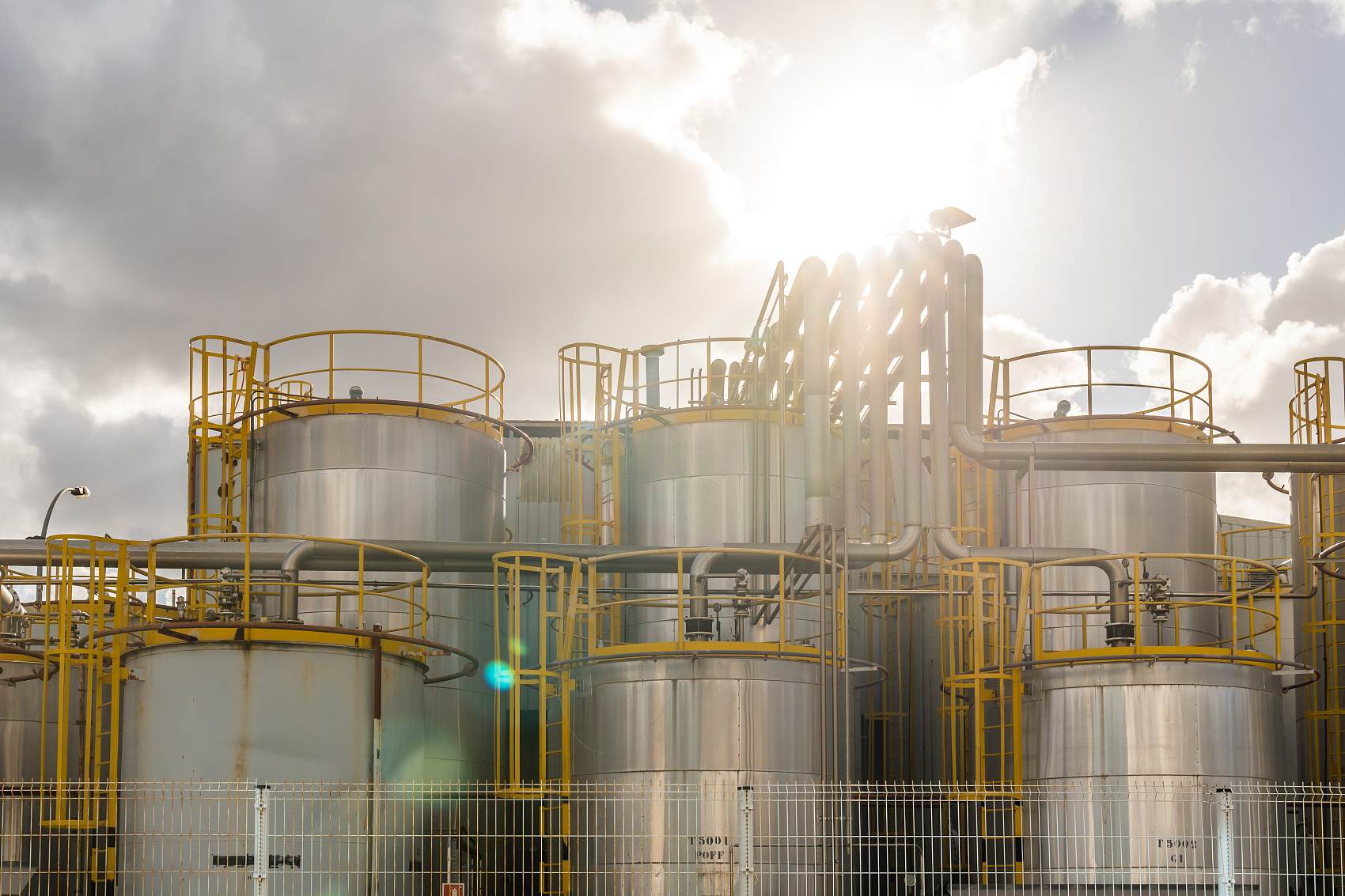
Formulation Design of Anti-wear Hydraulic Oil Additive Package
Anti-wear hydraulic oil is the "blood" of a hydraulic system, and its performance is directly related to the stable operation and service life of hydraulic equipment. The anti-wear hydraulic oil additive package is the core element determining the performance of hydraulic oil. Through the reasonable compounding of various functional additives, it endows hydraulic oil with a series of key properties such as anti-wear, anti-oxidation, anti-rust, and anti-foaming. Formulation design is the process of scientifically combining various additives, and its scientific nature and rationality have a decisive impact on the final performance of the product. A carefully designed formulation can enable a synergistic effect among additives, significantly improving the comprehensive performance of hydraulic oil. Conversely, if the formulation design is inappropriate, not only will the expected performance not be achieved, but it may also lead to antagonism among additives, reducing the usage effect of hydraulic oil and even causing damage to the hydraulic system. In the context of the increasing pursuit of high efficiency, energy conservation, and long service life in industrial production, in-depth research on the formulation design of anti-wear hydraulic oil additive packages has important theoretical and practical significance.
I. Basic Principles of Formulation Design of Anti-wear Hydraulic Oil Additive Package
(1) Balance Principle
The formulation design of anti-wear hydraulic oil additive packages needs to take into account multiple properties and ensure a balanced state among all properties. During the actual use of hydraulic oil, it faces various problems such as wear, oxidation, corrosion, and foaming. Excessive strengthening of a single property may have a negative impact on other properties. For example, excessively adding anti-wear agents to improve anti-wear performance may affect the anti-oxidation and anti-foaming properties of hydraulic oil. Therefore, during formulation design, various performance indicators such as anti-wear, anti-oxidation, anti-rust, and anti-foaming need to be comprehensively considered. According to different application scenarios and equipment requirements, the types and dosages of additives should be reasonably adjusted to enable hydraulic oil to achieve good performance in all aspects.
(2) Synergistic Effect Principle
There are complex interaction relationships among different additives, and a reasonable formulation design should make full use of the synergistic effect among additives. The synergistic effect means that when two or more additives are used in combination, their effect is greater than the sum of their individual effects when used alone. For example, when an antioxidant and a metal deactivator are used in combination, the metal deactivator can inhibit the catalytic effect of metal on the oxidation reaction, thereby enhancing the anti-oxidation effect of the antioxidant. The synergistic effect of anti-wear agents and extreme pressure agents can form a more tenacious protective film on the metal surface, significantly improving the anti-wear and extreme pressure properties of hydraulic oil. During the formulation design process, it is necessary to conduct in-depth research on the interaction mechanism among additives and screen out additive combinations with good synergistic effects through experiments to improve the overall performance of the additive package.
(3) Stability Principle
The anti-wear hydraulic oil additive package should maintain good physical and chemical stability during storage and use. Physical stability requires that the additive package does not exhibit phenomena such as stratification and precipitation under different temperature and pressure conditions. Chemical stability requires that no chemical reactions occur among additives, resulting in a decrease in performance or the generation of harmful substances. To ensure stability, when selecting additives, their compatibility and chemical properties need to be considered, and additive combinations that may react should be avoided. At the same time, it is also necessary to verify and optimize the stability of the formulation through stability tests, such as high-temperature storage tests and low-temperature fluidity tests.
(4) Economic Principle
On the premise of meeting the product performance requirements, formulation design also needs to consider economic factors. The cost of additives accounts for a large proportion of the production cost of hydraulic oil. Therefore, it is necessary to reasonably select the types and dosages of additives to reduce the production cost while ensuring performance. You can compare the prices and performances of additives from different suppliers and select products with high cost performance. You can also optimize the formulation, reduce the dosage of expensive additives, and find substitutes with similar performance but lower cost. In addition, it is also necessary to consider the production process and production efficiency of the formulation, reduce energy consumption and labor costs during the production process, and improve the market competitiveness of the product.
II. Experimental Methods for Formulation Design of Anti-wear Hydraulic Oil Additive Package
(1) Orthogonal Experimental Method
The orthogonal experimental method is an efficient, rapid, and economical experimental design method that is widely used in the formulation design of anti-wear hydraulic oil additive packages. It selects representative experimental points through reasonable experimental arrangements and the use of orthogonal tables to obtain comprehensive experimental information with a small number of experimental times. When using the orthogonal experimental method, the experimental factors and levels need to be determined first. Experimental factors usually include the types and dosages of various additives, and the levels refer to the different values of each factor. For example, when studying the influence of anti-wear agents, antioxidants, and anti-rust agents on the performance of hydraulic oil, the dosage of anti-wear agents, the types of antioxidants, and the dosage of anti-rust agents can be used as experimental factors, and each factor can be set with different levels.
Then, select an appropriate orthogonal table according to the experimental factors and levels and arrange the experiments. Through the analysis of the experimental results, the primary and secondary order of the influence of each factor on the product performance can be determined, as well as the optimal level combination of each factor. The orthogonal experimental method can effectively reduce the number of experiments, improve experimental efficiency, and accurately analyze the interaction among each factor, providing a scientific basis for formulation optimization.
(2) Single-factor Experimental Method
The single-factor experimental method is to change the level of only one factor while keeping other factors unchanged and observe its influence on the product performance. This method is simple and intuitive and is suitable for initially exploring the influence law of a certain factor on the product performance. For example, when studying the influence of the dosage of anti-wear agents on the anti-wear performance of hydraulic oil, the dosages and types of other additives such as antioxidants and anti-rust agents can be fixed, and only the dosage of anti-wear agents is changed. Through experiments, the anti-wear performance indicators of hydraulic oil under different dosages of anti-wear agents, such as the diameter of the wear spot and the amount of wear, are tested, so as to obtain the relationship curve between the dosage of anti-wear agents and the anti-wear performance.
Although the single-factor experimental method can clarify the influence of a single factor, it cannot consider the interaction among factors. Therefore, it is usually used in combination with other experimental methods. In the initial stage of formulation design, the single-factor experimental method can be used to screen out the factors that have a greater influence on the product performance, providing a basis for subsequent orthogonal experiments or other complex experiments.
(3) Response Surface Analysis Method
The response surface analysis method is an experimental design and data analysis method based on mathematical and statistical principles. It establishes a mathematical model between the response variable (such as a certain performance index of hydraulic oil) and multiple experimental factors to describe the relationship between the factors and the response variable and search for the optimal experimental conditions. The response surface analysis method usually adopts experimental design methods such as central composite design, selects a certain number of experimental points within the experimental region for experiments, and then uses the regression analysis method to establish a response surface equation.
Through the analysis of the response surface equation, the influence law of each factor on the response variable and the interaction among factors can be obtained. At the same time, an optimization algorithm can also be used to search for the optimal solution on the response surface and determine the best formulation combination. The response surface analysis method can more accurately describe the nonlinear relationship between factors and response variables and is suitable for the optimization design of complex formulation systems.
III. Technical Routes for Formulation Optimization of Anti-wear Hydraulic Oil Additive Package
(1) Optimization Based on Performance Testing
Performance testing is an important basis for formulation optimization. During the formulation design process, it is necessary to conduct comprehensive performance tests on anti-wear hydraulic oils with different formulations, including anti-wear performance tests (such as four-ball machine tests and vane pump tests), anti-oxidation performance tests (such as rotating oxygen bomb tests and pressure differential scanning calorimetry), anti-rust performance tests (such as liquid phase rust tests), and anti-foaming performance tests (such as ASTM D892 foam characteristics tests), etc.
Through the analysis of the test results, identify the performance weaknesses in the formulation and adjust the types and dosages of additives accordingly. For example, if the anti-wear performance of hydraulic oil does not meet the standard, the dosage of anti-wear agents can be appropriately increased or a more excellent anti-wear agent can be replaced. If the anti-oxidation performance is insufficient, additives with stronger anti-oxidation performance can be considered for addition or the formulation ratio of antioxidants can be adjusted. Through continuous performance testing and formulation adjustment, the formulation is gradually optimized to enable the various performances of hydraulic oil to reach the expected goals.
(2) Optimization Based on Computer Simulation
With the continuous development of computer technology, computer simulation is playing an increasingly important role in the formulation optimization of anti-wear hydraulic oil additive packages. Molecular simulation technology can study the interaction mechanism between additives and base oils, as well as between additives, at the molecular level, and predict the dispersibility, solubility of additives in base oils, and their adsorption behavior on the metal surface. Through molecular simulation, the formulation combinations of additives can be preliminarily screened before experiments, reducing the blindness of experiments and improving the efficiency of formulation optimization.
In addition, simulation methods such as computational fluid dynamics (CFD) can simulate the flow and heat transfer processes of hydraulic oil in the hydraulic system and analyze the influence of different formulations on the performance of the hydraulic system. By combining computer simulation with experiments, a more comprehensive understanding of the influence of the formulation on product performance can be obtained, providing a more scientific basis for formulation optimization.
(3) Optimization Based on Industry Standards and Customer Needs
The formulation design of anti-wear hydraulic oil additive packages needs to comply with relevant industry standards and specifications, such as ISO, ASTM, GB, and other standards. During the formulation optimization process, it is necessary to ensure that the various performance indicators of hydraulic oil meet the standard requirements. At the same time, it is also necessary to fully consider the actual needs of customers. The performance requirements of hydraulic oil vary among different industries and different equipment. For example, the construction machinery industry has higher requirements for the anti-wear and extreme pressure performance of hydraulic oil, while the food processing industry pays more attention to the safety and hygiene of hydraulic oil.
Therefore, during formulation optimization, the formulation needs to be adjusted individually according to the specific needs of customers. Through communication and feedback with customers, the formulation is continuously optimized to make the product better meet market needs and improve the market share of the product.
Conclusion
The formulation design of anti-wear hydraulic oil additive packages is a systematic and complex process that involves knowledge and technologies from multiple disciplinary fields. From the perspective of the basic principles of formulation design, the principles of balance, synergistic effect, stability, and economy are interrelated and mutually restrictive, jointly guiding the direction of formulation design. In terms of experimental methods, the orthogonal experimental method, single-factor experimental method, and response surface analysis method each have their own characteristics. Through the reasonable selection and comprehensive application of these experimental methods, the information required for formulation design can be efficiently obtained. In terms of the technical routes for formulation optimization, the optimization methods based on performance testing, computer simulation, as well as industry standards and customer needs complement each other, improving and perfecting the formulation from different angles.
The scientific formulation design process first needs to clarify the performance goals and application scenarios of the product, then determine the preliminary formulation according to the basic principles, use appropriate experimental methods to conduct experimental research and optimization on the formulation, verify the rationality of the formulation through performance testing and computer simulation, and finally make final adjustments and improvements in combination with industry standards and customer needs. Only by following such a scientific and rigorous process can a formulation of anti-wear hydraulic oil additive package with excellent performance, stable reliability, and economic applicability be designed, providing a strong guarantee for the normal operation of hydraulic equipment and promoting the sustainable development of related industries.
The Price of Hydraulic Oil Additives Package
The price of Hydraulic Oil Additives Package varies depending on factors such as brand, specification, composition, and sales channels. If you are interested in Hydraulic Oil Additives Package, please feel free to contact us.
Supplier of Hydraulic Oil Additives Package
UNPChemicals is a professional supplier of high-quality and effective Hydraulic Oil Additives Package. We offer several remarkable products, namely High zinc hydraulic oil additives UNP AH502A,Low Zinc Hydraulic Oil Additives UNP AH502B,Zinc-free Hydraulic Oil Additives UNP AH502C,etc.
High zinc hydraulic oil additives UNP AH502A are a type of chemical additive used in hydraulic oils that contain high levels of zinc dialkyldithiophosphate (ZDDP). ZDDP is a well-known anti-wear agent that also provides antioxidant, anti-corrosion, and anti-foam properties. The zinc in these additives plays a crucial role in forming a protective film on metal surfaces within the hydraulic system, thereby reducing wear and extending the life of the system components.
Low Zinc Hydraulic Oil Additives UNP AH502B are a class of advanced lubricant additives designed to enhance the performance of hydraulic oils with reduced zinc content.These additives are formulated to provide a balance of anti-wear,extreme pressure,and antioxidant properties,making them suitable for modern hydraulic systems that demand high performance with lower environmental impact.
Zinc-free Hydraulic Oil Additives UNP AH502C are a new class of environmentally friendly lubricant additives designed for hydraulic systems.These additives are formulated to provide the same level of performance as traditional zinc-containing additives but without the heavy metal content,reducing the environmental impact of hydraulic fluids.
Professional Lubricant Additive Manufacturer
UNPChemicals,aka Luoyang Pacific United Petrochemical Co., Ltd., focuses on the application and development of special lubricating grease additives such as MODTC, MODTP, molybdenum amide, thiadiazole metal deactivators, and phosphate esters. With nearly 30 products in seven series, including extreme pressure anti-wear additives and special grease additives, it is a global manufacturer of special lubricating grease additives and a national high-tech enterprise with great influence and leading role in the industry. If you are looking for Lubricant Additive or technical information, feel free to contact UNPChemicals.