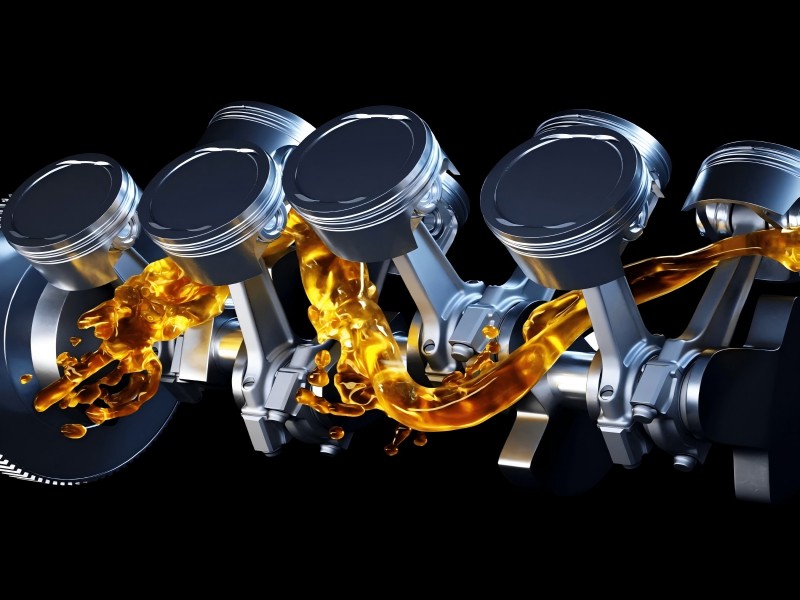
How to Choose Turbine Oil Additives?
In modern industrial and energy sectors, turbines are core equipment in critical industries such as power generation, aerospace, marine propulsion, and petrochemicals. Their stable operation is vital to the efficient functioning of the entire industrial system. Turbine oil, as a key element in ensuring the proper operation of turbines, directly impacts their efficiency and service life through its performance and quality. Therefore, a deep understanding of turbine working principles, types, lubrication systems, and the purposes, selection methods, and roles of turbine oil additives is of great significance for ensuring the efficient and reliable operation of turbines.
1. Definition and Working Principle of Turbines
A turbine is a rotary power machine that efficiently converts the energy of a fluid (liquid or gas) into mechanical energy. Its working principle relies on high-speed fluid impacting turbine blades, causing the turbine rotor to rotate continuously and produce usable mechanical energy. This energy conversion method is highly efficient and stable, making it widely applied across various fields. For instance, in power plants, steam turbines utilize high-temperature, high-pressure steam generated by boilers to drive the rotor and power generators. In aerospace, gas turbines rely on high-temperature, high-pressure gas from combustion to drive the turbine, providing powerful thrust for aircraft.
2. Types of Turbines
Steam Turbines
Steam turbines use steam as their working medium. After being heated to high temperature and pressure in a boiler, the steam enters the turbine and drives the blades to rotate. Based on steam parameters and application scenarios, steam turbines can be classified into condensing, back-pressure, and extraction types. Condensing steam turbines, primarily used in large thermal power plants, exhaust steam into a condenser where it is cooled into water for recycling, improving thermal efficiency. Back-pressure steam turbines discharge steam for industrial heating, enabling cascaded energy utilization. Extraction steam turbines draw steam from different stages based on user needs, meeting various industrial steam demands.
Gas Turbines
Gas turbines use gas as their working medium and consist of a compressor, combustion chamber, and turbine. Air is compressed by the compressor, mixed with fuel, and ignited in the combustion chamber, producing high-temperature, high-pressure gas. This gas expands in the turbine, driving the blades to rotate. Gas turbines are quick to start and have high power density, making them widely used in aviation engines, gas turbine power units, and marine propulsion. In aviation, their high performance enables aircraft to break speed barriers, while in power generation, they respond rapidly to grid demand fluctuations, ensuring stability.
Hydraulic Turbines
Hydraulic turbines use water as their working medium, converting water flow energy into rotational energy via the runner. Based on energy conversion methods and structural features, they are divided into reaction and impulse types. Reaction turbines, suitable for low-head, high-flow hydropower stations (e.g., axial-flow and Francis turbines), convert energy through the reaction force of water on the runner blades. Impulse turbines, suited for high-head, low-flow stations (e.g., Pelton turbines), use high-speed water jets to strike the runner buckets and drive rotation.
3. Components and Functions of Turbine Lubrication Systems
The stable operation of turbines relies on a well-designed lubrication system, which includes key components such as oil tanks, pumps, filters, coolers, and control valves. Its primary function is to supply clean, lubricating, and cooling oil to the turbine, ensuring normal operation and long-term stability.
Oil Tank
The oil tank, a crucial part of the lubrication system, stores turbine oil. To meet varying operational demands, it typically has a large capacity. Internal baffles separate impurities and water from the oil while aiding heat dissipation, maintaining oil cleanliness and quality.
Oil Pump
The oil pump, the system's core power component, delivers oil from the tank to the turbine's lubrication points and working parts. Common types, such as gear pumps and screw pumps, offer high pressure and flow stability, ensuring timely and accurate oil delivery.
Filter
Filters play a vital protective role and are divided into coarse and fine types. Coarse filters, installed at the pump's inlet, remove larger impurities to prevent pump damage. Fine filters, located at the pump's outlet, perform precision filtration to ensure the oil meets operational cleanliness standards.
Cooler
Turbines generate significant heat during operation, raising oil temperatures. High temperatures impair oil performance and lubrication, making coolers essential. Using water or air as a cooling medium, coolers dissipate heat to maintain oil within an optimal temperature range. Common types include tube and plate coolers, known for their efficient heat exchange.
Control Valve
Control valves regulate the pressure and flow of the lubrication system to adapt to varying turbine operating conditions. Including pressure and flow control valves, they automatically adjust opening based on operating parameters and signals, achieving precise system control.
4. Basic Uses and Roles of Turbine Oil
Turbine oil is primarily used for lubricating and cooling various turbines (steam, gas, and hydraulic) and their associated components, such as reduction gearboxes and governors. It is also employed in industrial equipment like compressors and pumps with high lubrication demands, ensuring reliable operation.
Lubrication
One key role of turbine oil is to form a uniform, stable oil film between high-speed moving parts, separating metal surfaces to reduce friction and wear. For example, in bearings, the oil film supports the rotor's weight and radial/axial forces, ensuring smooth operation and extending equipment life.
Cooling
Turbines generate substantial heat during operation, which, if not dissipated, threatens performance and longevity. Turbine oil absorbs heat and transfers it to the cooler via the cooling medium, reducing equipment temperature and maintaining optimal conditions.
Cleaning
Detergent-dispersant additives in turbine oil disperse metal debris, oxidation products, and other impurities generated during operation, preventing sediment buildup that could impair performance. Filters further remove these contaminants, keeping the oil clean and effective.
Corrosion Protection
To prevent corrosion of metal components, turbine oil contains rust inhibitors and antioxidants. These additives form a protective film on metal surfaces, blocking reactions with oxygen and moisture. For long-term turbine operation, this corrosion protection significantly extends service life and reduces maintenance costs.
5. Selection of Turbine Oil
Choosing the right turbine oil is critical for ensuring normal operation and extending equipment life. Selection should consider the following factors:
Turbine Type
Different turbines have unique oil performance requirements. For example, steam turbines, prone to steam contamination and emulsification, demand high oxidation and emulsification resistance. Gas turbines, operating at high gas temperatures, require strong high-temperature and anti-wear properties. Hydraulic turbines, in humid environments, need excellent rust and hydrolysis resistance.
Operating Conditions
Operating conditions include temperature, pressure, and speed. Turbines running under extreme conditions (high temperature, pressure, or speed) require oils with superior high-temperature, anti-wear, and oxidation-resistant properties. For instance, gas turbines in aviation engines, operating at extreme temperatures, need specialized high-temperature oils.
Manufacturer Recommendations
Manufacturers provide oil brand and model recommendations based on turbine design and operational needs. Following these ensures compatibility, optimizing performance, reducing failures, and enhancing reliability and stability.
Oil Quality and Performance Metrics
Key metrics include viscosity, viscosity index, flash point, acid value, oxidation resistance, anti-wear properties, and emulsification resistance. Viscosity affects flow and lubrication; a higher viscosity index indicates better temperature-viscosity performance; a higher flash point improves safety; a high acid value signals corrosive potential; and strong oxidation, anti-wear, and emulsification resistance enhance oil longevity and equipment reliability.
6. Turbine Oil Additives and Their Roles
Turbine oil additives are chemical substances blended into base oils to enhance performance, meeting the operational demands of turbines under various conditions. They provide special properties like oxidation resistance, anti-wear, emulsification resistance, and rust protection, adapting to harsh environments and ensuring comprehensive turbine protection. Below is a detailed overview of common additive types, roles, applications, and maintenance considerations:
(1) Common Turbine Oil Additives and Their Roles
1. Antioxidants
Antioxidants are essential in turbine oil. During operation, oil reacts with oxygen, degrading performance (e.g., increased viscosity, acid value, and sludge formation). Antioxidants inhibit these reactions, extending oil life. Common types include phenolic and amine compounds, which capture free radicals to halt oxidation chains.
2. Anti-Wear Agents
In high-speed components like bearings and gears, friction and wear are inevitable. Anti-wear agents form a protective film on metal surfaces, reducing direct contact and wear. Zinc dialkyldithiophosphate (ZDDP), for example, creates a sulfide film, enhancing wear protection and extending component life.
3. Demulsifiers
In steam or hydraulic turbines, water or steam contamination can emulsify oil, reducing lubrication and heat dissipation. Demulsifiers destabilize oil-water interfaces, enabling rapid separation and restoring oil performance. Typically surfactants, they lower interfacial tension to promote separation.
4. Rust Inhibitors
Turbine metal parts are prone to rust from moisture and oxygen. Rust inhibitors form a dense protective film on metal surfaces, blocking contact with corrosive elements. Common types include fatty acid salts and sulfonates, which adsorb onto surfaces for effective rust prevention.
5. Detergent-Dispersants
Metal debris and oxidation products generated during operation can form deposits if accumulated. Detergent-dispersants disperse these impurities in the oil, preventing buildup, and neutralize acidic substances to avoid corrosion. High-molecular compounds, they encapsulate impurities via lipophilic and hydrophilic groups.
6. Antifoam Agents
Foaming can occur during oil circulation, reducing lubrication and heat transfer, and destabilizing operation. Antifoam agents quickly eliminate foam and prevent its formation, ensuring oil stability. Typically silicones, they lower surface tension to suppress foam.
7. Metal Deactivators
Metal ions in oil can catalyze oxidation, accelerating degradation. Metal deactivators bind these ions into stable complexes, inhibiting catalysis and extending oil life.
8. Extreme Pressure (EP) Additives
Under high-load, high-temperature conditions, turbine components face extreme pressure. EP additives form a chemical reaction film on metal surfaces, enhancing oil's load-carrying capacity and preventing wear or scoring. Common types include sulfur-phosphorus compounds and chlorides.
(2) Applications of Turbine Oil Additives
Turbine oil additives are widely used across all turbine types requiring lubrication and cooling. Key applications include:
1. Steam Turbines
In thermal power plants, steam turbines face complex conditions where steam contamination can emulsify and oxidize oil. Demulsifiers and antioxidants maintain oil performance, while rust inhibitors and anti-wear agents prevent corrosion and wear.
2. Gas Turbines
Used in aviation, power generation, and marine propulsion, gas turbines demand high-temperature and anti-wear performance due to extreme heat and loads. Antioxidants, anti-wear agents, and EP additives ensure oil stability and lubrication under these conditions.
3. Hydraulic Turbines
Operating in wet environments, hydraulic turbines require demulsifiers and rust inhibitors to counter emulsification and corrosion. Detergent-dispersants and antifoam agents enhance oil cleanliness and stability, preventing impurity buildup and foaming.
4. Industrial Gearboxes and Hydraulic Systems
Turbine oil is often used in gearboxes and hydraulic systems, requiring high cleanliness, anti-wear, and oxidation resistance. Detergent-dispersants, anti-wear agents, and antioxidants improve oil performance and extend equipment life.
(3) Maintenance Considerations for Turbine Oil Additives
Proper maintenance ensures oil performance and equipment reliability. Key points include:
1. Regular Oil Quality Testing
Periodically test viscosity, acid value, oxidation resistance, and emulsification resistance to monitor oil condition. If performance declines, replenish or replace additives to restore functionality.
2. Maintaining Oil Cleanliness
Regularly clean tanks and filters to prevent contamination by impurities or water, ensuring additives perform effectively and reducing wear and failures.
3. Temperature Control
Excessive oil temperatures accelerate oxidation and additive depletion. Maintain optimal temperatures via functional coolers, regularly checking their heat exchange efficiency.
4. Following Manufacturer Recommendations
Use oils and additives recommended by manufacturers based on equipment design and needs to maximize lifespan and minimize failures.
5. Additive Compatibility
Ensure new additives are compatible with existing oil and additives to avoid performance degradation or equipment issues. Conduct thorough testing before adding new additives.
Turbine oil additives play a vital role in modern industry, imparting properties like oxidation resistance, anti-wear, demulsification, and rust protection to adapt to harsh conditions and ensure stable turbine operation. Proper selection and use of additives significantly enhance oil performance, extend equipment life, reduce maintenance costs, and provide reliable power support for industrial production and societal development.
The Price of Turbine Oil Additive Packages
The price of Turbine Oil Additive Packages varies depending on factors such as brand, specification, composition, and sales channels. If you are interested in Turbine Oil Additive Packages, please feel free to contact us.
Supplier of Turbine Oil Additive Packages
UNPChemicals is a professional supplier of high-quality and effective Turbine Oil Additive Packages. We offer several remarkable products, namely Turbine Oil Additives UNP TB602,etc.
Turbine Oil Additives UNP TB602 are a sophisticated blend of compounds designed to enhance the performance and longevity of turbine oils used in a variety of industrial applications.These additives are carefully formulated to address the specific challenges of high-temperature,high-pressure environments common in steam,gas,and hydro turbines.
Professional Lubricant Additive Manufacturer
UNPChemicals, aka Luoyang Pacific United Petrochemical Co., Ltd., focuses on the application and development of special lubricating grease additives such as MODTC, MODTP, molybdenum amide, thiadiazole metal deactivators, and phosphate esters. With nearly 30 products in seven series, including extreme pressure anti-wear additives and special grease additives, it is a global manufacturer of special lubricating grease additives and a national high-tech enterprise with great influence and leading role in the industry. If you are looking for Lubricant Additive or technical information, feel free to contact UNPChemicals.