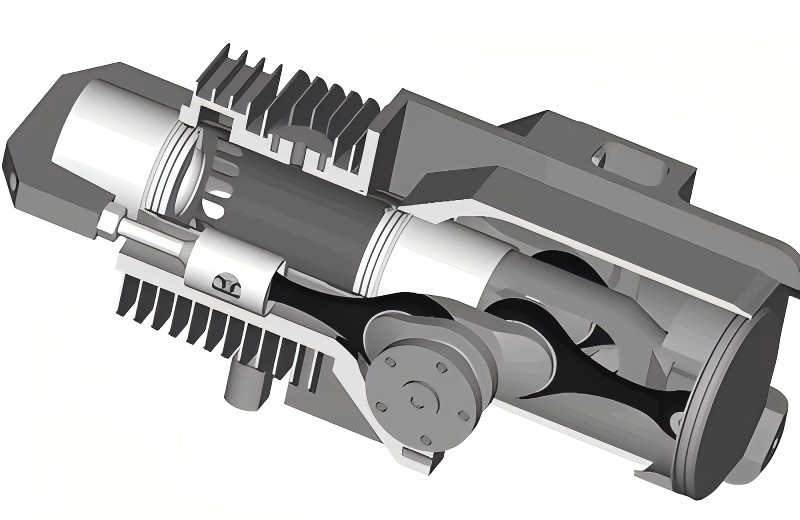
Compressor Oil Additives: Maintaining the Efficiency of Compressed Air Systems
In the intricate framework of modern industry, compressed air systems are a critical component in ensuring the power supply for various production processes. From the operation of automated production lines to essential processes in industries such as chemicals and pharmaceuticals, compressed air plays an indispensable role. Compressor oil, as the lubricant for these systems, is undeniably vital.
Compressor oil is a specialized lubricant designed for compressors. Inside a compressor, moving parts operate at high speeds and frequencies. The primary function of compressor oil is to form a lubricating film between these components, reducing the friction coefficient, minimizing wear, preventing excessive heat buildup from friction, aiding in heat dissipation, and ensuring stable operation at appropriate temperatures. Additionally, it serves a sealing function to prevent gas leaks, maintaining compression efficiency, while also resisting corrosion from external substances, preventing rust and damage to metal components.
However, with the rapid advancement of industrial technology, the operating conditions of compressors have become increasingly complex and demanding. Extreme conditions such as high temperatures, high pressures, high humidity, and high-speed operations have become the norm, placing greater demands on compressor oil performance. Relying solely on base oils is no longer sufficient to meet these needs, making the addition of additives a key factor in enhancing the operational efficiency of compressed air systems and enabling compressor oil to handle diverse challenging conditions.
Types of Compressor Oil Additives Package
Anti-Wear Agents
The mechanical components inside a compressor endure intense motion. Pistons reciprocate within cylinders at speeds of several meters per second, connecting rods and crankshafts rotate continuously under significant torque, and bearings bear substantial radial and axial loads. In such high-friction environments, anti-wear agents play a crucial role in protecting these components.
Take organic molybdenum anti-wear agents as an example. When blended into compressor oil, they react chemically with metal surfaces under high-temperature and high-pressure conditions, forming an extremely thin yet robust molybdenum sulfide lubricating film. This film has an exceptionally low friction coefficient, effectively reducing resistance between moving parts, while also possessing strong load-bearing capacity to withstand significant pressure without breaking down. This not only significantly reduces component wear rates and extends their service life but also minimizes system contamination from wear debris, ensuring stable compressor operation, reducing maintenance and replacement frequency, and saving time and costs for businesses.
Corrosion Inhibitors
In compressed air systems, metal components are susceptible to corrosion from external substances. Inhaled air often contains moisture, oxygen, and acidic gases, and condensate generated during compression exacerbates corrosion risks. Under these conditions, metal components can corrode, potentially leading to equipment failure.
Corrosion inhibitors address this issue. With their unique molecular structures, they chemically adsorb onto active sites on metal surfaces, forming a dense protective layer that isolates the metal from corrosive substances. For instance, amine-based corrosion inhibitors create an adsorption film on metal surfaces that prevents direct contact with oxygen and moisture while neutralizing acidic substances, effectively inhibiting corrosion. Whether in humid regions or industries with high concentrations of corrosive gases, such as chemicals, corrosion inhibitors protect the internal metal components of compressors, ensuring structural integrity and normal operation, extending equipment lifespan, and reducing maintenance costs for businesses.
Demulsifiers
Moisture infiltration is unavoidable during the operation of compressed air systems, originating from humid intake air or condensate formed during compression. When moisture mixes with compressor oil, it can form a stable emulsion, severely impairing the oil's performance.
Emulsions reduce the oil's lubricating ability, turning a stable oil film into a viscous, unstable layer incapable of effectively isolating metal surfaces, thus increasing wear risks. Additionally, emulsions diminish the oil's heat dissipation capacity, preventing timely release of heat generated during compressor operation, placing additional strain on the equipment. They may also clog filters, disrupting oil circulation and supply, ultimately affecting normal compressor function.
Demulsifiers break the stability of oil-water emulsions. These molecules have both oil-attracting (lipophilic) and water-attracting (hydrophilic) ends. When added to an emulsion, the lipophilic end bonds with oil molecules, while the hydrophilic end interacts with water molecules, reducing surface tension at the oil-water interface. This causes water droplets dispersed in the oil to coalesce and settle, separating from the oil. After demulsifier treatment, compressor oil regains its purity and lubricating properties, ensuring normal compressor operation.
Oxidation Inhibitors
During continuous compressor operation, significant heat is generated, with internal temperatures reaching hundreds of degrees Celsius. As compressors are exposed to ambient air, large amounts of oxygen enter the system. Under the combined effects of high temperatures and oxygen, compressor oil is prone to oxidation.
Oxidation degrades the molecular structure of compressor oil, increasing its viscosity, causing cloudiness, raising acidity, and producing harmful substances like sludge and varnish. These substances adhere to internal compressor components, clogging filters and oil passages, impeding normal oil circulation, reducing operational efficiency, and potentially damaging parts due to poor lubrication, affecting equipment performance.
Oxidation inhibitors effectively combat this. Typically categorized as phenolic or amine-based, these inhibitors work by capturing free radicals generated during oxidation, interrupting the chain reaction. When compressor oil molecules produce free radicals under high temperatures and oxygen exposure, oxidation inhibitor molecules quickly bind to them, stabilizing the radicals and preventing further oxidation. This delays the oil's oxidation rate, maintains its performance, extends oil change intervals, and reduces oil costs for businesses.
Functions of Compressor Oil Additives Package
Performance Enhancement
By incorporating various additives judiciously, the overall performance of compressor oil is significantly enhanced, transforming it from a basic lubricant into a high-performance protective agent, positively impacting compressor performance.
First, equipment reliability improves dramatically. The lubricating film formed by anti-wear agents and the protective layer created by corrosion inhibitors work together to safeguard critical compressor components, enabling them to maintain optimal condition under harsh operating environments. This greatly reduces failure rates due to wear and corrosion, minimizing downtime for repairs and costs, ensuring smooth execution of production schedules, and boosting efficiency.
Second, compressor service life is notably extended. The synergistic effects of additives slow the oil's degradation, preserving its lubricating properties and physicochemical characteristics, allowing the compressor to operate stably over extended periods. This reduces equipment replacement frequency, saving businesses capital investment while aligning with sustainability principles.
Additionally, enhanced compressor oil performance increases operational efficiency. Superior lubrication reduces friction resistance between components, lowering energy losses and enabling the compressor to produce more compressed air with the same power input, improving energy efficiency and reducing production costs.
Challenges and Solutions for Compressor Oil Additives Package
High-Temperature Issues
During compressor operation, high-speed friction of mechanical components and gas compression generate substantial heat. If not dissipated promptly, oil temperatures can rise sharply, accelerating oxidation and decomposition reactions.
In high-temperature environments, oil molecule activity increases, reacting faster with oxygen, while chemical bonds break, leading to decomposition into low-molecular-weight compounds and free radicals. These byproducts reduce oil viscosity, impairing its ability to form an effective lubricating film, and exacerbate oxidation in a vicious cycle.
To address this, the industry employs multiple strategies. Compressor designs incorporate efficient cooling systems, such as air or water cooling, to remove heat via forced convection. High-temperature-resistant additives, like antioxidants and anti-wear agents, are added to the oil. These specially synthesized additives offer excellent thermal stability and oxidation resistance, maintaining structural integrity and performance at high temperatures, suppressing oil oxidation and wear, and ensuring normal compressor operation under extreme heat.
Moisture Issues
Moisture ingress is a common challenge in compressed air systems, stemming from humid intake air—especially in high-humidity regions or seasons—condensate from gas cooling during compression, or external water infiltration due to poor sealing.
Moisture harms both compressor oil and the compressor in multiple ways: it causes emulsification, degrading lubrication and heat dissipation; reacts with acidic gases in the compressed air to form corrosive substances, accelerating metal corrosion; and may freeze in low temperatures, damaging internal components.
To tackle moisture, comprehensive measures are adopted. Equipment-wise, enhanced sealing and drainage designs use high-performance materials to minimize water ingress, while drainage devices at the compressor base and pipeline low points periodically remove condensate. In compressor oil, demulsifiers separate water to restore oil purity, and corrosion inhibitors form protective films on metal surfaces to prevent corrosion.
Pressure Issues
Compressors must compress gas to high pressures to meet industrial demands. Under high-pressure conditions, compressor oil faces challenges: the oil film can break under extreme pressure, leading to direct component contact and wear, while also accelerating oil oxidation and degradation, reducing performance.
To address pressure challenges, extreme-pressure (EP) anti-wear agents are added to compressor oil. These agents, with specialized molecular structures, react with metal surfaces under high pressure, forming a high-strength protective film. This film offers excellent shear resistance and load-bearing capacity, maintaining oil film integrity under extreme pressure and ensuring proper lubrication. Additionally, some advanced compressor oils use tailored formulations to improve viscosity index and pressure resistance, adapting to high-pressure conditions.
Conclusion
In summary, the various additives in compressor oil work synergistically to address challenges like high temperatures, moisture, and pressure, playing a critical role in ensuring smooth compressor operation.
They significantly enhance the operational efficiency of compressed air systems, reduce energy consumption, lower production costs, extend equipment lifespan, and decrease maintenance and replacement frequency, mitigating equipment investment risks for businesses. Moreover, additive use aligns with modern industrial sustainability goals by reducing environmental impacts from equipment failures and replacements.
As industrial technology evolves, compressor performance and operating conditions will continue to advance, raising the bar for compressor oil additive performance. Future efforts should focus on increased R&D investment, deeper exploration of additive mechanisms and formulation optimization, and the development of more efficient, eco-friendly additives suited to complex conditions, meeting the increasingly stringent demands of industrial applications and driving sustained progress in the field.
The Price of Compressor Oil Additives Package
The price of Compressor Oil Additives Package varies depending on factors such as brand, specification, composition, and sales channels. If you are interested in Compressor Oil Additives Package, please feel free to contact us.
Supplier of Compressor Oil Additives Package
UNPChemicals is a professional supplier of high-quality and effective Compressor Oil Additives Package. We offer several remarkable products, namely Compressor Oil Additives UNP CP603A,etc.
Compressor Oil Additives UNP CP603Ais a multifunctional compound designed for high temperature applications. It is optimized with anti-oxidant, anti-wear agent, anti-corrosion and anti-rust agent and other components, with excellent anti-corrosion and anti-wear performance.
Professional Lubricant Additive Manufacturer
UNPChemicals, aka Luoyang Pacific United Petrochemical Co., Ltd., focuses on the application and development of special lubricating grease additives such as MODTC, MODTP, molybdenum amide, thiadiazole metal deactivators, and phosphate esters. With nearly 30 products in seven series, including extreme pressure anti-wear additives and special grease additives, it is a global manufacturer of special lubricating grease additives and a national high-tech enterprise with great influence and leading role in the industry. If you are looking for Lubricant Additive or technical information, feel free to contact UNPChemicals.