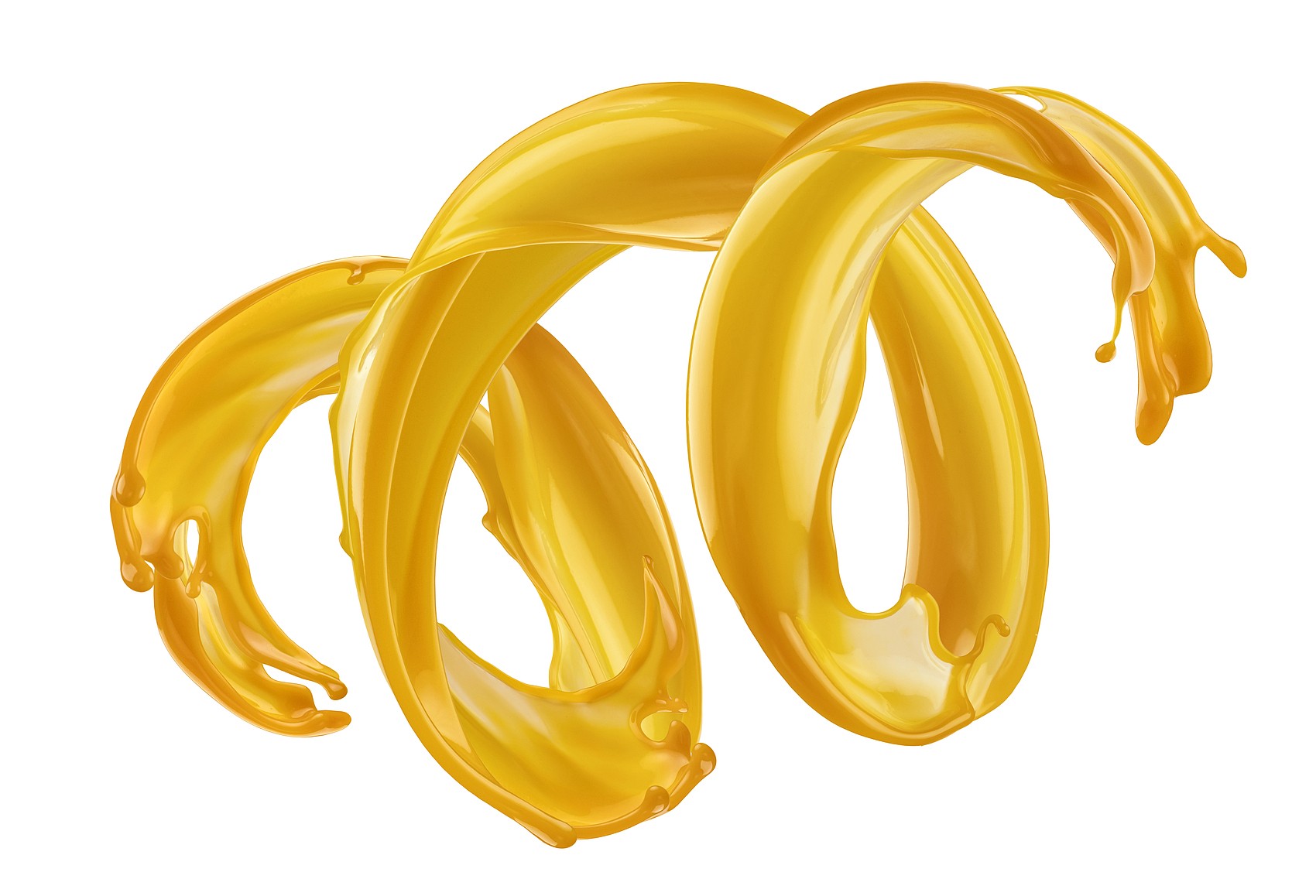
Challenges and Solutions for Maintaining Lubrication Performance in Harsh Industrial Environments
Industrial production, while creating huge value for society, also faces various severe environmental challenges. Among the many factors affecting the operation of industrial equipment, the test of harsh industrial environments on the lubrication performance of equipment has become increasingly prominent. Once there are problems with the lubrication performance, the wear of the equipment will intensify, energy consumption will increase, and it may even lead to equipment failure and shutdown. This not only affects production efficiency but also significantly increases the operating costs of enterprises. Therefore, a thorough understanding of the impact of harsh industrial environments on lubrication performance and finding practical solutions are of great practical significance for ensuring the efficient, stable, and safe operation of industrial production. This article will systematically analyze the common problems in harsh industrial environments, discuss the role of compound additives in solving these problems, and provide best practice suggestions for lubrication management, aiming to provide comprehensive and practical guidance for the lubrication management of industrial enterprises.
Identification of Common Problems in Harsh Industrial Environments
(1) Pollution Problems
During the industrial production process, there are a large number of pollutants in the environment where the equipment is located. Once these pollutants enter the lubrication system, they will have a serious impact on the lubrication performance. Common pollutants include solid particles and liquid impurities.
The sources of solid particles are extremely extensive. For example, in industries such as mining and construction, there is a large amount of dust in the air. These dust particles vary in size, ranging from a few micrometers to dozens of micrometers. When the equipment operates in such an environment, the dust can easily enter the lubrication system through the gaps and ventilation openings of the equipment. In addition, the wear debris generated by the equipment itself during operation, such as metal particles, is also an important source of solid particle pollutants. Once these solid particles are mixed into the lubricating oil, they will act like an abrasive, increasing the friction between the equipment components. For example, in a gear transmission system, solid particles will embed in the surface of the gears, resulting in uneven tooth surface wear, which in turn affects the transmission accuracy of the gears and reduces the service life of the equipment.
Liquid impurities cannot be ignored either. In some humid industrial environments, moisture can easily enter the lubrication system. When moisture is mixed into the lubricating oil, it will cause the lubricating oil to emulsify and damage its lubrication performance. For example, in the engine system of a ship, due to the long-term operation of the ship in a water environment, the engine's lubrication system is easily invaded by moisture. In addition, some chemical substances, such as acids and alkalis, may also be mixed into the lubricating oil. These chemical substances will react chemically with the lubricating oil, changing its chemical properties, making it lose its lubricating function, and even causing corrosion to the equipment components.
(2) High Temperature Problems
In many industrial fields, such as steel smelting, glass manufacturing, and the chemical industry, a large amount of heat is generated during the operation of equipment, resulting in a significant increase in the working environment temperature. The impact of high temperature on lubrication performance is mainly reflected in two aspects.
Firstly, high temperature will reduce the viscosity of the lubricating oil. The viscosity of the lubricating oil is one of the key indicators to ensure its lubrication performance. When the viscosity is reduced to a certain extent, the lubricating oil cannot form an oil film of sufficient thickness on the surface of the equipment components, resulting in direct contact between the equipment components and increasing friction and wear. For example, in an internal combustion engine operating in a high-temperature environment, the lubricating oil film between the piston and the cylinder wall is likely to become thinner due to the increase in temperature, thereby intensifying the wear of the piston and the cylinder wall.
Secondly, high temperature will accelerate the oxidation of the lubricating oil. The hydrocarbon compounds in the lubricating oil react with the oxygen in the air at high temperatures to form substances such as organic acids, resins, and asphaltenes. These oxidation products will darken the color of the lubricating oil and increase its viscosity. At the same time, they will also form deposits on the surface of the equipment components, affecting the heat dissipation and normal operation of the equipment. For example, in a transformer operating in a high-temperature environment for a long time, its insulating oil will deteriorate due to oxidation, reducing the insulation performance of the transformer and even causing safety accidents.
The Role of Compound Additives in Solving Lubrication Problems
(1) Composition and Principle of Compound Additives
Compound additives are compounded from a variety of additives with specific functions in a certain proportion. These additives mainly include anti-wear agents, antioxidants, detergents and dispersants, anti-emulsifiers, etc. Compound additives effectively solve various problems faced by the lubrication system in harsh industrial environments through their synergistic effects.
The function of an anti-wear agent is to form a protective film on the surface of the equipment components, reducing direct contact between the components and thus reducing friction and wear. Common anti-wear agents include organic sulfides and organic phosphides. These anti-wear agents will react chemically with the metal surface under high-temperature and high-pressure conditions to form a tough chemical reaction film. This film has good anti-wear performance and can effectively protect the equipment components.
The function of an antioxidant is to inhibit the oxidation reaction of the lubricating oil. Common antioxidants include phenols and amines. These antioxidants can capture the free radicals generated during the oxidation process of the lubricating oil, preventing the chain propagation of the oxidation reaction, thereby delaying the oxidation rate of the lubricating oil and extending its service life.
The function of a detergent and dispersant is to disperse the deposits and pollutants generated during the oxidation process of the lubricating oil in the lubricating oil, preventing them from depositing on the surface of the equipment components. Common detergents and dispersants include sulfonates and salicylates. These detergents and dispersants have surface activity and can adsorb on the surface of the deposits and pollutants, dispersing them in the lubricating oil and being filtered out with the circulation of the lubricating oil.
The function of an anti-emulsifier is to prevent the lubricating oil from emulsifying with water. Common anti-emulsifiers include polyethers and esters. These anti-emulsifiers can change the interfacial tension between oil and water, separating the oil and water, thus ensuring the lubrication performance of the lubricating oil.
(2) Specific Mechanisms of Compound Additives in Solving Pollution and High Temperature Problems
Solving Pollution Problems: When solid particles and liquid impurities enter the lubrication system, the detergents and dispersants in the compound additives will quickly adsorb on the surface of these pollutants and disperse them in the lubricating oil. At the same time, the anti-emulsifier can prevent the lubricating oil from emulsifying with water, enabling the water to separate from the lubricating oil and be discharged from the lubrication system through the drainage device. In addition, the protective film formed by the anti-wear agent on the surface of the equipment components can prevent the direct erosion of the pollutants on the equipment components, thereby reducing the impact of pollution on the lubrication performance.
Solving High Temperature Problems: In a high-temperature environment, the antioxidants in the compound additives can effectively inhibit the oxidation reaction of the lubricating oil and delay the deterioration rate of the lubricating oil. At the same time, the chemical reaction film formed by the anti-wear agent under high-temperature and high-pressure conditions can still maintain good anti-wear performance when the viscosity of the lubricating oil decreases, ensuring the normal lubrication between the equipment components. In addition, some compound additives also contain viscosity index improvers, which can increase the viscosity of the lubricating oil at high temperatures and keep it within an appropriate range to ensure the stability of the lubrication performance.
Best Practices for Lubrication Management
(1) Selecting Appropriate Compound Additives
Selecting According to the Characteristics of the Industrial Environment: Different industrial environments have different requirements for lubrication performance. Therefore, it is necessary to select appropriate compound additives according to the specific characteristics of the industrial environment. For example, in an environment with a large amount of dust, compound additives with good detergency and dispersancy should be selected to effectively disperse and remove solid particle pollutants; in a humid environment, compound additives with good anti-emulsification performance should be selected to prevent the lubricating oil from emulsifying; in a high-temperature environment, compound additives with good antioxidant and anti-wear performance should be selected to ensure the stability and lubrication performance of the lubricating oil at high temperatures.
Selecting According to the Equipment Type: Different types of equipment also have different requirements for the performance of the lubricating oil. For example, the gear transmission system has high requirements for the anti-wear performance and load-carrying capacity of the lubricating oil, so compound additives containing high-performance anti-wear agents should be selected; the hydraulic system has high requirements for the anti-emulsification performance and filtration performance of the lubricating oil, so compound additives with good anti-emulsification performance and detergency and dispersancy should be selected.
(2) Formulating a Reasonable Lubrication Plan
Determining the Lubrication Cycle: The determination of the lubrication cycle should comprehensively consider factors such as the operating conditions of the equipment, the working environment, and the quality of the lubricating oil. Generally speaking, in the case of harsh operating conditions of the equipment, a poor working environment, and low quality of the lubricating oil, the lubrication cycle should be shortened; conversely, the lubrication cycle can be appropriately extended. For example, in mining equipment, due to the harsh operating environment, a large amount of dust, and strong vibrations, the lubrication cycle should be relatively short, generally once a week or every two weeks; while in some electronic equipment with relatively stable operating conditions, the lubrication cycle can be extended to several months or even years.
Controlling the Lubricating Oil Filling Quantity: The filling quantity of the lubricating oil should be carried out strictly in accordance with the requirements of the equipment manufacturer. Excessive filling quantity will lead to an increase in the operating resistance of the equipment, an increase in the oil temperature, and also an increase in the consumption of the lubricating oil; insufficient filling quantity will lead to poor lubrication and intensify the wear of the equipment. Therefore, when filling the lubricating oil, professional measuring tools should be used to ensure the accuracy of the filling quantity.
(3) Strengthening the Maintenance and Monitoring of the Lubrication System
Regularly Cleaning the Lubrication System: Regularly cleaning the lubrication system can effectively remove the deposits and pollutants in the system and ensure the smoothness of the lubrication system. Special cleaning agents should be used during the cleaning process, and the operation should be carried out in accordance with the correct cleaning procedure. Generally speaking, the cleaning cycle is once every six months or once a year, and the specific cycle should be determined according to the operating conditions of the equipment and the pollution degree of the lubrication system.
Real-time Monitoring of the Lubricating Oil Performance: By monitoring the performance indicators of the lubricating oil in real time, such as viscosity, acid value, and moisture content, the quality status of the lubricating oil can be understood in a timely manner, and potential lubrication problems can be discovered. The monitoring method can combine online monitoring and offline monitoring. Online monitoring can obtain the performance data of the lubricating oil in real time and discover abnormal situations in a timely manner; offline monitoring can conduct a comprehensive analysis of the lubricating oil, providing a more accurate basis for lubrication management.
In conclusion, maintaining lubrication performance in harsh industrial environments faces many challenges, such as pollution and high temperature problems. These problems seriously affect the normal operation and service life of the equipment. As an effective means to solve these problems, compound additives can significantly improve the performance of the lubricating oil through their unique composition and action mechanisms, effectively coping with the test of harsh industrial environments on the lubrication performance. At the same time, reasonable lubrication management measures, including selecting appropriate compound additives, formulating a reasonable lubrication plan, and strengthening the maintenance and monitoring of the lubrication system, are crucial for ensuring the stability of the lubrication performance and the reliable operation of the equipment. In future industrial production, with the continuous development of industrial technology and the increasing complexity of industrial environments, the requirements for lubrication performance will also become higher and higher. Therefore, we need to continuously conduct in-depth research on lubrication technology, develop more efficient and environmentally friendly compound additive products, and further improve the lubrication management system to meet the new needs of industrial development and provide a strong guarantee for the efficient, stable, and sustainable development of industrial production.
The Price of Additive Packages
The price of Additive Packages varies depending on factors such as brand, specification, composition, and sales channels. If you are interested in Additive Packages, please feel free to contact us.
Supplier of Additive Packages
UNPChemicals is a professional supplier of high-quality and effective Additive Packages. We offer several remarkable products, namely Industrial Gear Oil Additives UNP IG402A,High extreme pressure (EP) type industrial gear oil additive packages UNP IG402B,Low-Odor Type Industrial Gear Oil Additive Package UNP IG402C,etc.
Industrial Gear Oil Additives UNP IG402A are a specialized class of compounds designed to enhance the performance of gear oils in various industrial applications.These additives are carefully formulated to provide a combination of properties that improve the efficiency,longevity,and reliability of gear systems.
High extreme pressure (EP) type industrial gear oil additive packages, like UNP IG402B, are specialized blends of chemical compounds designed to enhance the performance of base oils used in industrial gear lubricants. These packages are formulated to provide exceptional protection under conditions where gears experience heavy loads, high pressures, and potential metal-to-metal contact.
The Low-Odor Type Industrial Gear Oil Additive Package UNP IG402C is a specialized blend of chemical additives designed to enhance the performance of industrial gear oils while minimizing the strong odors typically associated with traditional gear oil additives, particularly those containing sulfur-based extreme pressure (EP) agents. This additive package is mixed with base oils (mineral or synthetic) to create gear lubricants that protect industrial gearboxes under demanding conditions, such as high loads and temperatures, while being more user-friendly in terms of smell—ideal for environments where odor control is a priority.
Professional Lubricant Additive Manufacturer
UNPChemicals,aka Luoyang Pacific United Petrochemical Co., Ltd., focuses on the application and development of special lubricating grease additives such as MODTC, MODTP, molybdenum amide, thiadiazole metal deactivators, and phosphate esters. With nearly 30 products in seven series, including extreme pressure anti-wear additives and special grease additives, it is a global manufacturer of special lubricating grease additives and a national high-tech enterprise with great influence and leading role in the industry. If you are looking for Lubricant Additive or technical information, feel free to contact UNPChemicals.