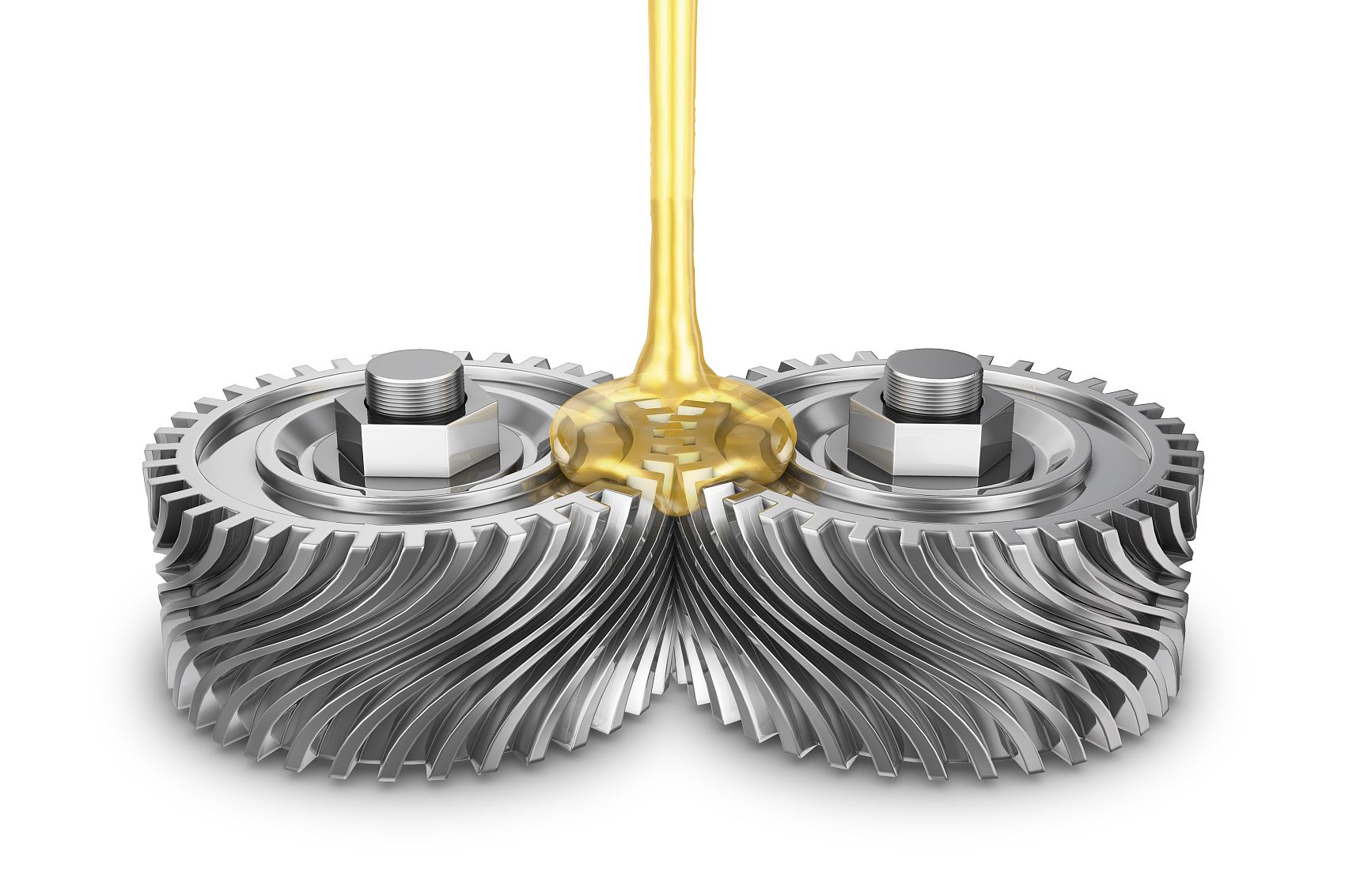
Industrial Gear Oil: The Key Guardian of Industrial Gear Transmission Systems
The Core Position of Gear Oil in Gear Transmission Systems
In the gear transmission systems of various mechanical equipment, gear oil serves as a silent but crucial guardian. It undertakes the dual missions of lubrication and protection, playing a decisive role in enabling the gears to operate smoothly without any jams and significantly extending the service life of the equipment. During the daily operation of machinery, the gears continuously engage and disengage, generating intense friction. Without an appropriate lubricating medium, the tooth surfaces are highly prone to damage due to excessive friction, which not only causes unstable operation of the equipment but also greatly shortens its service life. The presence of gear oil is like providing a "cushion" for the friction between the gears, greatly reducing the negative impacts of friction.
However, when the gear transmission system encounters some extremely harsh working environments, relying solely on base oil is insufficient. For example, under heavy load conditions, the gears bear pressures far beyond the normal range, and the force between the tooth surfaces increases sharply. In high-speed operation conditions, the gears experience countless engagements and disengagements in a short period, significantly increasing the friction frequency and heat generation rate. In these extreme situations, the base oil struggles to maintain a stable oil film and cannot provide reliable lubrication for the gears. At this time, industrial gear lubricants with more excellent performance are urgently needed.
Industrial Gear Lubricants: Tailor-Made Lubricants for Industrial Transmissions
(I) Comprehensive Function Analysis
Industrial gear lubricants are lubricants carefully designed specifically for the special needs of various industrial gear transmission systems, and their role is of great significance in the vast landscape of industrial production. In the steel manufacturing industry, huge rolling mills rely on gear transmission to achieve the precise rotation of the rolling rolls, processing red-hot steel billets into various specifications of steel products. In the mining industry, the gear transmission systems of large excavation equipment, hoists, etc., need to bear the heavy task of handling materials. In the machining industry, the gear transmission of precision machine tools is related to the machining accuracy.
In these diverse and complex industrial scenarios, industrial gear lubricants can form a continuous and stable oil film between the tooth surfaces of the gears. This oil film is like a sturdy barrier, separating the originally directly contacting tooth surfaces and effectively reducing the friction coefficient between the tooth surfaces. According to relevant test data, a suitable industrial gear lubricant can reduce the friction coefficient between the tooth surfaces to a fraction or even lower of the original value, thus greatly reducing the heat generated by friction. This not only prevents serious failure modes such as gear wear and scuffing but also provides an efficient cooling effect on the gears. It is like an efficient heat transporter, promptly taking away the heat generated during the operation of the gears to ensure that the gears are always within an appropriate working temperature range. Research shows that a good cooling effect can reduce the working temperature of the gears by 10 - 20℃, which is of great significance for ensuring the accuracy and efficiency of gear transmission and extending the service life of the gears. In addition, industrial gear lubricants also have excellent sealing and protection capabilities, which can effectively prevent external water vapor, dust, and other pollutants from entering the gear meshing area, creating a clean and safe operating environment for the gear transmission system.
(II) Analysis of Unique Characteristics
1. High Load-Carrying Capacity: In the actual operation of industrial gears, they often face huge loads. Take the gears of a large-scale mine crusher as an example. When crushing hard ores, the pressure on the tooth surfaces can reach several thousand or even tens of thousands of Newtons. Under such heavy load conditions, industrial gear lubricants must have sufficient oil film strength. Through special formulation design and the synergistic effect of additives, the lubricant can form a tough oil film on the tooth surface to ensure that the tooth surfaces do not come into direct contact, effectively preventing tooth surface damage such as pitting and spalling. Experimental verification shows that high-quality industrial gear lubricants can reduce the contact stress on the tooth surface by 30% - 50% under simulated heavy load conditions, greatly improving the load-carrying capacity of the gears.
2. Good Anti-Wear Property: Due to the continuous meshing friction of the gear tooth surfaces, wear is inevitable. High-quality industrial gear lubricants contain special anti-wear additives, such as molybdenum disulfide, borate, etc. These additives can quickly react chemically with the tooth surface metal when friction occurs on the tooth surface, forming a tough and self-healing protective film. This protective film is like putting on a "armor" for the tooth surface, which can effectively reduce the wear rate. Relevant research shows that using industrial gear lubricants containing high-efficiency anti-wear additives can reduce the gear wear amount by more than 50%, significantly extending the service life of the gears.
3. Excellent Oxidation Stability: The industrial environment is complex and changeable, and the gears are in operation for a long time. The lubricant will inevitably come into contact with air and undergo oxidation reactions. Once oxidation occurs, the lubricant will gradually deteriorate, producing acidic substances and sludge. Acidic substances will corrode the metal surface of the gears, and the sludge will block the oil passage, affecting the normal circulation and heat dissipation of the lubricant. Industrial gear lubricants with good oxidation stability can effectively inhibit the occurrence of oxidation reactions by adding high-performance antioxidants, such as hindered phenol antioxidants and amine antioxidants. Experimental data shows that the oxidation induction period of such lubricants can be extended several times under harsh environments such as high temperature and high humidity, which can maintain stable performance for a long time, reduce sludge generation, and ensure the reliable operation of the gear transmission system.
4. Appropriate Viscosity: The viscosity of industrial gear lubricants needs to be precisely controlled to be just right. In the equipment startup stage, the viscosity of the lubricant is relatively high in a low-temperature environment. If the viscosity is too high, it will lead to poor fluidity of the lubricant, making it difficult to reach all lubrication parts quickly, increasing the startup resistance, and even possibly causing difficulties in equipment startup. When the equipment enters the normal operation state, under different working condition temperature changes, the lubricant needs to maintain a certain oil film thickness to ensure good lubrication. Therefore, an appropriate viscosity can not only ensure sufficient fluidity to quickly reach the lubrication parts during startup but also adapt to different working condition temperature changes and maintain the oil film thickness during operation. For example, in cold winter regions, low-viscosity industrial gear lubricants with better low-temperature fluidity are required to ensure that the equipment can be started smoothly. In high-temperature and heavy-load industrial production environments, lubricants with higher viscosity and excellent viscosity-temperature performance are needed to ensure the stability of the oil film.
(III) Interpretation of Strict Requirements
1. Compatibility with Materials: Industrial gear lubricants need to be perfectly compatible with the metal materials of transmission components such as gears and bearings, as well as sealing materials. On the one hand, it should not corrode the metal materials. Taking steel gears as an example, if the lubricant contains corrosive substances, during long-term use, it will gradually erode the gear surface, causing problems such as pitting and rust on the metal surface, seriously affecting the strength and accuracy of the gears. On the other hand, the lubricant should not cause the sealing materials to age or deform. The seals play an important role in preventing the leakage of lubricating oil and the entry of external pollutants in the gear transmission system. Once the seals are damaged due to incompatibility with the lubricant, it will lead to the leakage of lubricating oil, reducing the lubrication effect. At the same time, the entry of external pollutants will also exacerbate the wear of the gears. Therefore, during the research, development, and production of industrial gear lubricants, strict material compatibility tests must be carried out to ensure harmonious coexistence with various related materials.
2. Cleaning and Dispersing Property: During the operation of the gears, wear particles, metal debris, and external pollutants are inevitably generated. If these impurities are not removed in a timely manner, they will accumulate in the gear meshing area, causing secondary wear and further aggravating the damage to the gears. Industrial gear lubricants have excellent cleaning and dispersing properties, which can effectively disperse these wear particles, pollutants, etc. in the oil and keep them in a stable suspended state. In this way, during the lubricant circulation process, the impurities can be easily removed through the filtration system, maintaining the cleanliness of the lubricant and providing a clean lubrication environment for the gears. Relevant experiments show that industrial gear lubricants with good cleaning and dispersing properties can reduce the gear wear amount by 20% - 30%, greatly improving the reliability of the gear transmission system.
3. Demulsibility: In some industrial environments, such as wet mining sites, or when the cooling system of the equipment leaks, water can easily mix into the industrial gear lubricant. Once the lubricant forms an emulsion with water, its lubrication performance will be greatly reduced, and it cannot effectively protect the gears. Therefore, industrial gear lubricants must have the ability to quickly separate from water, that is, good demulsibility. By adding special demulsifiers, the lubricant can break the emulsification interface between water and oil, causing the water to settle and separate quickly, restoring the normal lubrication performance of the lubricant. Through practical application verification, high-quality industrial gear lubricants can achieve oil-water separation in a short time when water is mixed in, ensuring that the gear transmission system can still operate normally in wet or water-mixed harsh environments.
Lubrication Methods of Industrial Gear Oil
(I) Immersion Lubrication: A Classic and Practical Lubrication Option
Immersion lubrication is a relatively common lubrication method in industrial gear transmission systems. Its operation principle is relatively simple. Just immerse a part of the gear in a specially set lubricant pool. When the gear rotates, it will carry the lubricant to the meshing part by itself, thus achieving the lubrication of the gear. This lubrication method has the significant advantages of simple structure and low cost. For some low-speed and medium-load gear transmission systems, it is an economical and reliable choice. For example, in the gear transmissions of some small food processing equipment and simple conveying devices, immersion lubrication is widely used.
However, immersion lubrication is not perfect. Since the gear will continuously stir the lubricant when rotating in the lubricant pool, this will lead to a certain amount of energy loss and increase the operating cost of the equipment. At the same time, its heat dissipation effect is relatively slow. When the gear operates at high speed or under heavy load, it is difficult to dissipate the generated heat quickly, which may cause the temperature of the lubricant to be too high and affect its lubrication performance. In addition, if the oil level is not controlled properly, a too high oil level is likely to cause the leakage of lubricating oil, which not only wastes resources but also may pollute the working environment. A too low oil level cannot ensure that the gears are fully lubricated, increasing the wear of the gears.
(II) Spray Lubrication: An Efficient and Precise Lubrication Solution
Spray lubrication is a lubrication method that sprays the lubricant to the gear meshing area at a certain pressure through an oil pump. This method has many advantages. Firstly, it can precisely control the oil supply amount. According to the actual working load, rotation speed, and other parameters of the gears, the lubricant spray amount can be flexibly adjusted to ensure that the gears can obtain sufficient and appropriate lubrication under different working conditions. Secondly, the heat dissipation effect of spray lubrication is excellent. The high-speed sprayed lubricant can quickly take away a large amount of heat generated by the gear meshing, effectively reducing the working temperature of the gears and improving the load-carrying capacity and operating efficiency of the gears. Therefore, spray lubrication is particularly suitable for high-speed and heavy-load gear transmission systems, such as the gearboxes of large wind turbines and the transmission gears of high-speed trains.
However, spray lubrication also has some limitations. This method requires the installation of special oil pumps, oil pipes, filters, and other devices, and the equipment cost is relatively high. Moreover, the maintenance of these devices is relatively complicated. It is necessary to regularly check the working pressure of the oil pump, the tightness of the oil pipes, and the cleanliness of the filters, etc. Once a certain component fails, it may cause the entire lubrication system to fail and affect the normal operation of the equipment. In addition, spray lubrication has extremely high requirements for the cleanliness of the lubricant. If the lubricant contains impurities, it may block the spray nozzles and affect the lubrication effect.
(III) Oil Mist Lubrication: An Energy-Saving and Environmentally Friendly Lubrication Innovation
Oil mist lubrication is a relatively new lubrication method. It uses compressed air to atomize the lubricant and then it to the gear part. During this process, the lubricant is transformed into fine oil mist particles, which can evenly adhere to the tooth surface to achieve the lubrication of the gears. Oil mist lubrication has unique advantages. It can achieve minimal lubrication. Compared with traditional lubrication methods, it can significantly reduce the amount of lubricant used, lower production costs, and is more environmentally friendly. In addition, the heat dissipation effect of the oil mist is very good, which can quickly take away the heat generated during the operation of the gears and keep the gears running at a low temperature. Therefore, oil mist lubrication is particularly suitable for high-speed and light-load gear transmissions, such as the high-speed gears of textile machinery and the precision gears of electronic equipment.
However, oil mist lubrication has high requirements for the air source. A stable and clean air source is the key to ensuring the normal formation and transportation of the oil mist. If the air source is unstable and the pressure fluctuates greatly, it will lead to uneven sizes of the oil mist particles, affecting the lubrication effect. If the air source contains a large amount of impurities, it may also block the atomization device, making the oil mist lubrication system unable to work properly. In addition, attention needs to be paid to safety issues during the use of oil mist lubrication. The oil mist is flammable to a certain extent. When used in an environment with an open flame or high temperature, corresponding protective measures need to be taken to prevent fire or explosion accidents.
Industrial Gear Oil Additive Packages: The Core Code of Modern Industrial Gear Lubrication
(I) An Inevitable Choice to Cope with Complex Working Conditions
In modern industrial production, the working conditions faced by industrial gears are becoming increasingly complex and diverse, and a single base oil simply cannot meet these harsh requirements. Industrial gear oil additive packages have emerged as the key to solving this problem. Industrial gear oil additive packages contain a variety of functional additives, which work together synergistically to provide comprehensive protection for industrial gears.
Among them, extreme pressure anti-wear agents play a crucial role under heavy load and impact load conditions. When the gears bear huge pressure and instant impact force, the extreme pressure anti-wear agents can react chemically with the tooth surface metal to form a tough chemical reaction film on the tooth surface, greatly enhancing the oil film strength and effectively preventing serious failure forms such as tooth surface scuffing and spalling. For example, in the large forging equipment in the metallurgical industry, the gears bear strong impact loads during the forging process, and the extreme pressure anti-wear agents can ensure that the gears still maintain good operating conditions under such extreme working conditions.
Antioxidants are also an important part of industrial gear oil additive packages. As mentioned before, the gears in the industrial environment operate for a long time, and the lubricant is very likely to undergo oxidation when it comes into contact with air. Antioxidants can significantly extend the service life of the lubricant by capturing free radicals and decomposing peroxides. In practical applications, industrial gear oils added with high-quality antioxidants can extend the oil change cycle by 1 - 2 times, greatly reducing the costs brought by frequent oil changes, including lubricant procurement costs and equipment shutdown maintenance costs.
Rust inhibitors provide reliable anti-rust protection for the gears. In industrial environments with humidity or corrosive media, such as chemical production workshops and industrial facilities in coastal areas, the gears are easily threatened by corrosion. Rust inhibitors can form a dense protective film on the metal surface of the gears to prevent water vapor, corrosive gases, etc. from coming into contact with the metal, thus preventing the gears from rusting. Relevant experiments show that using industrial gear oils containing rust inhibitors can reduce the corrosion rate of the gears in a humid environment by more than 80%, effectively extending the service life of the gears.
(II) Facilitating the Preparation of Personalized Products
For lubricant manufacturers, the use of industrial gear oil additive packages has great convenience. Different industries and working conditions have different performance requirements for industrial gear lubricants. For example, the high-temperature and heavy-load working conditions in the steel industry require lubricants to have higher load-carrying capacity and oxidation resistance. The precision gear transmissions in the electronics industry have stricter requirements for the cleanliness, anti-wear property, and compatibility with electronic components of the lubricants. By using industrial gear oil additive packages, lubricant manufacturers can quickly prepare personalized industrial gear lubricant products according to these different requirements. Just add the corresponding additive packages in a certain proportion to the base oil, and through simple processes such as mixing and stirring, high-performance lubricants that meet specific working conditions can be produced. This method not only improves production efficiency but also ensures the stability of product quality. Manufacturers can flexibly adjust the product formula according to market demand, providing comprehensive and high-performance lubrication guarantees for the reliable operation of industrial gears and occupying a dominant position in the fierce market competition.
The Price of Additive Packages
The price of Additive Packages varies depending on factors such as brand, specification, composition, and sales channels. If you are interested in Additive Packages, please feel free to contact us.
Supplier of Additive Packages
UNPChemicals is a professional supplier of high-quality and effective Additive Packages. We offer several remarkable products, namely Industrial Gear Oil Additives UNP IG402A,High extreme pressure type industrial gear oil additive package UNP IG402B,Low-odor type industrial gear oil additive package UNP IG402C,etc.
UNP IG402A is a high-performance gear oil additive package that includes sulfur,phosphorus,and nitrogen types of additives.It is known for its excellent antioxidation,antirust,and antiwear properties.This additive package is characterized by its low dosage requirement,high cost-effectiveness,and broad applicability,making it suitable for a wide range of industrial gear oils,particularly those based on hydrotreated oils.
High extreme pressure (EP) type industrial gear oil additive packages, like UNP IG402B, are specialized blends of chemical compounds designed to enhance the performance of base oils used in industrial gear lubricants. These packages are formulated to provide exceptional protection under conditions where gears experience heavy loads, high pressures, and potential metal-to-metal contact.
The Low-Odor Type Industrial Gear Oil Additive Package UNP IG402C is a specialized blend of chemical additives designed to enhance the performance of industrial gear oils while minimizing the strong odors typically associated with traditional gear oil additives, particularly those containing sulfur-based extreme pressure (EP) agents. This additive package is mixed with base oils (mineral or synthetic) to create gear lubricants that protect industrial gearboxes under demanding conditions, such as high loads and temperatures, while being more user-friendly in terms of smell—ideal for environments where odor control is a priority.
Professional Lubricant Additive Manufacturer
UNPChemicals, aka Luoyang Pacific United Petrochemical Co., Ltd., focuses on the application and development of special lubricating grease additives such as MODTC, MODTP, molybdenum amide, thiadiazole metal deactivators, and phosphate esters. With nearly 30 products in seven series, including extreme pressure anti-wear additives and special grease additives, it is a global manufacturer of special lubricating grease additives and a national high-tech enterprise with great influence and leading role in the industry. If you are looking for Lubricant Additive or technical information, feel free to contact UNPChemicals.