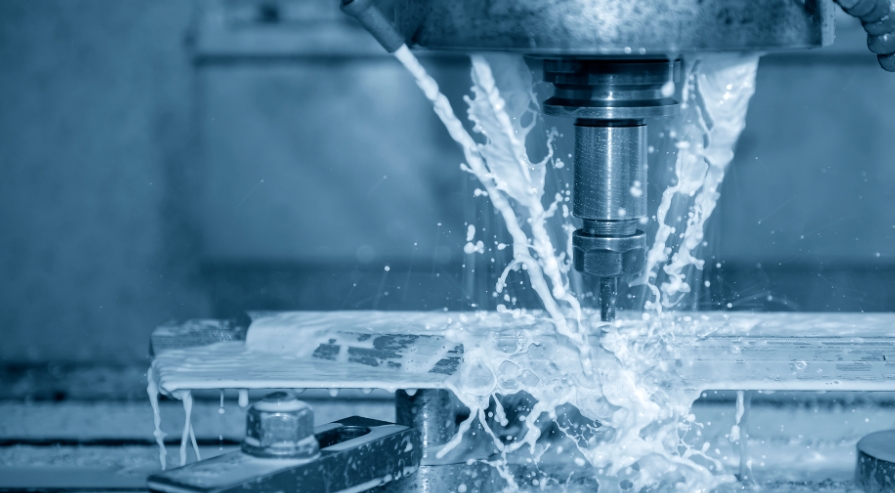
A comprehensive introduction to metal working fluid additives
What are Metalworking Fluid Additives?
Metalworking fluid additives are chemical compounds added to metalworking fluids to enhance their performance in various metalworking processes, such as cutting, grinding, forming, and metal removal. They improve the lubrication, cooling, chip removal, corrosion resistance, and emulsion stability properties of fluids, ensuring smooth operation, reducing tool wear, and extending the life of the fluids.
Advantages of Metalworking Fluid Additives
Metalworking fluid additives offer numerous advantages to various metalworking processes, such as cutting, grinding, forming, and metal removal, by enhancing the performance of the base fluids:
Improved Lubrication:
Additives enhance the lubrication properties of metalworking fluids, reducing friction between the tool and workpiece, improving surface finish quality, and facilitating smooth and efficient operations.
Better Cooling:
They help dissipate heat generated during metalworking processes, preventing overheating, protecting both tools and workpieces from thermal damage, and ensuring the longevity of tools and equipment.
Enhanced Emulsion Stability:
In water-miscible metalworking fluids, additives like emulsifiers contribute to increased emulsion stability, ensuring consistent fluid performance throughout the process.
Corrosion Protection:
Corrosion inhibitors prevent rust and metal corrosion on workpieces, tools, and equipment, extending their useful life, preserving product quality, and minimizing production downtime.
Biostatic Properties:
Biocides control the growth of bacteria, fungi, and other microorganisms that can cause foul odors, fluid degradation, and corrosion, keeping metalworking fluids functioning effectively and maintaining a cleaner working environment.
Foam Control:
Defoamants minimize foam formation in metalworking fluids, optimizing performance by preventing inefficient heat transfer, lubrication loss, and potential workpiece contamination.
Extreme Pressure and Anti-Wear Protection:
Some additives, like extreme pressure agents, provide added protection against wear and metal-to-metal contact under heavy loads, prolonging tool life, and ensuring smooth operations.
Increased Tool Life:
Enhanced fluid performance through the use of additives leads to reduced tool wear, contributing to longer tool life and lower replacement costs.
Improved Surface Finish:
Metalworking fluid additives can help ensure a better surface finish on final products by reducing friction and minimizing heat-induced damage during the process.
Cost Efficiency:
Enhanced fluid performance, extended tool life, and reduced fluid maintenance requirements as a result of using metalworking fluid additives contribute to overall cost efficiency in the production process.
These advantages make metalworking fluid additives an essential component for a wide range of industries and applications, as they enable effective, efficient, and high-quality metalworking processes that meet industry-specific demands.
The Importance of Metalworking Fluid Additives in Metalworking Processes
Metalworking fluid additives play a crucial role in enhancing the performance of metalworking fluids, providing a range of benefits and significantly impacting the efficiency and outcomes of metalworking processes. Understanding their importance in various metalworking operations can help ensure optimal results across industries and applications.
Improved Lubrication: Additives improve the lubrication capabilities of metalworking fluids, allowing smoother operations by reducing friction between the cutting tool and workpiece. This results in less tool wear, longer tool life, and a better surface finish on the final product.
Enhanced Cooling: During metalworking processes, additives maintain appropriate temperature levels by dissipating the heat generated, which prevents thermal damage to workpieces, tools, and equipment. This improves process efficiency and prevents component failure or deformation.
Corrosion Prevention: Metalworking fluid additives protect metal surfaces from rust and corrosion, prolonging the life of tools, machines, and workpieces, minimizing maintenance and replacement costs, and ensuring better product quality.
Stable Fluid Performance: Additives like emulsifiers help stabilize emulsion properties in water-based fluids, ensuring consistent fluid performance and preventing issues arising from phase separation or emulsion breakdown.
Biological Control: Metalworking fluid additives like biocides mitigate microbial growth that can cause foul odors, fluid degradation, and corrosion, sustaining fluid performance and maintaining a cleaner, healthier work environment.
Enhanced Process Efficiency: The use of additives results in improved fluid performance that contributes to higher metal removal rates, faster cutting speeds, and reduced downtime, making overall metalworking processes more efficient.
Better Surface Finish: Additives help reduce friction, minimize heat-induced surface damage, and maintain fluid cleanliness, which contributes to superior surface quality for the finished components.
Cost Savings: By prolonging tool life, reducing fluid maintenance requirements, and minimizing machine downtime, metalworking fluid additives contribute to cost savings in terms of reduced operational and maintenance expenditures.
Adaptability: Advances in metalworking processes and materials necessitate the development and use of specialized additives, capable of addressing particular requirements, such as operating temperature, cutting characteristics, or material hardness, ensuring optimal results in diverse applications.
In conclusion, the importance of metalworking fluid additives lies in their ability to enhance the functional properties of base fluids and optimize process efficiency, tool life, and finished product quality across various industries and applications. By understanding this importance and selecting the suitable additives tailored to specific needs, metalworking processes can be conducted smoothly and effectively.
Detailed Types of Metalworking Fluid Additives
Metalworking fluid additives encompass a diverse range of compounds designed to enhance the performance of base fluids across a variety of metalworking processes. These additives address specific application requirements, enabling optimal operational efficiency and product quality. Below are detailed descriptions of common metalworking fluid additive types:
Lubricity Agents:
Lubricity agents, such as fatty acids, esters, and vegetable oils, serve to improve the lubrication properties of metalworking fluids. By reducing friction between cutting tools and workpieces, they help minimize heat generation, extend tool life, and improve surface finish quality.
Extreme Pressure Additives:
These additives, which include sulfur-based compounds, chlorinated paraffin, and phosphorus-based agents, are used to protect metal surfaces during heavy load cutting and grinding operations. They react with the metal surface, forming a low friction, chemically resistant film that protects metal-to-metal contact areas, enabling heavy load protection and enhanced tool life.
Corrosion Inhibitors:
Corrosion inhibitors, such as amines, carboxylic acids, and phosphoric acid esters, defend against rust and corrosion on metal parts and equipment. They work either by forming a protective film on the metal surfaces or by neutralizing the corrosive environment within the fluid. This protection prolongs the life of tools, equipment, and workpieces.
Emulsifiers:
Essential for stabilizing oil-in-water or water-in-oil emulsions in water-based metalworking fluids, emulsifiers maintain homogeneity and consistent performance throughout the process. Common emulsifiers include sulfonates, fatty alcohols, and non-ionic surfactants.
Biocides:
Biocides, such as formaldehyde-releasing agents, isothiazolones, and quaternary ammonium compounds, control microbial growth, like bacteria, fungi, and algae, in metalworking fluids. Their usage prevents fluid degradation, foul odors, and potential health risks to workers.
Defoamants:
Some types of operations may cause unwanted foam formation in metalworking fluids, which can impair their performance and reduce heat transfer and lubrication. Defoamants, like silicone-based compounds and polyglycols, effectively control and reduce foam formation, ensuring optimal fluid performance.
Anti-Mist Agents:
High-speed machining operations can generate airborne oil mist, posing inhalation risks to workers and contaminating the work environment. Anti-mist agents help minimize the formation of mist, improving workplace conditions and reducing health hazards.
Coupling Agents:
Coupling agents optimize the balance between oil and water in emulsified metalworking fluids, maintaining emulsion stability and performance at higher concentrations. These additives also prevent separation of the different components under varying operational conditions.
Understanding these detailed types of metalworking fluid additives aids in selecting the appropriate formulation to meet application-specific requirements and achieve efficient and superior results in various metalworking processes.
What Effect Can Metalworking Fluid Additives Achieve?
Metalworking fluid additives can achieve a range of positive effects on base fluids, leading to enhanced performance, improved operational efficiency, and better product quality across various metalworking processes. Some notable effects of metalworking fluid additives are:
Improved Lubrication: Additives enhance lubrication properties of fluids, resulting in reduced friction between the cutting tool and workpiece, ultimately leading to smoother operations, minimized wear, and a superior surface finish on the final product.
Enhanced Cooling: By dissipating the heat generated during metalworking processes, additives ensure more effective cooling and prevent overheating, protecting both tools and workpieces from thermal damage and maintaining the longevity of tools and equipment.
Corrosion Prevention: The inclusion of corrosion inhibitors protects metal surfaces from rust and corrosion, extending the life of tools, machines, and workpieces, minimizing maintenance and replacement costs, and ensuring better product quality.
Emulsion Stability: Additives, particularly emulsifiers, help maintain the stability of emulsions in water-based fluids, ensuring consistent fluid performance, smooth operations, and preventing issues arising from phase separation or emulsion breakdown.
Biological Control: Additives like biocides mitigate microbial growth in fluids, thwarting fluid degradation, foul odors, and corrosion, sustaining fluid performance, and maintaining a cleaner, healthier work environment.
Foaming Reduction: Defoamants minimize foam formation in fluids, optimizing performance by preventing heat transfer reduction, lubrication loss, and potential workpiece contamination.
Heavy Load Protection: Extreme pressure additives provide protection under heavy loads by creating low-friction, chemically resistant films on metal surfaces, prolonging tool life and ensuring smooth operations.
Extended Tool and Fluid Life: The enhanced fluid properties achieved by using metalworking fluid additives contribute to longer tool life and reduced fluid maintenance requirements, leading to cost savings and reduced waste generation.
Improved Surface Finish: Additives that help reduce friction and maintain fluid cleanliness allow for a better surface finish on finished components, meeting the high-quality standards and precision requirements in various industries.
Application Cases of Metalworking Fluid Additives
Metalworking fluid additives are widely used across various industries to enhance the performance of base fluids, ensuring optimal operational efficiency, tool life, and product quality. The following are some application cases where metalworking fluid additives are employed:
Automotive Manufacturing: Metalworking fluid additives are used in milling, turning, drilling, and grinding operations for automotive components. They play a crucial role in processes such as engine block and cylinder head machining, gear cutting, and production of engine parts, bearings, and other critical components.
Aerospace Industry: In the aerospace sector, additives are used for the machining and finishing of aerospace parts made from high-strength alloys, superalloys, and composites. They help enhance cooling, lubrication, and surface finish, ensuring precision and compliance with stringent industry specifications.
Heavy Machinery: Metalworking fluid additives play an essential role in cutting, shaping, and forming processes for large equipment used in construction, agriculture, and mining industries. Additives help address challenges related to high operating temperatures, extreme pressures, and materials with complex compositions.
Metal Fabrication: Metal fabrication processes, including cutting, bending, and shaping of sheet metal and structural steel, require metalworking fluid additives for improved process efficiency and product quality. Additives enhance lubrication, cooling, and corrosion protection during processes like laser cutting, punching, and stamping.
Electronic Manufacturing: In the electronics industry, additives help optimize metalworking processes for the production of components and devices, such as connectors, heat sinks, and chassis parts. They promote precision and high-quality surface finishes necessary for meeting strict manufacturing tolerances.
Medical Device Manufacturing: Metalworking fluid additives are used in the production of medical devices and implants, particularly for machining and finishing operations of materials like titanium and stainless steel. They contribute to achieving high precision, superior surface finish, and strict adherence to medical industry specifications.
Oil and Gas: Additives enable the efficient machining and production of specialized components for the oil and gas industry, such as valves, drilling equipment, pipelines, and fittings, facilitating operations in challenging environments with high-pressure, high-temperature, and corrosive conditions.
Railway Industry: In the manufacture of railway components, such as rails, wheels, axles, and couplings, metalworking fluid additives support machining and forming operations for materials like high-strength steel and wear-resistant alloys, delivering better performance, extended tool life, and corrosion protection.
What Should I Consider When Choosing Metalworking Fluid Additives?
When choosing metalworking fluid additives, it is essential to take into account several factors to ensure optimal performance, efficient operation, and consistent results across your metalworking processes. Here are some key factors to consider:
Compatibility: Ensure that the selected additives are compatible with the base fluids, other additives within the formulation, the machinery, operating conditions, and the materials being processed. Incompatible additives may cause adverse reactions, fluid degradation, or poor performance.
Effectiveness: Assess the effectiveness of the additives in meeting your specific application requirements, such as lubrication, cooling, and corrosion protection. Choose additives that provide the necessary performance enhancements based on your process and material needs.
Safety, Health, and Environmental Considerations: Opt for metalworking fluid additives with low toxicity, reduced environmental impact, and compliance with safety regulations to minimize potential risks for workers and the environment. Ensure proper handling, storage, and disposal practices are followed.
Supplier Reputation and Product Quality: Evaluate the supplier's reputation in the industry and ascertain the quality of their products. Seek recommendations, read reviews, and consult industry resources to make informed decisions about potential additives and suppliers.
Industry-Specific Requirements: Consider the unique requirements of your industry when selecting additives. These may include regulations, material compatibility, production rate, or precision specifications.
Cost Efficiency: Keep in mind the overall cost of the additives while making your decision. Analyze factors like the price per unit, the required concentration levels, and the potential cost savings that may be achieved by using these additives to optimize your operations.
Customization Possibilities: In some cases, custom-formulated additives might be necessary to address specific metalworking process needs. Determine whether the supplier can offer tailored solutions that cater to your unique requirements.
Support and Technical Expertise: Gauge the supplier's level of technical expertise and their ability to provide support and guidance on proper usage, monitoring, and maintenance of the additives.
By carefully considering these factors and conducting thorough research, you can choose the right metalworking fluid additives that will address your specific requirements, optimize your processes, and improve the overall efficiency of your metalworking operations.
Several Metalworking Fluid Additives Top global suppliers
There are several prominent global suppliers known for their high-quality metalworking fluid additives and exceptional customer support. Some of the top suppliers include:
Lubrizol Corporation:
Lubrizol is a leading chemical company that produces a wide range of metalworking fluid additives, such as corrosion inhibitors, emulsifiers, and extreme pressure agents. Their additives cater to various applications, including cutting, forming, grinding, and metal removal operations.
FUCHS Lubricants:
FUCHS is a world-renowned lubricant manufacturer, offering an extensive range of specialized metalworking fluid additives for different industries like automotive, aerospace, and heavy machinery. They also provide technical support and customized solutions tailored to specific applications.
Chevron Oronite:
Chevron Oronite is known for their high-quality metalworking fluid additives, including lubricating oils and grease additives, corrosion inhibitors, and biocidal agents. They serve a diverse range of industries and are recognized for their focus on reliable performance, application expertise, and customer support.
Dow:
Dow is a leading global supplier of specialty chemicals, including a wide array of metalworking fluid additives, such as emulsifiers, corrosion inhibitors, biocides, and defoamers. They serve numerous industries and applications in the metalworking sector, offering technical support and innovative solutions to their customers.
Evonik Industries:
Evonik offers a comprehensive range of metalworking fluid additives for cutting fluids, forming oils, and grinding operations. They are known for their focus on sustainability, innovation, and high-performance additives, catering to various metalworking applications.
Afton Chemical:
Afton Chemical specializes in the development and production of high-quality metalworking fluid additives, including extreme pressure agents, anti-wear additives, and corrosion inhibitors. They are recognized for their strong research and development capabilities, application expertise, and customer-centric approach.
Croda International:
Croda International is a global chemical company offering a variety of metalworking fluid additives, such as lubricity enhancers, corrosion inhibitors, and ester-based base fluids. They provide bio-based and sustainable additive solutions, making them an environmentally friendly choice in the industry.
UNP Chemical:
A professional lubricant additive manufacturer and supplier in China specializing in special lubricants and metal processing additives, oilfield chemicals, and synthetic material auxiliaries, Organic molybdenum friction modifiers (MoDTP, MoDTC). thiazole metal deactivators, phosphate ester extreme pressure and anti-wear agents, and grease additives.
Professional Lubricant Additive Manufacturer UNPChemicals in China
UNPChemicals, also known as Luoyang United Pacific Petrochemical Co., Ltd. (LPUPC), focuses on the application and development of special lubricating grease additives such as MODTC, MODTP, molybdenum amide, thiadiazole metal deactivators, and phosphate esters. With nearly 30 products in seven series, including extreme pressure anti-wear agents and special grease additives, it is a global manufacturer of special lubricating grease additives and a national high-tech enterprise with great influence and leading role in the industry. If you are interested in Metalworking Fluid Additives, try some samples, feel free to contact UNP chemicals.