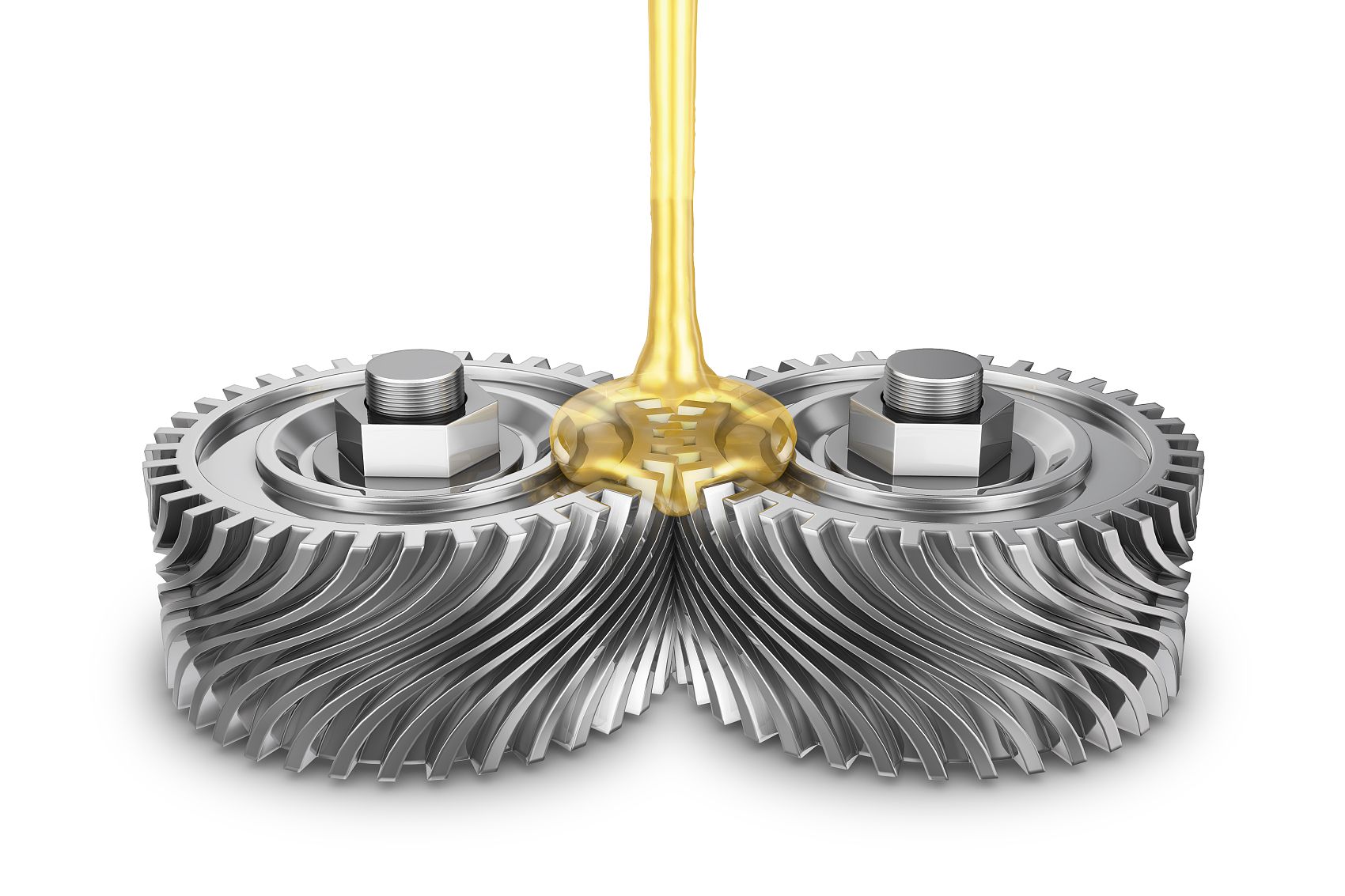
How to Choose Lubricant Rust inhibitor additives ?
In the lubricant system, additives and Rust inhibitor additives are crucial components. For lubricant manufacturing enterprises, thoroughly understanding the types, working principles of these products, and how to accurately select suitable Rust inhibitor additives is the core to improving product quality and enhancing market competitiveness. Next, we will delve into the field of lubricant additives, with a particular focus on the professional knowledge of Rust inhibitor additives .
I. The Importance of Lubricant Additives
Lubricant additives are chemical substances added to optimize the performance of lubricants, and they play a significant role in practical applications. In terms of oxidation resistance, when an automobile engine operates at a high temperature continuously, ordinary lubricants are prone to oxidize and deteriorate under the combined action of high temperature and oxygen. Lubricants with added anti - oxidation additives can effectively slow down this oxidation process and extend the service life of the lubricants. Regarding anti - wear, in industrial machinery, components such as gears and bearings rub against each other at high speeds, resulting in severe wear. Appropriate anti - wear additives can form a protective film on the component surface, reducing the friction coefficient, minimizing wear, and ensuring the stable operation of the machinery. In terms of corrosion resistance, when lubricants are used in working environments containing chemical corrosive media, anti - corrosion additives can neutralize or inhibit corrosive substances to prevent metal components from being corroded. The rust - prevention performance is related to the service life of metal components. In various mechanical equipment, rusting of metal components will lead to a decline in their performance and strength. Rust - prevention additives can effectively prevent rust from occurring. Among the many types of additives, Rust inhibitor additives are particularly prominent as they act directly on metal components, preventing metals from rusting due to factors such as oxidation and water during use, ensuring the normal operation and service life of the equipment.
II. Types of Lubricant Rust inhibitor additives
Lubricant Rust inhibitor additives can be mainly classified into the following categories based on their chemical composition and action mechanisms:
-Inorganic Rust inhibitor additives : Substances such as phosphates and silicates belong to the category of inorganic Rust inhibitor additives . Taking phosphates as an example, it undergoes a chemical reaction on the metal surface to form an insoluble iron phosphate or zinc phosphate protective film. This film has a dense structure and can effectively block the direct contact between oxygen and moisture in the air and the metal, thus achieving the purpose of preventing rust. In the lubrication of some industrial equipment with high environmental requirements, silicate Rust inhibitor additives are widely used. The protective film formed on the metal surface by them can not only prevent rust but also has certain high - temperature resistance.
-Organic Rust inhibitor additives : Calcium sulfonate, fatty acids, etc. belong to organic Rust inhibitor additives . The calcium sulfonate molecule has a special structure. One end is a lipophilic group that can blend well with the lubricant, and the other end is a polar group that can closely adsorb on the metal surface, forming a film with both lubricating and rust - preventing functions. This film can reduce the friction coefficient of the metal surface and at the same time prevent the intrusion of moisture and oxygen. Fatty acids react chemically with the active sites on the metal surface to form a metal soap film. This film can not only isolate external corrosive media but also has a certain lubricating effect and is often used in the lubricants of precision instruments with high requirements for both lubrication and rust prevention.
-Composite Rust inhibitor additives : It combines the advantages of inorganic and organic Rust inhibitor additives . For example, an inorganic rust preventive with good film - forming properties is compounded with an organic rust preventive with strong adsorption. First, the inorganic rust preventive forms a basic protective film on the metal surface, and then the organic rust preventive further fills the gaps and enhances the adsorption force, thus providing more comprehensive and long - lasting rust protection. In the engine lubricants of some large ships, composite Rust inhibitor additives are widely used to cope with the corrosion threat of the complex marine environment to metal components.
III. Working Principles of Lubricant Rust inhibitor additives
The working principles of Rust inhibitor additives mainly cover the following three mechanisms:
-Forming a Protective Film: This is a common rust - prevention method. The active ingredients in the rust preventive gradually accumulate on the metal surface through physical or chemical adsorption to form a dense protective film. For example, some high - molecular polymer - type Rust inhibitor additives have their molecular chains intertwined to form a protective layer on the metal surface, isolating air, moisture, and other corrosive substances and fundamentally preventing rust from occurring. In the lubrication protection of outdoor large - scale steel structures, Rust inhibitor additives that prevent rust by forming a protective film are widely used.
-Electrochemical Protection: Some special Rust inhibitor additives can change the electrochemical properties of the metal surface. When the metal and its surrounding environment form a corrosion cell, the active ingredients in the rust preventive will participate in the electrode reaction, inhibiting the anodic dissolution process or promoting the cathodic hydrogen evolution reaction, thus disrupting the formation conditions of the corrosion cell and reducing the occurrence of rust. For example, in the anti - corrosion of some metal pipes, Rust inhibitor additives using the principle of electrochemical protection can effectively extend the service life of the pipes.
-Adsorption Effect: The polar groups in the rust preventive molecules have a strong affinity for the metal surface and can form a close - fitting adsorption film on the metal surface. This adsorption film prevents the direct contact between moisture, oxygen, and other corrosive media and the metal. Some organic Rust inhibitor additives containing polar atoms such as nitrogen and oxygen achieve the rust - prevention function through this adsorption effect and are often used in the lubrication and maintenance of electronic equipment with high rust - prevention requirements.
IV. How to Select Appropriate Lubricant Rust inhibitor additives
Selecting suitable Rust inhibitor additives requires comprehensive consideration of multiple factors:
-Metal Type: Different metals have different chemical activities and crystal structures, resulting in different requirements for Rust inhibitor additives. For example, aluminum and its alloys are relatively soft and chemically active, and they are prone to chemical reactions with certain Rust inhibitor additives , leading to corrosion. Therefore, it is necessary to select Rust inhibitor additives that are specifically designed for aluminum, have good compatibility, do not react adversely with aluminum, and can form an effective protective film on its surface. For metals such as steel, due to their high susceptibility to rust, Rust inhibitor additives with strong rust - prevention performance and the ability to closely bind to iron atoms are required.
-Working Environment: The use environment of lubricants is complex and diverse. In high - temperature environments, such as the high - temperature furnace front equipment in steel smelting plants, Rust inhibitor additives with good high - temperature resistance need to be selected to ensure that the performance of the Rust inhibitor additives remains stable at high temperatures and does not decompose due to excessive heat. In high - humidity environments, like the industrial equipment in coastal areas, the moisture - proof performance of Rust inhibitor additives is crucial to effectively resist the erosion of a large amount of water vapor. If the working environment contains chemical corrosive media, such as the production equipment in chemical enterprises, Rust inhibitor additives with anti - chemical corrosion performance also need to be selected to adapt to the harsh chemical environment.
-Performance Requirements: According to the expected performance standards of the lubricant, additives with corresponding rust - prevention performance should be selected. If it is used in high - speed and high - load mechanical equipment, the rust preventive is required to have not only good rust - prevention performance but also certain anti - wear and extreme - pressure resistance to ensure the normal operation of the equipment under harsh working conditions. For some precision instruments with high requirements for cleanliness, the rust preventive should not contain impurities and should not affect the accuracy of the instrument.
-Cost - effectiveness: On the basis of meeting performance requirements, the cost factor cannot be ignored. Enterprises need to comprehensively evaluate the price, usage amount of the rust preventive, and the benefits it can bring. For example, although some high - performance imported Rust inhibitor additives have excellent rust - prevention effects, they are expensive. For some small enterprises with limited budgets and not particularly high requirements for rust - prevention performance, domestic Rust inhibitor additives with higher cost - effectiveness may be a better choice. Through the cost - effectiveness analysis of different Rust inhibitor additives , enterprises can select products that both meet their needs and are cost - effective.
Lubricant Rust inhibitor additives play a key role in protecting the metal components of mechanical equipment. For lubricant manufacturing enterprises, in - depth understanding of the types, working principles, and scientific and reasonable selection methods of Rust inhibitor additives is an important factor for standing out in the market competition. By accurately selecting and correctly using Rust inhibitor additives, not only can the service life of the equipment be significantly extended, the costs of equipment repair and replacement be reduced, but also the comprehensive performance of the lubricant can be improved in all aspects, enhancing the competitiveness of the enterprise's products in the market. Reasonable selection of lubricant Rust inhibitor additives can effectively protect the equipment and save a large amount of maintenance costs for the enterprise.
The Price of Rust inhibitor
The price of Rust inhibitor varies depending on factors such as brand, specification, composition, and sales channels. If you are interested in Rust inhibitor, please feel free to contact us.
Supplier of Rust inhibitor
UNPChemicals is a professional supplier of high-quality and effective Rust inhibitor. We offer several remarkable products, namely Oleic acid imidazoline corrosion inhibitor CMET AO,N-acyl sarcosine type corrosion inhibitor CMET SO,Dodecylene succinic acid CMET T746,Heptadecenyl imidazoline succinate CMET T703,etc.
Oleic acid imidazoline corrosion inhibitor CMET AO is a multifunctional additive derived from imidazoline, known for its versatility in various applications, including serving as a corrosion inhibitor, dewatering agent, and emulsifier for lubricants.
N-acyl sarcosine type corrosion inhibitor CMET SO, an N-acyl sarcosine, is a corrosion inhibitor of lubricating oil, grease and fuel oil. With exceptional performance when used in combination with CMET AO, CMET SO is suitable for food-grade lubricating oil formulas and boasts good oil solubility.
Dodecylene succinic acid CMET T746 is an oil soluble ashless rust inhibitor with dodecyl succinic acid structure. The product has good oil solubility and can form a solid oil film on the metal surface, comprehensively protecting the metal from rust and corrosion.
Heptadecenyl imidazoline succinate CMET T703 is an oil soluble ashless antirust additive made by neutralization of alkenyl Imidazoline and dodecenyl succinic acid. This product has excellent acid neutralization ability.
Professional Lubricant Additive Manufacturer
UNPChemicals, aka Luoyang Pacific United Petrochemical Co., Ltd., focuses on the application and development of special lubricating grease additives such as MODTC, MODTP, molybdenum amide, thiadiazole metal deactivators, and phosphate esters. With nearly 30 products in seven series, including extreme pressure anti-wear additives and special grease additives, it is a global manufacturer of special lubricating grease additives and a national high-tech enterprise with great influence and leading role in the industry. If you are looking for Lubricant Additive or technical information, feel free to contact UNPChemicals.