pressure inside the oxygen bomb gradually decreases. When the pressure drops to a specified value, the test time at this moment is recorded, and this time is the oxidation induction period.
The longer the oxidation induction period, the better the antioxidant performance of the anti-wear hydraulic oil additive concentrate, indicating that it can resist oxidation for a longer time and maintain the stability and performance of the oil. The rotating oxygen bomb method can quickly evaluate the antioxidant performance of anti-wear hydraulic oil additive concentrates under high temperature and high pressure conditions. The test results have good repeatability and comparability, providing important bases for product formulation optimization and service life prediction. However, this method also has certain limitations. The working conditions in actual hydraulic systems are complex and variable, and there are differences between them and the test conditions set by the rotating oxygen bomb method. Therefore, when applying the test results, a comprehensive analysis needs to be carried out in combination with the actual situation.
Test Methods for the Demulsibility Performance of Anti-wear Hydraulic Oil Additive Concentrates
The demulsibility performance is an important indicator for measuring whether the anti-wear hydraulic oil additive concentrate can quickly separate water from the oil when water is mixed in, maintaining the cleanliness and lubricating performance of the oil. In actual hydraulic systems, due to the complex operating environment of the equipment, water may mix into the oil through various channels, such as rainwater intrusion and leakage of the equipment cooling system. If the demulsibility performance of the anti-wear hydraulic oil additive concentrate is not good, water will mix with the oil to form an emulsion, which will reduce the lubricating performance of the oil, accelerate equipment wear, and may also cause corrosion of metal components.
The common test method for demulsibility performance is carried out in accordance with relevant standards, such as GB/T 7305 "Determination of Water Separation Characteristics of Petroleum and Synthetic Fluids". The test process of this method is as follows: After mixing a certain amount of anti-wear hydraulic oil additive concentrate sample with distilled water, it is filled into a specific glass measuring cylinder. Then, the measuring cylinder is placed in a constant temperature water bath at a specified temperature and stirred at a certain rotational speed for a certain period of time to fully mix the oil and water to form an emulsion. After stopping the stirring, record the time required for the oil layer, water layer, and emulsion layer to separate to a certain volume ratio.
According to the standard regulations, different types of anti-wear hydraulic oil additive concentrates have corresponding demulsibility performance index requirements. Generally speaking, if the oil and water can be quickly separated within the specified time and the volume of the emulsion layer is small, it indicates that the demulsibility performance of the anti-wear hydraulic oil additive concentrate is good. An anti-wear hydraulic oil additive concentrate with good demulsibility performance can effectively separate the mixed-in water, maintain the normal performance of the oil, and ensure that the hydraulic system can still operate stably in a humid environment or when water intrudes.
Evaluation Methods for Other Properties of Anti-wear Hydraulic Oil Additive Concentrates
The viscosity index is an important parameter for measuring the characteristic of how the viscosity of the anti-wear hydraulic oil additive concentrate changes with temperature. In hydraulic systems, the temperature can change significantly under different working conditions. If the viscosity index of the anti-wear hydraulic oil additive concentrate is too low, its viscosity will decrease significantly as the temperature rises or increase substantially as the temperature drops, which will affect the normal operation of the hydraulic system. For example, too low a viscosity may lead to increased leakage and reduced lubricating performance; too high a viscosity will make it difficult for the hydraulic pump to start and increase power loss.
The commonly used method for evaluating the viscosity index is to measure the kinematic viscosity of the anti-wear hydraulic oil additive concentrate at different temperatures and then calculate the viscosity index according to the relevant formula. Generally, the kinematic viscosity of the oil at 40°C and 100°C is measured, and the formula specified in standards such as ASTM D2270 is used for calculation. The higher the viscosity index, the smaller the change in the viscosity of the anti-wear hydraulic oil additive concentrate with temperature, and the better its viscosity-temperature performance. It can maintain an appropriate viscosity within a wider temperature range to meet the working requirements of the hydraulic system under different working conditions.
In addition to the viscosity index, other properties of the anti-wear hydraulic oil additive concentrate, such as foaming characteristics, rust prevention performance, and hydrolytic stability, also need to be evaluated accordingly. The foaming characteristics can be determined through foaming tendency and foam stability tests, the rust prevention performance can be evaluated by using a corrosion test, and the hydrolytic stability can be investigated through a hydrolysis test. These performance indicators are interrelated and jointly affect the overall performance of the anti-wear hydraulic oil additive concentrate and its application effect in the hydraulic system.
In conclusion, the performance evaluation of anti-wear hydraulic oil additive concentrates covers the testing and evaluation of many important performance indicators, including anti-wear performance, antioxidant performance, demulsibility performance, viscosity index, and other properties. The test methods used, such as the four-ball test, the rotating oxygen bomb method, the demulsibility performance test, and the viscosity index calculation, quantify and analyze the performance of the additive concentrates from different angles, providing comprehensive and scientific data support for product quality control.
These performance evaluation methods have a high degree of scientificity. Based on rigorous test principles and standardized operation procedures, they can relatively accurately simulate the working environment and working conditions of anti-wear hydraulic oil additive concentrates in actual hydraulic systems, thereby effectively evaluating their various performances. At the same time, these methods also have strong practicality. Whether it is in the product research and development stage for screening and optimizing formulations, in the production process for quality inspection and control, or in the product use process for monitoring and evaluating performance, they all play an indispensable role.
However, we should also clearly recognize that the existing performance evaluation methods are not perfect. There is still a certain gap compared with the complex and variable working conditions in actual hydraulic systems. Therefore, in practical applications, it is necessary to comprehensively consider various factors in combination with the actual usage situation and conduct a reasonable analysis and judgment on the performance evaluation results. At the same time, with the continuous progress of science and technology and the increasing demand of the industry, it is also necessary to continuously conduct in-depth research and improvement on the performance evaluation methods to make them closer to the actual working conditions, more accurately and comprehensively reflect the performance of anti-wear hydraulic oil additive concentrates, and provide more powerful guarantees for the stable operation of hydraulic equipment and the efficient development of industrial production.
The Price of Hydraulic Oil Additives Package
The price of Hydraulic Oil Additives Package varies depending on factors such as brand, specification, composition, and sales channels. If you are interested in Hydraulic Oil Additives Package, please feel free to contact us.
Supplier of Hydraulic Oil Additives Package
UNPChemicals is a professional supplier of high-quality and effective Hydraulic Oil Additives Package. We offer several remarkable products, namely High zinc hydraulic oil additives UNP AH502A,Low Zinc Hydraulic Oil Additives UNP AH502B,Zinc-free Hydraulic Oil Additives UNP AH502C,etc.
High zinc hydraulic oil additives UNP AH502A are a type of chemical additive used in hydraulic oils that contain high levels of zinc dialkyldithiophosphate (ZDDP). ZDDP is a well-known anti-wear agent that also provides antioxidant, anti-corrosion, and anti-foam properties. The zinc in these additives plays a crucial role in forming a protective film on metal surfaces within the hydraulic system, thereby reducing wear and extending the life of the system components.
Low Zinc Hydraulic Oil Additives UNP AH502B are a class of advanced lubricant additives designed to enhance the performance of hydraulic oils with reduced zinc content.These additives are formulated to provide a balance of anti-wear,extreme pressure,and antioxidant properties,making them suitable for modern hydraulic systems that demand high performance with lower environmental impact.
Zinc-free Hydraulic Oil Additives UNP AH502C are a new class of environmentally friendly lubricant additives designed for hydraulic systems.These additives are formulated to provide the same level of performance as traditional zinc-containing additives but without the heavy metal content,reducing the environmental impact of hydraulic fluids.
Professional Lubricant Additive Manufacturer
UNPChemicals,aka Luoyang Pacific United Petrochemical Co., Ltd., focuses on the application and development of special lubricating grease additives such as MODTC, MODTP, molybdenum amide, thiadiazole metal deactivators, and phosphate esters. With nearly 30 products in seven series, including extreme pressure anti-wear additives and special grease additives, it is a global manufacturer of special lubricating grease additives and a national high-tech enterprise with great influence and leading role in the industry. If you are looking for Lubricant Additive or technical information, feel free to contact UNPChemicals.