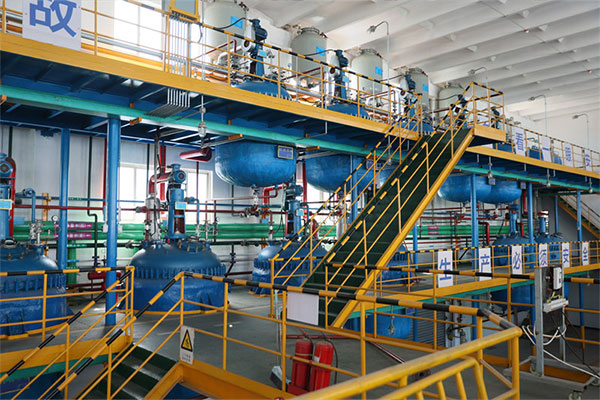
Grease Additive Packages Manufacturing Process
Grease Additive Packages are essential formulations designed to enhance the performance, stability, and longevity of lubricating greases. These packages typically contain various functional additives, including antioxidants, anti-wear agents, extreme pressure agents, rust inhibitors, and thickeners improvers. As a leading manufacturer of grease additive packages, UNPChemicals is dedicated to providing high-quality, customized solutions for a wide range of industrial applications. This article outlines the complete manufacturing process of Grease Additive Packages, emphasizing the critical steps that determine their quality and performance.Raw Material Selection
The selection of raw materials is a fundamental step in the production of grease additive packages. Ensuring the quality and compatibility of these materials is crucial for producing high-performance additive packages.
Antioxidants: Such as phenolic and amine-based antioxidants to prevent oxidation and thermal degradation.
Anti-wear Agents: Commonly used additives include zinc dialkyldithiophosphate (ZDDP) and molybdenum disulfide (MoS₂) to enhance wear protection.
Extreme Pressure (EP) Agents: Sulfur-phosphorus compounds, chlorinated paraffins, and borate esters designed to protect surfaces under heavy load conditions.
Rust and Corrosion Inhibitors: Organic and inorganic compounds that form protective films on metal surfaces to prevent corrosion.
Viscosity Modifiers & Thickeners Improvers: To ensure consistent grease structure and performance across a wide temperature range.
UNPChemicals uses only high-quality, certified raw materials to ensure excellent performance, stability, and compatibility with various grease formulations.
Formulation Design and Optimization
Developing an effective grease additive package requires precise formulation design and optimization, taking into account the target application, base grease type, and expected operating conditions.
Additive Synergy: Carefully selecting and balancing various additives to achieve desired properties such as oxidation resistance, anti-wear performance, extreme pressure protection, and corrosion inhibition.
Formulation Compatibility: Ensuring that the additives are compatible with different base greases (e.g., lithium, calcium, aluminum complex, polyurea, etc.) without causing separation or instability.
Performance Tuning: Utilizing laboratory testing, field trials, and computational modeling to optimize the formulation for specific applications.
Customized Solutions: UNPChemicals offers tailor-made grease additive packages to meet specialized requirements, ensuring superior performance under demanding conditions.
Pre-Mixing and Dosing
Once the formulation design is completed, precise dosing and pre-mixing of additives are essential steps to ensure homogeneity and stability.
Accurate Weighing and Dosing: Each raw material is measured according to the optimized formulation, with tight tolerances to prevent formulation errors.
Pre-Mixing Tanks: Additives are blended in dedicated pre-mixing tanks to achieve initial uniform dispersion.
Dissolution and Heating: High-viscosity or solid additives may require pre-heating or dilution to enhance their solubility and dispersion during subsequent mixing.
Blending and Homogenization
The core blending process involves thorough mixing of all components to achieve a homogeneous and stable product.
High-Shear Mixing: High-speed mixers are employed to uniformly disperse additives throughout the grease formulation.
Temperature Control: The blending process is usually conducted at controlled temperatures between 40°C and 80°C, depending on the nature of the additives.
Homogenization: Additional homogenization steps are performed to prevent phase separation and ensure consistent particle distribution.
Quality Control and Testing
Rigorous quality control is essential to ensure the additive packages meet the required performance standards.
Physical Testing: Assessing properties such as viscosity, penetration, dropping point, and oil separation.
Chemical Analysis: Measuring the concentration of active ingredients and monitoring for contaminants.
Performance Evaluation: Conducting oxidation stability tests, anti-wear performance tests, corrosion resistance tests, and extreme pressure tests.
Compatibility Testing: Ensuring the additive package is compatible with various base greases and meets the specific requirements of different applications.
UNPChemicals employs advanced analytical techniques and comprehensive testing protocols to guarantee product quality and consistency.
Filtration and Packaging
Once the product passes all quality control tests, it proceeds to filtration and packaging.
Fine Filtration: Ensuring that any solid particles or impurities are removed from the final product.
Packaging and Labeling: The finished product is carefully packaged into sealed drums, containers, or bulk storage tanks, with clear labeling for identification and traceability.
Storage Conditions: Proper storage under controlled conditions (e.g., cool, dry, and protected from direct sunlight) to maintain product stability and performance.
Storage and Logistics
The safe and efficient transportation of grease additive packages is critical to maintaining product quality.
Shipping Compliance: Following all relevant regulations for the transportation of chemical products.
Logistics Management: Ensuring timely and reliable delivery to customers.
Conclusion
The manufacturing process of Grease Additive Packages involves a complex series of steps, from raw material selection and formulation design to blending, testing, and packaging. By adhering to stringent quality standards and utilizing advanced manufacturing techniques, UNPChemicals consistently provides high-performance grease additive packages that meet the specific needs of industrial clients worldwide. For customized solutions and detailed specifications, feel free to contact us