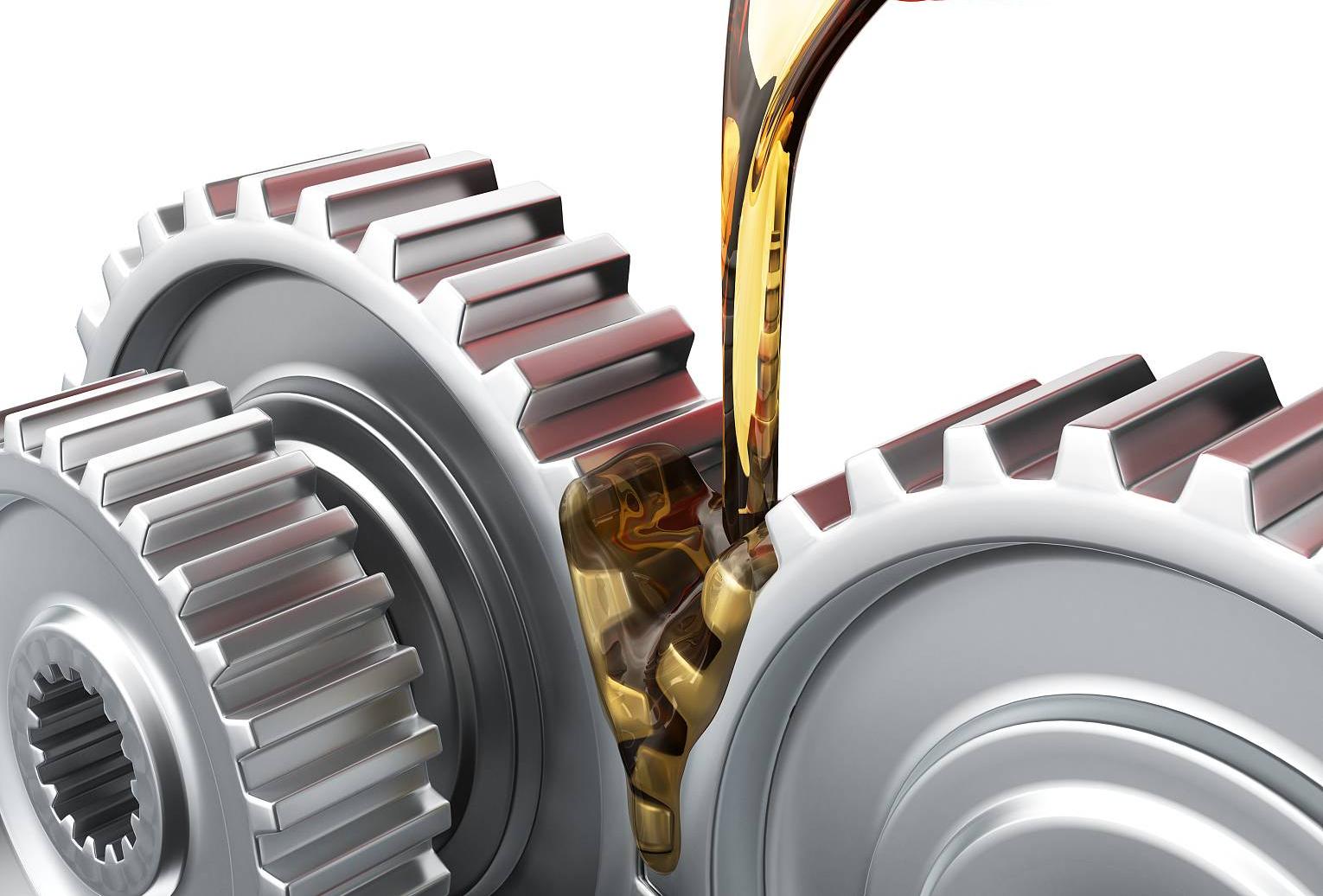
Friction Modifiers in Gear Oil: Balancing Efficiency and Wear Resistance
Friction in Gear Systems
Gear systems are one of the most common and widely used forms of mechanical transmission. They play an irreplaceable role in various fields such as automotive transmissions, industrial gearboxes, aerospace equipment, and marine power systems. During the operation of gear transmission, friction, as a ubiquitous physical phenomenon, is both a fundamental condition for the normal operation of the gear system and an important factor affecting its performance and service life. The friction in gear systems mainly occurs in the meshing area between the gear teeth and at the contact interfaces between the gears and related components such as bearings and shafts. These frictional forces are directly related to the energy transfer efficiency of the system, the degree of component wear, and the overall service life.
Friction in gear systems has a dual nature. On the positive side, moderate friction is a prerequisite for gear transmission. Gears achieve meshing through the frictional force between their tooth surfaces, thus transmitting power from one shaft to another and ensuring the normal operation of the mechanical system. However, on the negative side, excessive friction leads to significant energy losses. These losses are usually manifested in the form of heat, which not only reduces the transmission efficiency of the gear system but also accelerates the wear of the gear surface due to high temperatures, and may even cause material fatigue or local failure. In addition, friction can also cause damage such as scratches, pitting, or spalling on the gear surface, further shortening the service life of the gears.
In practical applications, gear systems often need to operate under different working conditions, such as high loads, high speeds, or extreme temperature environments. These harsh conditions amplify the negative impacts of friction, making the problems of energy loss and wear more prominent. Therefore, a deep understanding of the generation mechanism of friction in gear systems and its influencing factors, and the adoption of effective control measures have become key issues for improving gear performance and extending their service life. In this context, gear oil, as the core lubricating medium of the gear system, its performance directly determines the control effect of frictional forces. And the friction modifiers added to gear oil have become an important technical means to optimize frictional characteristics and achieve a balance between efficiency and wear resistance.
Friction Modifiers: Working Principles and Applications
2.1 Working Principles
Friction modifiers are chemical additives specifically added to gear oil, and their main function is to improve lubrication performance, reduce the friction coefficient in the gear system, thereby reducing energy losses and component wear. The core function of friction modifiers lies in forming a protective film on the frictional surface, effectively isolating the direct metal-to-metal contact between the gear teeth. The formation mechanism of this protective film usually includes the following types:
Physical Adsorption Film: The molecules of the friction modifier are adsorbed on the gear surface through van der Waals forces, forming a thin and uniform lubricating film. This film can effectively reduce the frictional resistance under low-load conditions.
Chemical Reaction Film: Under higher temperatures or pressures, the active components in the friction modifier react chemically with the metal on the gear surface to form a compound film with low shear strength. This film can not only reduce friction but also improve the anti-wear performance to a certain extent.
Deposition Film: Some friction modifiers can form a solid lubricating layer through the deposition process during friction, such as molybdenum disulfide or graphite particles. This film is suitable for the lubrication requirements under extreme working conditions.
Through the above mechanisms, the friction modifier can establish a stable lubricating interface between the gear teeth, significantly reducing the friction coefficient. At the same time, it can absorb and dissipate the heat generated by friction, protecting the gear surface from excessive wear. In addition, the friction modifier can also improve the oxidation resistance and thermal stability of the gear oil to a certain extent, further enhancing the overall performance of the lubrication system.
2.2 Application Scenarios
Friction modifiers are widely used in gear systems, especially under harsh working conditions, their effects are particularly significant. The following are several typical application scenarios:
Automotive Transmissions: In automotive manual or automatic transmissions, gears need to operate continuously under high-speed and high-load conditions. The friction modifier can effectively reduce the frictional resistance between the tooth surfaces, reduce energy losses, and thus improve the fuel economy of the vehicle. At the same time, the protective film it forms can also reduce the wear of gears and synchronizers, extending the service life of the transmission.
Industrial Gearboxes: In heavy machinery equipment, such as gearboxes in mining equipment, wind turbines, or steel production lines, gears usually bear extremely high loads and operate for long periods. The friction modifier, by enhancing the lubrication performance, reduces the wear rate of the gear surface, and decreases the downtime and maintenance costs caused by wear.
Aerospace Field: Aerospace gear systems have extremely high requirements for weight and efficiency, and they need to operate under extreme temperatures and pressures. The application of friction modifiers can optimize the transmission efficiency, ensure the high reliability of the system, and at the same time meet the requirements of aircraft for long service life and high safety.
Marine Power Systems: Marine gear systems are often in a humid and highly saline environment. The friction modifier can not only reduce friction and wear but also enhance the corrosion resistance of the gear oil through its chemical properties, adapting to the complex marine working conditions.
In these applications, the specific type and addition amount of the friction modifier need to be adjusted according to the working conditions, materials, and performance objectives of the gear system. For example, under low-speed and high-load conditions, it may be necessary to select a friction modifier that mainly focuses on wear resistance; while under high-speed and light-load conditions, it is more advisable to choose an additive that mainly reduces the friction coefficient.
Balancing Strategies: Optimization Suggestions for Efficiency and Wear Resistance
In gear systems, transmission efficiency and wear resistance are two core performance indicators. There is a close relationship between them, but they often show a certain degree of contradiction. Improving transmission efficiency usually requires reducing frictional resistance, but too low friction may weaken the protective effect of the lubricating film, leading to increased wear of the gear surface; conversely, overemphasizing wear resistance may lead to an increase in frictional resistance, thereby reducing efficiency. Therefore, in the research, development, and application of gear oil, finding the optimal balance between efficiency and wear resistance has become a key task. The following are optimization suggestions put forward from multiple aspects:
3.1 Selecting the Appropriate Friction Modifier
There are a wide variety of friction modifiers, and different types have their own focuses in reducing friction and improving wear resistance. For example, oil-soluble organic friction modifiers (such as fatty acid esters) can significantly reduce the friction coefficient and are suitable for scenarios where high efficiency is pursued; while solid lubricant-type friction modifiers (such as molybdenum disulfide) are better at providing wear protection under high loads. In practical applications, the most suitable type of friction modifier should be selected according to the specific working conditions (such as load, speed, temperature) and performance requirements (such as prioritizing efficiency or wear resistance) of the gear system. In addition, the compatibility of the friction modifier with other additives also needs to be considered to avoid reducing the overall lubrication performance due to chemical reactions.
3.2 Optimizing the Lubricating Oil Formula
The performance of gear oil depends not only on the friction modifier but also on the formula of its base oil and other additives. For example:
Anti-wear Agents: Such as sulfurized phosphates, which can form a tough chemical film under high loads, enhancing wear resistance.
Extreme Pressure Agents: Such as sulfurized hydrocarbon compounds, which are suitable for protecting gears under extreme pressure conditions.
Antioxidants: Such as phenolic compounds, which can extend the service life of gear oil and maintain its lubrication performance.
By scientifically formulating these additives, wear resistance can be ensured while improving efficiency. For example, in high-load gear systems, the proportion of extreme pressure agents and anti-wear agents can be appropriately increased to enhance the strength of the protective film; while in high-speed gear systems, the proportion of friction modifiers can be increased to reduce frictional losses.
3.3 Controlling Lubrication Conditions
The physical parameters of the lubricating oil have a direct impact on friction and wear, mainly including the following aspects:
Viscosity: If the viscosity of the lubricating oil is too low, it may lead to insufficient oil film thickness, increasing the risk of wear; if the viscosity is too high, it will increase the viscous resistance and reduce efficiency. The appropriate viscosity grade should be selected according to the operating speed and load of the gears.
Temperature: High temperatures will reduce the viscosity of the lubricating oil and weaken the strength of the oil film; low temperatures may increase the fluid resistance. The oil temperature needs to be controlled within an appropriate range through a cooling system or heating device.
Flow Rate: Insufficient supply of lubricating oil may lead to dry friction, while excessive supply may increase the agitation loss. Optimize the oil supply system to ensure that the flow rate of the lubricating oil meets the requirements.
By precisely controlling these lubrication conditions, a dynamic balance between efficiency and wear resistance can be achieved. For example, under high-temperature and high-load conditions, a high-viscosity oil can be selected and the concentration of the friction modifier can be increased to balance both efficiency and wear resistance.
3.4 Gear Design Optimization
Friction and wear are not only related to the lubricating oil but also affected by the design of the gears themselves. The following design optimization measures can further support the balance between efficiency and wear resistance:
Geometric Shape: Optimizing the tooth shape design (such as using profile-modified gears) can reduce the sliding friction during the meshing process and improve the transmission efficiency.
Material Selection: Selecting materials with high strength and high wear resistance (such as carburized steel or alloy steel) can enhance the wear resistance of the gears.
Surface Treatment: Reducing the tooth surface roughness through polishing, nitriding, or coating technologies (such as DLC coating) can reduce friction and, at the same time, enhance the surface hardness and wear resistance.
By combining the optimization of the lubricating oil with the optimization of the gear design, friction and wear can be reduced from the source, achieving higher performance goals.
The Importance of Balance
In gear systems, the application of friction modifiers provides important support for improving transmission efficiency and wear resistance. By forming a protective film on the gear surface, the friction modifier can effectively reduce the friction coefficient, reduce energy losses, and protect the gears from excessive wear. However, the relationship between efficiency and wear resistance is not simply a direct or inverse proportion but a dynamic balance that needs to be weighed. Over-pursuing high efficiency may lead to insufficient strength of the lubricating film and increase the risk of wear; overemphasizing wear resistance may reduce the system efficiency due to the increase in frictional resistance. Therefore, it is crucial to find this balance point in the research, development, and application of gear oil.
Achieving this balance requires comprehensive consideration of multiple factors, including the selection of friction modifiers, the optimization of the lubricating oil formula, the control of lubrication conditions, and the improvement of gear design. Only through a systematic approach can the gear system operate efficiently while having excellent wear resistance, meeting the requirements of modern industry for high-performance and long-service-life transmission systems. With the continuous progress of technology, the research and development of gear oil and its additives will continue to deepen. The future goal will be to develop more efficient and durable lubrication solutions to cope with increasingly complex working condition challenges. This process can not only enhance the economic benefits of the gear system but also make a positive contribution to environmental protection by reducing energy consumption and maintenance requirements.
The Price of Additive Packages
The price of Additive Packages varies depending on factors such as brand, specification, composition, and sales channels. If you are interested in Additive Packages, please feel free to contact us.
Supplier of Additive Packages
UNPChemicals is a professional supplier of high-quality and effective Additive Packages. We offer several remarkable products, namely Industrial Gear Oil Additives UNP IG402A,High extreme pressure (EP) type industrial gear oil additive packages UNP IG402B,Low-Odor Type Industrial Gear Oil Additive Package UNP IG402C,etc.
Industrial Gear Oil Additives UNP IG402Aare a specialized class of compounds designed to enhance the performance of gear oils in various industrial applications.These additives are carefully formulated to provide a combination of properties that improve the efficiency,longevity,and reliability of gear systems.
High extreme pressure (EP) type industrial gear oil additive packages, like UNP IG402B, are specialized blends of chemical compounds designed to enhance the performance of base oils used in industrial gear lubricants. These packages are formulated to provide exceptional protection under conditions where gears experience heavy loads, high pressures, and potential metal-to-metal contact.
The Low-Odor Type Industrial Gear Oil Additive Package UNP IG402C is a specialized blend of chemical additives designed to enhance the performance of industrial gear oils while minimizing the strong odors typically associated with traditional gear oil additives, particularly those containing sulfur-based extreme pressure (EP) agents. This additive package is mixed with base oils (mineral or synthetic) to create gear lubricants that protect industrial gearboxes under demanding conditions, such as high loads and temperatures, while being more user-friendly in terms of smell—ideal for environments where odor control is a priority.
Professional Lubricant Additive Manufacturer
UNPChemicals,aka Luoyang Pacific United Petrochemical Co., Ltd., focuses on the application and development of special lubricating grease additives such as MODTC, MODTP, molybdenum amide, thiadiazole metal deactivators, and phosphate esters. With nearly 30 products in seven series, including extreme pressure anti-wear additives and special grease additives, it is a global manufacturer of special lubricating grease additives and a national high-tech enterprise with great influence and leading role in the industry. If you are looking for Lubricant Additive or technical information, feel free to contact UNPChemicals.