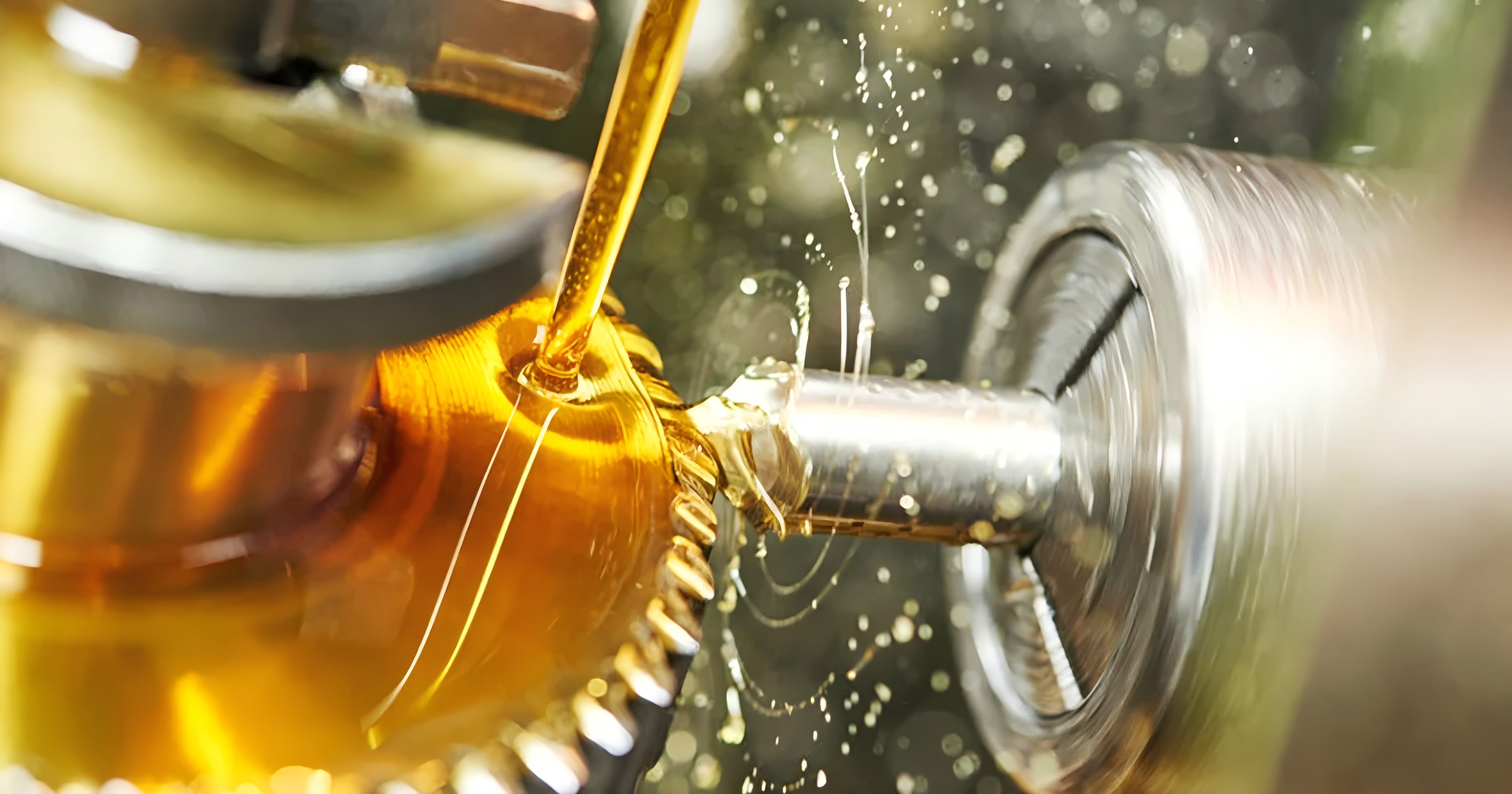
How much do you know about the classification and selection principles of industrial lubricants?
There are a wide variety of industrial lubricants, such as common anti - wear hydraulic oil, heat - transfer oil, gear oil, air compressor oil, etc. The oil - using standards vary for different industries and equipment. It's really not easy to select the suitable industrial lubricant.
What is an industrial lubricant?
An industrial lubricant is a type of lubricant specifically designed for industrial machinery and equipment. Its main functions are to reduce friction and wear, lower the heat and energy loss of mechanical components, thus extending the service life of equipment, improving operational efficiency, and ensuring the stability and reliability of industrial production.
Working principles of industrial lubricants
Lubrication and friction reduction
The primary working principle of industrial lubricants is to form an oil film between two relatively moving metal surfaces. When the components of the equipment rub against each other, the lubricant molecules will adsorb onto the metal surfaces, creating an oil film with a certain strength and toughness. This oil film acts like a buffer, separating the originally directly - contacting metal surfaces.
As a result, the friction between them changes from dry friction between solids to intermolecular friction within the liquid. Since the intermolecular friction of the liquid is much smaller than the friction between solid surfaces, the frictional resistance during the operation of the equipment is greatly reduced, the wear of components is decreased, and the service life of the equipment is extended. For example, in a large - scale gear transmission system, the lubricant can effectively reduce the friction between gear tooth surfaces and prevent the tooth surfaces from being damaged due to excessive wear.
Cooling and heat dissipation
During the operation of equipment, a large amount of heat is generated due to friction. Industrial lubricants can absorb this heat and transfer it out through their own circulation. When the lubricant flows inside the equipment, it continuously comes into contact with the surfaces of the heat - generating components, absorbs heat, and then, as the lubricant flows, it carries the heat to the cooling device (such as a radiator). Through heat exchange with the outside air or coolant, the heat is dissipated, thus keeping the equipment temperature within the normal range. For instance, in an engine, the lubricant not only plays a lubricating role but also takes away a large amount of heat generated by combustion and mechanical friction, preventing the engine from being damaged due to overheating.
Sealing and leakage prevention
In some industrial equipment, such as compressors and hydraulic systems, good sealing is required to ensure the normal operation of the system. Industrial lubricants can fill the gaps between components, forming an effective seal to prevent the leakage of gases or liquids. For example, in a reciprocating compressor, the lubricant forms an oil film between the piston and the cylinder wall, which not only lubricates but also prevents the compressed gas from leaking through the gap between the piston and the cylinder wall, improving the working efficiency of the compressor.
Cleaning and dispersion
During the operation of the equipment, some impurities such as metal debris, dust, and carbon deposits are generated. The detergent - dispersant in the industrial lubricant can disperse these impurities in the oil, preventing them from aggregating into larger particles. This avoids the wear or blockage of the oil passage caused by these impurities. At the same time, when the lubricant passes through the filtration system, these dispersed impurities can be effectively intercepted by the filter, maintaining the cleanliness of the lubricant. For example, in an automobile engine, the detergent - dispersant in the lubricant can disperse the carbon deposits and metal wear particles generated by combustion in the oil, preventing them from depositing inside the engine and affecting the engine's performance.
Product classification of industrial lubricants
Although there are numerous varieties of industrial lubricants, according to the main classification and application scenarios, they can be divided into nine major categories: hydraulic oil, gear oil, turbine oil, air compressor oil, vacuum pump oil, oil - film bearing oil, heat - transfer oil, chain oil, etc. It also includes other oil products such as paper machine circulating oil, knitting machine oil, marine engine oil, etc.
Hydraulic oil: Mainly used in hydraulic transmission systems.
Gear oil: Mainly used in gear - driven equipment in industries such as cement, steel, and power.
Turbine oil: Mainly used in various turbine units, such as for the lubrication and cooling of the sliding bearings of steam turbines.
Heat - transfer oil: Used in closed or open indirect heat - transfer systems.
Air compressor oil: Mainly used in various air compressors, such as screw air compressors and reciprocating air compressors.
Vacuum pump oil: Mainly used for the lubrication, sealing, and cooling of vacuum pumps.
Oil-film bearing oil: Suitable for the circulating system of Morgan high - speed wire rod rolling mills.
Chain oil: Mainly used for the transmission lubrication of chains.
Refrigerating machine oil: Mainly used for lubricating refrigerators with low pour point and low freezing point.
Other oil products: Paper machine circulating oil, knitting machine oil, marine engine oil, medium - speed high - alkaline oil, cylinder oil, system circulating oil, guideway oil, spindle oil, diffusion pump oil, transformer oil, etc.
Industrial lubricant series products- such as hydraulic oil, vacuum pump oil, air compressor oil, high - temperature chain oil, etc. - are all formulated with deeply refined mineral oil as the base oil and added with a variety of additives such as anti - wear, extreme - pressure, rust - proof, and anti - foaming agents. These products not only play the roles of lubrication, anti - oxidation, and anti - corrosion, but also have water - resistance and wear - resistance, providing good maintenance for specific equipment.
Hydraulic oil: The hydraulic oil series products can provide excellent anti - corrosion protection for demanding hydraulic components. They can be used in vane - type, gear - type, and piston - type oil pumps of mobile construction machinery operating in a high - temperature range and in the hydraulic systems of large - scale injection molding machines.
Vacuum pump oil: The vacuum pump oil series products are all made from deeply refined mineral oil as the raw material and added with a variety of additives such as anti - wear, extreme - pressure, and rust - proof agents. They have excellent viscosity - temperature performance, significantly improved anti - wear performance, and can reduce the interface wear during the compression of the pump.
Air compressor oil: The air compressor oil series products are all high - quality clean - type air compressor oils. They can provide reliable lubrication protection for rotary sliding compressors and screw air compressors.
High-temperature chain oil: The synthetic chain lubricating oil series products are formulated with high - quality synthetic oil as the base oil and added with a variety of additives. They have excellent high - temperature oxidation stability, anti - wear properties, low carbon - deposition properties, low volatility, high flash point, etc. They are pollution - free, rust - free, and have good lubricity when used for a long time at high temperatures. They are used for the lubrication of mechanical chain transmission systems operating under high - temperature conditions and can meet the use requirements in high - temperature working environments.
Roles of industrial lubricants in various industries
Lubricants are liquid lubricants used on various types of machinery to reduce friction, protect the machinery, or for machining. They mainly play roles such as lubrication, cooling, rust - prevention, cleaning, sealing, and buffering. The general requirements for lubricants are as follows:
Friction and wear reduction: Reduce frictional resistance to save energy, reduce wear to extend the mechanical life, and improve economic efficiency.
Cooling: It is required to discharge the frictional heat out of the machine at any time.
Sealing: It is required to prevent leakage, dust, and gas - stringing.
Anti-corrosion and rust - prevention: Protect the surface of equipment components from rust and corrosion.
Cleaning and flushing: It is required to clean and remove the scale on the friction surface.
Stress dispersion and buffering: Disperse the load, buffer impacts, and dampen vibrations.
Kinetic energy transfer: In hydraulic systems, remote - control motors, and friction - type stepless speed - changers, etc.
Importance of industrial lubricants
Ensure normal operation of equipment
Industrial equipment usually operates under harsh conditions such as high load, high speed, and high temperature. Without proper industrial lubricants for lubrication and protection, the components of the equipment will be quickly damaged due to excessive wear, overheating, etc., resulting in equipment failure and downtime. Using high - quality industrial lubricants can ensure the smooth operation of all components of the equipment, reduce the probability of failures, and guarantee the continuity and stability of industrial production. For example, in steel production, large - scale equipment such as blast furnaces and rolling mills cannot operate normally without the support of industrial lubricants. If there is a problem with the lubricant, it may lead to equipment shutdown, causing huge economic losses to the enterprise.
Improve production efficiency
By reducing the frictional resistance of the equipment and reducing the downtime due to failures, industrial lubricants can significantly improve production efficiency. When the equipment operates smoothly, its production speed and product quality can be effectively improved. For example, on an automated production line, an accurate transmission system and well - lubricated equipment can ensure the high - precision manufacturing of products and, at the same time, reduce production delays caused by equipment failures, improving the overall production efficiency.
Reduce energy consumption
Since industrial lubricants can reduce the frictional losses of the equipment, the power required for the equipment to operate is reduced, thus reducing energy consumption. In the context of the global advocacy of energy conservation and emission reduction, this role is particularly important. According to statistics, the rational use of industrial lubricants can reduce the energy consumption of industrial equipment by 5% - 20%. For some large - scale industrial enterprises, this means considerable savings in energy costs.
Prolong the service life of equipment
As mentioned above, the lubrication, cooling, and cleaning functions of industrial lubricants can effectively reduce the wear, corrosion, and aging of equipment components, thus prolonging the service life of the equipment. Compared with frequently replacing equipment components or purchasing new equipment, the cost of using industrial lubricants for equipment maintenance is much lower. This not only saves a large amount of funds for enterprises but also reduces the environmental impact caused by equipment replacement.
Selection principles of industrial lubricants
Viscosity selection is the first step in doing a good job in equipment lubrication management. You can select according to the selection query table, or you can select according to the following principles:
Load size: If the load is large, select an oil with high viscosity and good extreme - pressure properties; if the load is small, select an oil with low viscosity.
Operating speed: If the speed is high, select an oil with low viscosity; if the speed is low, select an oil with high viscosity.
Wear degree: For new and relatively precise equipment, select an oil with moderate viscosity; for old equipment, select an oil with relatively high viscosity.
Ambient temperature: If the ambient temperature is low, select a lubricant with low viscosity and pour point (or cloud point); conversely, it can be higher.
Mechanical temperature: If the working temperature of the machinery is high, select a lubricant with relatively high viscosity, high flash point, and good oxidation stability.
Presence of water: In humid environments and working conditions with more contact with water, select a lubricant with strong anti - emulsification and good rust - prevention properties.
Precision level: For equipment with precision components such as servo valves, high - cleanliness oil products are required.
Replacement difficulty: For equipment that is very troublesome to replace, it is best to use synthetic lubricants with a long service life.
Mechanical material: Check if there are active metal materials such as copper and silver to ensure that the oil product will not cause oxidation and rust of the components.
Lubrication device: See what type and viscosity of oil the lubrication device of the equipment is suitable for. Both too high and too low viscosities may lead to poor results.
The Price of Additives for industrial lubricant
The price of Additives for industrial lubricant depending on factors such as brand, specification, composition, and sales channels. If you are interested in Additives for industrial lubricant, please feel free to contact us.
Supplier of Additives for industrial lubricant
UNPChemicalsis a professional supplier of high-quality and effective Additives for industrial lubricant. We offer several remarkable products, namely Tolyltriazole derivatives CSUM 4200,Thiadiazole derivatives CSUM 5202,Siloxane ketone oligomer CSUM 8150,etc.
CSUM 4200is a Tolyltriazole derivatives (TTA), water-soluble copper corrosion inhibitor, that is soluble in water and ethylene glycol systems. It is designed to function as a metal deactivator and provides an effective alternative to solid benzotriazole and methyl benzotriazole. CSUM 4200 can efficiently protect yellow metals and prevent cobalt from spilling. Its effectiveness can be enhanced when used in combination with carboxylate-based anti-rust agents, such as ternary carboxylic acid, resulting in comprehensive corrosion protection for a wide range of metals.
CSUM 5202 is a completely water-soluble thiadiazole derivative that offers various advantages, such as low viscosity, high water solubility, and exceptional extreme pressure performance. It is specifically designed to improve the extreme pressure capacity of water-soluble metalworking fluids, making it particularly suitable for fully synthetic metalworking fluids or low oil content semi-synthetic metalworking fluids used in demanding metalworking processes. With its unique characteristics and compatibility with different water-based metalworking systems, CSUM 5202 has become a popular choice as a substitute for extreme pressure emulsions.
CSUM 8150is a complex product of siloxane oligomer, also known as siloxane ketone, formed by hydrolysis and condensation of various special silanes. It is a water-based aluminum corrosion inhibitor with exceptional performance and an affordable price. CSUM 8150 can be completely dissolved in water and is soluble in alcohol, acetone, as well as most aliphatic and ester groups. Mainly used for corrosion inhibition of aluminum in water-based environments, CSUM 8150 also offers outstanding corrosion inhibition for soldering tin, reducing its corrosion in water environments.
Professional Lubricant Additive Manufacturer
UNPChemicals, aka Luoyang Pacific United Petrochemical Co., Ltd., focuses on the application and development of special lubricating grease additives such as MODTC, MODTP, molybdenum amide, thiadiazole metal deactivators, and phosphate esters. With nearly 30 products in seven series, including extreme pressure anti-wear additives and special grease additives, it is a global manufacturer of special lubricating grease additives and a national high-tech enterprise with great influence and leading role in the industry. If you are looking for Additives for industrial lubricant or technical information, feel free to contact UNPChemicals.