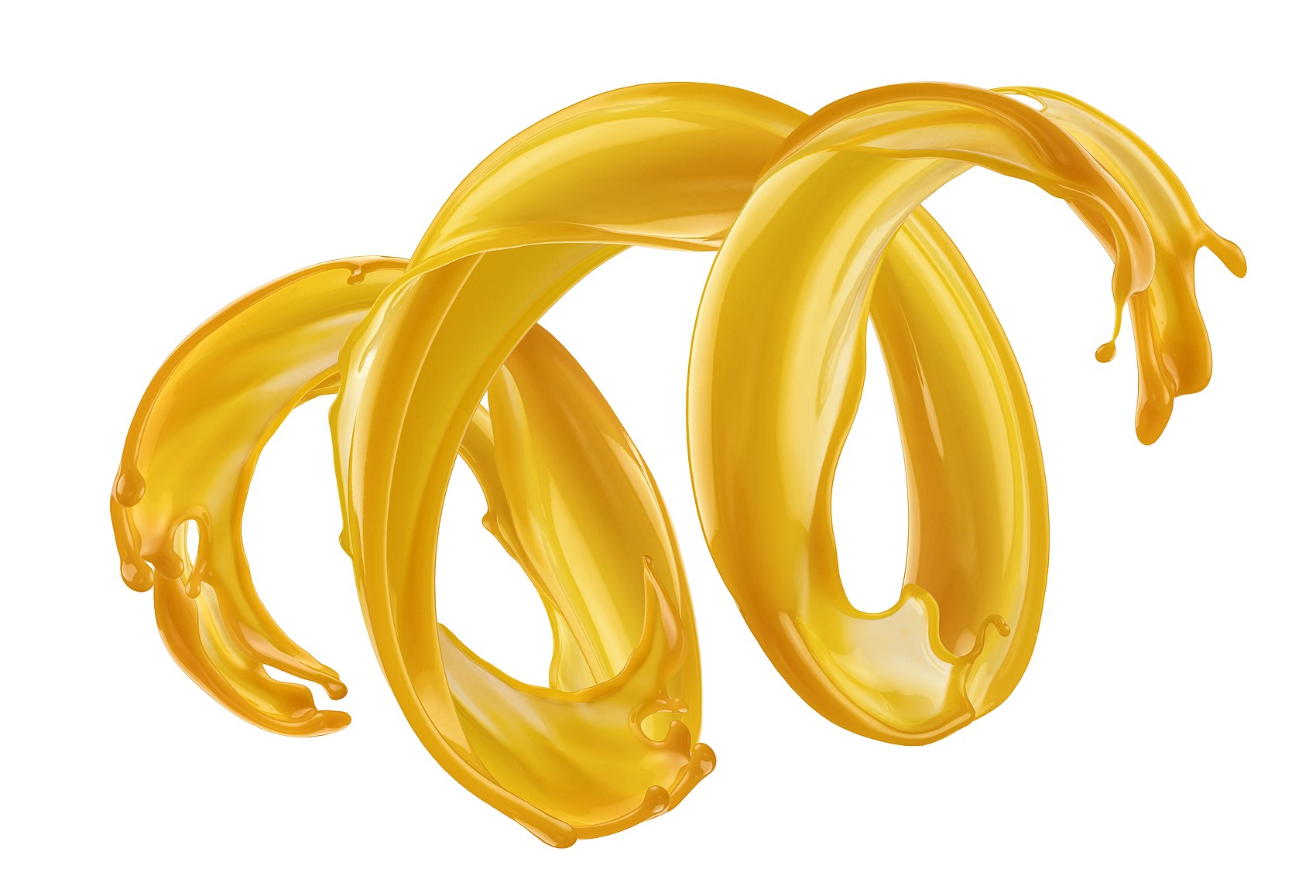
Gear Transmission and Industrial Gear Lubricants
I. Characteristics of Gear Transmission
(1) High Transmission Efficiency
Gear transmission exhibits outstanding efficiency among various mechanical transmission forms, usually reaching 95% - 99%. This is mainly due to its direct meshing transmission method. During power transmission, energy losses are mainly concentrated in areas such as tooth surface friction and bearing operation friction. Compared with methods like belt transmission, gear transmission has no slipping phenomenon, effectively reducing energy losses. This enables more efficient power transmission, giving full play to the effectiveness of the power source and significantly reducing energy consumption costs in industrial production.
(2) Stable Transmission Ratio
Once the module and number of teeth of a gear are determined, its transmission ratio is fixed and not affected by fluctuations in working conditions. This stable transmission ratio characteristic makes gear transmission the first choice for equipment with strict requirements for speed ratio accuracy. For example, in the transmission system of a precision machine tool, the stable transmission ratio ensures the precise movement relationship between the tool and the workpiece, thus guaranteeing the consistency and stability of machining accuracy and providing a solid guarantee for the production of high - quality parts.
(3) Reliable Operation and Long Service Life
A scientifically designed and precisely manufactured gear transmission system has a high degree of reliability and a long service life under normal operating conditions that meet the working conditions. Its compact structure can withstand large loads. This is because gear materials are mostly high - strength alloy steels, and through heat treatment processes such as quenching and carburizing, the tooth surface hardness and wear resistance are greatly improved. At the same time, reasonable tooth profile design and lubrication measures further extend the service life of the gear, reducing equipment maintenance and replacement frequencies and lowering production operation costs.
(4) Wide Application Range
Gear transmission has extremely strong adaptability and can operate under various working conditions. Whether it is low - speed and heavy - load metallurgical and mining machinery or high - speed and light - load aerospace equipment, a suitable gear transmission solution can be found. Moreover, it is not only applicable to the transmission between parallel axes but also widely used in the transmission between intersecting axes (such as bevel gear transmission) and non - intersecting axes (such as worm and worm gear transmission), meeting the diverse transmission requirements of complex mechanical systems and becoming an indispensable key transmission component in modern mechanical equipment.
II. Lubrication Characteristics of Closed - type Gears
(1) Diverse Lubrication Methods
The common lubrication methods for closed - type gear transmission are mainly bath lubrication and spray lubrication. Bath lubrication is simple to operate and has a low cost. Part of the gear is immersed in the oil sump, and when the gear rotates, it will carry the lubricating oil to the tooth surface to achieve lubrication. It is suitable for working conditions where the circumferential speed is generally below 12 - 15m/s. Spray lubrication, on the other hand, uses an oil pump to spray the lubricating oil onto the tooth surface at a specific pressure. This method is suitable for occasions with a high circumferential speed. It can quickly and effectively deliver the lubricating oil to the tooth surface, and at the same time, it can play a good cooling role on the tooth surface, effectively reducing the tooth surface temperature and reducing thermal deformation and wear.
(2) High Requirements for Lubricating Oil Cleanliness
Since the closed - type gearbox is a relatively closed space, the lubricating oil is recycled in the box. If impurities such as metal debris and dust are mixed into the lubricating oil, it will exacerbate tooth surface wear during the gear meshing process and greatly shorten the service life of the gear. Therefore, closed - type gear transmission systems usually install high - precision filters in the lubricating oil circuit to strictly filter the lubricating oil, ensure its cleanliness, maintain a good lubrication state, and guarantee the smooth operation of the gear transmission.
(3) Good Sealing Performance
To prevent lubricating oil leakage from causing lubrication failure and the intrusion of external impurities, moisture, etc. from contaminating the lubricating oil, the closed - type gearbox must have good sealing performance. Usually, various sealing methods such as sealants and sealing rings are used to effectively seal the various joint surfaces, shaft extensions, and other parts where leakage may occur in the gearbox, maintain the normal liquid level and quality of the lubricating oil in the box, and ensure that the gear transmission system works in a clean and stable lubrication environment.
III. Lubrication Characteristics of Open - type Gears
(1) Harsh Lubrication Conditions
Open - type gears are directly exposed to the external environment and are easily contaminated by dust, moisture, impurities, etc. At the same time, the heat dissipation conditions are poor, and the tooth surface temperature is relatively high during operation, making lubrication more difficult. These unfavorable factors make the wear rate of open - type gears relatively fast, and the requirements for lubrication are more urgent and special.
(2) Mostly Use High - viscosity Lubricants
In order to maintain good lubrication effects under harsh working conditions, open - type gears usually use high - viscosity lubricants. High - viscosity lubricants can form a relatively thick oil film on the tooth surface, resist the intrusion of external impurities, and have good adhesion, making it difficult to be thrown off or washed away, thus providing long - lasting lubrication protection for the gears.
(3) Regular Manual Application or Spray Lubrication
Due to the structural characteristics of open - type gears, it is difficult to achieve the automatic circulation lubrication like that of closed - type gears. Generally, lubrication is carried out by regularly applying or spraying lubricants manually. This lubrication method requires strict operation according to the specified time interval and lubricant dosage to ensure that the gears are always in a good lubrication state. At the same time, it also puts forward high requirements for the professional skills and sense of responsibility of the operators.
IV. Classification of Gear Oils
Classification | Details |
Standard | The GB/T76317 - 1995 gear oil classification standard is formulated by equivalently adopting ISO/6743 - 6:1990. It is divided into industrial closed - type gear oil, industrial open - type gear oil, and vehicle gear oil. |
Industrial Gear Oil | Purpose: Mainly used for the gears of industrial equipment, formulated from base oil and additives. Base Oil: Mostly paraffin - based base oil, blended with heavy bright stock and light neutral oil. Additives: Viscosity index improver, demulsifier, pour point depressant, antifoaming agent, friction modifier, extreme - pressure anti - wear agent, rust inhibitor, antioxidant, etc. |
Industrial Closed - type Gear Oil | Lubrication Occasion Classification: Divided into continuous lubrication and continuous splash lubrication occasions. Continuous Lubrication (by splash, circulation or spraying) Varieties: CKB, CKC, CKD, CKE, CKS, CKT (The second letter 'K' is introduced to avoid confusion with diesel engine oil). Continuous Splash Lubrication Variety: CKG. Characteristics of CKB: Refined mineral oil, with anti - oxidation, anti - corrosion (for both ferrous and non - ferrous metals) and anti - foaming properties. Characteristics of CKC: Based on CKB oil, with improved extreme - pressure and anti - wear properties. Characteristics of CKD: Based on CKC oil, with improved thermal/oxidative stability, enabling use at higher temperatures. Characteristics of CKE: Based on CKB oil, with a low friction coefficient. Characteristics of CKS: A lubricant used under extremely low and high temperature conditions, with anti - oxidation, anti - friction and anti - corrosion (for both ferrous and non - ferrous metals) properties. Characteristics of CKT: A CKS - type lubricant under extremely low and high temperatures and heavy loads. Characteristics of CKG: Lubricating grease with extreme - pressure and anti - wear properties. |
Industrial Open - type Gear Oil | GB/T 76317 - 1995 Classification: Industrial open - type gears equipped with safety baffles, for intermittent, immersion or mechanical applications, are divided into three varieties: CKH, CKJ, CKL; for intermittent applications, it is divided into one variety: CKM. Characteristics of CKH: Usually an asphalt - type product with anti - corrosion properties. Characteristics of CKJ: Based on CKH - type products, with improved extreme - pressure and anti - wear properties. Characteristics of CKL: Lubricating grease with improved extreme - pressure, anti - wear, anti - corrosion and thermal stability. Characteristics of CKM: Products that allow use under extreme loads, with improved anti - scuffing properties and anti - corrosion properties. |
V. What is Industrial Gear Oil?
Industrial gear oil is a lubricating oil specially designed for various industrial gear transmission devices. Its base oil is usually composed of mineral oil, synthetic oil, or a mixture of both. Mineral oil has a wide source and a relatively low cost, with certain lubrication performance; synthetic oil performs more outstandingly in terms of high - and low - temperature performance, oxidation resistance, and anti - wear performance, and is suitable for gear transmission systems with complex working conditions and harsh requirements. In addition, industrial gear oil is added with a variety of functional additives to meet the lubrication needs of gear transmission under different working conditions, and it is a key lubricating material to ensure the normal operation of industrial gear equipment.
VI. Functions of Industrial Gear Oil
(1) Lubrication and Friction Reduction
During the gear meshing process, industrial gear oil forms an oil film between the tooth surfaces, separating the metal surfaces, greatly reducing the friction coefficient between the tooth surfaces, reducing wear and energy losses, and making the gear transmission more stable and efficient.
(2) Cooling and Heat Dissipation
Gears generate heat due to friction during operation. Industrial gear oil can absorb and carry away this heat, and dissipate the heat through a circulating cooling system, effectively reducing the working temperature of the gears, preventing the occurrence of failure forms such as tooth surface gluing and annealing due to overheating, and extending the service life of the gears.
(3) Rust and Corrosion Prevention
The rust inhibitors and anti - corrosion agents in industrial gear oil can form a protective film on the gear metal surface, preventing moisture, oxygen, and other corrosive media from coming into contact with the metal, preventing the gears from rusting and corroding, and ensuring that the gears can still maintain good performance in harsh working environments.
(4) Cleaning and Dispersion
The detergent - dispersants in industrial gear oil can disperse the wear particles, impurities, etc. generated during the gear operation in the oil, prevent them from accumulating on the tooth surface, avoid causing abrasive wear, and at the same time filter out these impurities through a filter to maintain the cleanliness and lubrication performance of the lubricating oil.
VII. Lubrication Requirements for Industrial Gear Oil
(1) Appropriate Viscosity
Viscosity is one of the important performance indicators of industrial gear oil. It is necessary to select gear oil with an appropriate viscosity according to the type of gear, working conditions (such as speed, load, temperature, etc.). If the viscosity is too low, the oil film thickness is insufficient, making it difficult to effectively bear the load, and easily leading to tooth surface wear and gluing; if the viscosity is too high, it will increase power loss and starting resistance, and at the same time affect the fluidity and heat dissipation effect of the lubricating oil. Generally, high - viscosity gear oil should be selected for low - speed and heavy - load, high - temperature working conditions, while low - viscosity gear oil is suitable for high - speed and light - load, low - temperature working conditions.
(2) Good Anti - wear Performance
During the gear meshing process, the tooth surfaces bear large pressure and friction, and are prone to wear. Therefore, industrial gear oil must have good anti - wear performance, be able to form a tough protective film on the tooth surface, effectively resist wear, and ensure the normal meshing and service life of the gears.
(3) Excellent Oxidation Resistance
During the gear transmission process, the lubricating oil may oxidize and deteriorate due to factors such as contact with air, heat, and metal catalysis. After oxidation, the viscosity of the gear oil increases, the acid value rises, and precipitates and varnishes are generated, reducing the lubrication performance and even corroding the gears. Therefore, industrial gear oil needs to have excellent oxidation resistance and be able to maintain stable chemical properties and lubrication performance for a long time.
(4) Demulsibility
When the gear oil comes into contact with water, it should have good demulsibility and be able to quickly separate the water to avoid the formation of an emulsion. The lubrication performance of emulsified gear oil is greatly reduced, and it is likely to cause increased metal corrosion and wear. Therefore, demulsibility is particularly important for gear transmission systems working in humid environments or those that may come into contact with water.
VIII. Selection of Industrial Gear Oil Additives
(1) Anti - wear Additives
Anti - wear additives are indispensable components in industrial gear oil. Common types include sulfur - phosphorus type and sulfur - nitrogen type. Sulfur - phosphorus type anti - wear additives can chemically react with the tooth surface metal under high temperature and high pressure to form a chemical reaction film, effectively reducing the friction coefficient of the tooth surface and reducing wear. When selecting anti - wear additives, it is necessary to reasonably match them according to the working conditions and load of the gears to ensure good anti - wear protection under different working conditions.
(2) Extreme - pressure Additives
Extreme - pressure additives are mainly used to meet the gear lubrication requirements under extreme working conditions such as heavy loads and impact loads. Common extreme - pressure additives include chlorine - containing, phosphorus - containing, sulfur - containing compounds, etc. These additives can chemically react with the tooth surface metal under extreme - pressure conditions to generate a reaction film with low shear strength, preventing tooth surface gluing and scuffing. When selecting extreme - pressure additives, it is necessary to fully consider their compatibility with the base oil and other additives, as well as their impact on the environment.
(3) Antioxidant Additives
Antioxidant additives can inhibit the oxidation process of gear oil and extend its service life. Common antioxidant additives include phenolic and amine types. Phenolic antioxidant additives have good anti - oxidation effects and thermal stability, and are relatively low in toxicity; amine - type antioxidant additives have more outstanding antioxidant performance at high temperatures. In practical applications, phenolic and amine - type antioxidant additives are usually used in combination to achieve the best antioxidant effect.
(4) Rust - inhibiting Additives
The function of rust - inhibiting additives is to prevent the gear metal from rusting. Common rust - inhibiting additives include petroleum sulfonates, fatty acids and their soaps, etc. These additives can form an adsorption film or chemical reaction film on the metal surface, preventing moisture and oxygen from coming into contact with the metal, thus playing a rust - preventing role. When selecting rust - inhibiting additives, it is necessary to consider their rust - preventing effects in different environmental conditions and their compatibility with other additives.
(5) Antifoaming Additives
Antifoaming additives are used to eliminate the foam generated during the circulation of gear oil. The presence of foam will affect the normal circulation and lubrication effect of the lubricating oil, reduce the oil film strength, and lead to increased tooth surface wear. Silicone - based antifoaming additives are commonly used antifoaming agents. They can reduce the surface tension of the foam, causing the foam to burst quickly. When adding antifoaming additives, it is necessary to pay attention to controlling their addition amount to avoid affecting other properties of the gear oil due to excessive addition.
The Price of EP/AW additives
The price of EP/AW additives depending on factors such as brand, specification, composition, and sales channels. If you are interested in EP/AW additives, please feel free to contact us.
Supplier of EP/AW additives
UNPChemicalsis a professional supplier of high-quality and effective EP/AW additives. We offer several remarkable products, namely Amine-neutralized hexyl phosphate PSAIL 3490,Amine-neutralized mixed phosphate Esters PSAIL 2280,Phosphorothioate acrylate derivatives PSAIL 3530,etc.
Amine-neutralized hexyl phosphate PSAIL 3490 is a specialized mixture of amine phosphate salts known for its multifunctional ashless additive characteristics. As an ashless additive, PSAIL 3490 does not produce ash as combustion by-products, reducing engine deposits and harmful emissions. PSAIL 3490 is a multifunctional additive, providing a range of benefits in a single product, making it highly versatile and cost-effective.
Amine-neutralized mixed phosphate esters PSAIL 2280 is a multifunctional ashless additive structured as a phosphate ester amine salt with excellent load carrying capacity, anti-wear and corrosion protection properties. As a multifunctional additive, PSAIL 2280 reduces the amount of anti-emulsifier and rust inhibitor and has good tribological properties, especially at higher temperatures, forming thicker boundary lubricant films. In addition, PSAIL2280 is widely used in metalworking fluid formulations in conjunction with sulfur carriers because of its good anti-wear properties.
Phosphorothioate Acrylate Derivatives PSAIL 3530 is an ashless EP/AW additive with dialkyl dithiophosphate structure, especially suitable for industrial lubricating oils with FZG test requirements, such as industrial gear oil, anti-wear hydraulic oil containing ZDDP, lubricating grease and metal processing oil.
Professional Lubricant Additive Manufacturer
UNPChemicals, aka Luoyang Pacific United Petrochemical Co., Ltd., focuses on the application and development of special lubricating grease additives such as MODTC, MODTP, molybdenum amide, thiadiazole metal deactivators, and phosphate esters. With nearly 30 products in seven series, including extreme pressure anti-wear additives and special grease additives, it is a global manufacturer of special lubricating grease additives and a national high-tech enterprise with great influence and leading role in the industry. If you are looking for Lubricant Additive or technical information, feel free to contact UNPChemicals.