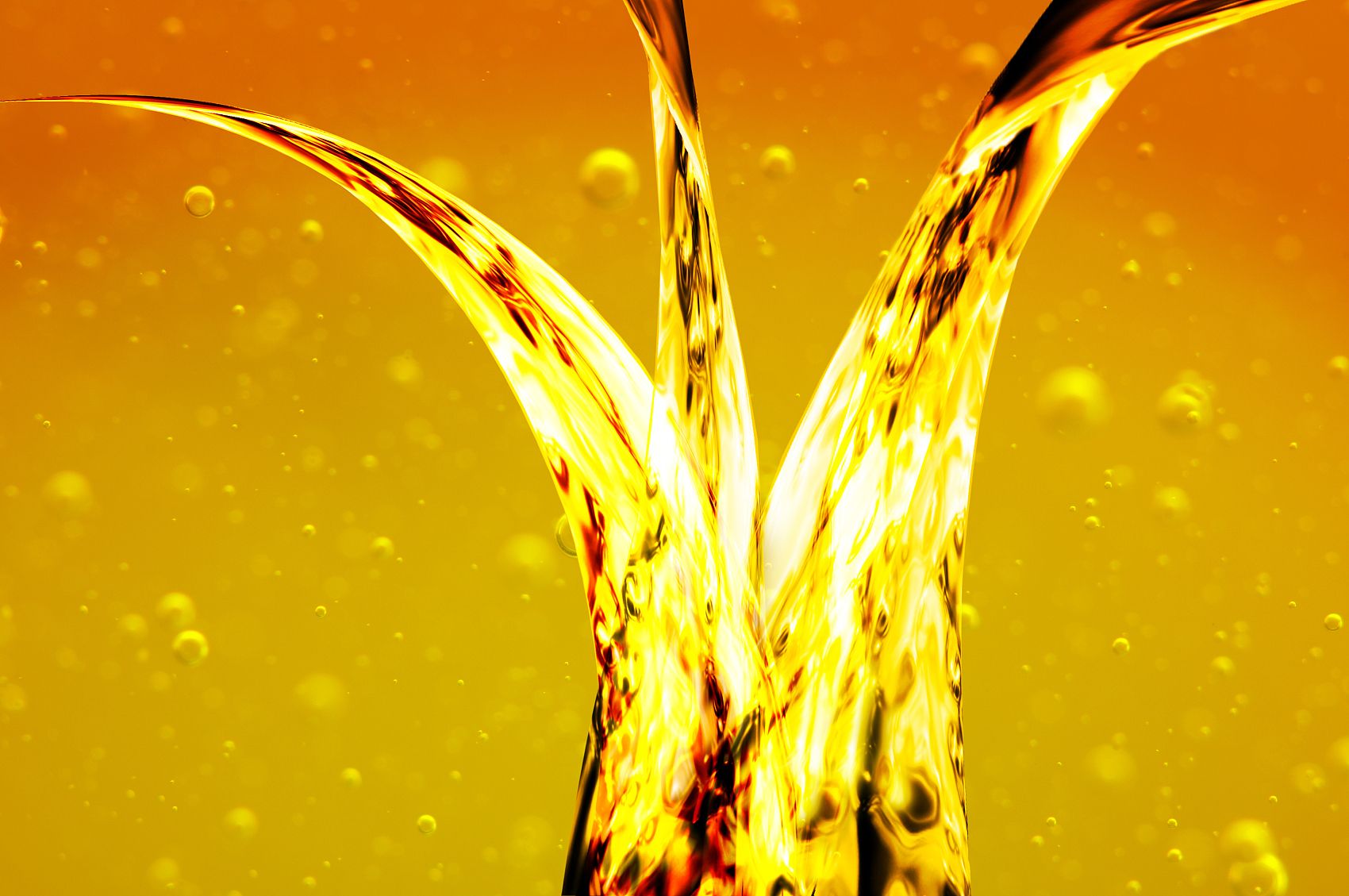
Key Attributes of Hydraulic Oil Performance and Compound Additives
Hydraulic oil is a core component of hydraulic systems, and its performance is directly related to the efficiency, reliability, and service life of the system. To meet the requirements of hydraulic systems under different working conditions, hydraulic oil needs to possess a series of key attributes, and its functions are optimized by adding compound additives. This article will start with the requirements of hydraulic systems for fluid performance, discuss in detail key attributes such as viscosity, oxidation stability, and wear resistance, analyze the role of compound additives taking anti-wear agents as an example, and finally emphasize the importance of selecting appropriate compound additives.
1. Requirements of Hydraulic Systems for Fluid Performance
Hydraulic systems are a widely used power transmission technology in modern mechanical equipment. They transfer energy through the incompressibility of liquids, achieving the amplification of force, control of motion, and conversion of energy. As the "blood" of hydraulic systems, hydraulic oil not only undertakes the task of energy transfer but also needs to perform multiple functions such as lubrication, cooling, and sealing. Therefore, the performance of hydraulic oil directly affects the operating efficiency and reliability of the system.
Hydraulic systems put forward the following basic requirements for fluid performance:
Appropriate Viscosity: Viscosity determines the fluidity and lubrication ability of hydraulic oil. Excessively high viscosity will increase the system resistance, leading to energy loss and heat generation; while excessively low viscosity may cause leakage and reduce the lubrication effect.
Good Oxidation Stability: Hydraulic oil is prone to oxidation under high-temperature and high-pressure environments, generating acidic substances and deposits, which will affect the system performance.
Excellent Wear Resistance: Moving parts such as pumps and valves in hydraulic systems require hydraulic oil to provide lubrication protection to reduce wear.
Demulsibility and Antifoaming Property: Hydraulic oil should be able to separate water and air quickly to avoid emulsification or foaming from affecting the system operation.
Seal Compatibility: Hydraulic oil should not chemically react with the sealing materials to ensure the sealing effect.
Wide Temperature Performance: Hydraulic oil needs to maintain stable performance in both high and low-temperature environments to ensure the normal operation of the system.
In addition, hydraulic oil also needs to have characteristics such as low compressibility, good filterability, and low volatility to meet the requirements of different application scenarios. For example, in the aerospace field, hydraulic oil may also need excellent electrical insulation; while in cold regions, the low-temperature fluidity of hydraulic oil is particularly crucial.
To meet these diverse requirements, hydraulic oil usually consists of base oil and compound additives. The base oil provides basic lubrication and flow performance, while the compound additives enhance specific functions of the hydraulic oil, such as anti-wear, anti-oxidation, and anti-emulsification, through chemical or physical actions.
2. Key Attributes: Viscosity, Oxidation Stability, and Wear Resistance
The performance of hydraulic oil is determined by multiple attributes. Among them, viscosity, oxidation stability, and wear resistance are the core factors affecting the system operation. The following will analyze the roles and importance of these attributes one by one.
2.1 Viscosity
Viscosity is the most basic physical property of hydraulic oil, directly affecting the energy transfer efficiency of the system and the lubrication effect of components. The viscosity of hydraulic oil is usually expressed by kinematic viscosity (unit: mm²/s), and its magnitude needs to select an appropriate grade according to the operating temperature and pressure of the system. Internationally recognized viscosity classification standards include ISO VG (International Organization for Standardization Viscosity Grade) and SAE (Society of Automotive Engineers) classification.
The selection of viscosity needs to balance multiple factors:
Excessively High Viscosity: It will increase the oil suction resistance of the pump, resulting in energy loss and system overheating. At the same time, it will slow down the liquid flow rate and affect the response speed.
Excessively Low Viscosity: It will lead to increased leakage, reduced system pressure stability, insufficient thickness of the lubricating film, and increased component wear.
In addition, the viscosity of hydraulic oil changes with temperature, and this characteristic is called the viscosity-temperature characteristic. The viscosity index (VI) is an indicator to measure the viscosity-temperature performance. The higher the VI, the smaller the viscosity fluctuation of the hydraulic oil when the temperature changes. For example, in a cold environment, hydraulic oil with a low pour point and high VI should be selected to ensure smooth low-temperature startup and operation. To improve the viscosity-temperature characteristic, viscosity index improvers such as polymethyl methacrylate are usually added to the hydraulic oil.
2.2 Oxidation Stability
Hydraulic oil is prone to oxidation reactions under the action of high temperature, high pressure, and oxygen, generating acidic substances, gums, and deposits. These oxidation products may corrode metal parts, block filters and valves, and lead to system failures. Therefore, oxidation stability is an important indicator to measure the life of hydraulic oil and the reliability of the system.
The advantages and disadvantages of oxidation stability can be evaluated by the following indicators:
Acid Value: It reflects the content of acidic substances in the hydraulic oil. An increase in the acid value indicates an intensification of oxidation.
Deposits: The solid particles generated by oxidation may affect the cleanliness of the system.
Viscosity Change: Oxidation will cause the viscosity of the hydraulic oil to increase, affecting its fluidity and lubricity.
To improve oxidation stability, antioxidants are usually added to the base oil. Antioxidants inhibit the progress of the oxidation chain reaction by capturing free radicals or decomposing peroxides. Common antioxidants include:
Phenolic Antioxidants: Such as 2,6-di-tert-butyl-p-cresol (BHT), which is suitable for medium and low-temperature environments.
Amine Antioxidants: Such as phenyl-α-naphthylamine, which is suitable for high-temperature conditions.
In addition, the selection of base oil also affects the oxidation stability. Compared with ordinary mineral oil, synthetic oil (such as polyalphaolefin) has higher oxidation stability and is suitable for harsh working conditions.
2.3 Wear Resistance
Components such as pumps, valves, and actuators in hydraulic systems operate under high pressure, and there are sliding or rolling contacts between metals, which require hydraulic oil to provide effective lubrication protection to reduce wear. Insufficient wear resistance will lead to damage to the surface of components and shorten the service life of the system.
The quality of wear resistance can be evaluated by experimental methods:
Four-Ball Test: Evaluate the anti-wear performance of hydraulic oil by measuring the wear scar diameter and friction coefficient.
Gear Pump Test: Simulate the actual working conditions to detect the wear resistance effect of hydraulic oil under high pressure.
To improve wear resistance, anti-wear agents are usually added to the hydraulic oil. Anti-wear agents can form a protective film on the metal surface to reduce friction and wear. Common anti-wear agents include phosphates, sulfides, and organic metal compounds. For example, zinc dialkyldithiophosphate (ZDDP) is a multifunctional anti-wear agent that can form a zinc phosphate film on the metal surface to provide excellent wear resistance protection.
3. The Role of Compound Additives: Taking Anti-wear Agents as an Example
Compound additives are the key to improving the performance of hydraulic oil. They endow hydraulic oil with specific functions through physical or chemical actions to meet the complex needs of the system. As one of the most common compound additives in hydraulic oil, the role of anti-wear agents is particularly prominent.
3.1 Types of Anti-wear Agents
There are a wide variety of anti-wear agents. According to their chemical composition and action mechanism, they can be divided into the following categories:
Phosphorus-based Anti-wear Agents: Such as tricresyl phosphate (TCP), which forms a phosphide film on the metal surface and is suitable for medium and low-load conditions.
Sulfur-based Anti-wear Agents: Such as sulfurized isobutylene, which forms a sulfide film under high temperature and pressure and has excellent extreme pressure performance.
Organic Metal Compounds: Such as ZDDP, which not only provides anti-wear protection but also has anti-oxidation and anti-corrosion functions.
Nano Anti-wear Agents: Utilize the special properties of nanoparticles to provide efficient anti-wear effects.
Polymer Anti-wear Agents: Reduce friction and wear by forming a polymer film.
3.2 Action Mechanism of Anti-wear Agents
Anti-wear agents protect the metal surface through the following mechanisms:
Adsorption Film Theory: Anti-wear agent molecules are adsorbed on the metal surface to form a lubricating film, reducing direct contact.
Chemical Reaction Film Theory: Anti-wear agents react with the metal surface to generate a wear-resistant chemical film, such as a phosphide film or a sulfide film.
Deposition Film Theory: Anti-wear agents decompose during friction, generating solid particles that are deposited on the surface to form a protective layer.
Taking ZDDP as an example, it decomposes under high temperature and pressure, generating phosphates and sulfides, which react with the metal to form a multi-layer protective film, including an oxide layer, a sulfide layer, and a phosphate layer. This composite film can effectively reduce wear under harsh conditions.
3.3 Selection of Anti-wear Agents
When selecting anti-wear agents, the following factors need to be comprehensively considered:
Working Conditions: Temperature, pressure, and speed determine the type of anti-wear agent. For example, adsorption-type anti-wear agents are suitable for high-speed and low-load conditions, while reaction-type anti-wear agents are required for low-speed and high-load conditions.
Material Compatibility: Anti-wear agents should not have adverse reactions with the metals or sealing materials in the system.
Synergism of Compound Additives: Anti-wear agents need to work synergistically with other additives (such as antioxidants) to improve the overall performance.
Environmental Protection Requirements: Give priority to selecting anti-wear agents with low toxicity and low pollution to meet regulatory requirements and the needs of sustainable development.
For example, in heavy-duty hydraulic equipment, ZDDP is widely used due to its excellent anti-wear performance and multifunctionality; while in occasions with high environmental protection requirements, nano anti-wear agents can be selected to replace traditional sulfur and phosphorus-containing additives.
4. The Importance of Selecting Appropriate Compound Additives
The performance of hydraulic oil directly determines the operating efficiency and service life of the hydraulic system, and compound additives are the key to improving the performance of hydraulic oil. By optimizing attributes such as viscosity, oxidation stability, and wear resistance, compound additives can meet the requirements of hydraulic systems under different working conditions. Taking anti-wear agents as an example, they significantly reduce component wear by forming a protective film and extend the service life of the system.
Selecting appropriate compound additives requires comprehensively considering the working conditions of the system, material compatibility, the interaction between compound additives, and environmental protection requirements. For example, in a high-temperature environment, efficient antioxidants should be selected, and in heavy-load conditions, powerful anti-wear agents should be used in combination. At the same time, the formulation design of compound additives needs to avoid antagonistic effects and ensure synergistic enhancement.
With the progress of hydraulic technology and the improvement of environmental protection requirements, compound additives in the future will develop in the direction of multi-functionality, high efficiency, and greenness. For example, developing compound additives that have both anti-wear and anti-oxidation functions, or using nanotechnology to improve the performance of additives. These innovations will further promote the improvement of hydraulic oil performance and meet a wider range of application scenarios.
In conclusion, through scientific selection and optimization of compound additives, the performance of hydraulic oil can be significantly improved, ensuring the efficient, reliable, and long-life operation of the hydraulic system. This is not only an embodiment of technological progress but also an important path to achieve industrial sustainable development.
The Price of Hydraulic Oil Additives Package
The price of Hydraulic Oil Additives Package varies depending on factors such as brand, specification, composition, and sales channels. If you are interested in Hydraulic Oil Additives Package, please feel free to contact us.
Supplier of Hydraulic Oil Additives Package
UNPChemicals is a professional supplier of high-quality and effective Hydraulic Oil Additives Package. We offer several remarkable products, namely High zinc hydraulic oil additives UNP AH502A,Low Zinc Hydraulic Oil Additives UNP AH502B,Zinc-free Hydraulic Oil Additives UNP AH502C,etc.
High zinc hydraulic oil additives UNP AH502A are a type of chemical additive used in hydraulic oils that contain high levels of zinc dialkyldithiophosphate (ZDDP). ZDDP is a well-known anti-wear agent that also provides antioxidant, anti-corrosion, and anti-foam properties. The zinc in these additives plays a crucial role in forming a protective film on metal surfaces within the hydraulic system, thereby reducing wear and extending the life of the system components.
Low Zinc Hydraulic Oil Additives UNP AH502B are a class of advanced lubricant additives designed to enhance the performance of hydraulic oils with reduced zinc content.These additives are formulated to provide a balance of anti-wear,extreme pressure,and antioxidant properties,making them suitable for modern hydraulic systems that demand high performance with lower environmental impact.
Zinc-free Hydraulic Oil Additives UNP AH502C are a new class of environmentally friendly lubricant additives designed for hydraulic systems.These additives are formulated to provide the same level of performance as traditional zinc-containing additives but without the heavy metal content,reducing the environmental impact of hydraulic fluids.
Professional Lubricant Additive Manufacturer
UNPChemicals,aka Luoyang Pacific United Petrochemical Co., Ltd., focuses on the application and development of special lubricating grease additives such as MODTC, MODTP, molybdenum amide, thiadiazole metal deactivators, and phosphate esters. With nearly 30 products in seven series, including extreme pressure anti-wear additives and special grease additives, it is a global manufacturer of special lubricating grease additives and a national high-tech enterprise with great influence and leading role in the industry. If you are looking for Lubricant Additive or technical information, feel free to contact UNPChemicals.