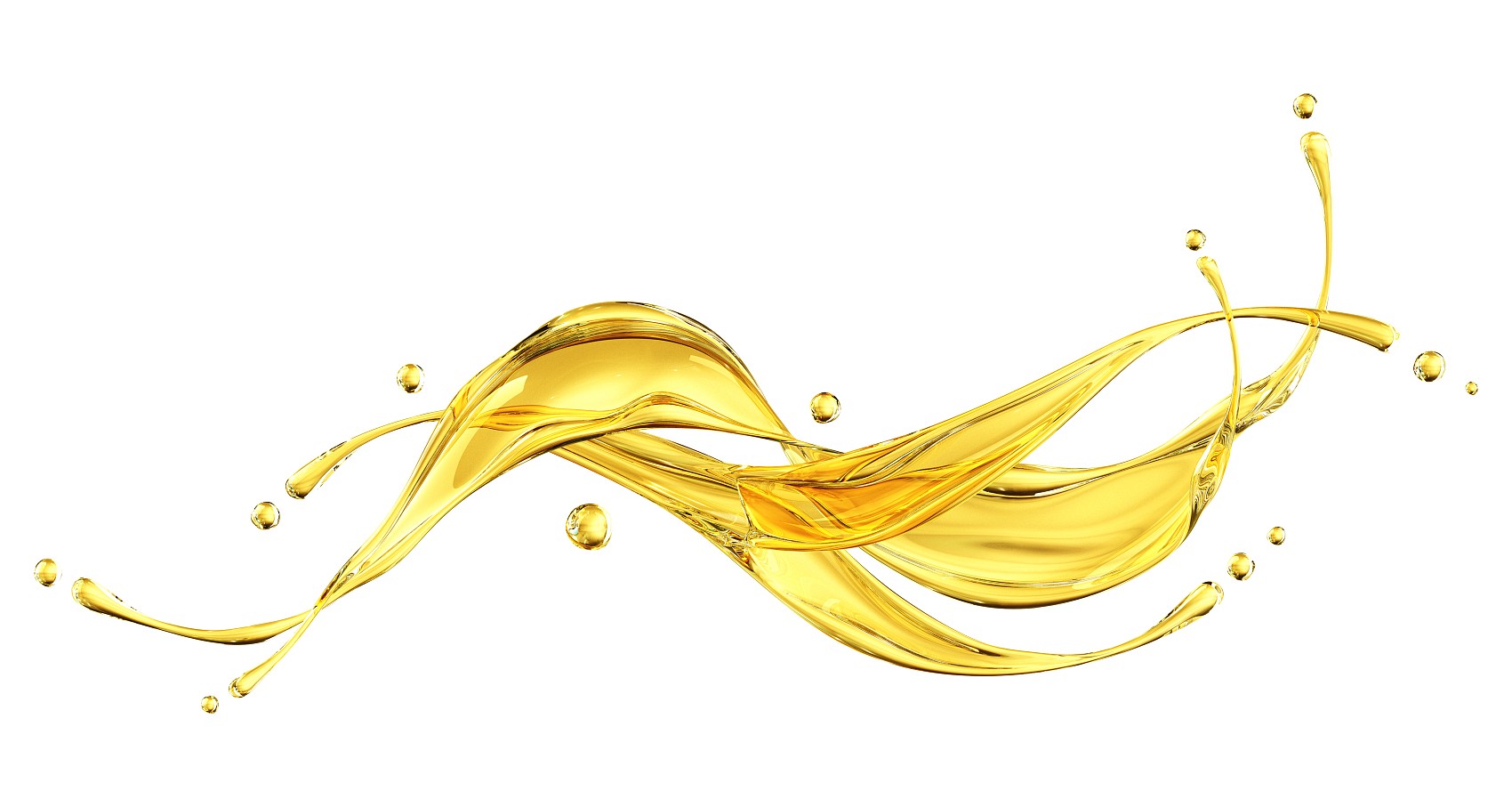
Application and Analysis of Industrial Lubricants and Additive Packages
In the modern industrial system, industrial lubricants and Additive Packages are crucial elements for ensuring the normal operation of various mechanical equipment, playing a vital and significant role in maintaining the stable operation of the equipment.
Industrial Lubricants: The Key Support for Industrial Operation
Industrial lubricants are specifically designed for various industrial equipment. Their core function is to reduce the friction and wear between equipment components, comprehensively protect the mechanical parts, and ensure the smooth and stable operation of the equipment. They are widely applied in numerous industrial fields. In the manufacturing industry, ranging from precision electronic component production equipment to large-scale automotive manufacturing production lines; in the mining industry, whether it is the underground mining excavation equipment or the surface transportation loading machinery; in the metallurgical field, from the mechanical transmission devices beside high-temperature furnaces to the large rolling mills in the steel rolling workshops; in the power industry, from the steam turbines in thermal power generation to the gearboxes in wind power generation; in the transportation sector, from the engines of large ships to the engines of logistics transportation vehicles, industrial lubricants are indispensable.
Based on different application scenarios and the specific lubrication requirements of equipment, industrial lubricants come in a wide variety. They mainly include hydraulic oil, gear oil, engine oil, compressor oil, and lubricating grease. Take the automated production line of an automobile manufacturing factory as an example. A large number of robotic arms, mechanical transmission devices, and high-precision processing equipment all require precisely matched industrial lubricants to maintain their high-precision operation. When the equipment operates at high speed, the friction between components will generate a large amount of heat. Without suitable lubricants for effective lubrication and heat dissipation, the components are prone to damage due to excessive friction heat. This not only affects production efficiency but also significantly shortens the service life of the equipment. High-quality industrial lubricants can form a uniform and stable oil film on the surface of the components, effectively reducing the friction coefficient, minimizing heat generation, and at the same time, carrying away the tiny particles generated by the friction, thus ensuring the long-term stable operation of the equipment.
Industrial Lubricant Additive Packages: The Key to Enhancing Lubricant Performance
Industrial lubricant Additive Packages are mixtures formulated with scientific and precise formulas using a variety of functional additives. These additives each possess unique properties, and when combined, they can endow base lubricants with more excellent and comprehensive characteristics. Their main components usually include antioxidants, anti-wear agents, rust inhibitors, detergents and dispersants, and extreme pressure agents.
Antioxidants can effectively resist the oxidation reaction of lubricants caused by factors such as high temperature, oxygen, and metal catalysis during the use of lubricants. The oxidation of lubricants will lead to deterioration, manifested as an increase in viscosity, a darker color, and a significant decrease in lubrication performance. Antioxidants can capture the free radicals generated during the oxidation process and interrupt the oxidation chain reaction, thereby avoiding the deterioration of the oil product and ensuring that the lubricant maintains good lubrication performance for a long time.
Anti-wear agents can significantly reduce the friction coefficient between metal surfaces and decrease wear. At the key friction parts of the equipment, such as gears, bearings, and pistons, the anti-wear agent molecules are closely adsorbed on the metal surface and undergo a chemical reaction at the high temperature generated by the friction to form a tough protective film with low shear strength. This protective film can effectively prevent the metal surfaces from direct contact and scratching, greatly extending the maintenance cycle of the equipment and reducing the equipment maintenance cost.
The main function of rust inhibitors is to prevent metal parts from rusting and corrosion. For equipment that operates in a humid environment for a long time, has frequent contact with water, or works in an environment containing corrosive gases, such as marine engines, mine drainage pumps, and the agitators of reaction vessels in chemical enterprises, the role of rust inhibitors is particularly important. The effective components in rust inhibitors can, by virtue of their special chemical structure and polarity, form a dense protective layer on the metal surface, isolating water, oxygen, and other corrosive media, and protecting the core metal parts of the equipment to ensure its normal operation in harsh environments.
Detergents and dispersants can adsorb and disperse impurities such as sludge, carbon deposits, and metal debris generated during the use of lubricants, making them evenly suspended in the oil and preventing them from depositing on the surface of the equipment. If these impurities deposit on the surface of the equipment, it will affect the heat dissipation effect of the equipment, cause the equipment to overheat, and may also hinder the normal flow of the lubricant, affecting the lubrication effect and thus the normal operation of the equipment. Detergents and dispersants keep the lubricant system clean and ensure that the interior of the equipment is in a relatively clean working environment.
Extreme pressure agents are used to deal with extreme pressure working conditions. When the equipment operates under high-load and high-pressure working conditions, such as in the forging, stamping, and rolling processes of metal processing, the ordinary lubricating oil film is easily damaged, resulting in direct contact between the metal surfaces, causing serious wear and even sintering. Extreme pressure agents can undergo a chemical reaction with the metal surface under extreme conditions of high temperature and high pressure to form a chemical reaction film with high compressive strength and anti-shear performance, effectively preventing the scratching and sintering of the metal surface and ensuring the normal operation of the equipment under extreme pressure conditions.
The Remarkable Effects of Industrial Lubricant Additive Packages
Anti-oxidation:Ensuring the Stable Performance of the Oil Product
When industrial equipment is in operation, lubricants are susceptible to oxidation reactions due to various factors such as high temperature, oxygen, and metal catalysis. The oxidation reaction will gradually deteriorate the performance of the lubricant, such as an increase in viscosity, an increase in acid value, and the generation of precipitates. These changes will not only reduce the lubrication performance of the lubricant but may also cause serious damage to the equipment. The antioxidants in industrial lubricant Additive Packages can capture the free radicals generated during the oxidation process and interrupt the oxidation chain reaction, effectively slowing down the oxidation rate of the lubricant, avoiding the deterioration of the oil product, ensuring that the lubricant maintains good lubrication performance for a long time, extending the service life of the lubricant, and reducing the failures and downtime of the equipment caused by lubricant oxidation problems.
Anti-wear:Prolonging the Service Life of Key Equipment Components
During the operation of industrial equipment, friction between metal surfaces is inevitable, especially at key friction parts such as gears, bearings, and pistons, which bear huge pressure and friction force. Without effective anti-wear protection measures, the metal surfaces are prone to wear, resulting in a decrease in the accuracy of the equipment, deterioration of performance, and even failures. The anti-wear agents in industrial lubricant Additive Packages can form a tough protective film at the key friction parts of the equipment. Under extreme working conditions such as heavy load, high-speed operation, and high-load impact, they can effectively prevent the metal surfaces from direct contact and scratching, greatly extending the service life of the key components of the equipment, reducing the equipment maintenance cost and replacement frequency, and improving the operation efficiency and reliability of the equipment.
Anti-rust and Anti-corrosion:Protecting the Core Components of the Equipment
The rusting and corrosion of metal parts are common problems faced by industrial equipment. In humid environments, in situations with frequent contact with water, and in industrial environments containing corrosive gases, metal parts are more vulnerable to corrosion threats. Once the metal parts are corroded, not only will their strength and accuracy be reduced, but it may also lead to serious failures such as equipment leakage and blockage, affecting the normal operation of the equipment and even causing safety accidents. The rust inhibitors in industrial lubricant Additive Packages can form a dense protective layer on the metal surface, isolating water, oxygen, and other corrosive media from the metal contact, protecting the core components of the equipment, and ensuring the safe and stable operation of the equipment in harsh working environments.
Detergency and Dispersancy:Maintaining the Cleanliness Inside the Equipment
During the use of industrial lubricants, due to factors such as the oxidation of the oil product, the wear of equipment components, and the intrusion of external impurities, impurities such as sludge, carbon deposits, and metal debris will gradually be generated in the lubricant. If these impurities deposit inside the equipment, it will seriously affect the heat dissipation effect, lubrication performance, and normal operation of the equipment. The detergents and dispersants in industrial lubricant Additive Packages can adsorb and disperse these impurities, making them evenly suspended in the oil and preventing them from depositing on the surface of the equipment. This not only keeps the interior of the equipment clean but also ensures the normal flow of the lubricant and the lubrication effect, extending the service life of the equipment and improving the operation efficiency of the equipment.
Why Use Industrial Lubricant Additive Packages?
Performance Enhancement, Adapting to Complex Industrial Working Conditions
In modern industrial production, industrial equipment faces increasingly complex and variable working conditions, such as high temperature, high pressure, high load, high-speed operation, humid environment, and corrosive media. Pure base oil is often unable to meet the performance requirements of lubricants for these complex working conditions. However, industrial lubricant Additive Packages can, through the synergistic effect of multiple additives, specifically enhance various performances of the lubricant, enabling it to adapt to various extreme conditions. For example, in a high-temperature environment, antioxidants and anti-wear agents can prevent the oxidation and wear of the lubricant; under high-pressure and high-load working conditions, extreme pressure agents and anti-wear agents can provide strong anti-wear protection; in a humid environment, rust inhibitors can ensure that the metal parts are not corroded. Using industrial lubricant Additive Packages can significantly improve the operation stability and reliability of the equipment, ensure the efficient operation of the equipment under complex and variable industrial working conditions, and reduce the huge losses caused by unexpected downtime due to equipment failures.
Extending the Service Life of the Oil Product, Reducing Costs and Improving Efficiency
The service life of industrial lubricants is directly related to the equipment maintenance cost and the economic benefits of the enterprise. When the equipment is in operation, the lubricant will gradually deteriorate due to factors such as oxidation, contamination, and wear. When the performance of the lubricant drops to a certain extent, it needs to be replaced. Frequent replacement of lubricants not only increases the oil consumption cost of the enterprise but also leads to equipment downtime, affecting production efficiency. Industrial lubricant Additive Packages can effectively inhibit the deterioration rate of the lubricant through their functions of anti-oxidation, anti-contamination, and anti-wear, and extend the service life of the lubricant. For example, antioxidants can slow down the oxidation process of the lubricant and reduce the deterioration of the oil product; detergents and dispersants can adsorb and disperse impurities in the oil to prevent the impurities from affecting the performance of the oil product; anti-wear agents can reduce the wear of equipment components and lower the contamination of the oil product by wear particles. Using industrial lubricant Additive Packages can greatly reduce the replacement frequency of lubricants, lower the oil consumption cost and equipment maintenance cost of the enterprise, and improve the economic benefits of the enterprise.
Comprehensive Equipment Protection, Upgrading Equipment Protection
Industrial equipment is an important fixed asset of an enterprise, and its normal operation is related to the production efficiency and economic benefits of the enterprise. Industrial lubricant Additive Packages provide a one-stop lubrication solution for the equipment, comprehensively protecting the equipment from multiple aspects such as anti-wear, anti-rust, detergency and dispersancy, anti-oxidation, and extreme pressure protection. Using industrial lubricant Additive Packages can effectively reduce the failure rate of the equipment, extend the overall service life of the equipment, reduce the equipment maintenance and replacement costs, and provide a strong guarantee for the preservation and appreciation of the enterprise's fixed assets. For example, in a large factory, the equipment using industrial lubricant Additive Packages has significantly fewer maintenance times and a significantly extended service life, which not only improves production efficiency but also reduces the equipment investment cost of the enterprise.
The Working Principle of Industrial Lubricant Additive Packages
The additives of different components in industrial lubricant Additive Packages play their roles according to their respective unique chemical properties and physical properties, and they cooperate and synergize with each other to build an efficient lubrication protection system. Antioxidants interrupt the chain reaction by capturing free radicals during the oxidation process of the lubricant. When the lubricant starts to oxidize due to factors such as high temperature and oxygen, a large number of free radicals will be generated, which will continuously trigger new oxidation reactions, leading to the rapid deterioration of the oil product. The antioxidant molecules can react with the free radicals to stabilize them, preventing the further spread of the oxidation reaction and maintaining the good performance of the lubricant.
Anti-wear agent molecules have a special chemical structure and can undergo physical adsorption and chemical adsorption on the metal friction surface. When the equipment is operating normally, the anti-wear agent molecules form a thin protective film on the metal surface through physical adsorption; when the temperature and pressure of the friction surface increase, the anti-wear agent molecules will undergo a chemical reaction to form a chemical reaction film with low shear strength, separating the metal surfaces and reducing friction and wear.
The working principle of rust inhibitors is based on the polarity and chemical activity of their molecules. The polar groups in the rust inhibitor molecules can undergo a chemical reaction with the atoms on the metal surface to form strong chemical bonds, tightly adsorbing on the metal surface; the non-polar groups extend outward to form a hydrophobic and oxygen-isolating barrier, preventing water, oxygen, and other corrosive media from contacting the metal, thus achieving the purpose of rust and corrosion prevention.
Detergents and dispersants have surface activity, with one end of the molecule being a lipophilic group and the other end being a hydrophilic group. When impurities such as sludge and carbon deposits appear in the lubricant, the lipophilic groups of the detergents and dispersants will adsorb on the surface of the impurities, and the hydrophilic groups will face outward, wrapping the impurities and making them evenly dispersed in the oil. In this way, the impurities will not deposit on the surface of the equipment but will be carried away with the flow of the oil, keeping the interior of the equipment clean.
When the equipment is in operation, these additives will dynamically adjust their effects according to the operating status and working conditions of the equipment. When the equipment is in a high-load and high-temperature operating state, the anti-wear agents and extreme pressure agents will quickly play their roles to enhance the protection of the metal surface; when the equipment is in a humid environment, the rust inhibitors will work more actively to ensure that the metal parts are not corroded. They cooperate with each other and continuously optimize the lubrication environment to provide comprehensive and efficient lubrication protection for the equipment.
Types of Industrial Lubricant Additive Packages
Single-agent Compound, Focusing on Specific Performance Enhancement
Single-agent compound industrial lubricant Additive Packages focus on strengthening a specific performance to meet the special requirements of specific industrial equipment or processes for a certain aspect of the lubricant's performance. For example, specialized extreme pressure anti-wear Additive Packages are mainly used for metal processing equipment that bears huge pressure, such as forging machines, stamping machines, and rolling mills. When these equipment are working, extremely high pressure and friction force are generated between the metal parts. If the anti-wear performance of the lubricant is insufficient, the metal surface is prone to wear, scratching, or even sintering, affecting the processing accuracy and the service life of the equipment. Extreme pressure anti-wear Additive Packages can form a high-strength and high-toughness protective film on the metal surface by adding high-performance anti-wear agents and extreme pressure agents, effectively resisting wear under high-pressure and high-friction conditions, ensuring the sharpness of the cutting tools and the processing accuracy of the workpieces, and improving the efficiency and quality of metal processing.
Multifunctional Compound, Meeting the Needs of General Equipment
Multifunctional compound industrial lubricant Additive Packages integrate multiple functions such as anti-oxidation, anti-wear, anti-rust, and detergency and dispersancy, and are suitable for general industrial equipment. Common general machine tools, fans, pumps, and other equipment in factory workshops have relatively complex working conditions and require lubricants with multiple performances. The lubricants formulated with multifunctional Additive Packages can meet the lubrication requirements of these equipment under different working conditions, with simple operation and strong adaptability. For example, when a general machine tool is in operation, it requires the lubricant to have good anti-wear performance to ensure the normal operation of transmission components such as gears and lead screws; it also needs to have anti-oxidation performance to prevent the lubricant from deteriorating during long-term use; anti-rust performance is also required to protect the metal parts from corrosion in a humid environment; at the same time, detergency and dispersancy performance is indispensable to ensure that the impurities in the lubricant do not deposit on the surface of the equipment. The lubricants formulated with multifunctional Additive Packages can meet these requirements simultaneously, providing comprehensive and reliable lubrication protection for general equipment, reducing the equipment maintenance cost and failure rate, and improving the operation efficiency of the equipment.
In conclusion, industrial lubricant Additive Packages play an important role in the modern industrial field. They are the key to ensuring equipment lubrication and maintenance and also an important force in promoting the efficient production of various industries. With the continuous development and progress of industrial technology, the performance requirements for industrial lubricant Additive Packages will become higher and higher. In the future, the research, development, and application of industrial lubricant Additive Packages will have a broader space for development, providing a more solid guarantee for the continuous innovation and development of the industrial field.
The Price of Additive Packages
The price of Additive Packages varies depending on factors such as brand, specification, composition, and sales channels. If you are interested in Additive Packages, please feel free to contact us.
Supplier of Additive Packages
UNPChemicals is a professional supplier of high-quality and effective Additive Packages. We offer several remarkable products, namely High zinc hydraulic oil additives UNP AH502A,Low Zinc Hydraulic Oil Additives UNP AH502B,Zinc-free Hydraulic Oil Additives UNP AH502C,etc.
High zinc hydraulic oil additives UNP AH502A are a type of chemical additive used in hydraulic oils that contain high levels of zinc dialkyldithiophosphate (ZDDP). ZDDP is a well-known anti-wear agent that also provides antioxidant, anti-corrosion, and anti-foam properties. The zinc in these additives plays a crucial role in forming a protective film on metal surfaces within the hydraulic system, thereby reducing wear and extending the life of the system components.
Low Zinc Hydraulic Oil Additives UNP AH502B are a class of advanced lubricant additives designed to enhance the performance of hydraulic oils with reduced zinc content.These additives are formulated to provide a balance of anti-wear,extreme pressure,and antioxidant properties,making them suitable for modern hydraulic systems that demand high performance with lower environmental impact.
Zinc-free Hydraulic Oil Additives UNP AH502C are a new class of environmentally friendly lubricant additives designed for hydraulic systems.These additives are formulated to provide the same level of performance as traditional zinc-containing additives but without the heavy metal content,reducing the environmental impact of hydraulic fluids.
Professional Lubricant Additive Manufacturer
UNPChemicals, aka Luoyang Pacific United Petrochemical Co., Ltd., focuses on the application and development of special lubricating grease additives such as MODTC, MODTP, molybdenum amide, thiadiazole metal deactivators, and phosphate esters. With nearly 30 products in seven series, including extreme pressure anti-wear additives and special grease additives, it is a global manufacturer of special lubricating grease additives and a national high-tech enterprise with great influence and leading role in the industry. If you are looking for Lubricant Additive or technical information, feel free to contact UNPChemicals.