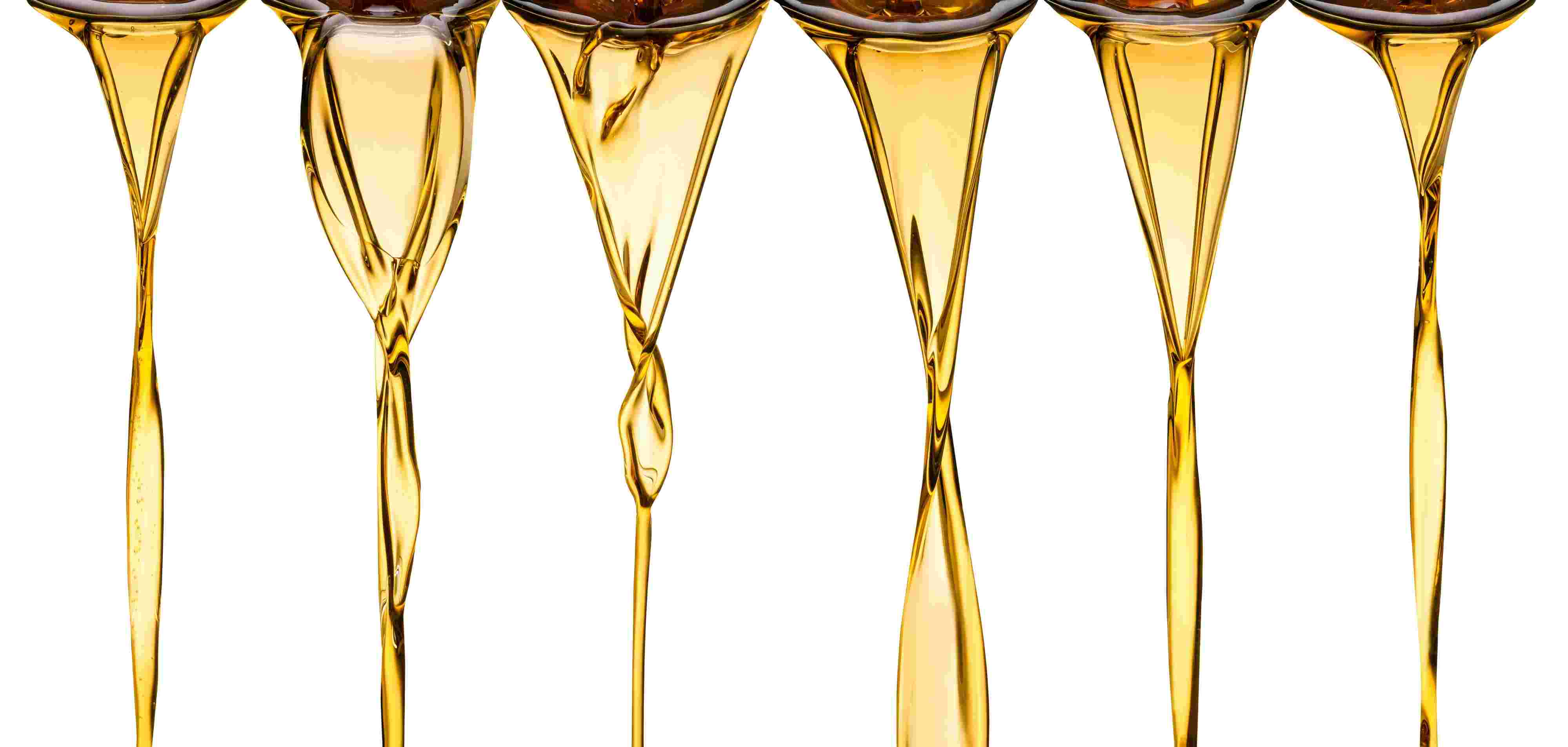
Hydraulic Oil: A Key Lubricant in the Industrial Sector
In the modern industrial system, hydraulic transmission technology, with its continuously evolving advantages, has seen its application scope expand, widely covering key industries such as aviation, automobiles, ships, construction, petroleum, and various engineering machinery. Within the entire hydraulic system, hydraulic oil serves as an indispensable core component, playing a pivotal role, and its performance directly determines the operational efficiency of the hydraulic system. Therefore, for all types of hydraulic machinery, the precise selection of suitable hydraulic oil is the fundamental prerequisite for ensuring the normal operation of the equipment.
I. Stringent Requirements for Hydraulic Oil in Hydraulic Machinery
Taking the oil pump as an example, it is the core hub of the entire hydraulic system, and hydraulic oil is akin to the blood circulating within the system. Even if the hydraulic equipment is exquisitely designed and manufactured with high precision, if the hydraulic oil is not correctly selected and used, not only will its performance advantages not be fully realized, but in severe cases, it may even lead to major accidents, causing equipment damage or significantly shortening the equipment's service life. The reliable, efficient, and economical operation of the hydraulic system largely depends on the performance of the hydraulic oil.
Specifically, the requirements for hydraulic oil are mainly reflected in the following key aspects:
Appropriate viscosity and excellent viscosity-temperature performance: Viscosity is a key parameter for measuring the performance of hydraulic oil and is one of the primary factors to consider when selecting hydraulic oil. Its selection needs to comprehensively balance factors such as the type of oil pump, working pressure, usage environment, and ambient temperature, while also taking into account the specific needs of other hydraulic components. Viscosity that is too high or too low will have negative impacts on the equipment, leading to reduced overall efficiency, poor control performance, and insufficient operational flexibility.
Excellent rust and corrosion resistance: Hydraulic components are usually made of various metal materials, which are highly susceptible to rust under the combined action of moisture and oxygen (including inherent oxygen in the oil and oxygen mixed in from the air). In addition, after oxidation, hydrolysis, and other chemical reactions, hydraulic oil and its additives will also generate corrosive substances. Therefore, hydraulic machinery operating in special environments such as ports has extremely high requirements for the rust resistance of hydraulic oil.
Outstanding oxidation resistance: When hydraulic machinery is in operation, hydraulic oil inevitably comes into contact with air and undergoes oxidation and deterioration, especially under conditions of increased temperature and pressure, where the oxidation rate significantly accelerates. The acidic substances produced after oxidation enhance the corrosiveness to metals, and the viscous sludge precipitates generated can clog the pores of filters and other components, hinder the normal operation of control mechanisms, reduce system efficiency, and exacerbate equipment wear. Therefore, the better the oxidation resistance of hydraulic oil, the longer its service life.
Excellent demulsibility: Hydraulic equipment that operates in humid environments for extended periods is prone to water droplets mixing into the hydraulic oil tank. The water that enters the tank, under the vigorous agitation of hydraulic components such as oil pumps and oil motors, easily disperses in the hydraulic oil to form an emulsion. This not only accelerates the deterioration of hydraulic oil and produces precipitates but also affects the heat transfer of coolers, clogs the pores of filters, pipes, valves, and other hydraulic components, thereby reducing the lubricating performance of hydraulic oil. Therefore, hydraulic equipment requires hydraulic oil to have good demulsibility.
II. Selection of Hydraulic Oil Additives or Compound Agents
The rational selection of hydraulic oil additives or compound agents is crucial for optimizing the performance of hydraulic oil and meeting the complex working condition requirements of hydraulic systems. When selecting, multiple factors need to be comprehensively considered.
Selection based on hydraulic system working conditions: For hydraulic systems with high pressure, high load, and high working temperatures, emphasis should be placed on selecting compound agents containing high-performance anti-wear additives and antioxidant additives. For example, in large hydraulic equipment in the metallurgical industry, due to high system pressure and high oil temperature, selecting compound agents containing efficient anti-wear agents such as zinc dialkyldithiophosphate (ZDDP) and phenolic and amine antioxidants can effectively improve the anti-wear and antioxidant properties of hydraulic oil, ensuring stable operation of the equipment under harsh conditions. For hydraulic systems operating in low-temperature environments, compound agents with pour point depressants and low-temperature fluidity improvers should be selected to ensure that the hydraulic oil maintains good fluidity and pumpability at low temperatures, such as in hydraulic systems of engineering machinery operating in polar regions, where such compound agents play a key role.
Considering the type of hydraulic oil base oil: Different types of base oils have varying sensitivities to additives. For hydraulic oils based on mineral oil, when selecting additives, attention should be paid to their compatibility and synergistic effects with mineral oil. For example, for hydraulic oils based on paraffinic mineral oil, certain detergents and antioxidants can perform better, helping to keep the oil clean and extend its service life. For hydraulic oils based on synthetic oils, such as polyalphaolefin (PAO) synthetic oil, which inherently have good thermal and oxidative stability, additives or compound agents that focus on enhancing anti-wear and demulsibility can be selected to further optimize the comprehensive performance of hydraulic oil under specific working conditions.
Paying attention to the compatibility between additives: Hydraulic oil compound agents are usually composed of multiple additives, and the compatibility between these additives directly affects the overall performance of the compound agent. For example, there may be interactions between anti-wear agents and rust inhibitors, and if the compatibility is improper, it may lead to a decrease in rust resistance or a weakening of the anti-wear effect. Therefore, when selecting compound agents, it is necessary to ensure that the additives can synergize with each other to achieve the best effect. Generally, mature compound agent products that have undergone professional research and development and extensive experimental verification have better assurance in terms of additive compatibility.
Following industry standards and equipment manufacturer requirements: Different industries and equipment manufacturers have specific requirements and standards for hydraulic oil additives or compound agents. For example, in the aerospace field, the performance requirements for hydraulic oil are extremely stringent, and they must comply with relevant aviation standards. The selected additives or compound agents must undergo strict certification and testing. In industrial equipment, equipment manufacturers usually explicitly recommend applicable hydraulic oil and additive types in the equipment manual, and following these requirements helps ensure the normal operation and maintenance of the equipment.
III. Analysis of the Current Development Status of Hydraulic Oil
China began researching hydraulic oil in the 1960s and, after years of development, has now established a relatively complete system of hydraulic oil varieties. However, compared with well-known foreign petroleum companies, there is still a certain gap, prominently manifested in the relatively lagging market introduction of clean hydraulic oil and green hydraulic oil products by domestic oil producers.
Looking back at the development history of hydraulic oil, it can be roughly divided into the following stages:
Ordinary hydraulic oil: Ordinary hydraulic oil is based on deeply refined mineral oil, with added antioxidants, preservatives, rust inhibitors, and antifoaming agents, and some also include a small amount of anti-wear agents and pour point depressants. Its performance is similar to that of foreign rust and oxidation-inhibited (R&O type) hydraulic oils. However, for medium and high-pressure hydraulic systems, its anti-wear performance is slightly insufficient, and in such systems, anti-wear hydraulic oil is more suitable. Currently, globally, ordinary hydraulic oil is gradually being replaced by anti-wear hydraulic oil.
Anti-wear hydraulic oil: Anti-wear hydraulic oil can be subdivided into ash-containing type (ZDDP type) and ashless type. Ash-containing anti-wear hydraulic oil has excellent anti-wear performance and can meet the usage requirements of vane pumps; ashless anti-wear hydraulic oil performs better in terms of hydrolytic stability, demulsibility, oil filterability, and thermal and oxidative stability, with its performance standard equivalent to Denison HF-O.
Low-temperature hydraulic oil: In areas with low ambient temperatures (below -15°C) or significant temperature variations, hydraulic equipment operating outdoors needs to use hydraulic oil with a low pour point and high viscosity index, giving rise to low-temperature hydraulic oil. Compared with anti-wear hydraulic oil, low-temperature hydraulic oil has a lower pour point, better low-temperature fluidity, a higher viscosity index (generally above 130), and good low-temperature stability. However, it also has some shortcomings, such as inferior anti-wear properties compared to anti-wear hydraulic oil and poor shear resistance. When hydraulic equipment is under heavy load, the viscosity drops rapidly after strong shearing, which may affect the normal operation of the equipment.
Clean hydraulic oil: Hydraulic systems equipped with electro-hydraulic servo valves have extremely high requirements for hydraulic oil quality, especially the solid particle content in the oil must be strictly controlled within a certain range. This is because solid particles can cause extensive premature wear of precision components such as hydraulic pumps and valves, rendering them inoperable and thus causing the hydraulic system to fail to function properly.
Fire-resistant hydraulic oil: Fire-resistant hydraulic oil is mainly used in hydraulic systems close to or adjacent to fire sources and heat sources in industries such as metallurgy, mining, power plants, and machining. It is mainly divided into three types: water-based hydraulic oil (water-in-oil type, oil-in-water type, water-glycol type), phosphate ester type, and other synthetic types, each suitable for hydraulic systems with different pressure ranges and temperature ranges.
Green hydraulic oil: Over the past 20 years, environmental issues have become a key research topic for scientists worldwide. To address this challenge, developed countries have taken the lead in conducting relevant research and launching a series of biodegradable lubricants. In 1994, the usage of green hydraulic oil accounted for 7% of the total hydraulic oil usage, and by 2000, this proportion increased to 10%. Green hydraulic oil, also known as biodegradable hydraulic oil, is required to be degraded by active microorganisms into carbon dioxide and water in a relatively short period. Currently, the most commonly used biodegradability test method is CEC L33T82, issued by the Coordinating European Council (CEC) in 1982, now renamed CEC L33T93, used to evaluate various lubricants. For green hydraulic oil, the biodegradability rate is required to be greater than 80%, and the base fluid is a key factor affecting the biodegradability of lubricants. Vegetable oils and synthetic esters have good biodegradability and are often used as base oils for green hydraulic oil.
IV. Outlook on the Future Development Trends of Hydraulic Oil
With the continuous advancement of hydraulic technology, the performance requirements for hydraulic oil are becoming increasingly stringent. Relying solely on the compounding technology of compound agents is no longer sufficient to fully meet the demand for improving hydraulic oil quality; it is necessary to leverage high-quality component oils such as hydrotreated base oils and synthetic oils for synergistic cooperation. Ashless anti-wear agents should possess excellent anti-wear performance, good hydrolytic stability, and thermal stability, laying a solid foundation for the development of high-quality ashless anti-wear hydraulic oil. New liquid antioxidants or antioxidant additives will become the research and development direction for antioxidants. The level of compound agents has become an important indicator of today's lubrication technology. Due to the diverse molecular structures and mechanisms of action of various additives, their performance in different additive formulation systems varies, necessitating a fine balance of related additives and summarizing patterns to prepare competitive hydraulic oil compound agents.
In addition, industrial machinery components are becoming increasingly complex, with hydraulic systems, gear transmission systems, bearings, etc., often belonging to the same set of mechanical equipment, leading to an excessive variety of oils used in the same system, which brings many inconveniences to equipment maintenance and oil management. Therefore, the future development trend of hydraulic oil is, on the one hand, to deeply promote the research work on new ashless anti-wear hydraulic oils, and on the other hand, to vigorously develop oils with strong versatility to meet the oil requirements of complex systems.
The Price of Hydraulic Oil Additives Package
The price of Hydraulic Oil Additives Package varies depending on factors such as brand, specification, composition, and sales channels. If you are interested in Hydraulic Oil Additives Package, please feel free to contact us.
Supplier of Hydraulic Oil Additives Package
UNPChemicals is a professional supplier of high-quality and effective Hydraulic Oil Additives Package. We offer several remarkable products, namely High zinc hydraulic oil additives UNP AH502A,Low Zinc Hydraulic Oil Additives UNP AH502B,Zinc-free Hydraulic Oil Additives UNP AH502C,etc.
High zinc hydraulic oil additives UNP AH502A are a type of chemical additive used in hydraulic oils that contain high levels of zinc dialkyldithiophosphate (ZDDP). ZDDP is a well-known anti-wear agent that also provides antioxidant, anti-corrosion, and anti-foam properties. The zinc in these additives plays a crucial role in forming a protective film on metal surfaces within the hydraulic system, thereby reducing wear and extending the life of the system components.
Low Zinc Hydraulic Oil Additives UNP AH502B are a class of advanced lubricant additives designed to enhance the performance of hydraulic oils with reduced zinc content.These additives are formulated to provide a balance of anti-wear,extreme pressure,and antioxidant properties,making them suitable for modern hydraulic systems that demand high performance with lower environmental impact.
Zinc-free Hydraulic Oil Additives UNP AH502C are a new class of environmentally friendly lubricant additives designed for hydraulic systems.These additives are formulated to provide the same level of performance as traditional zinc-containing additives but without the heavy metal content,reducing the environmental impact of hydraulic fluids.
Professional Lubricant Additive Manufacturer
UNPChemicals, aka Luoyang Pacific United Petrochemical Co., Ltd., focuses on the application and development of special lubricating grease additives such as MODTC, MODTP, molybdenum amide, thiadiazole metal deactivators, and phosphate esters. With nearly 30 products in seven series, including extreme pressure anti-wear additives and special grease additives, it is a global manufacturer of special lubricating grease additives and a national high-tech enterprise with great influence and leading role in the industry. If you are looking for Lubricant Additive or technical information, feel free to contact UNPChemicals.