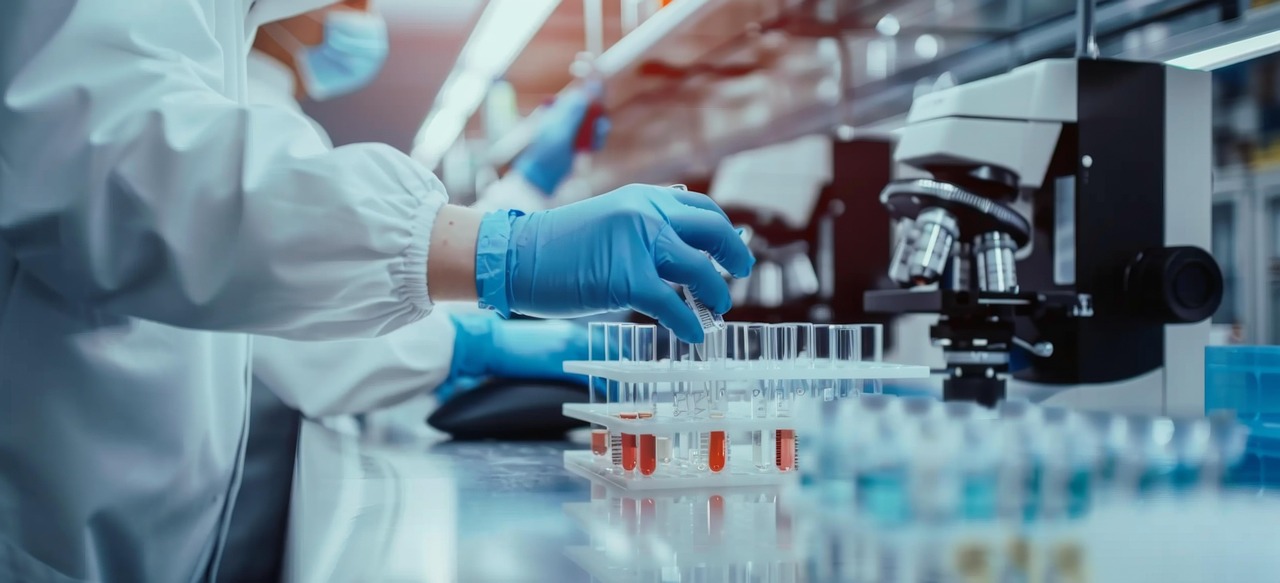
Gear Wear and the Mitigating Effect of Compound Agents
The gear transmission system, as a core component in mechanical equipment, directly affects the service life and operational efficiency of the equipment. However, gear wear is inevitable during operation, and the design and application of lubricating compound agents have become crucial means to alleviate wear and enhance the durability of gears. This article will conduct a detailed analysis and elaboration from four aspects: the gear wear mechanism, the design of lubricating compound agents, performance testing methods, and their mitigating effects.
I. Analysis of the Gear Wear Mechanism
Gear wear is a complex multi-physical field coupling process involving the interaction of material physics, chemical kinetics, and tribological behavior. The following analysis is carried out from four main types of wear:
1. Adhesive Wear
Adhesive wear occurs in the high-pressure contact of the micro-asperities on the tooth surface, and its process can be divided into three stages: Firstly, under heavy load conditions, the lubricating oil film ruptures due to the inability to withstand the Hertz contact stress as high as 1.5-3 GPa. Secondly, the metal surfaces come into direct contact, and atomic diffusion occurs to form adhesive junctions. Finally, the tangential force causes the adhesive junctions to shear and break, and part of the material is transferred to the mating surface. This type of wear is particularly significant at higher sliding speeds (such as in hypoid gears), and the wear rate is proportional to the 0.7th power of the sliding speed and the 1.2th power of the contact stress. Local high temperatures (400-800°C) further intensify the plastic deformation and phase transformation of the material.
2. Abrasive Wear
Abrasive wear is caused by external particles or wear debris, and its dynamic behavior is affected by the Reynolds number. When the particle diameter is larger than the thickness of the lubricating oil film (h < 2d), the particles embed in the tooth surface, forming three-body wear. Experiments have shown that quartz sand particles with a diameter of 10-50 μm can increase the wear rate by 3-5 orders of magnitude, and directional furrows with a depth of 5-15 μm appear on the tooth surface, and the surface roughness Ra value increases from 0.8 μm to more than 3.2 μm. This type of wear not only damages the geometric accuracy of the tooth surface but also accelerates subsequent fatigue failure.
3. Fatigue Wear
Fatigue wear originates from the initiation and propagation of cracks under cyclic stress and follows Paris' law (da/dN = C(ΔK)^m). For carburized steel gears, cracks often originate from non-metallic inclusions at a subsurface depth of 0.1-0.3 mm. Under the action of the maximum shear stress, the cracks propagate to a critical length, and finally, the surface spalls to form pitting pits (with a diameter of 0.5-2 mm). This process is closely related to the service life cycle of the gear and is the main failure mode of heavy-duty long-life gears.
4. Corrosive Wear
Corrosive wear is driven by electrochemical reactions and is particularly severe in environments containing Cl⁻. The critical potential for pitting on the tooth surface is approximately -0.4 V (SCE), and the generated corrosion products (such as Fe₂O₃·nH₂O, with a Mohs hardness of 5-6) act as secondary abrasive particles, further intensifying the wear. This synergistic effect increases the material loss rate by 2-3 times, especially in wet or acidic working conditions.
II. Design of Gear Lubricating Compound Agents
Aiming at the above wear mechanisms, the lubricating compound agent needs to improve the gear performance through a multi-scale synergistic protection system. Its design is carried out from two aspects: the selection of base oil and the combination of additives:
1. Selection of Base Oil
The base oil needs to meet the viscosity classification requirements of GB/T 3141. For closed gear transmissions, oils with a viscosity grade of ISO VG 220 or above are recommended. Synthetic ester oils (such as trimethylolpropane trioctanoate) are preferred due to their excellent boundary lubrication performance (reducing the friction coefficient by 18-25%). Bio-based oils (such as rapeseed oil) have a long oxidation induction period (IP 48 can reach 300 min), but 0.3-0.5% of antioxidant (such as BHT) needs to be added to improve thermal stability.
2. Design of Additive Compatibility
The optimization of the additive formula uses the Response Surface Methodology (RSM). Experiments have shown that the optimal mass ratio of the sulfur-based extreme pressure agent (T321) to the phosphorus-based anti-wear agent (T306) is 2.5:1, and the sintering load (PB value) can reach 1500 N. Nano-copper particles (with a particle size of 20-50 nm and an addition amount of 0.05%) fill the microscopic pits and form a transfer film, reducing the wear scar diameter (WSD) by 32%.
3. Action Mechanism of Functional Additives
ZDDP (zinc dialkyldithiophosphate): It decomposes at 150-250°C to form ZnS and Zn₃(PO₄)₂, forming a glassy protective film with a thickness of 10-20 nm, significantly reducing friction and wear.
Borate: When compounded with ZDDP, it forms a B₂O₃ glass layer, increasing the contact resistance by 2 orders of magnitude and inhibiting electrochemical corrosion.
Ionic liquid: Such as [BMIM][PF6], it forms an electric double layer through electrostatic adsorption, and the friction coefficient is reduced to below 0.05, which is suitable for extreme working conditions.
III. Performance Testing Standards and Methods for Compound Agents
The performance evaluation of the compound agent needs to meet the classification requirements of ISO 6743-6, and the testing system includes four levels: basic performance, tribological performance, working condition simulation, and characterization techniques:
1. Basic Performance Testing
High-temperature oxidation stability: ASTM D943 rotating oxygen bomb method (150°C, 620 kPa), and the oxidation life needs to be ≥ 300 min.
Low-temperature fluidity: The apparent viscosity at -40°C is measured by a Brookfield viscometer, and the requirement is ≤ 15000 mPa·s.
Foam characteristics: According to the ASTM D892 standard, the volume of first-level foam < 100 mL, and the defoaming time < 10 min.
2. Tribological Performance Testing
SRV tester: Under the conditions of 500 N, 50 Hz, and an amplitude of 1 mm, the wear volume of the optimized formula ≤ 0.2 mm³.
Timken OK tester: According to the ASTM D2782 standard, the OK value ≥ 50 lb.
Gear contact fatigue test: ISO 10825, Hertz stress of 1.2 GPa, and the pitting rate ≤ 3% after 10⁷ cycles.
3. Working Condition Simulation Technology
Variable load strengthening test: Simulate the impact load of mining machinery (0-100% rated load, cycle of 30 s), and the acid value increase < 0.5 mgKOH/g after 500 hours.
Wet and heat aging test: At 85°C and 95% humidity, the copper strip corrosion ≤ Grade 1 after 1000 hours.
Dispersibility of nanoparticles: The average particle size measured by dynamic light scattering (DLS) < 100 nm, and the Zeta potential > 30 mV.
4. Characterization Techniques
XPS depth profiling: Ar⁺ ion sputtering shows that the P element in the ZDDP film layer reaches a peak value at a depth of 20 nm.
AFM surface morphology: The nano-MoS₂ additive reduces the roughness by 40% and forms a smooth transfer film with a thickness of 5-8 nm.
Oil ferrography analysis: The oil needs to be replaced when the wear index (WIP) exceeds 150.
IV. Summary of the Mitigating Effect of Compound Agents on Gear Wear
1. Quantification of Protection Effect
The compound agent containing 1.2% ZDDP, 0.5% sulfurized olefins, and 0.3% nano-graphene increases the gear fatigue life by 2.8 times, and the failure load in the FZG test reaches Level 12 (40% higher than the traditional formula).
2. Engineering Application Cases
After a port crane's main reducer uses the new compound agent, the tooth surface wear rate is reduced from 0.15 μm/h to 0.05 μm/h, the oil change cycle is extended from 2000 hours to 5000 hours, and the vibration acceleration is reduced from 1.2 m/s² to 0.7 m/s².
3. Technical Bottlenecks and Breakthrough Directions
Phosphorus-free formula: Develop derivatives of benzotriazole (BTA), and increase the thermal decomposition temperature to 320°C.
Intelligent self-healing: Use microcapsule technology to release nano-copper particles for in-situ repair of wear.
4. Future Prospects
Gear lubricants will develop in the directions of functional diversification (anti-wear, anti-corrosion, conductivity), intelligent response (dynamic adjustment of performance), and environmental friendliness (the proportion of bio-based raw materials > 50%), providing reliable guarantees for high-end equipment.
Through in-depth analysis of the gear wear mechanism and scientific design of the compound agent, various types of wear can be effectively alleviated, and the reliability and service life of the gear transmission system can be improved. Future technological breakthroughs will further promote the intelligence and greening of lubricants, bringing broader application prospects to the industrial field.
The Price of Additive Packages
The price of Additive Packages varies depending on factors such as brand, specification, composition, and sales channels. If you are interested in Additive Packages, please feel free to contact us.
Supplier of Additive Packages
UNPChemicals is a professional supplier of high-quality and effective Additive Packages. We offer several remarkable products, namely Industrial Gear Oil Additives UNP IG402A,High extreme pressure (EP) type industrial gear oil additive packages UNP IG402B,Low-Odor Type Industrial Gear Oil Additive Package UNP IG402C,etc.
Industrial Gear Oil Additives UNP IG402Aare a specialized class of compounds designed to enhance the performance of gear oils in various industrial applications.These additives are carefully formulated to provide a combination of properties that improve the efficiency,longevity,and reliability of gear systems.
High extreme pressure (EP) type industrial gear oil additive packages, like UNP IG402B, are specialized blends of chemical compounds designed to enhance the performance of base oils used in industrial gear lubricants. These packages are formulated to provide exceptional protection under conditions where gears experience heavy loads, high pressures, and potential metal-to-metal contact.
The Low-Odor Type Industrial Gear Oil Additive Package UNP IG402C is a specialized blend of chemical additives designed to enhance the performance of industrial gear oils while minimizing the strong odors typically associated with traditional gear oil additives, particularly those containing sulfur-based extreme pressure (EP) agents. This additive package is mixed with base oils (mineral or synthetic) to create gear lubricants that protect industrial gearboxes under demanding conditions, such as high loads and temperatures, while being more user-friendly in terms of smell—ideal for environments where odor control is a priority.
Professional Lubricant Additive Manufacturer
UNPChemicals, aka Luoyang Pacific United Petrochemical Co., Ltd., focuses on the application and development of special lubricating grease additives such as MODTC, MODTP, molybdenum amide, thiadiazole metal deactivators, and phosphate esters. With nearly 30 products in seven series, including extreme pressure anti-wear additives and special grease additives, it is a global manufacturer of special lubricating grease additives and a national high-tech enterprise with great influence and leading role in the industry. If you are looking for Lubricant Additive or technical information, feel free to contact UNPChemicals.