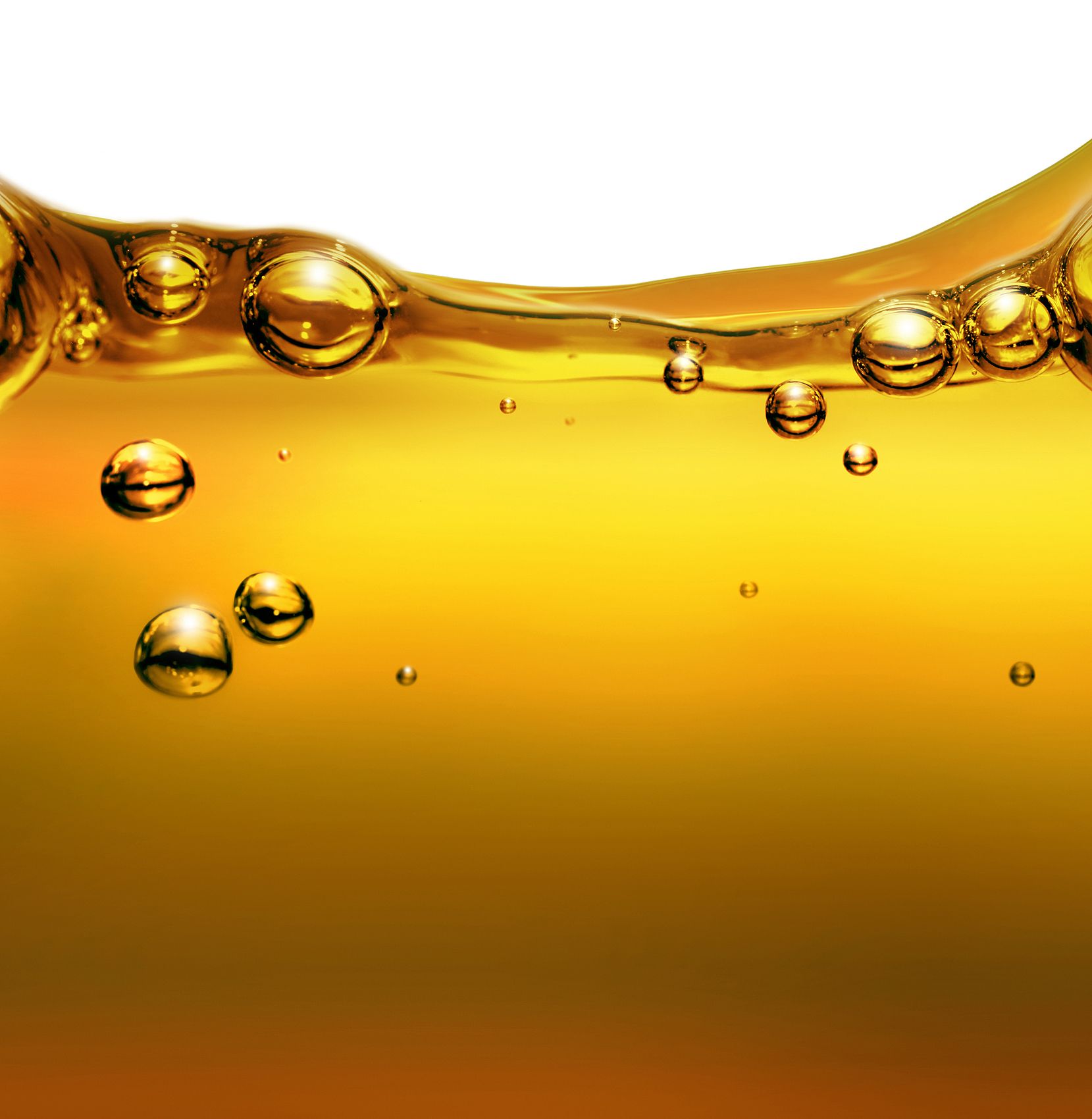
Understand Friction Modifiers to Enhance Mechanical Performance
In the complex world of mechanical operation, friction, a seemingly ordinary yet far - reaching physical phenomenon, has always been a "persistent problem" that plagues the efficient and stable operation of machinery. Understanding the nature of friction and its different forms is the key to finding solutions.How Does Friction Occur?
During the operation of machinery, the principle of friction generation is based on the microscopic interaction between the surfaces of objects in contact. When two objects come into contact and have a relative motion tendency or are already in relative motion, friction will occur.
Dry friction is the most basic form of friction. It refers to the friction that occurs when two solid surfaces come into direct contact and move relative to each other without any lubricant. This type of friction is often accompanied by relatively large frictional forces, which can lead to severe wear and energy consumption. For example, in early mechanical devices, without proper lubrication measures, the dry friction between metal parts would make the equipment extremely difficult to operate and could even cause serious damage to the parts in a short period.
Boundary friction is the friction state when there is an extremely thin lubricating film between two relatively moving surfaces. The thickness of this lubricating film usually ranges from a few molecular layers to dozens of microns. Although it can reduce friction to a certain extent, due to its thinness, it is not sufficient to completely separate the two surfaces, and there will still be some direct contact between the metal surfaces, resulting in a certain amount of frictional force and wear. Boundary friction is relatively common in some low - speed, heavy - load, or high - temperature working conditions.
Fluid friction is a more ideal friction state. At this time, the two relatively moving surfaces are completely separated by a continuous lubricating fluid with a certain thickness, and the frictional force mainly comes from the viscous resistance inside the fluid. In this case, the friction coefficient is relatively low, the wear of the equipment is greatly reduced, and energy consumption can also be effectively controlled. For example, in a modern automobile engine, under normal operating conditions, the lubrication between the piston and the cylinder wall is basically in a state of fluid friction.
Numerous studies and practical cases have shown that friction has a serious negative impact on energy consumption, equipment wear, and service life. Statistics show that in the industrial field, approximately 30% - 50% of energy consumption is due to overcoming frictional resistance. In the automotive industry, the frictional losses inside the engine can account for 10% - 20% of the total energy losses. At the same time, equipment wear caused by friction is also one of the main causes of equipment failures and maintenance. For example, an industrial gearbox without proper lubrication measures, after running continuously for thousands of hours, will experience severe wear on the gear surface, leading to changes in the tooth shape, which in turn affects the normal operation of the entire equipment and greatly shortens the service life of the equipment.
The Role of Friction Modifiers
Facing the various problems brought about by friction, friction modifiers have emerged as the times require. A friction modifier is a type of additive that can significantly reduce the friction coefficient and wear, thereby improving the operating efficiency and service life of mechanical equipment. In the lubricating oil system, it occupies a unique and indispensable position. Lubricating oil, as the "blood" of mechanical equipment, mainly plays the roles of lubrication, cooling, cleaning, and rust prevention. The addition of friction modifiers further enhances the lubrication performance of the lubricating oil, enabling it to better cope with various complex working conditions.
Friction modifiers can be classified into different types according to their physical forms and action methods. Oil - soluble friction modifiers can completely dissolve in lubricating oil to form a homogeneous solution. This type of friction modifier usually has good low - temperature performance and dispersibility, can quickly take effect in a low - temperature environment, and remains stable in lubricating oil for a long time. For example, some fatty acid esters, which are oil - soluble friction modifiers, are widely used in automobile engine lubricating oil and can effectively reduce the friction between internal engine parts.
Solid - suspended friction modifiers are in the form of tiny solid particles suspended in lubricating oil. These solid particles usually have special crystal structures and physical properties, such as graphite and molybdenum disulfide. They can form a solid film with good lubrication performance on the friction surface and exhibit excellent friction - reducing performance under extreme working conditions such as high temperature and heavy load. For example, in the gear transmission systems of some large - scale industrial equipment, adding solid - suspended friction modifiers can effectively reduce the wear between gears and improve the reliability of the equipment.
The Action Principle of Friction Modifiers
Among numerous friction modifiers, organic molybdenum friction modifiers have received much attention due to their unique molecular structures and excellent friction - reducing properties. The molecular structure of organic molybdenum friction modifiers contains molybdenum elements, and molybdenum atoms are connected to organic groups through chemical bonds. This special structure gives organic molybdenum friction modifiers good solubility and stability in lubricating oil, and at the same time, they can undergo a series of complex physical and chemical reactions on the metal surface.
When an organic molybdenum friction modifier is added to lubricating oil and comes into contact with the metal surface, under the action of frictional heat and mechanical force, its molecules will decompose and undergo chemical reactions. The organic groups will first adsorb on the metal surface to form a physical adsorption film, which can reduce the energy of the metal surface and decrease the friction coefficient. As the friction continues, the molybdenum atoms will react chemically with the metal surface to form a protective film containing molybdenum compounds, such as molybdenum sulfide and molybdenum oxide. This protective film has extremely low shear strength and good wear resistance, which can effectively isolate the metal surface and further reduce the friction coefficient.
With the help of advanced simulation experimental techniques, we can clearly observe the dynamic process of the formation of a protective film by the organic molybdenum friction modifier on the metal surface and the reduction of the friction coefficient. In the simulation experiment, through a high - resolution microscope and a friction coefficient testing device, we can see that in the initial stage of friction, the organic molybdenum molecules quickly adsorb on the metal surface, and the friction coefficient begins to gradually decrease. As the friction time increases, the chemical reaction gradually proceeds, the protective film gradually forms and becomes more complete, and the friction coefficient further decreases and stabilizes. Experimental data show that after adding an appropriate amount of organic molybdenum friction modifier, the friction coefficient can be reduced by 30% - 50%, significantly improving the lubrication performance of the equipment.
What Are the Types of Friction Modifiers?
There are a wide variety of friction modifiers, and the common types are as follows:
Classification by Chemical Composition
Organic Friction Modifiers:
Fatty Acids and Their Esters: Fatty acids and their esters are obtained through chemical reactions from animal and plant oils or petrochemical products. For example, fatty acids such as oleic acid and stearic acid, and fatty acid esters such as methyl oleate and ethyl stearate. Their molecular structures contain long - chain hydrocarbon groups and polar carboxyl or ester groups. The polar groups can adsorb on the metal surface, and the hydrocarbon groups play a lubricating role, thus reducing friction. They are commonly used in fields such as lubricating oil and metalworking fluids and can effectively reduce friction between metals.
Organic Molybdenum Compounds: Common ones include molybdenum dialkyldithiophosphate (MoDDP), molybdenum dialkyldithiocarbamate (MoDTC), etc. In their molecular structures, molybdenum atoms form special chemical bonds with sulfur, phosphorus, and other atoms. During the friction process, they can form a molybdenum - compound protective film with good lubrication performance on the metal surface, significantly reducing the friction coefficient and improving the anti - wear performance. They are widely used in engine oils, gear oils, etc., and can improve the extreme - pressure and anti - wear performance of oil products.
Amines and Amides: Such as fatty amines and alkanolamides. The amino groups in amine molecules have strong polarity and can adsorb on the metal surface, and their long - chain hydrocarbon groups provide lubricity. Amides are formed by the reaction of amines and carboxylic acids and also have good lubrication and anti - wear properties. They are commonly used in products such as lubricating greases and cutting fluids to reduce friction and wear.
Inorganic Friction Modifiers:
Graphite: Graphite has a typical layered crystal structure. The layers are combined by weak van der Waals forces. Under external force, the layers are easy to slide relative to each other, thus playing a lubricating role. It has good high - temperature resistance, chemical stability, and self - lubrication. It is often added as a solid lubricant to lubricating greases, powder metallurgy materials, etc., for lubrication under special working conditions such as high temperature and heavy load.
Molybdenum Disulfide: The crystal structure of molybdenum disulfide is similar to that of graphite. It is a layered structure composed of sulfur atoms and molybdenum atoms, with weak inter - layer binding force and an extremely low friction coefficient. It has good anti - wear, extreme - pressure, and chemical stability properties and is commonly used for mechanical lubrication under harsh conditions such as high temperature, high pressure, and high speed, such as in the aerospace and automotive engine fields.
Borates: Such as zinc borate and sodium borate. During the friction process, borates can form a hard and smooth protective film on the metal surface, playing a role in reducing friction and wear. At the same time, borates also have certain anti - rust and anti - oxidation properties. They can be used in products such as lubricating oils, lubricating greases, and metalworking fluids to improve the comprehensive performance of products.
Classification by Physical Form:
Oil - Soluble Friction Modifiers: This type of friction modifier can be uniformly dissolved in lubricating oil in a molecular state to form a homogeneous system. They have good dispersibility and stability in lubricating oil and can quickly reach the friction surface with the flow of lubricating oil to play a role in reducing friction and wear. Common oil - soluble friction modifiers include organic molybdenum compounds and fatty acid esters. They are suitable for various mechanical equipment that requires lubrication with lubricating oil, such as automobile engines, gearboxes, and hydraulic systems.
Solid - Suspended Friction Modifiers: Solid - suspended friction modifiers are in the form of tiny solid particles suspended in lubricating oil or lubricating grease. During the lubrication process, these solid particles can fill the microscopic unevenness of the friction surface, playing a role in supporting and lubricating, and reducing the friction coefficient. Common ones include graphite, molybdenum disulfide, boron nitride, etc. They are commonly used for lubrication under working conditions such as high temperature, heavy load, and low speed, such as in mining machinery and construction machinery.
Emulsion - Type Friction Modifiers: Emulsion - type friction modifiers are formed by dispersing friction - modifier components in water or other solvents to form an emulsion. It combines the cooling performance of water and the lubrication performance of friction modifiers, having good cooling, lubrication, and cleaning properties. It is commonly used in the metal processing field, such as in cutting fluids and grinding fluids, and can effectively reduce the friction and heat during the processing process and improve the processing quality and efficiency.
Performance Improvement of Friction Modifiers
In practical applications, friction modifiers have demonstrated significant advantages in multiple fields. Taking the automobile engine as an example, according to the engine model, working conditions, and the basic formula of the lubricating oil, the addition amount of the friction modifier is generally between 0.5% - 2%. When adding, the friction modifier needs to be uniformly mixed into the lubricating oil according to a certain proportion to ensure its full dispersion in the lubricating oil. Through actual tests on multiple vehicles, after adding the friction modifier, the fuel consumption of the vehicle is reduced by an average of 5% - 10%. This means that in the long - term use process, it can save considerable fuel costs for vehicle owners.
In the field of industrial gearboxes, friction modifiers also play an important role. For different types of industrial gearboxes, such as closed - type gearboxes and open - type gearboxes, the addition amount and usage methods of friction modifiers will be different. Generally, the addition amount of friction modifiers in closed - type gearboxes is 1% - 3%, while for open - type gearboxes, due to more severe working conditions, the addition amount may be appropriately increased. By detecting the wear amount of industrial gearboxes before and after adding the friction modifier, it is found that the wear amount is reduced by 30% - 60%, which greatly extends the service life of the gearbox, reduces the equipment maintenance cost and downtime, and brings significant economic benefits to enterprises.
In conclusion, as a powerful tool for taming mechanical friction, by deeply understanding the principles, types, and practical application performance of friction modifiers, we can give full play to their advantages and provide strong support for the efficient and sustainable development of the machinery industry.
The Price of Organic Molybdenum Lubricating Oil Additives
The price of organic molybdenum lubricating oil additives varies depending on factors such as brand, specification, composition, and sales channels. If you are interested in organic molybdenum lubricating oil additives, please feel free to contact us.
Supplier of Organic Molybdenum Lubricating Oil Additives
UNPChemicalsis a professional supplier of high-quality and effective organic molybdenum lubricating oil additives. We offer several remarkable products, namely Molybdenum dithiophosphate MSAIL 300L MoDTP, Molybdenum dithiocarbamate MSAIL 525A MoDTC, and Organomolybdenum complex S/P free MSAIL 8550, etc.
Molybdenum Dithiophosphate (MoDTP) MSAIL 300L as a liquid organic molybdenum friction modifier containing sulfur and phosphorus, it can greatly reduce the friction coefficient of oil products, and has multiple functions such as extreme pressure, anti-wear and anti-oxidation. It is widely used in internal-combustion engine oil, various industrial lubricants, pure oil metalworking fluid, grease, etc.
Molybdenum Dithiocarbamate MSAIL 525A MoDTCis a phosphate-free liquid organic molybdenum friction modifier, which can greatly reduce the friction coefficient of oil products, and has a variety of functions such as anti-wear and anti-oxygen, and is widely used in internal combustion engine oil, various industrial lubricants, pure oil-type metal working fluids, greases, etc.
Organomolybdenum complex (S/P free) MSAIL 8550 is a highly versatile and environmentally friendly lubricant additive belonging to the Organomolybdenum complex class. Its exceptional friction reduction properties, superior performance when combined with sulfur additives, and antioxidation synergism make it an ideal choice for a wide range of applications. Mainly used for internal-combustion engine oil, various industrial lubricating oils, pure oil metalworking fluid and lubricating grease.
Professional Lubricant Additive Manufacturer
UNPChemicals, aka Luoyang Pacific United Petrochemical Co., Ltd., focuses on the application and development of special lubricating grease additives such as MODTC, MODTP, molybdenum amide, thiadiazole metal deactivators, and phosphate esters. With nearly 30 products in seven series, including extreme pressure anti-wear additives and special grease additives, it is a global manufacturer of special lubricating grease additives and a national high-tech enterprise with great influence and leading role in the industry. If you are looking for Lubricant Additive or technical information, feel free to contact UNPChemicals.