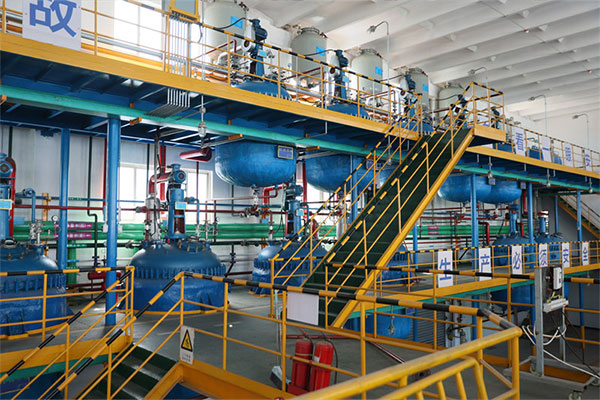
Manufacturing Process of Industrial Lubricant Additive Packages
Introduction
Industrial Lubricant Additive Packages are a critical component in lubricant formulations, designed to enhance oxidation resistance, wear protection, corrosion inhibition, and other performance aspects. As industrial equipment demands increasingly advanced lubricant performance, the quality and production process of additive packages have become a focal point in the industry. As a professional manufacturer of lubricant additives and additive packages, UNPChemicals is committed to delivering high-quality solutions tailored for various industrial applications. This article explores the manufacturing process of Industrial Lubricant Additive Packages and highlights the key steps that determine their quality and performance.
Raw Material Selection
The production of additive packages begins with rigorous raw material selection. High-quality raw materials are the foundation for stable and effective additive performance. Commonly used components include:
Antioxidants: Such as phenolic and amine-based antioxidants to suppress oil oxidation.
Anti-wear and extreme pressure agents: Including sulfur-phosphorus compounds to enhance wear and load-bearing properties.
Detergents and dispersants: To keep oil systems clean and prevent sludge formation.
Rust and corrosion inhibitors: Such as phosphate esters and borate esters to protect metal surfaces.
Friction modifiers: To improve friction behavior and reduce energy loss and heat buildup.
Purity and compatibility of raw materials directly affect the stability and performance of the final product. UNPChemicals uses internationally certified raw materials and strictly controls sourcing and quality.
Formulation Design and Optimization
Formulation design is at the heart of additive package production. Creating a high-performance formulation requires careful consideration of the compatibility and synergistic effects between different functional additives.
Proportioning: Laboratory studies help determine the optimal ratio of each component to ensure complementary effects among additives.
Performance tuning: Small-scale and pilot testing are conducted to validate performance in various base oils and applications.
Computer simulation: Modeling software may be used to simulate chemical interactions and predict physical properties, improving formulation accuracy and efficiency.
Pre-mixing and Dosing
Once raw materials are ready, they undergo precise dosing and pre-mixing.
Accurate weighing: Ingredients are measured strictly according to the formula.
Uniform pre-mixing: All additives are blended in pre-mix tanks to ensure even dispersion.
Dissolution or heating: Some high-viscosity or solid additives require heating or dilution to ensure smooth integration during final blending.
Blending and Homogenization
The pre-mixed components are transferred into high-shear mixers or reactors for full-scale blending and homogenization.
Temperature control: Each additive has a preferred operating temperature, usually between 40°C and 80°C to maintain stability and effectiveness.
High-speed mixing: Ensures that all additives are thoroughly dispersed in a short time.
Homogenization: Used to prevent particle separation or stratification, ensuring physical stability of the finished package.
Quality Control and Testing
Rigorous quality testing is essential for ensuring that the final product meets industry standards and customer requirements.
Physical tests: Viscosity, density, flash point, pour point, etc.
Chemical analysis: Acid number, base number, metal content, and active ingredient concentration.
Performance tests: Oxidation resistance, wear protection, foam control, and thermal stability.
Compatibility tests: Evaluate how the additive package interacts with various base oils to ensure no precipitation or gel formation occurs.
UNPChemicals applies advanced automated testing equipment and strict quality control protocols to ensure that every batch meets both regulatory and performance expectations.
Filtration and Packaging
Once the additive package passes inspection, it undergoes final filtration and packaging.
Fine filtration: Removes micro-particles and impurities introduced during mixing.
Aseptic filling: Filling is done in closed systems to prevent contamination.
Sealed packaging and labeling: Drums or containers are tightly sealed and labeled with batch numbers, production dates, and usage instructions to ensure traceability.
Storage and Logistics
Proper storage and transportation are essential to preserve product quality.
Storage conditions: Cool, dry, and dark environments help maintain stability and prevent degradation.
Transport safety: Packaging and shipping follow chemical transport regulations to prevent leaks or contamination during long-distance delivery.
Conclusion
The manufacturing of Industrial Lubricant Additive Packages involves a complex and tightly controlled process, with each step critical to ensuring high quality and performance. As a professional producer in this field, UNPChemicals utilizes advanced technology and stringent quality management systems to deliver reliable, high-performance additive packages that support long-term equipment operation and protection. For more information or customized solutions, feel free to contact us.